Table of Contents
- What an IMU is?
- What are the basic components of an IMU?
- What are the common applications of IMU?
- Why IMU is important in navigation and positioning systems.
- MEMS IMU: Overview of MEMS IMU and its applications.
- FOG IMU: Fiber-Optic Gyroscope IMU – use cases in high-precision applications
- MEMS and FOG gyroscopes – a brief comparison
- Bias Instability
- Initial Bias
- Range and Resolution
- Scale Factor and Scale Error
- Noise and Noise Density
- Bandwidth and Sample Rate
- Random Walk
- Factors to consider (performance specs, environment, size, cost).
- Understanding your application’s requirements (e.g., industrial, consumer electronics, automotive).
- Common mistakes to avoid when choosing an IMU.
Introduction
Inertial Measurement Units (IMUs) are the backbone of modern navigation systems. Whether in aircraft, missiles, self-driving cars, or even your smartphone, these sensors play a pivotal role in measuring motion and orientation without needing external references like GPS. Over the last two decades, the development of MEMS technology has drastically reduced their size and cost, making them indispensable across a broad range of industries.
In this comprehensive guide, I will walk you through the fundamentals of IMUs, including how they function, the different types of sensors they use, and why their performance metrics matter. From the latest aerospace innovations to consumer electronics, understanding what is IMU, how IMUs work is critical for anyone involved in designing or optimizing high-tech systems. By the end of this article, you’ll be well-equipped with the knowledge to select the right IMU for your project, ensuring you can meet even the most demanding requirements.
What is an Inertial measurement unit(IMU)/What is an IMU?
An Inertial Measurement Unit (IMU) is a sensor system that measures acceleration, angular velocity, and often magnetic fields to determine an object’s orientation and movement in space. It typically includes accelerometers, gyroscopes, and sometimes magnetometers. These components work together to provide crucial data for navigation, stabilization, and control in a wide range of applications, from aerospace and robotics to smartphones and autonomous vehicles. IMUs are essential in systems where precise movement and orientation data are required.
