Table of Contents
- What is a IMU?
- Components of an Inertial Measurement Unit
- How Does Inertial Measurement Unit Works?
- Autonomous and Self-Driving Vehicles
- Aerospace and Aviation
- Robotics
- Virtual Reality (VR) and Augmented Reality (AR)
- Medical Devices
- Sports Analytics and Motion Capture
- Consumer Electronics
- MEMS IMU vs FOG IMU: Key Differences
- MEMS IMU: Overview and Characteristics
- FOG IMU: Overview and Characteristics
- IMU Performance Indicators
- IMU Calibration Methods
- Advantages of Inertial Measurement Units
- Limitations of Inertial Measurement Units
- IMU vs AHRS (Attitude and Heading Reference System)
- IMU vs INS (Inertial Navigation System)
- Different Types of IMUs and Their Market Overview
- Future Trends and Development of Inertial Measurement Unit
Introduction
Inertial Measurement Units (IMUs) are crucial in today’s high-tech industries, including autonomous vehicles, robotics, and aerospace. However, despite their widespread use, many still struggle to fully understand how IMUs work and their potential. Without this understanding, there’s a risk of inefficiencies and errors in system performance. In this article, we will explore the basics of IMUs, their applications, and future trends, ensuring you get the most out of this technology.
An Inertial Measurement Unit (IMU) is a device that measures acceleration, angular velocity, and sometimes magnetic fields to determine an object’s orientation and position. IMUs are essential in navigation, control systems, and motion tracking. By combining sensor data, IMUs enable precise tracking of motion and orientation in environments where GPS signals may be weak or unavailable.
The future of IMUs is exciting, with trends such as sensor fusion and AI integration opening new possibilities. Let’s dive into how these systems work and what the future holds for their role in cutting-edge technologies.
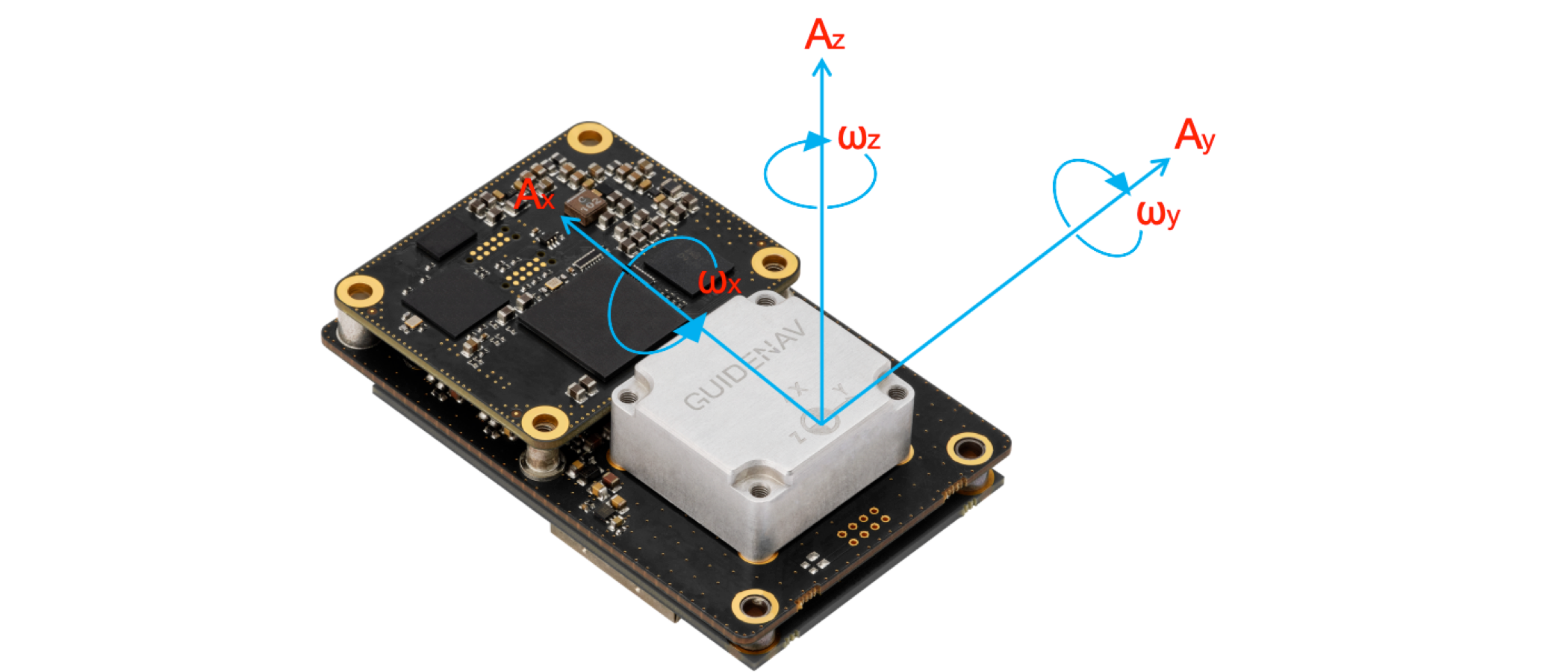
The Basics of Inertial Measurement Unit(IMU)
Components of an Inertial Measurement Unit
An IMU typically includes the following key sensors. Let’s break them down and look at how each contributes to the overall functionality:
Component | Function | Output |
---|---|---|
Accelerometer | Measures linear acceleration along the X, Y, and Z axes. | Provides data on velocity and displacement. |
Gyroscope | Measures the angular velocity (rate of rotation) around the X, Y, and Z axes. | Provides data on orientation (attitude). |
Magnetometer (Optional) | Measures the magnetic field strength and direction relative to the Earth’s magnetic field. | Provides heading (compass direction). |
Each of these sensors plays a crucial role in providing real-time motion data, helping us understand how the object is moving and rotating in space.
How Does Inertial Measurement Unit Works?
Here’s how we, at GuideNav, design IMUs to function seamlessly:
- Acceleration Measurement: The accelerometer detects changes in velocity along three axes. This data allows us to determine how fast the object is accelerating or decelerating, which is critical for tracking displacement over time.
- Angular Velocity Measurement: The gyroscope tracks how much the object is rotating around each of the three axes. By integrating this rotational data over time, the IMU can tell us the object’s precise orientation in space.
- Magnetic Field Measurement (Optional): If included, the magnetometer measures the Earth’s magnetic field, providing a compass heading. This helps correct any drift in the gyroscope readings, ensuring the IMU remains accurate over long periods.
At GuideNav, we use sensor fusion algorithms to combine data from these components. By doing so, we create a highly accurate representation of the object’s position and orientation in 3D space.
Applications of Inertial Measurement Units (IMUs)
Inertial Measurement Units (IMUs) are used in a wide range of applications, providing essential data on acceleration, angular velocity, and sometimes magnetic fields. Their precision and versatility make them crucial in industries like autonomous vehicles, aerospace, robotics, virtual reality, healthcare, sports analytics, and consumer electronics. Below, we’ll explore some of the key applications where IMUs are indispensable.
