With over 15 years of experience working in the inertial navigation field, I understand how overwhelming it can be to choose the right sensor for your application. In this article, I’ll guide you through everything you need to know about MEMS IMUs—what they are, how they work, and why they’re critical for precise navigation in today’s technologies.
A MEMS IMU (Micro-Electro-Mechanical System Inertial Measurement Unit) combines accelerometers, gyroscopes, and sometimes magnetometers into a single device to measure motion and orientation. These tiny yet powerful units provide crucial data in countless applications, from drones to industrial robots, making them indispensable for businesses aiming to integrate precise navigation and control into their systems.
Read on as I break down the core elements of MEMS IMUs and how they can enhance your projects.
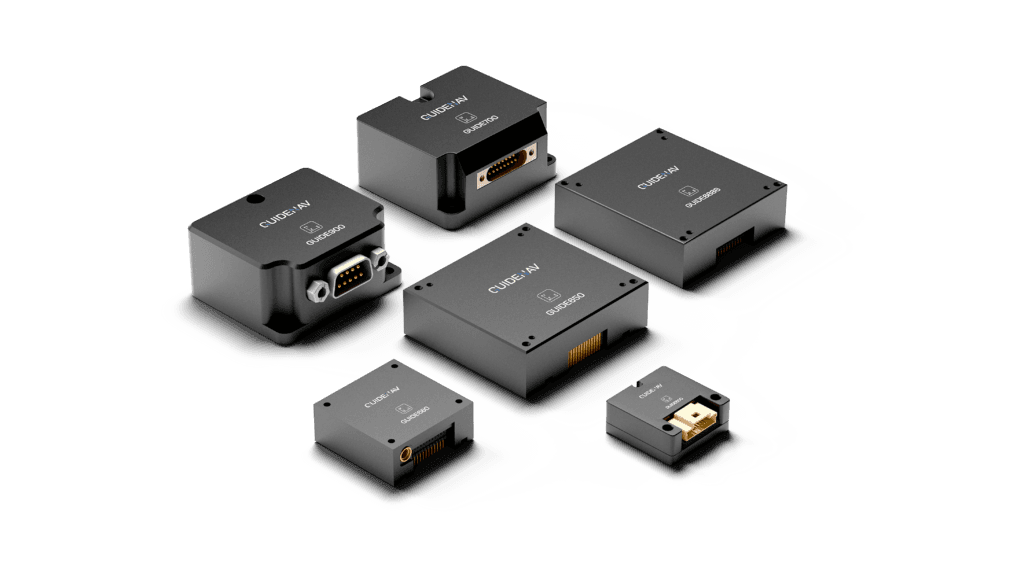
Table of contents
How does a MEMS IMU Work?
A MEMS IMU works by using tiny mechanical components to measure both acceleration and rotational movement. Picture this: you’re holding your smartphone, and as you tilt it, the screen automatically rotates. That’s thanks to a MEMS IMU inside your phone. It detects how the device moves through space using accelerometers, which measure linear motion, and gyroscopes, which track rotation. The combination of these two sensor types allows the device to monitor its orientation and position in real-time.
In some cases, MEMS IMUs also include a magnetometer, which measures the Earth’s magnetic field to determine heading. This is especially useful in applications that require orientation relative to the Earth’s poles, such as compasses or navigation systems.
When all these elements work together, they create a cohesive picture of how an object is moving—whether it’s a drone flying through the air or a robot navigating a factory floor.
What are the Main Components of a MEMS IMU?
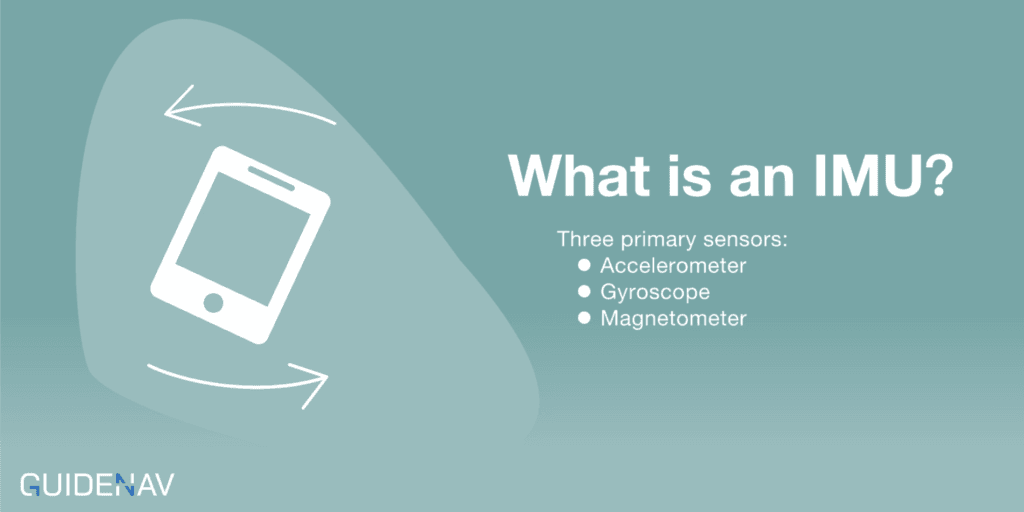
When we break down a MEMS IMU, we’re essentially looking at three core components:
- Accelerometer – This sensor measures changes in velocity. It can detect linear acceleration, which helps determine how fast an object is moving in a specific direction.
