Inaccurate navigation systems can lead to disastrous results: mission failures, costly delays, or even compromised safety. If your project relies on precise motion tracking, these issues can affect overall success. However, with a well-designed Inertial Measurement Unit (IMU), you can ensure accurate and stable navigation, eliminating such risks.
The primary function of an Inertial Measurement Unit (IMU) is to measure and report an object’s acceleration, angular velocity, and orientation, ensuring accurate navigation and motion control. IMUs are essential in industries such as aerospace, defense, and robotics, where precision is non-negotiable.
Let’s delve deeper to understand the IMU’s role in various applications.
Table of contents
What Are the Main Components of an IMU?
At its core, an IMU uses two primary types of sensors: accelerometers and gyroscopes. The accelerometers track how fast an object is speeding up or slowing down along three axes (x, y, z). Meanwhile, the gyroscopes measure how quickly that object is spinning or rotating. This combination lets the IMU monitor motion in three dimensions, providing real-time feedback.
Sometimes, high-end IMUs also include magnetometers. By incorporating magnetic field data from the magnetometer, the angular velocity accuracy of the gyroscope is further improved, leading to better yaw correction and enhanced overall navigation accuracy.
Think about it like this: whether you’re flying a drone, guiding a missile, or managing a satellite, the IMU is constantly feeding your control system the data it needs to keep everything running smoothly. It doesn’t matter if you’re in the sky or underwater; the IMU knows where you are. And that’s the beauty of it—it operates independently. Once the IMU is initialized before departure, it can operate independently for a period of time without GPS or after losing accurate GPS signals, while maintaining relatively high accuracy during that time.
How Does an IMU Ensure Precision in Navigation?
Precision in navigation is the name of the game, especially when you’re piloting aircraft or autonomous vehicles. While GPS systems give you external data on position, they’re not always reliable—think tunnels, deep forests, or outer space. That’s when your IMU steps up. By measuring acceleration and rotation non-stop, it calculates changes in position and orientation in real time.
The coolest part? IMUs and GPS often work hand in hand. When the GPS loses signal, the IMU takes over and keeps things on track. For example, imagine you’re flying a plane and suddenly the GPS drops out. No problem—the IMU will keep calculating the plane’s position, based purely on internal velocity and rotation measurements. As soon as the GPS comes back online, you’re still right on course. No drift, no guessing.
This seamless blend of internal IMU data and external GPS data gives you pinpoint accuracy, even in the trickiest environments.
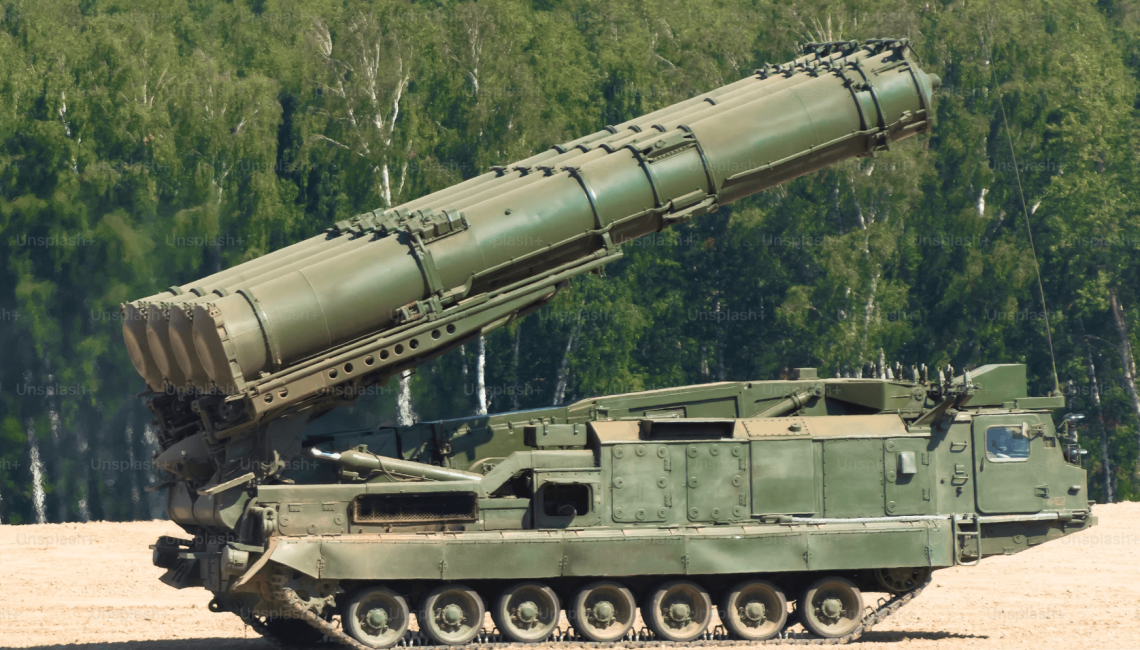
Why Are IMUs Essential for Stabilization?
Now let’s talk about stability. Whether it’s flying through turbulence or guiding a missile through unpredictable wind patterns, stabilization is critical. That’s another area where IMUs truly shine. In an aircraft, for instance, the IMU continuously sends motion data to the control system. When it detects any shift—like unexpected turbulence—it tells the system to make immediate adjustments. This keeps the ride smooth and stable.