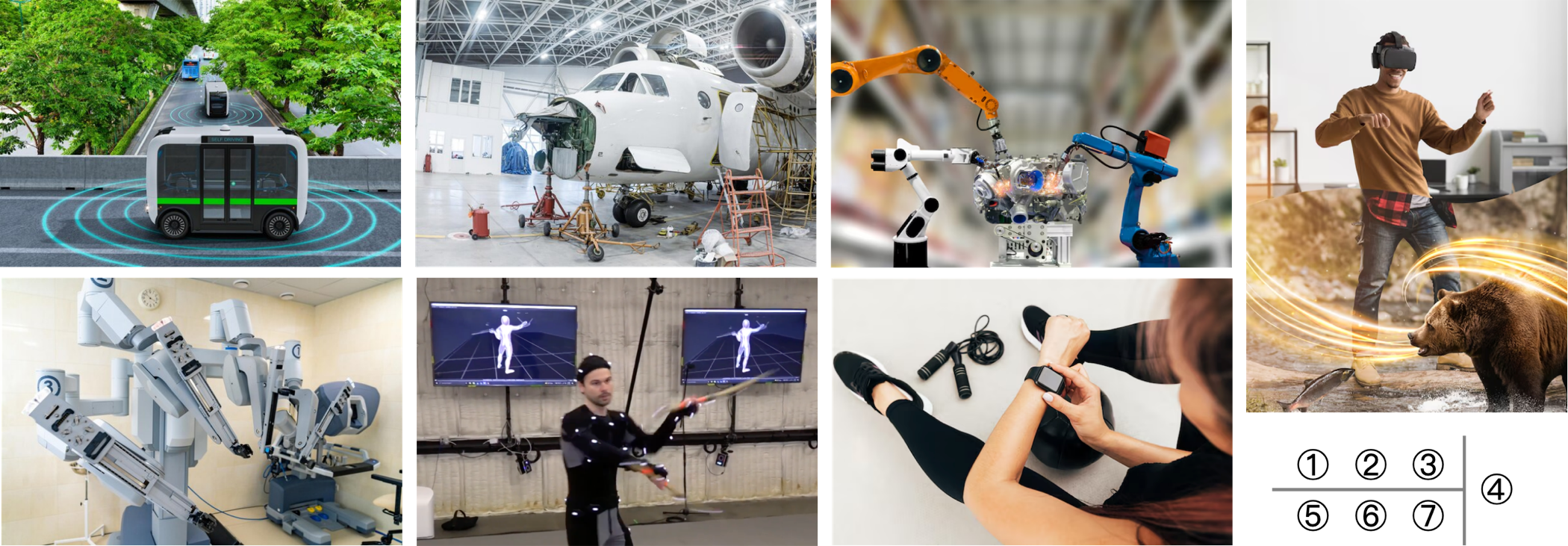
1. Autonomous and Self-Driving Vehicles
IMUs are critical in the development and operation of autonomous vehicles. They help track the vehicle’s movement and orientation in real-time, ensuring stability and precise navigation. While Global Positioning System (GPS) data is often used for positioning, IMUs are essential when GPS signals are weak or unavailable (e.g., in tunnels, urban canyons, or remote areas).
Application | Role of IMU |
---|---|
Autonomous Cars | Provides data on vehicle orientation and movement to enable stable navigation. |
Drones | Ensures precise control of flight path and position. |
Robotic Vehicles | Tracks movement in off-road or GPS-denied environments. |
2. Aerospace and Aviation
IMUs have long been integral to the aerospace and aviation industries. They provide real-time data on the orientation and motion of aircraft and spacecraft. IMUs are used in both commercial aviation and space exploration, offering high reliability and accuracy in challenging environments where GPS may not be available or practical.
Application | Role of IMU |
---|---|
Aircraft Navigation | Provides attitude (orientation) data for stable flight. |
Spacecraft Navigation | Ensures precise orientation and movement control in space. |
Satellite Orientation | Maintains satellite orientation and trajectory during operation. |
3. Robotics
In robotics, IMUs are used to monitor the movement, orientation, and balance of robots, whether in industrial, medical, or consumer applications. IMUs provide feedback to robot control systems, ensuring smooth and accurate motion in a variety of environments.
Application | Role of IMU |
---|---|
Industrial Robots | Ensures stable movement during manufacturing tasks. |
Medical Robots | Provides precise movement control for surgeries and rehabilitation. |
Autonomous Robots | Tracks position and orientation for navigation in dynamic environments. |
4. Virtual Reality (VR) and Augmented Reality (AR)
In the world of Virtual Reality (VR) and Augmented Reality (AR), IMUs are key components for tracking users’ head and body movements. By measuring rotation, acceleration, and sometimes magnetic fields, IMUs provide real-time motion data that enhances the immersive experience.
Application | Role of IMU |
---|---|
VR Headsets | Tracks head movements to adjust the virtual environment. |
AR Devices | Monitors hand movements to interact with virtual objects. |
Gesture Control | Recognizes user gestures for interaction within AR/VR systems. |
5. Medical Devices
IMUs are increasingly being integrated into medical devices for a variety of purposes, including motion tracking, rehabilitation, and diagnostics. Their ability to measure precise movements makes them invaluable for understanding and monitoring patient progress.
Application | Role of IMU |
---|---|
Physical Rehabilitation | Monitors patients’ movements during therapy to track progress. |
Wearable Devices | Tracks movement disorders, such as in patients with Parkinson’s disease. |
Motion Capture for Diagnostics | Measures abnormal movements for diagnostic purposes. |
6. Sports Analytics and Motion Capture
IMUs are widely used in sports analytics and motion capture to monitor athletes’ performance and optimize their movements. The precise motion tracking provided by IMUs helps in injury prevention, performance analysis, and improvement.
Application | Role of IMU |
---|---|
Athlete Performance | Tracks movement data to analyze speed, acceleration, and efficiency. |
Injury Prevention | Monitors movements to identify risks and optimize training. |
Motion Capture | Captures human motion for use in film, animation, and gaming. |
7. Consumer Electronics
IMUs are also embedded in many consumer electronics products, such as smartphones, wearables, and gaming controllers. These devices use IMUs to detect motion and orientation, enabling various features and enhancing the user experience.
Application | Role of IMU |
---|---|
Smartphones | Enables screen rotation, motion-based controls, and activity tracking. |
Fitness Trackers | Monitors step count, distance, and physical activity. |
Gaming Controllers | Tracks player movements for immersive gaming experiences. |
Inertial Measurement Unit (IMU) Types: MEMS IMU vs FOG IMU
Inertial Measurement Units (IMUs) are essential in many industries, particularly in defense and aerospace applications where high precision is critical. The two main types of IMUs, MEMS IMUs (Micro-Electro-Mechanical Systems) and FOG IMUs (Fiber Optic Gyroscope IMUs), differ significantly in terms of performance, size, cost, and suitability for different applications.