- Gyroscope – The gyroscope measures rotational velocity, meaning it tells you how fast an object is spinning around its axis. This is vital for applications where understanding orientation is key, like stabilizing drones or keeping a camera steady.
- Magnetometer (optional) – This sensor tracks magnetic fields, which is often used to find true north. It’s particularly useful in navigation systems, where knowing your orientation relative to the Earth’s magnetic field is essential.
Each of these sensors plays a critical role in giving an accurate measurement of movement, and when integrated into a single system like an IMU, they work together to provide comprehensive motion data.
For example, in a drone, the accelerometer might tell the system that the drone is accelerating forward, while the gyroscope measures how much it’s pitching upward. With this data, the drone can adjust its rotors to stabilize its flight path.
Can MEMS IMUs be Used in Defense Applications?
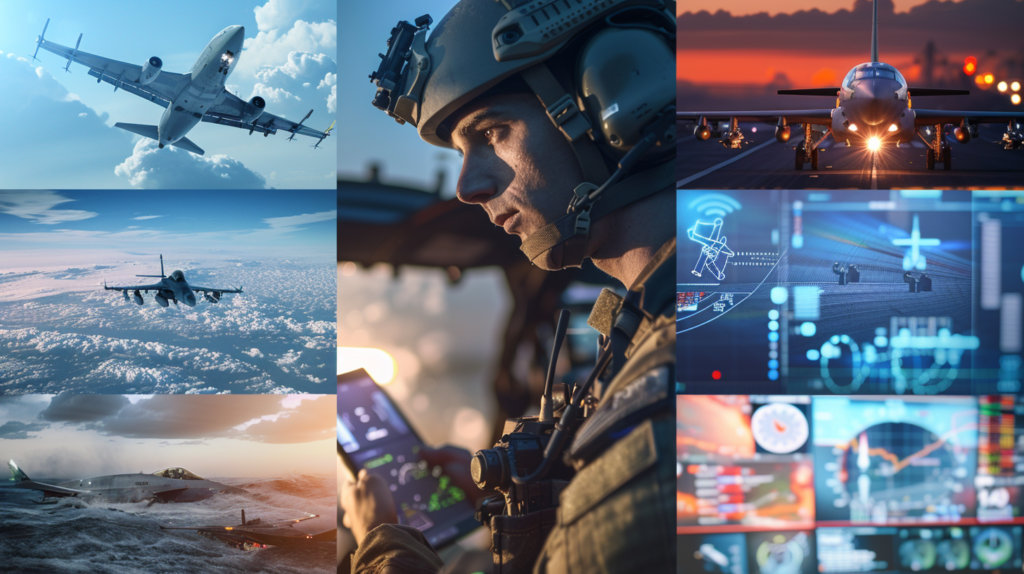
Absolutely. MEMS IMUs are not just for commercial use—they have significant value in defense applications as well. While traditional high-end military-grade IMUs often rely on more expensive technologies like FOGs (Fiber Optic Gyroscopes) or RLGs (Ring Laser Gyroscopes), advancements in MEMS technology have made these sensors increasingly attractive for defense applications.
One of the biggest advantages of using MEMS IMUs in defense is their compact size and low power consumption, which makes them ideal for use in applications like:
- Guided missiles: MEMS IMUs can track and control the movement of guided weapons, helping to improve precision while reducing the overall weight and power requirements of the system.
- Unmanned Aerial Vehicles (UAVs): Drones used for reconnaissance or other military operations benefit from MEMS IMUs for navigation and stabilization, ensuring they can operate effectively in dynamic environments.
- Soldier tracking systems: For dismounted soldiers, MEMS IMUs help track movement and orientation, enabling better situational awareness on the battlefield.
