Imagine you’re piloting a drone or driving an autonomous vehicle, relying solely on your device’s ability to understand its position, direction, and speed. But what happens if the system can’t accurately track its movement? Misjudgments, deviations, or even complete system failures can result in serious consequences, especially in industries like aerospace or defense. This is where Inertial Measurement Units (IMUs) come in—providing the critical data required for precise navigation and control.
An IMU sensor plays a central role in modern navigation systems by measuring an object’s acceleration, angular rate, and sometimes magnetic field to give precise movement data. It ensures stable, accurate motion tracking, making it indispensable in a wide range of high-tech applications.
Now, let me break down everything you need to know about IMU sensors based on my experience of over 15 years working in the inertial navigation industry.
Table of contents
How Does an IMU Sensor Work?
Given my years in the industry, I can tell you that the versatility of IMU sensors is staggering. You’ll find them everywhere, from commercial drones to military-grade navigation systems. Let’s explore a few areas where they play a pivotal role:
- Aerospace: In aviation and space exploration, accurate movement data is vital. IMUs help aircraft maintain stability, assist in autopilot systems, and guide rockets and satellites, ensuring they stay on course even when GPS is unreliable or unavailable.
- Defense: IMUs are integrated into guided missiles, tanks, and unmanned aerial vehicles (UAVs), helping these machines navigate complex environments with pinpoint accuracy. In military settings, the reliability of these sensors is often a matter of life and death.
- Robotics: For autonomous robots, IMUs provide real-time motion tracking, enabling them to navigate their surroundings, avoid obstacles, and complete tasks without human intervention. Without IMU sensors, robotics would lack the ability to move with precision.
- Marine Navigation: In submarines and surface ships, where GPS signals can be weak or absent, IMUs are used to track movement and orientation, ensuring accurate navigation through treacherous waters.
- Wearable Technology: Even in consumer electronics, like smartphones and fitness trackers, IMUs are responsible for detecting motion and providing data for applications like step counting or detecting whether the user is standing or sitting.