Although FOG IMUs have traditionally been used in high-precision areas like aerospace, defense, and robotics, recent advances in MEMS IMUs, such as the GUIDE900 and GUIDE900A, now offer precision levels of 0.1°/hr and 0.05°/hr, which are comparable to entry-level FOG IMUs. This improvement allows MEMS IMUs to be used in high-precision applications that were previously dominated by FOG IMUs.
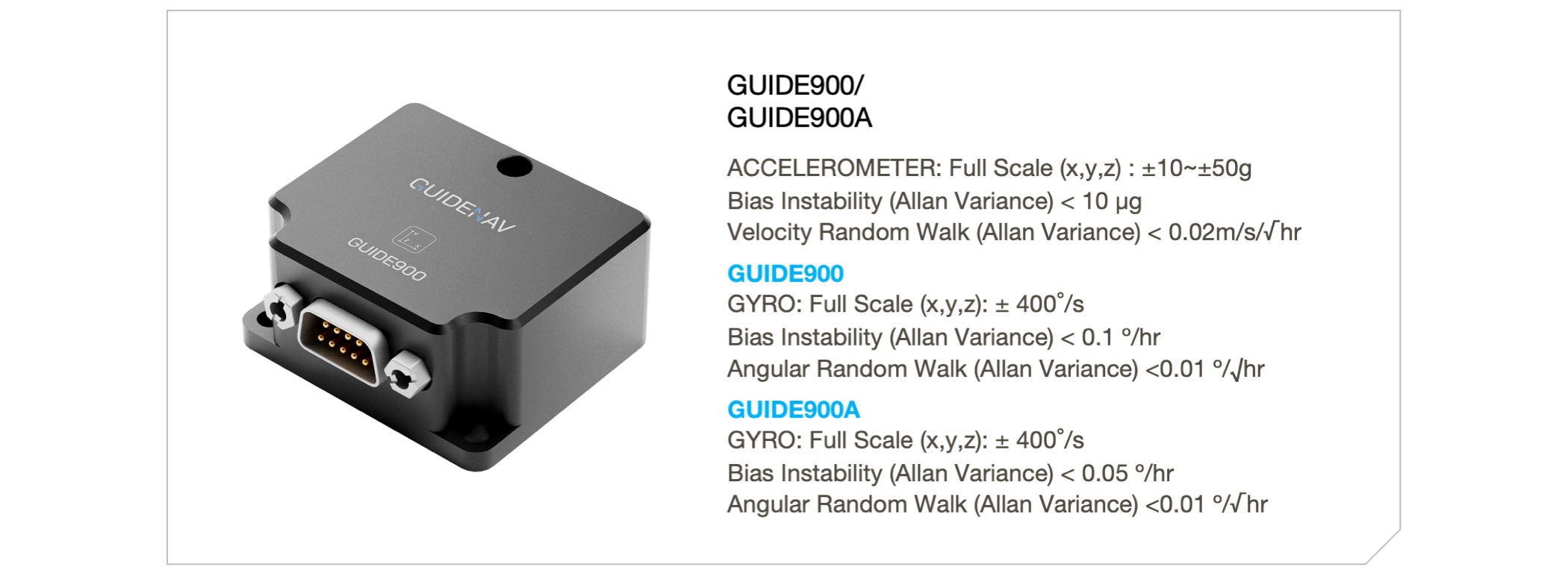
MEMS IMU vs FOG IMU: Key Differences
Parameter | MEMS IMU | FOG IMU |
---|---|---|
Technology | Based on Micro-Electro-Mechanical Systems (MEMS) sensors. | Uses fiber optic gyroscopes (FOGs) for angular velocity measurement. |
Size | Compact and lightweight, ideal for portable devices. | Larger, more robust, suited for precision applications in large-scale systems. |
Precision | Moderate precision, but newer high-precision MEMS IMUs can achieve 0.1°/hr or 0.05°/hr. | Extremely high precision, minimal drift, and more stable over time. |
Cost | Low cost, making them ideal for mass-market applications. | Higher cost due to advanced technology, used in high-end systems. |
Power Consumption | Low power consumption, suitable for battery-powered devices. | Higher power consumption, better suited for systems with higher energy budgets. |
Durability | Less durable under extreme environmental conditions. | Very durable, capable of handling harsh environments. |
Accuracy | Suitable for lower-to-medium precision applications. | High accuracy, suitable for high-precision navigation and stability. |
Applications | Consumer electronics, automotive systems, drones, UAVs, **military systems**. | Aerospace, defense, industrial robotics, high-end navigation systems. |
Drift | Higher drift over time, requiring recalibration. | Very low drift, ideal for long-term operation without recalibration. |
Response Time | Faster response due to smaller size and simpler design. | Slightly slower response but offers higher stability over time. |

MEMS IMU: Overview and Characteristics
MEMS Inertial Measurement Units use Micro-Electro-Mechanical Systems (MEMS) technology, where small mechanical components are integrated with electronics on a microchip. The primary advantages of MEMS IMUs are their small size, low cost, and low power consumption. These features make MEMS IMUs ideal for applications in consumer electronics, automotive systems, and increasingly in military applications as well.
At GuideNav, we are particularly proud of our high-precision MEMS IMUs such as the GUIDE900 and GUIDE900A, which provide accuracies of 0.1°/hr and 0.05°/hr, respectively, making them suitable for some high-precision applications that were traditionally dominated by FOG IMUs.
Key Features of MEMS IMUs:
- Small Size: Perfect for compact applications, such as smartphones, wearables, and military drones.
- Low Cost: Ideal for applications with large volumes, such as automotive systems, consumer electronics, and defense systemsthat need to balance performance with affordability.
- Moderate Precision: While MEMS IMUstraditionally offer lower accuracy than FOG IMUs, high-precision models now bridge this gap for many defense applications.
- Low Power Consumption: Highly efficient for battery-operated devices, crucial for military drones, smart weapons systems, and other mobile defense technologies.
Applications of MEMS IMUs:
- Defense: Used in military drones, navigation systemsfor armored vehicles, and missile guidance systems. These applications benefit from MEMS IMUs‘ compactness and low cost.
- Consumer Electronics: Found in smartphones, fitness trackers, and gaming controllers.
- Automotive Systems: Used in vehicle stability controland autonomous navigation.
- Drones and UAVs: Providing orientation and stabilization in military dronesand consumer-grade UAVs.
FOG IMU: Overview and Characteristics
FOG IMUs utilize fiber optic gyroscopes (FOGs) to measure angular velocity, which enables them to provide extremely high precision and stability. This makes FOG IMUs ideal for applications that require minimal drift and long-term reliability, such as aerospace navigation, missile guidance, and high-end robotics.