Let’s explore the world of IMUs in detail.
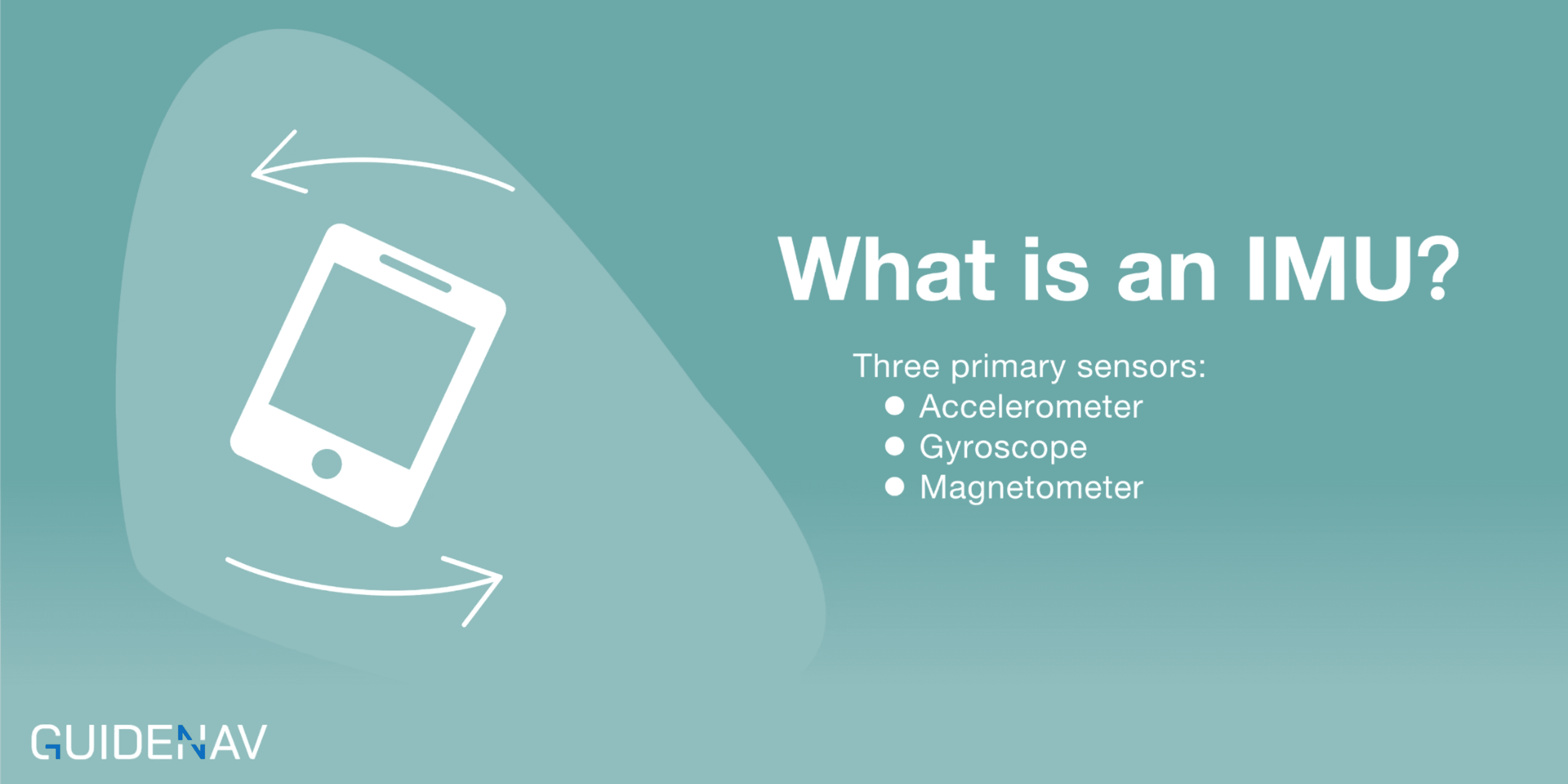
What is IMU Sensor Data?
The IMU sensor data consists of signals from three primary sensors:
- Accelerometers: Measure linear acceleration along the X, Y, and Z axes.
- Gyroscopes: Measure rotational velocity or angular velocity around the same axes.
- Magnetometers (optional): Measure the magnetic field to help with orientation in space, offering a compass-like functionality.
Each of these IMU sensors provides a stream of IMU data that, when combined and processed, gives a complete picture of an object’s movement and orientation. Typically, this data is used to derive important metrics like:
- Acceleration: Linear change in velocity.
- Angular Velocity: Rate of rotation around an axis.
- Orientation: The rotational position of an object in 3D space.
The precision and accuracy of IMU sensor data play a pivotal role in systems that require real-time tracking and navigation. When used in aerospace, defense, or industrial applications, the data can guide a spacecraft, aircraft, or robotic system with pinpoint accuracy.
What are the Basic Components of an IMU? /What is an IMU Sensor?
When we talk about an Inertial Measurement Unit (IMU), we’re really referring to a combination of several core sensors, each serving a critical function in measuring motion and orientation. The primary IMU sensors include accelerometers, gyroscopes, and, in many cases, magnetometers. These sensors work together to give us a comprehensive understanding of an object’s movement in space. Let’s break down how each of these sensors contributes to the IMU’s overall functionality.
The IMU’s core function is straightforward: it measures how fast an object is moving (linear acceleration) and how it’s rotating (angular velocity). This data is then used to calculate position, velocity, and orientation over time. Think of it as the internal “sense of balance” for machines. Whether it’s guiding a drone through the air, helping an autonomous car navigate, or stabilizing a smartphone screen, the IMU ensures that systems remain aware of their movements at all times.