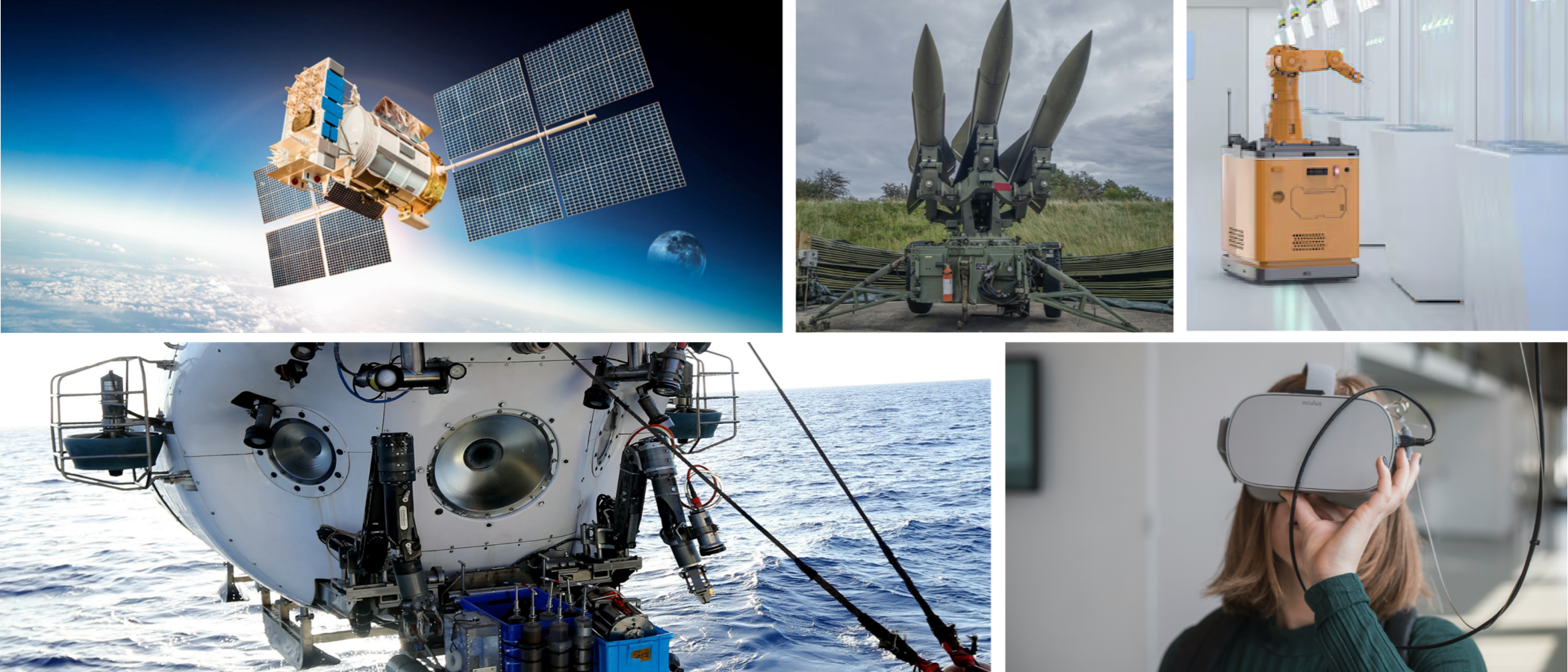
Types of IMU Sensors
One question I get asked frequently by clients is about the different types of IMUs available on the market. Over the years, I’ve seen a lot of innovation in this area, but the most commonly used types of IMU sensors fall into three categories:
- MEMS (Micro-Electro-Mechanical Systems) IMUs: These are widely used due to their small size, low cost, and decent accuracy. You’ll find them in consumer electronics, UAVs, and even some lower-end industrial applications. MEMS IMUs are ideal for applications where space is limited and cost is a factor.
- Fiber Optic Gyroscope (FOG) IMUs: If you need higher precision, FOG IMUsare the way to go. These sensors are based on the interference of light and offer exceptional accuracy, making them ideal for aerospace and military applications where even the smallest error in navigation could lead to mission failure.
- Ring Laser Gyroscope (RLG) IMUs: Even more precise than FOG IMUs, RLG IMUsare the gold standard in high-end navigation systems, such as those used in commercial aircraft or military vehicles. They provide the most accurate data possible but are also more expensive and bulkier than other types.
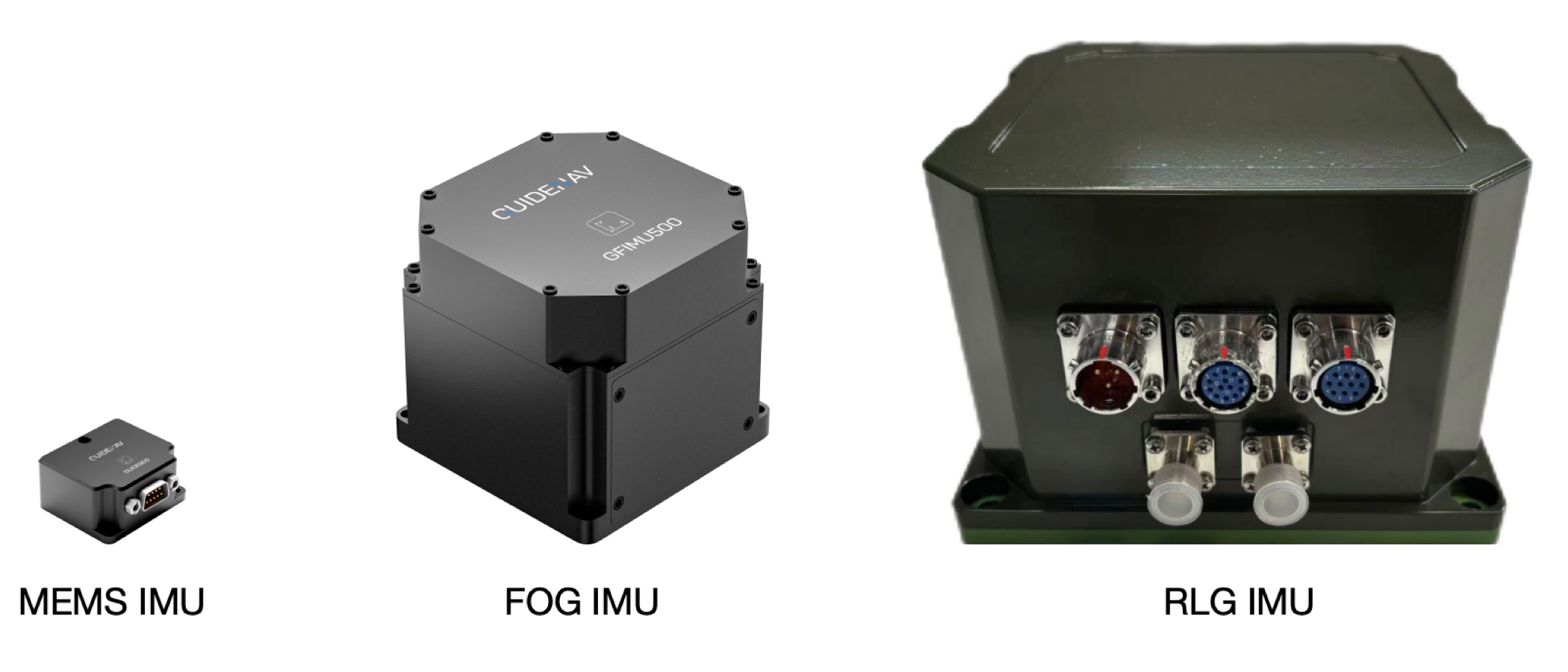
How Does an IMU Sensor Differ from GPS?
I often encounter confusion between IMUs and GPS systems, so let me clear that up. While both technologies are used for navigation, they serve different purposes. GPS relies on satellite signals to provide location data, but it can be unreliable in certain environments like tunnels, indoors, or underwater. An IMU, on the other hand, measures motion and orientation, making it extremely valuable in situations where GPS cannot function or when highly dynamic movement tracking is needed.
In fact, many systems use IMUs alongside GPS for improved accuracy. When GPS signals drop out, the IMU can continue providing motion data, ensuring that the system remains functional.
What Happens if IMUs Are Not Calibrated Properly?
Over time, even the best IMUs can experience drift—a slow degradation in the accuracy of the data they provide. This can be due to temperature changes, mechanical wear, or other factors. Calibration is the process of adjusting the sensor to ensure its output remains precise. In industries like aerospace or defense, where safety is paramount, regular calibration is critical.