While MEMS IMUs may not yet rival the extreme precision of higher-end sensors in some of the most demanding defense applications, their rapid improvements and versatility make them highly valuable for certain military use cases. Additionally, cost-effective MEMS technology allows defense organizations to deploy these sensors in a wider range of equipment, from handheld devices to sophisticated vehicles.
How Accurate is a MEMS IMU?
One of the key questions I often get is, How accurate are MEMS IMUs? The truth is, accuracy depends on several factors, including the quality of the sensors, calibration, and how the system processes the raw data.
MEMS IMUs are incredibly precise, but they do have limitations, especially when compared to other types of IMUs, such as Fiber Optic Gyroscopes (FOGs). MEMS-based systems can experience drift, which is a gradual loss of accuracy over time if the data isn’t corrected or filtered. However, advanced algorithms, such as Kalman filtering, can be used to mitigate these errors, ensuring the output remains reliable.
While they may not be as accurate as FOG IMUs in ultra-high-precision environments like aerospace or military-grade navigation, companies such as GuideNav manufactures MEMS IMUs offer more than enough precision that rivals even entry-level and mid-range fiber optic gyroscopes (FOGs).Plus, they come at a fraction of the cost and in a much smaller size, making them ideal for space-constrained applications like drones.
When classifying MEMS IMUs, they are generally categorized into four main grades based on bias instability (gyro bias in °/h) and precision: Consumer Grade, Industrial Grade, Tactical Grade, and Strategic Grade. Here’s a detailed breakdown of these classifications:
MEMS IMU Grade | Typical Bias Instability (Gyroscope, °/h) | Applications |
---|---|---|
Consumer Grade | > 10°/h | Smartphones, fitness trackers, gaming controllers |
Industrial Grade | 1°/h to 10°/h | Drones, robotics, automotive systems |
Tactical Grade | 0.1°/h to 1°/h | Defense systems, UAVs, precision industrial tools |
Strategic Grade | < 0.01°/h | Aerospace, submarines, strategic-level navigation |
What are Common Applications for MEMS IMUs?
MEMS IMUs are everywhere, even if you don’t realize it. Let me give you a few examples:
- Drones and UAVs: MEMS IMUs are at the heart of flight stabilization systems, ensuring drones can maintain level flight even in turbulent conditions. They’re responsible for tracking the drone’s movements and feeding that data back to the control system to make minute adjustments in real time.
- Smartphones: As I mentioned earlier, MEMS IMUs are what allow your phone to switch from portrait to landscape mode when you tilt it. But beyond that, they’re also used in augmented reality (AR) applications to detect how you’re moving your phone through space.
- Robotics: In industrial settings, MEMS IMUs are used to help robots navigate their environment, avoiding obstacles and accurately positioning themselves for tasks like assembly or material handling.
- Wearable Devices: Fitness trackers use MEMS IMUs to monitor your activity levels, tracking how many steps you’ve taken, how fast you’re running, or even how well you’re sleeping by detecting your movements throughout the day and night.
- Autonomous Vehicles: For self-driving cars, MEMS IMUs play a critical role in helping the vehicle understand its position and movement, especially when combined with other sensors like GPS and LIDAR.
In short, MEMS IMUs are integral to many of the technologies that shape our modern world, from the gadgets we carry in our pockets to the industrial systems that power manufacturing.
What is the Difference Between MEMS IMUs and FOG IMUs?
I often get asked about the differences between MEMS IMUs and Fiber Optic Gyroscopes (FOGs), and it really comes down to a trade-off between size, cost, and precision.
MEMS IMUs are compact, lightweight, and relatively inexpensive, making them suitable for commercial applications where space and cost are concerns. However, they may not offer the ultra-high precision needed in certain applications.
On the other hand, FOG IMUs offer extremely high accuracy and are often used in aerospace, defense, and other mission-critical applications. They use the interference of light to measure rotation, which is much more precise but also much bulkier and more expensive.
So, if your project demands pinpoint accuracy and you have the budget for it, a FOG IMU might be the better choice. But for most commercial applications, MEMS IMUs strike the right balance between performance and cost.