IMU Accelerometer:What Does a Accelerometer Measure?
The accelerometer measures linear acceleration along one or more axes. In simple terms, it tells you how fast something is speeding up or slowing down. This is essential for calculating velocity and changes in position over time. For example, in a car, the accelerometer would measure the forces as the car speeds up, slows down, or makes sharp turns.
In my experience, accelerometers are the backbone of motion tracking in most systems. Whether you’re working with UAVs (unmanned aerial vehicles), smartphones, or industrial equipment, accelerometers provide the foundational data necessary for calculating movement.
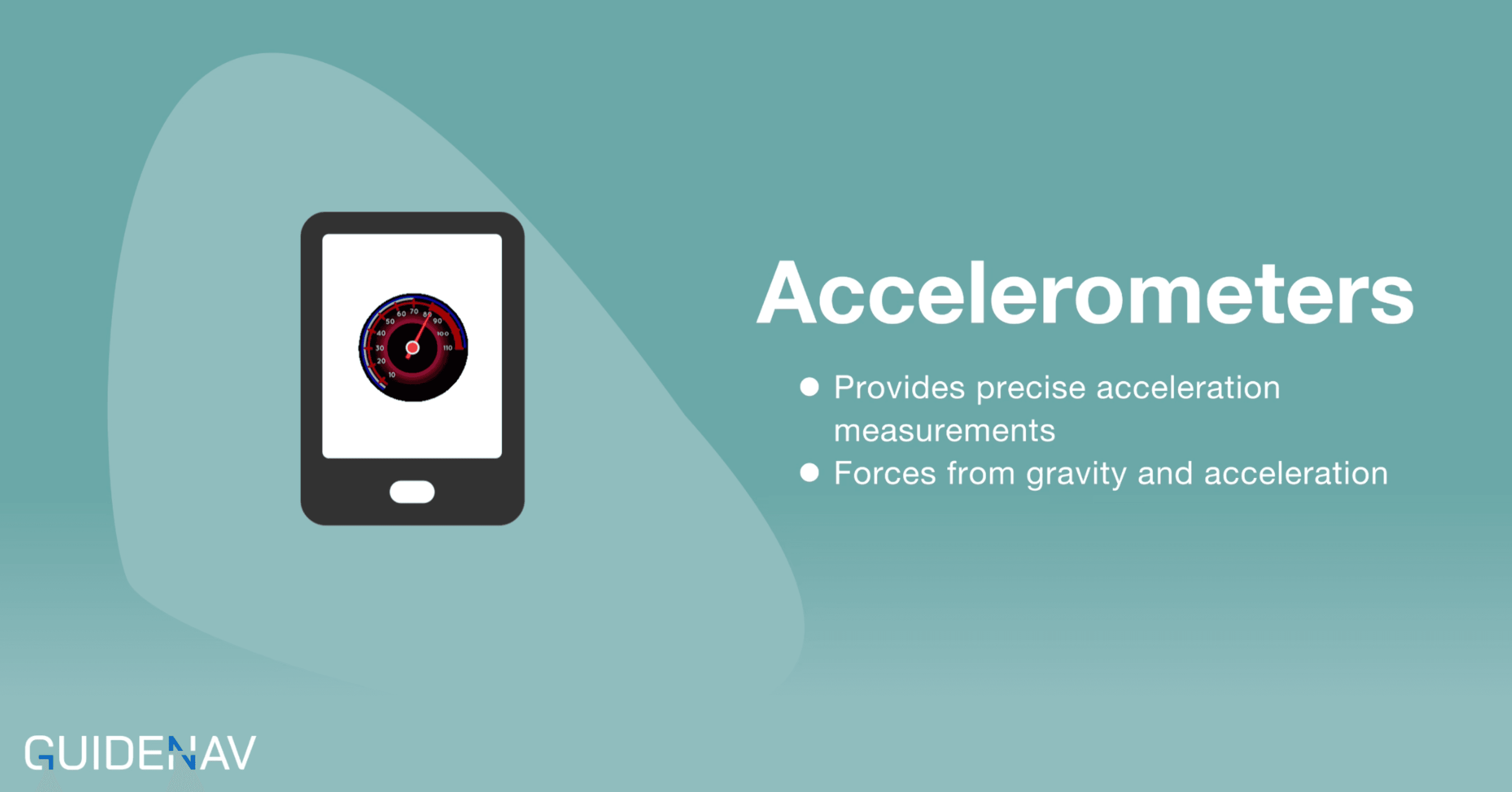
IMU Gyroscope: What Does a Gyroscope Measure?