For instance, imagine a drone that hasn’t had its IMU calibrated in months. As it flies, small inaccuracies in the sensor data accumulate, leading the drone to drift off course. In a best-case scenario, it may miss its destination. In a worst-case scenario, it could collide with obstacles or lose control altogether.
We at GuideNav recommend frequent calibration checks, especially in environments where precision is critical. With proper calibration, you can avoid sensor drift and ensure reliable, accurate data over the lifespan of the sensor.
How to Choose the Right IMU?
When it comes to selecting the right IMU, the decision is not just about the sensor’s price or size—it’s about understanding the exact requirements of your application. Based on my experience, here’s what I often advise clients to consider:
Accuracy
One common misconception is that MEMS IMUs are only suitable for low-end applications with less demanding accuracy requirements. While it’s true that traditional MEMS were often associated with lower precision compared to FOG or RLG sensors, advancements in high-precision MEMS IMUs have significantly closed this gap. Today, some high-end MEMS IMUs can offer precision comparable to mid-range FOG IMUs, making them a competitive choice for applications where both performance and compact size are required.
For example, if you’re working on UAVs, autonomous vehicles, or robotics, a well-designed MEMS IMU might offer the accuracy you need at a more cost-effective price point, while also being more resilient to shocks and vibrations than some FOG systems.
Application Environment
Consider the environment in which the IMU will operate. For aerospace or defense applications, where environmental factors such as extreme temperatures or high vibrations are common, you’ll need an IMU that can maintain accuracy under these harsh conditions. FOG and RLG IMUs are often favored here for their superior performance, but again, high-end MEMS IMUs are increasingly being used in these environments, as they can be more compact, shock-resistant, and still deliver impressive accuracy.
Cost vs. Performance
While FOG and RLG IMUs generally offer superior accuracy and stability, they also come with a higher cost. If your application doesn’t demand that level of precision, or if you need a more compact solution, a high-precision MEMS IMU can provide an excellent balance of performance and affordability.