Feature | MEMS IMU | FOG IMU |
---|---|---|
Technology | Micro-Electro-Mechanical Systems (MEMS) use miniaturized mechanical components. | Fiber Optic Gyroscope (FOG) uses light interference in fiber optics for measurement. |
Size & Weight | Smaller and lighter, making it ideal for space-constrained applications like drones and handheld devices. | Larger and heavier due to the use of optical fibers, more suitable for aerospace or industrial applications. |
Cost | Low cost, widely available in consumer and industrial markets. | Higher cost due to advanced technology and more complex manufacturing process. |
Accuracy | Good accuracy for general applications, but drift over time can be significant in high-precision environments. | Extremely high accuracy with very low drift, making it ideal for navigation and aerospace applications. |
Power Consumption | Low power consumption, suitable for battery-powered devices. | Higher power consumption due to optical components, better suited for systems with available power resources. |
Durability | Generally more resistant to shocks and vibrations, often used in rugged environments. | Fragile compared to MEMS; requires careful handling and is often installed in vibration-controlled environments. |
Applications | Consumer electronics, UAVs, automotive, wearable devices, defense, and general industrial uses. | Aerospace, defense, submarines, and high-precision navigation systems. |
How Do You Choose the Right MEMS IMU for Your Project?
Choosing the right MEMS IMU depends on several factors:
- Accuracy Requirements: For example, if you’re working on a drone that needs to maintain precise flight control in turbulent conditions, you’ll want an IMU with low drift and high precision.
- Size Constraints: Some projects, like wearable devices or compact drones, require the IMU to be as small and lightweight as possible.
- Environmental Tolerance: If your project involves harsh environments, like high heat, vibration, or moisture, you’ll need to choose a MEMS IMU that can withstand those conditions without losing accuracy.
- Budget: MEMS IMUs come in a wide range of price points, and more expensive models typically offer better performance. It’s crucial to balance your project’s budget with the level of precision you need.
- Power Consumption: In battery-operated devices, such as wearables or drones, you’ll want an IMU that consumes minimal power to extend the device’s operational time.
How GuideNav Can Help?
At GuideNav, we specialize in manufacturing high-precision IMUs, with our MEMS IMUs achieving accuracy comparable to entry-level and even mid-range fiber optic gyroscopes (FOGs). We also offer tailored solutions based on your specific application requirements, ensuring you get the best fit for your project.
If you’re in the market for the right IMU, I encourage you to reach out to us. We’re ready and equipped to help you find the perfect solution. Whether your project involves defense, autonomous systems, or industrial applications, we’re here to serve you.
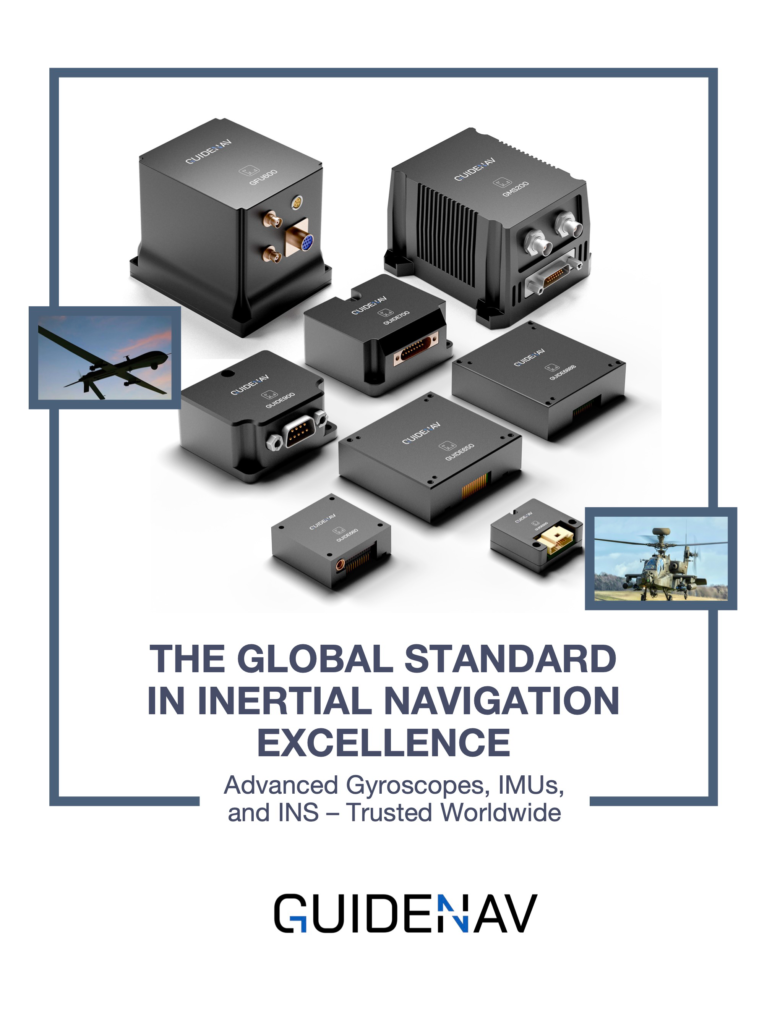