The gyroscope of the IMU measures angular velocity—basically how fast an object is spinning around its axes. If you’ve ever seen a top spinning on a table, that rotation is exactly what a gyroscope detects. This sensor helps us determine the orientation of a device, which is particularly useful in stabilizing systems or tracking an object’s exact rotational movement.
I’ve seen gyroscopes play a vital role in navigation systems, especially in aerospace applications. When accuracy is key, a high-quality gyroscope ensures that orientation is tracked with precision, even when external factors—like turbulence—come into play.
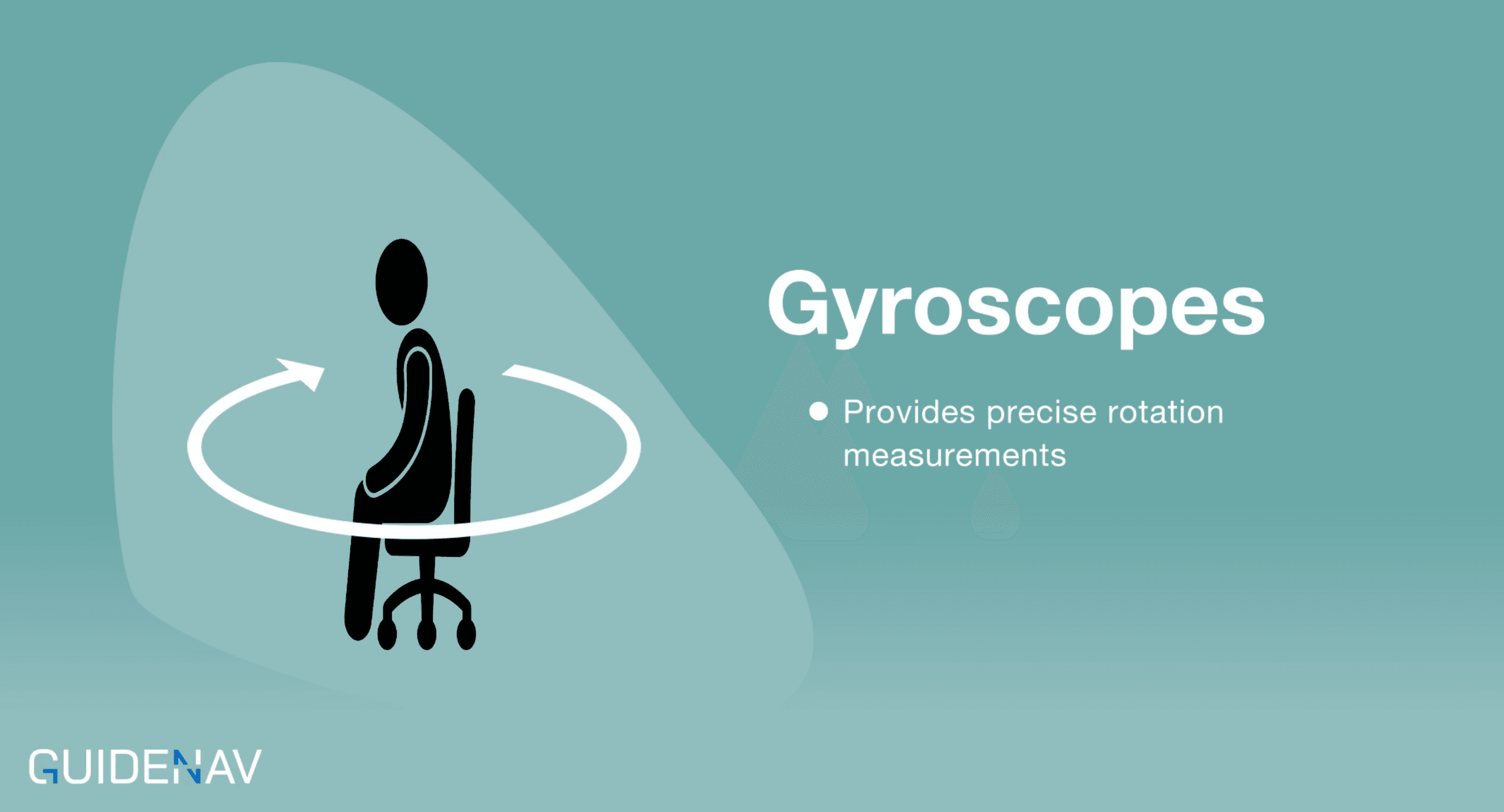
IMU Magnetometer: What Does a Magnetometer Measure