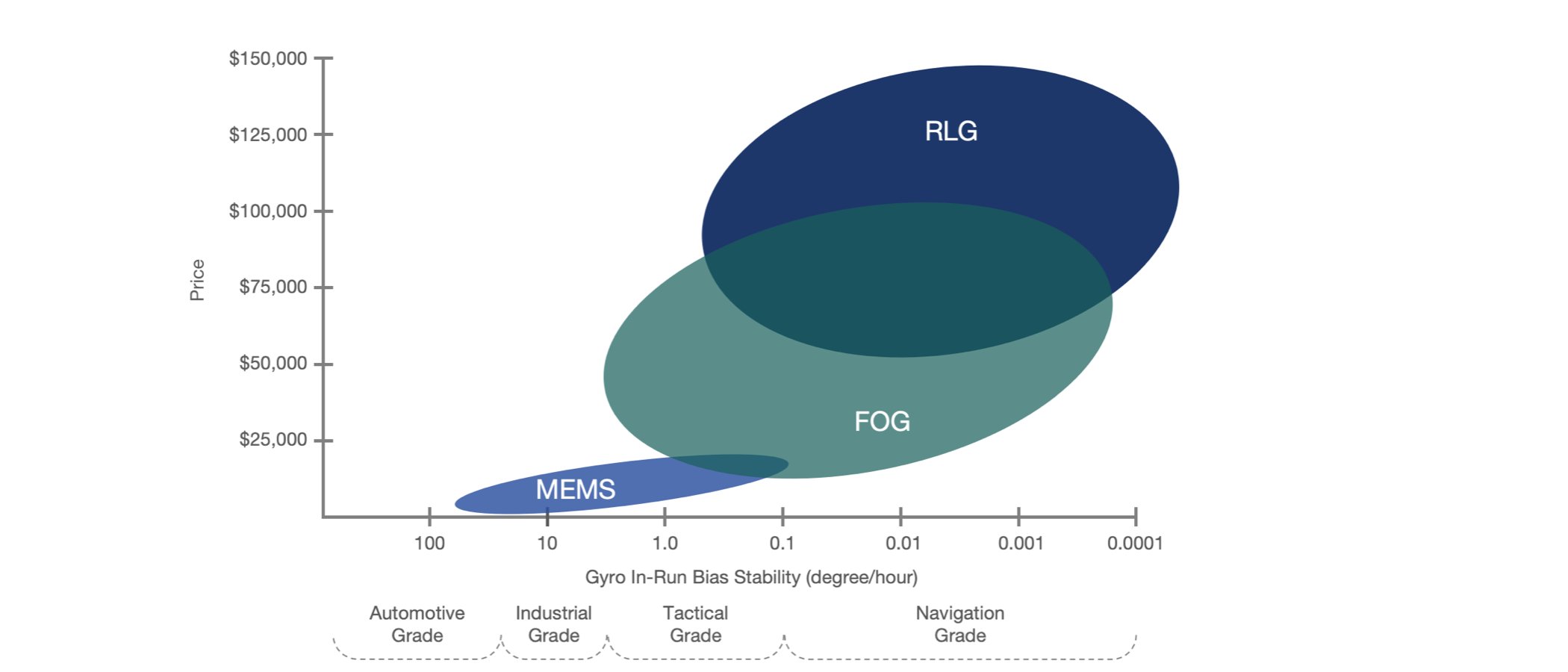
Calibration Needs
Consider the drift characteristics and how often the sensor will need recalibration. While all IMUs experience drift over time, some MEMS IMUs have improved in this area, offering lower drift rates, especially when used in systems with advanced filtering and sensor fusion algorithms.
In short, when choosing the right IMU, it’s critical to evaluate the specific performance needs of your project, as well as factors like size, cost, and operating environment. Whether it’s a FOG, RLG, or high-end MEMS IMU, the right choice will always depend on the balance between these elements.
How Does GuideNav IMU Stand Out?
I’ve worked with many types of IMUs over the years, and I can confidently say that the IMUs we manufacture at GuideNav are among the most reliable on the market. Our products are designed with the demanding requirements of industries like aerospace, defense, and robotics in mind. What sets us apart is not just the quality of our sensors, but our ability to customize them according to the unique needs of our clients. Whether you need enhanced accuracy, better durability, or integration with complex systems, we work closely with our clients to deliver a solution that exceeds their expectations.