In the defense world, think about missiles or UAVs. Even a tiny change in motion can throw off a missile’s trajectory. The IMU detects these subtle shifts and ensures the system stays on course, correcting for any deviations in real time. Without the IMU, you’re risking missed targets and failed missions. That’s just not acceptable when accuracy is everything.
IMUs also find their way into camera stabilization systems. If you’ve ever seen silky smooth drone footage, you can thank the IMU. By constantly sensing motion, it helps the camera stay steady, even during fast movements or vibrations.
What Role Do IMUs Play in Autonomous Systems?
Autonomous systems—think self-driving cars, drones, robots—rely heavily on IMUs. These machines need to understand their environment and how they’re moving through it, all without human input. That’s a big job, but the IMU handles it with ease.
Take self-driving cars as an example. Alongside sensors like LiDAR and cameras, the IMU works to keep the car aware of its orientation and velocity. What happens when the car enters a tunnel and the GPS drops out? The IMU seamlessly takes over, making sure the car continues navigating smoothly. Once the GPS signal returns, the car hasn’t missed a beat.
In industrial robotics, IMUs are just as important. Whether it’s assembling parts or moving across a factory floor, the robot relies on the IMU to understand its position and orientation. This ensures movements are precise and repeatable, with no room for error.
How Do IMUs Enhance Performance in Industrial Applications?
IMUs have found their way into all kinds of industrial applications. From mining to agriculture to construction, machines are often operating in remote areas where GPS can’t always be trusted. Enter the IMU. It tracks the movement and orientation of machinery, allowing operators to stay informed and keep everything running optimally.
In manufacturing, IMUs are integrated into robotic arms. These robots need to hit their marks with incredible precision, and that’s where the IMU comes in. Even the smallest motion changes are detected, allowing the robot to make immediate adjustments. The result? Flawless production lines, fewer mistakes, and less downtime.
Logistics is another area where IMUs are making waves. Automated guided vehicles (AGVs) move goods around warehouses efficiently. Thanks to the IMU, these vehicles can navigate large, complex spaces without human guidance, avoiding obstacles and staying on course.
What Types of IMUs Are Commonly Used?
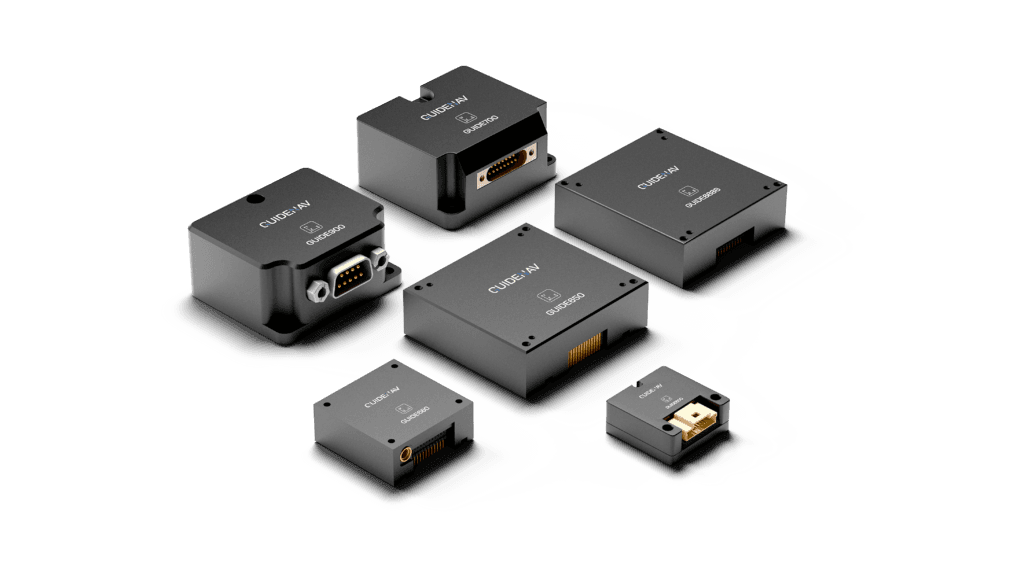
Not all IMUs are created equal. There are two primary types, each suited to different needs:
MEMS (Micro-Electro-Mechanical Systems) IMUs: These are small, affordable, and used in everything from smartphones to drones. They’re compact and do a decent job in applications that don’t require ultra-high precision.FOG (Fiber Optic Gyroscope) and RLG (Ring Laser Gyroscope) IMUs: If you need high precision, these are your go-to IMUs. They’re typically found in aerospace and military applications because they offer greater accuracy and stability. If you’re guiding a missile or navigating a spacecraft, you want FOG or RLG IMUs on your side.
Choosing the right IMU depends on your application, your accuracy requirements, and, of course, your budget. For everyday commercial uses, MEMS IMUs are more than capable. But if you’re dealing with defense or aerospace, you’ll likely need the higher-end FOG IMUs.
Conclusion
The Inertial Measurement Unit (IMU) is an indispensable tool for navigation, stabilization, and motion tracking across various industries. Whether you’re operating a drone, guiding a missile, or automating a production line, the IMU provides the real-time data necessary to ensure precision and reliability in any environment.