While FOG IMUs are widely regarded for their precision and durability, MEMS IMUs are closing the gap in performance, particularly in military applications where cost, size, and power consumption are key considerations.
Key Features of FOG IMUs:
- High Precision: FOG IMUsoffer extremely low drift, making them ideal for high-precision applications such as satellite navigation and military guidance systems.
- Durability: With the ability to handle extreme environmental conditions, FOG IMUsare ideal for aerospace and military systems that need to operate in harsh environments.
- Higher Power Consumption: FOG IMUsgenerally consume more power, making them better suited for systems with sufficient energy resources.
- Larger Size: FOG IMUsare bulkier compared to MEMS IMUs, which is why they are used in larger systems like aircraft and spacecraft.
Applications of FOG IMUs:
- Aerospace: Used in aircraftand satellite navigation, where high precision and stability are critical.
- Defense: Extensively used in missile guidance, unmanned military vehicles, and military navigation systems.
- High-End Robotics: Used in industrial robotics, surgical robots, and autonomous navigation systemswhere precision and long-term stability are necessary.
When to Choose MEMS IMU vs FOG IMU
Use Case | MEMS IMU | FOG IMU |
---|---|---|
Consumer Electronics | Ideal for smartphones, wearables, and fitness trackers. | Not suitable due to high cost and power consumption. |
Aerospace & Aviation | Suitable for low-cost, small systems with moderate precision requirements. | Essential for high-precision navigation and orientation systems. |
Autonomous Vehicles | Good for lower-cost solutions with moderate performance requirements. | Necessary for high-precision navigation in complex environments. |
Military & Defense | Used in **military drones**, **navigation systems** for **vehicles**, and **missile guidance systems**. | Used extensively for missile guidance, drones, and navigation in challenging conditions. |
Robotics | Suitable for consumer-grade robots or educational projects. | Preferred for industrial robots, surgical robots, and other precision-based systems. |
Inertial Measurement Unit (IMU) Performance and Calibration
The performance of Inertial Measurement Units (IMUs) can be influenced by various factors, such as sensor drift, temperature, and environmental conditions. To ensure optimal performance, it is essential to understand the key performance indicators (KPIs) of IMUs and the calibration methods used to enhance their accuracy.
IMU Performance Indicators
The performance of an Inertial Measurement Unit (IMU) is evaluated based on several key factors that directly influence its accuracy and reliability. Below are the most important performance indicators for IMUs:
Performance Indicator | Description |
---|---|
Bias Stability | The consistency of the IMU’s readings over time. A stable IMU will have minimal deviation in measurements. |
Scale Factor | The ratio between the actual physical movement and the IMU's output. Any errors in this ratio can lead to incorrect data interpretation. |
Noise | Random variations in the IMU's sensor readings. Low noise levels indicate higher accuracy in measurements. |
Random Walk | Describes the drift in the measurements over time. It refers to how much the measurement deviates from its true value due to random noise. |
Resolution | The smallest measurable change in the IMU's sensor readings. Higher resolution improves the accuracy of the measurements. |
Nonlinearity | The deviation from a straight-line relationship between input and output. Nonlinearities can cause errors at higher accelerations or angular velocities. |
Temperature Sensitivity | The variation in IMU measurements due to changes in ambient temperature. IMUs with low temperature sensitivity are more accurate in fluctuating environmental conditions. |
IMU Calibration Methods
Calibration is a vital process that helps improve the accuracy of an Inertial Measurement Unit (IMU) by correcting errors that may arise from sensor drift, misalignment, and other factors. IMU calibration typically involves three primary sensor systems: the accelerometer, gyroscope, and magnetometer. Each of these sensors requires specific calibration techniques to ensure accurate and reliable measurements.
1. Accelerometer Calibration
The accelerometer in an IMU measures linear acceleration along the X, Y, and Z axes. However, it is often subject to errors such as scale factor deviations, misalignments, and non-orthogonality of the axes.
Calibration Method | Description |
---|---|
Static Calibration | A common method where the IMU is placed in a known orientation (e.g., flat on a surface). By measuring the acceleration due to gravity (9.81 m/s²), the sensor errors can be corrected. |
Dynamic Calibration | Involves moving the IMU through different known accelerations and directions to correct for scale factor errors, bias, and misalignment between the axes. |
Temperature Compensation | Since accelerometers are temperature-sensitive, calibration also includes compensating for temperature variations that could cause measurement errors. |
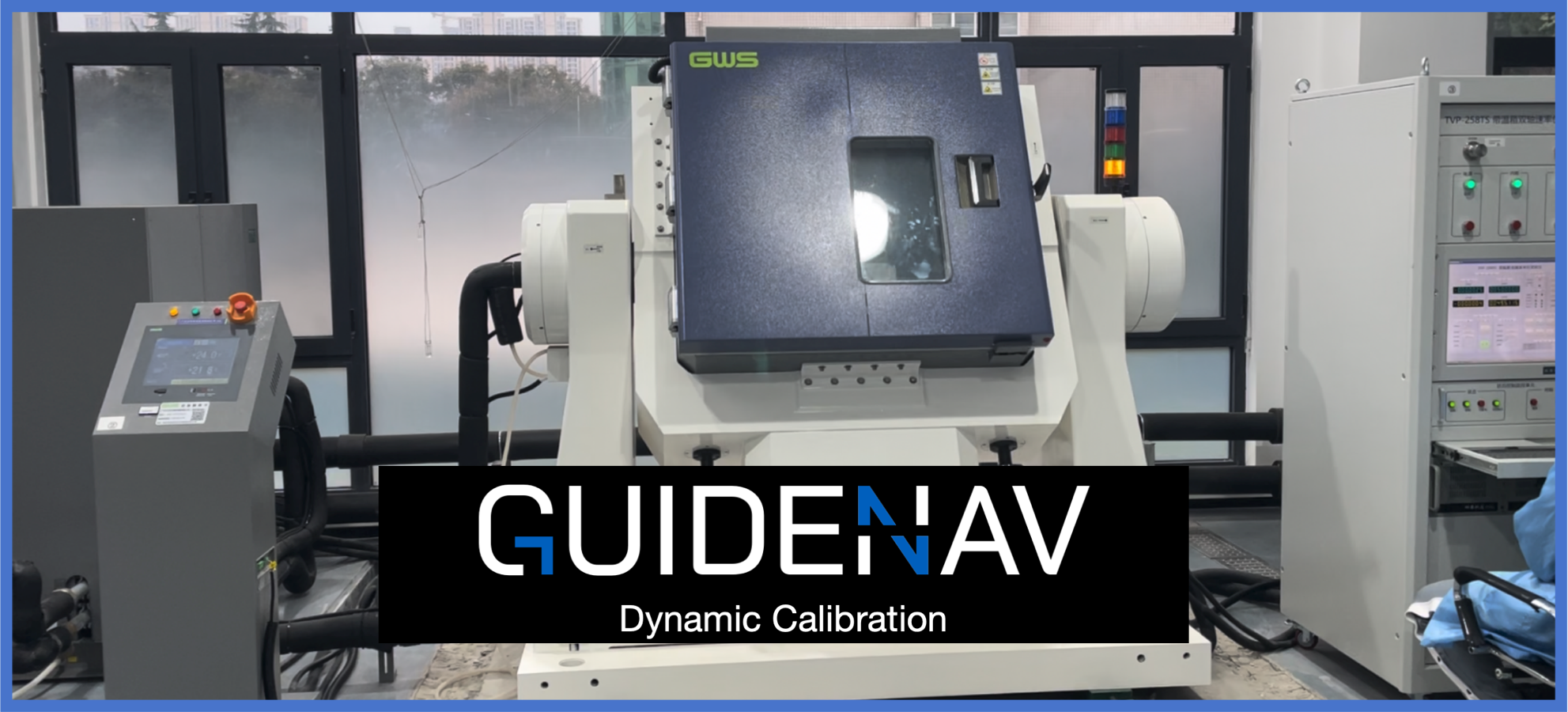
2. Gyroscope Calibration
The gyroscope measures the angular velocity around the IMU’s X, Y, and Z axes. Gyroscopes can suffer from drift (where the sensor readings slowly change over time) and bias instability (where there is a constant offset in measurements).