Finally, the magnetometer measures the magnetic field around the device, typically used to determine the heading or direction relative to the Earth’s magnetic field. Think of it as an electronic compass. While gyroscopes and accelerometers help track movement, a magnetometer enhances orientation accuracy by providing heading information relative to magnetic north.
I’ve found that the magnetometer is especially important in applications where GPS signals are weak or unavailable. For example, in dense urban environments, underground, or underwater, having an accurate sense of direction is crucial, and the magnetometer ensures you’re never “lost.”
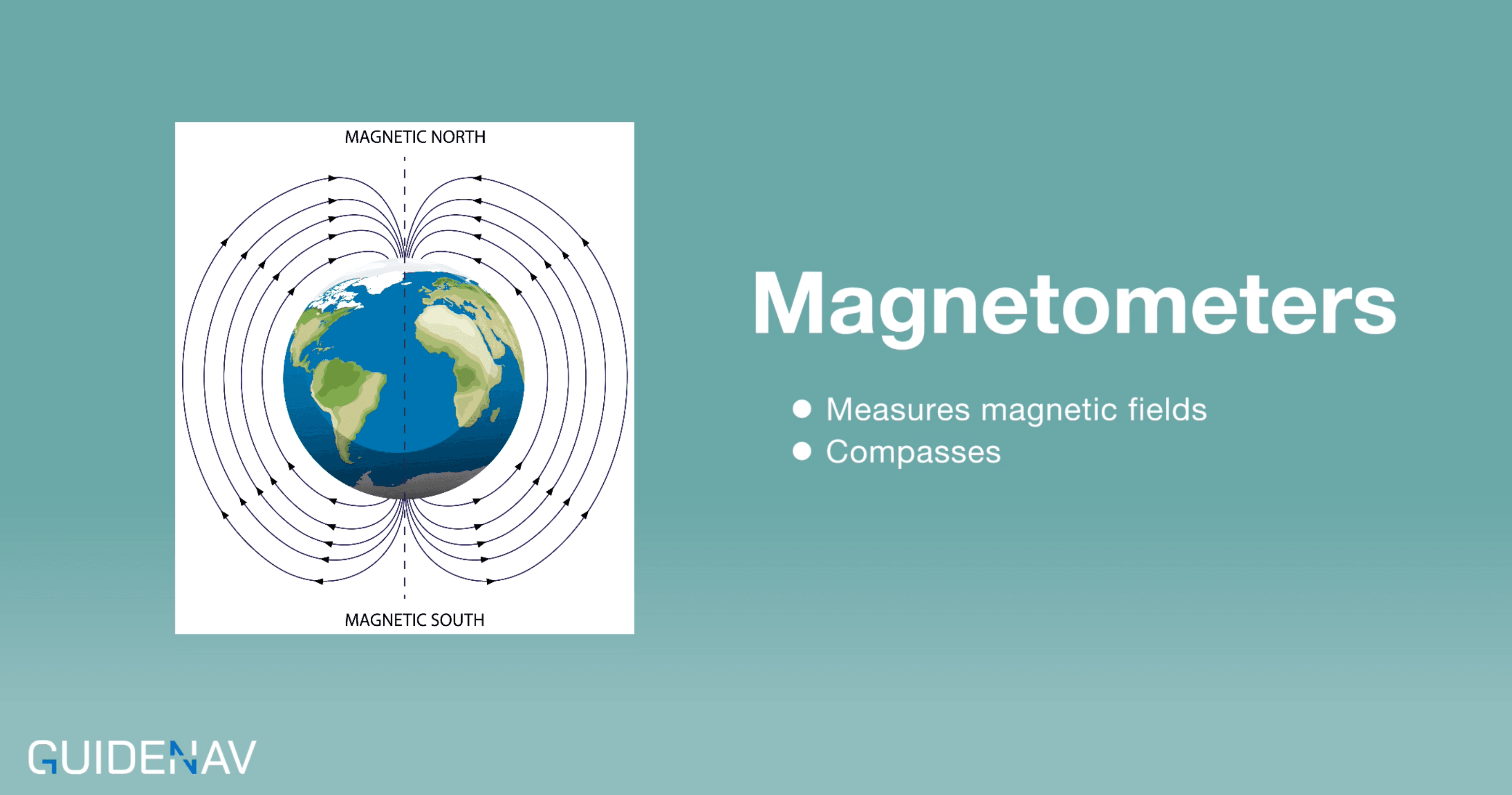
What are the Common Applications of IMU?