Calibration Method | Description |
---|---|
Zero-Rate Offset Calibration | In this method, the gyroscope is placed in a stationary position (no movement), and the offset or bias is measured and corrected. |
Rate Table Calibration | This involves rotating the IMU at different known angular velocities to determine any nonlinearity or scale factor errors. |
Temperature Calibration | Similar to accelerometers, gyroscopes are sensitive to temperature changes. Calibration accounts for variations in the sensor's behavior at different temperatures. |
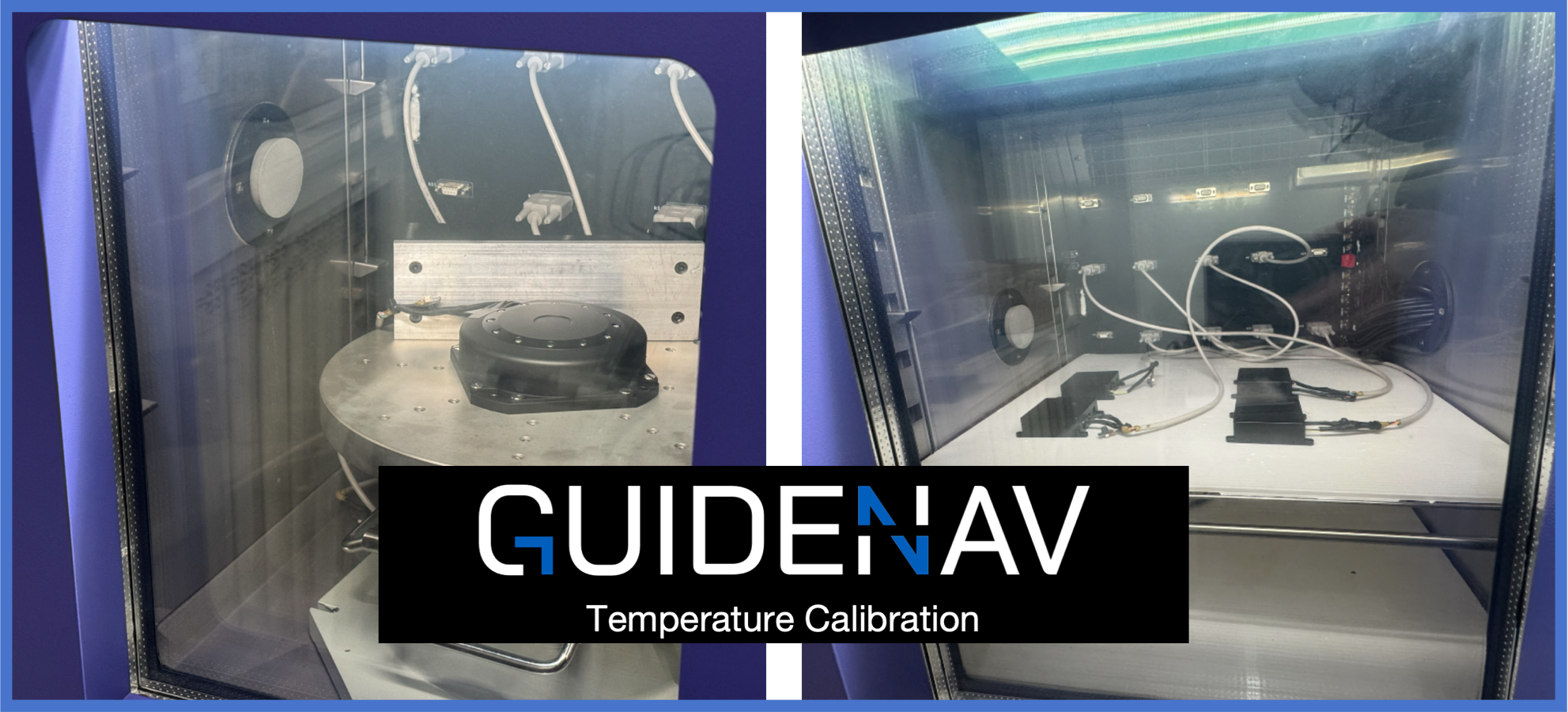
Calibrating the gyroscope ensures that the IMU’s angular velocity readings are accurate and free from drift, improving its performance in dynamic environments.
3. Magnetometer Calibration
The magnetometer measures the strength and direction of the Earth’s magnetic field, providing orientation data that is used for heading determination. Magnetometers can be affected by local magnetic disturbances, sensor misalignment, and errors in the scale factor.
Calibration Method | Description |
---|---|
Hard Iron Calibration | This method compensates for magnetic field distortions caused by the IMU’s own components (e.g., electronic devices). |
Soft Iron Calibration | Corrects for distortions caused by the surrounding environment or materials near the IMU. |
Multi-point Calibration | The magnetometer is exposed to a variety of known magnetic field strengths and directions to detect and correct for errors. |
Magnetometer calibration is essential for achieving accurate heading and orientation data, especially when the IMU is used in environments with varying magnetic conditions.
Advantages and Limitations of Inertial Measurement Units (IMUs)
Inertial Measurement Unitss offer exceptional real-time performance, independence from external systems, and are highly adaptable across industries. However, their drift, environmental sensitivity, and high-cost precision models need to be considered when choosing the right technology. MEMS IMUs strike a balance between cost and performance for many consumer and industrial applications, while FOG IMUs are the go-to choice for high-precision, long-duration tasks in aerospace and defense. Understanding the strengths and limitations of IMUs helps you select the best system for your specific needs.
Advantages of Inertial Measurement Units
Advantage | Description |
---|---|
High Precision in Dynamic Environments | IMUs provide real-time measurements of acceleration and angular velocity, essential for applications in autonomous vehicles, aerospace, and robotics, where GPS or other external references are unavailable. |
Independence from External Signals | IMUs operate without relying on external signals like GPS, making them highly reliable in environments such as underground navigation, space exploration, or indoor robotics. |
Compact and Lightweight | MEMS IMUs are small and light, ideal for applications like wearables, drones, and consumer electronics where space and weight are critical. |
Low Power Consumption | MEMS IMUs are energy-efficient, perfect for battery-powered devices like smartwatches and fitness trackers that need to operate for long periods. |
Real-Time Data Processing | IMUs deliver high-frequency, low-latency data, making them suitable for real-time control in robotics, drone stabilization, and vehicle navigation. |
Durability in Harsh Environments | FOG IMUs and some high-end MEMS IMUs can endure extreme conditions like high vibration, temperature variations, and shocks, making them ideal for military and aerospace applications. |
Limitations of Inertial Measurement Units
Limitation | Description |
---|---|
Drift Over Time | Gyroscopes in IMUs accumulate drift over time, leading to inaccurate measurements unless recalibrated regularly. This is a significant issue in long-duration applications. |
Environmental Sensitivity | IMUs are sensitive to environmental conditions like temperature and vibrations, which can introduce errors, especially in MEMS IMUs that are more prone to these disturbances. |
High Cost (for High-Precision Models) | While MEMS IMUs are cost-effective, high-precision IMUs such as FOG IMUs are expensive and may not be suitable for all applications due to their high cost and power consumption. |
Short-Term Accuracy vs Long-Term Stability | IMUs offer great short-term accuracy, but without external correction (e.g., GPS), they experience long-term instability—a challenge for high-precision navigation tasks over extended periods. |
Complexity in Data Fusion | IMUs often require sensor fusion (e.g., integrating GPS, magnetometers) to correct errors over time, adding complexity and computational load to the system. |
Limited Accuracy in High-Dynamics | In high-dynamic applications, MEMS IMUs may not match the precision of FOG IMUs, especially in applications like missile guidance or spacecraft orientation, which require ultra-high precision. |
Inertial Measurement Unit (IMU) vs Other Inertial Systems: IMU vs AHRS, IMU vs INS
Inertial Measurement Units (IMUs) are essential in many high-tech applications, but they are not the only systems available for measuring motion, orientation, and navigation. Attitude and Heading Reference Systems (AHRS) and Inertial Navigation Systems (INS) are two other commonly used systems that also rely on inertial sensors. While IMUs provide the fundamental data for both AHRS and INS, these systems offer additional capabilities and are designed for specific use cases. Let’s explore how IMUs compare with AHRS and INS.
IMU vs AHRS (Attitude and Heading Reference System)
IMUs and AHRS are both used for orientation and motion tracking, but they differ in terms of additional features and their respective use cases.
Parameter | IMU | AHRS |
---|---|---|
Definition | An **Inertial Measurement Unit (IMU)** measures acceleration and angular velocity, providing raw motion data. | An **Attitude and Heading Reference System (AHRS)** combines **IMU data** with additional sensors (e.g., magnetometers) to provide orientation and heading data. |
Components | Typically includes **accelerometers** and **gyroscopes**, sometimes **magnetometers**. | Uses **IMU data** (accelerometers and gyroscopes) plus **magnetometers** and sometimes other sensors (e.g., **GPS**, **barometers**). |
Output | Provides raw acceleration and angular velocity data. | Outputs orientation (attitude) and heading (compass direction) in a global frame (e.g., North, East, Down). |
Accuracy | IMUs provide accurate motion tracking but may suffer from **drift** over time due to sensor errors. | AHRS improves accuracy by using external references (magnetometers, GPS), reducing drift over time. |
Complexity | Simpler in design and operation, typically for basic motion tracking. | More complex due to the additional |
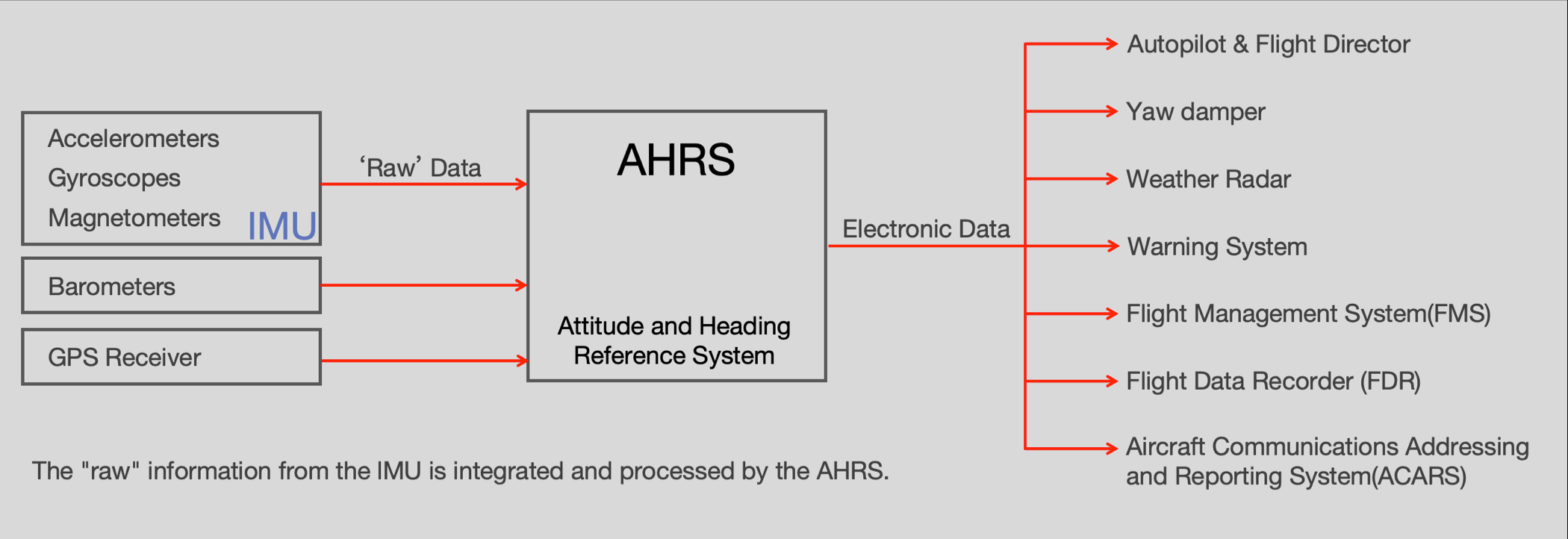
Key Difference: IMUs provide raw sensor data, while AHRS fuses this data with other sensors (like magnetometers) to offer precise orientation and heading. AHRS is typically used when precise attitude and heading information are required.