IMUs aren’t just confined to one specific field—they are used across a broad spectrum of industries. Their versatility is one of the key reasons they’ve become so integral to modern technology. Over the past 20 years, I’ve seen IMUs employed in everything from aerospace and automotive to consumer electronics, robotics, and defense/military. Here’s how they impact each sector:
Defense/Military
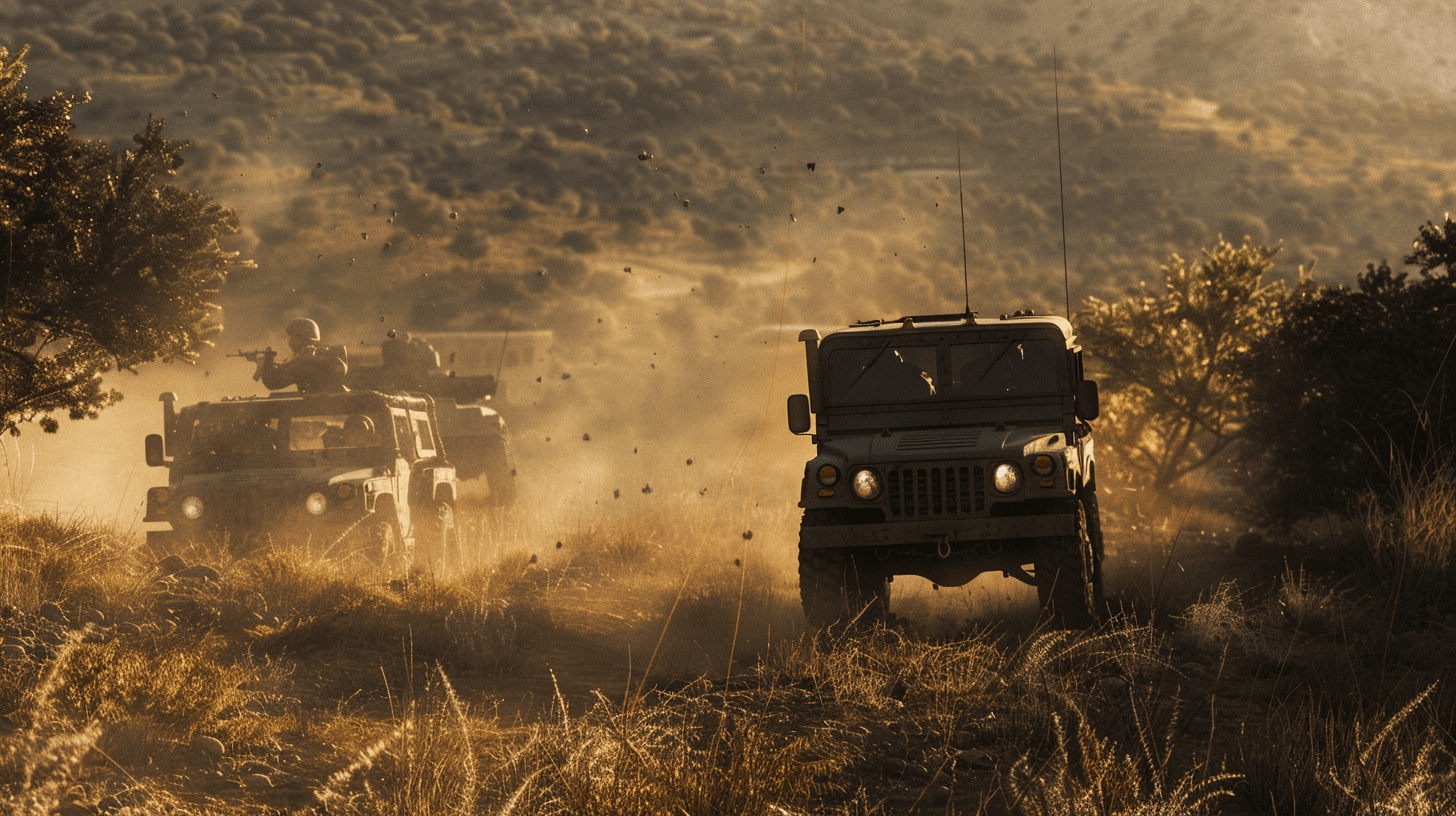
This is an industry where IMUs truly prove their worth. In defense and military applications, the need for precise navigation and stability is non-negotiable. From missile guidance systems to unmanned aerial vehicles (UAVs) and even soldier-worn devices, IMUs play an essential role in ensuring that operations proceed accurately and effectively.
I’ve been involved in several projects related to defense, and I can tell you firsthand that IMUs are critical in environments where failure is not an option. For example, in missile systems, the IMU provides real-time feedback on velocity and rotation, ensuring that the missile hits its target with precision. In UAVs, where GPS signals can be unreliable or jammed, IMUs provide the necessary inertial navigation to keep the craft on course.
Even at the soldier level, IMUs are embedded in tactical devices to track movement and location in the absence of GPS, helping provide situational awareness in complex terrains like dense urban environments or underground. IMUs are a key enabler of modern warfare’s increasing reliance on autonomous and semi-autonomous systems.