IMU vs INS (Inertial Navigation System)
An Inertial Navigation System (INS) is a more advanced system that integrates IMU data with additional processing capabilities, often using algorithms like Kalman filtering to compute the position, velocity, and orientation of an object.
Parameter | IMU | INS |
---|---|---|
Definition | An **Inertial Measurement Unit (IMU)** measures acceleration and angular velocity, providing raw motion data. | An **Inertial Navigation System (INS)** combines an **IMU** with computational processing (e.g., Kalman filter) to track position, velocity, and orientation. |
Components | Includes **accelerometers** and **gyroscopes**; sometimes **magnetometers**. | Combines an **IMU**, **algorithms** for sensor fusion, and sometimes other sensors (e.g., **GPS**). |
Output | Provides acceleration and angular velocity data. | Outputs **position**, **velocity**, and **orientation**, offering complete navigation data. |
Accuracy | IMUs have limited accuracy over time due to drift. | **INS** improves accuracy over time by fusing IMU data with algorithms and sometimes external corrections (e.g., GPS). |
Complexity | Simple, providing only motion data. | Complex due to data fusion, sensor processing, and the need for computational algorithms. |
Applications | Used for basic motion tracking, such as in drones, automotive, and robotics. | Used for **navigation** in **aircraft**, **submarines**, **spacecraft**, and **military applications**, where long-term position tracking is critical. |
Key Difference: While IMUs measure motion and orientation, INS uses that data along with algorithms to calculate position, velocity, and orientation over time, providing a full navigation solution.
Inertial Measurement Unit Market and Future Development: Types, Market Outlook, and Trends
Inertial Measurement Units (IMUs) are integral to modern navigation, motion tracking, and stability control systems across various industries. The growing demand for autonomous systems, robotics, aerospace, and consumer electronics has driven the evolution of IMU technologies, increasing their adoption worldwide. As the market for IMUs continues to expand, it is essential to understand the different types of IMUs, their current market conditions, and the trends shaping their future development.
Different Types of IMUs and Their Market Overview
IMUs come in various forms, each catering to different accuracy, size, cost, and performance requirements. The most commonly used types of IMUs are MEMS IMUs, FOG IMUs, and RLG IMUs (Ring Laser Gyroscope IMUs). Each has its unique characteristics, making it suitable for specific applications. Let’s look at these types and their current market scenarios.
1. MEMS IMUs
MEMS IMUs are the most widely used due to their compact size, low cost, and low power consumption. These IMUs rely on microelectromechanical systems (MEMS) sensors to measure acceleration and angular velocity. MEMS IMUs are highly suitable for consumer electronics, automotive applications, and low-cost systems.
Characteristic | MEMS IMU |
---|---|
Size | Compact, small, and lightweight. |
Cost | Low cost>, making them affordable for mass-market adoption. |
Precision | Moderate precision, though newer models achieve higher accuracy (e.g., **0.1°/hr**). |
Applications | Used in **consumer electronics**, **automotive systems**, **drones**, **robotics**, and **wearables**. |
Market Growth | Strong growth driven by **smartphones**, **automotive safety**, **drone technology**, and **IoT devices**. |
Market Outlook for MEMS IMUs:
The market for MEMS IMUs is expected to continue growing due to their affordability and versatility. These IMUs are increasingly used in smartphones, wearable devices, automotive safety systems, drone stabilization, and robotics. The automotive and consumer electronics sectors remain key drivers of growth, with the rising adoption of self-driving cars and IoT (Internet of Things) devices.
2. FOG IMUs (Fiber Optic Gyroscope IMUs)
FOG IMUs offer high precision and low drift, making them ideal for aerospace, defense, and navigation systems in environments requiring long-term stability and accuracy. FOGs use fiber optic technology to measure angular velocity and are known for their robustness in extreme conditions.
Characteristic | FOG IMU |
---|---|
Size | Larger and more robust than MEMS IMUs, designed for high-precision applications. |
Cost | **Higher cost**, making them suitable for specialized applications in **aerospace** and **military** sectors. |
Precision | **High precision** with minimal drift, ideal for **long-term stability** in **aerospace**, **defense**, and **navigation systems**. |
Applications | Used in **aerospace**, **military defense**, **high-end navigation systems**, and **precision guidance systems**. |
Market Growth | Steady growth in **aerospace**, **military**, and **high-precision navigation** sectors, but limited by high cost. |
Market Outlook for FOG IMUs:
The FOG IMU market is expected to grow steadily in aerospace, military defense, and high-precision navigation applications. The increasing demand for autonomous vehicles, space exploration, and missile guidance systems will drive FOG IMUs’ adoption. However, their high cost and power consumption remain limiting factors for broader market penetration, particularly in low-cost consumer applications.
3. RLG IMUs (Ring Laser Gyroscope IMUs)
RLG IMUs are similar to FOG IMUs but use ring laser gyroscopes to measure angular velocity. RLG IMUs are known for extremely high precision and stability, and they are often used in military, aerospace, and other high-performance sectors.
Characteristic | RLG IMU |
---|---|
Size | Similar to **FOG IMUs**, **larger** and more rugged, designed for **high-precision applications** in harsh environments. |
Cost | **Very high cost**, generally reserved for premium, mission-critical systems in **aerospace** and **military** industries. |
Precision | **Extremely high precision** with minimal drift, often used in **spacecraft navigation** and **military missile guidance** systems. |
Applications | Used in **military**, **spacecraft**, **satellite navigation**, and other **high-precision defense systems**. |
Market Growth | Although niche, **RLG IMUs** continue to be critical for **high-performance defense**, **aerospace**, and **space systems**. Market is stable with modest growth due to high costs. |
Market Outlook for RLG IMUs:
While the RLG IMU market is limited due to its high cost, it remains essential for military defense and aerospace applications, particularly for missile guidance and satellite orientation systems. RLG IMUs will continue to play a critical role in these sectors but may face competition from FOG IMUs and emerging technologies.
Future Trends and Development of Inertial Measurement Unit
The future of IMUs is marked by several key developments driven by advancements in sensor technology, data processing algorithms, and the growing demand for precision systems across various industries. Here are some of the key trends:
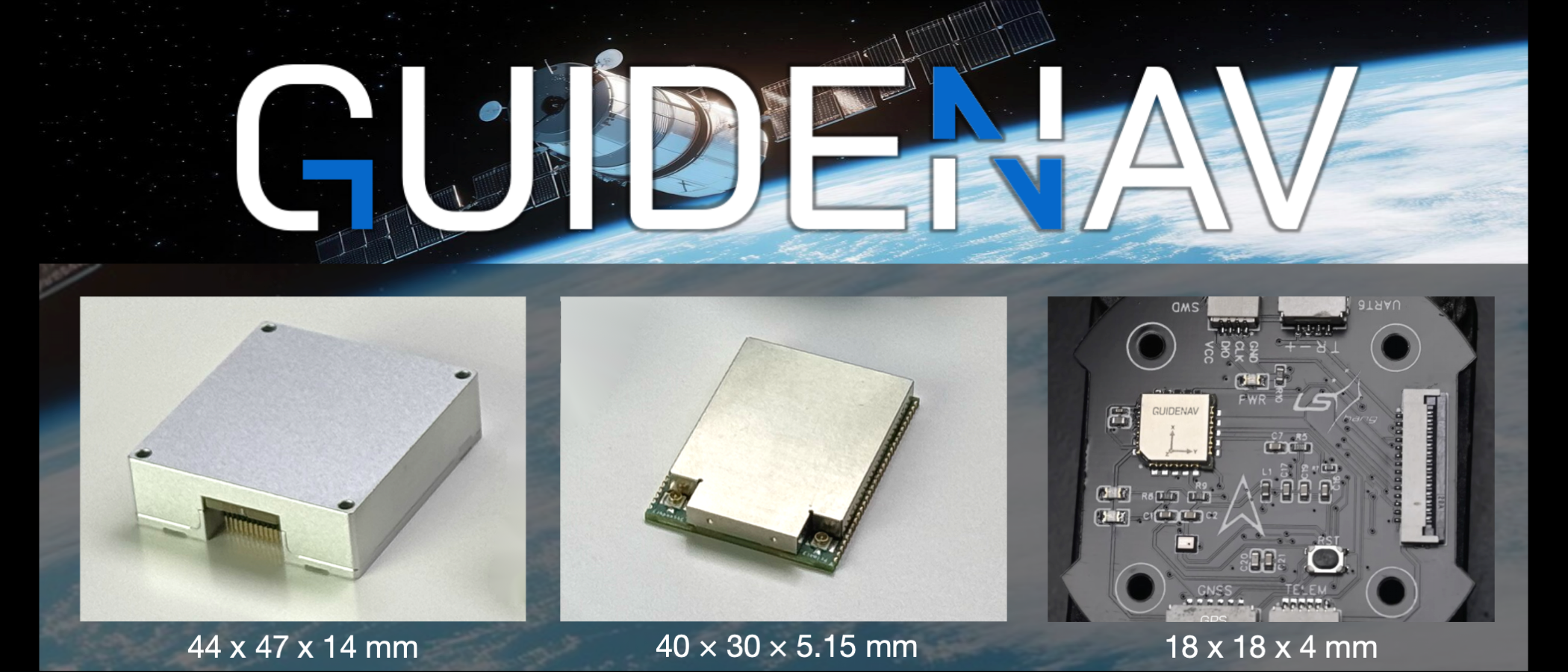
1. Miniaturization and Integration with Other Sensors
As the demand for compact and efficient systems rises, there is a growing trend toward miniaturizing IMUs. MEMS IMUs will continue to evolve, becoming even smaller, more cost-effective, and more powerful. Additionally, sensor fusion is a major development area, where IMUs are integrated with other sensors, like magnetometers, GPS, and barometers, to enhance performance and accuracy.
2. High Precision at Lower Cost
Recent advancements in MEMS IMU technology are driving a trend toward achieving high precision at a lower cost. Models like GUIDE900 and GUIDE900A can now achieve 0.1°/hr and 0.05°/hr accuracy, closing the gap with FOG IMUs. This means MEMS IMUs will be used in more high-precision applications, including aerospace and military systems, which were traditionally dominated by FOG IMUs.
3. Integration in Autonomous Systems
IMUs are integral to the development of autonomous vehicles, drones, and robotics. The growing interest in autonomous navigation and precision motion control will drive the demand for advanced IMUs. The integration of IMUs with AI algorithms and machine learning is enabling systems to adapt more effectively to real-world environments.
4. Use of AI and Sensor Fusion
AI algorithms will play an increasingly important role in IMU data processing. By combining IMU data with other sensor inputs and using machine learning, autonomous systems will be able to make more accurate predictions and adjustments. The combination of IMUs with technologies such as vision systems, LiDAR, and radar is expected to push the boundaries of real-time navigation and stabilization.
5. Improved Durability and Environmental Resilience
IMUs are expected to become even more robust and resilient to harsh conditions such as extreme temperatures, vibration, and electromagnetic interference. FOG IMUs and MEMS IMUs will evolve to meet the growing demand in aerospace, defense, and industrial applications.
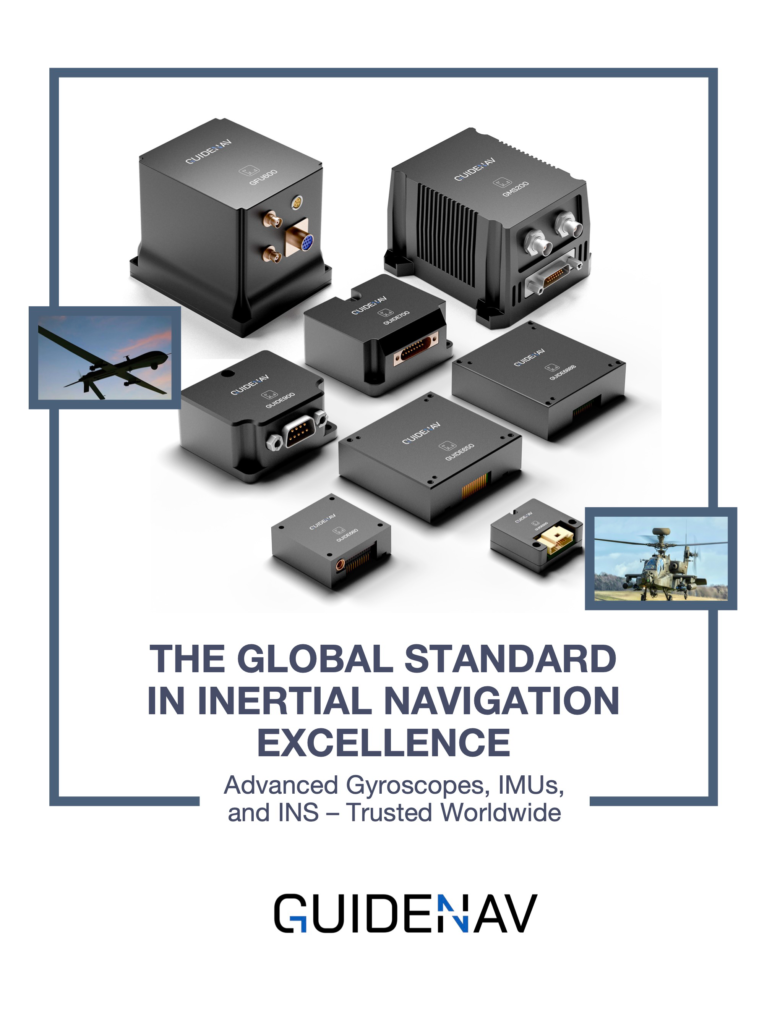