Aerospace
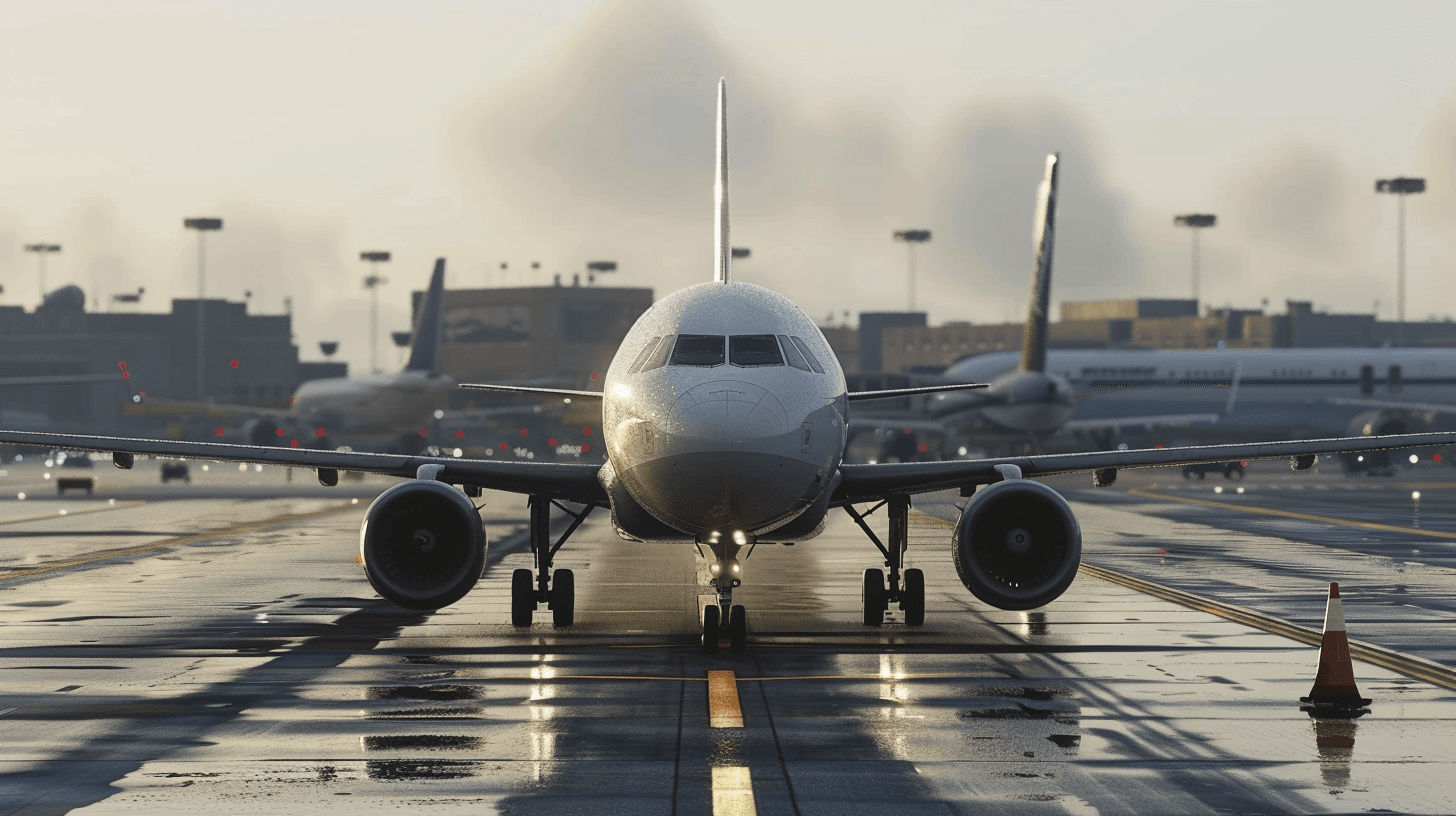
In aerospace, the importance of IMUs cannot be overstated. Whether in aircraft, spacecraft, or drones, IMUs provide the critical data necessary for navigation, control, and stability. They are essentially the backbone of autopilot systems, ensuring smooth flight paths and accurate landings.
When I’ve worked with aerospace clients, they often demand high-performance IMUs that can operate in extreme environments—think high altitudes or even outer space. The IMU keeps aircraft on course, adjusting for turbulence, wind shear, or other external forces. In space exploration, IMUs are essential for maintaining the orientation of satellites and rovers, where there’s no GPS to rely on.
Automotive
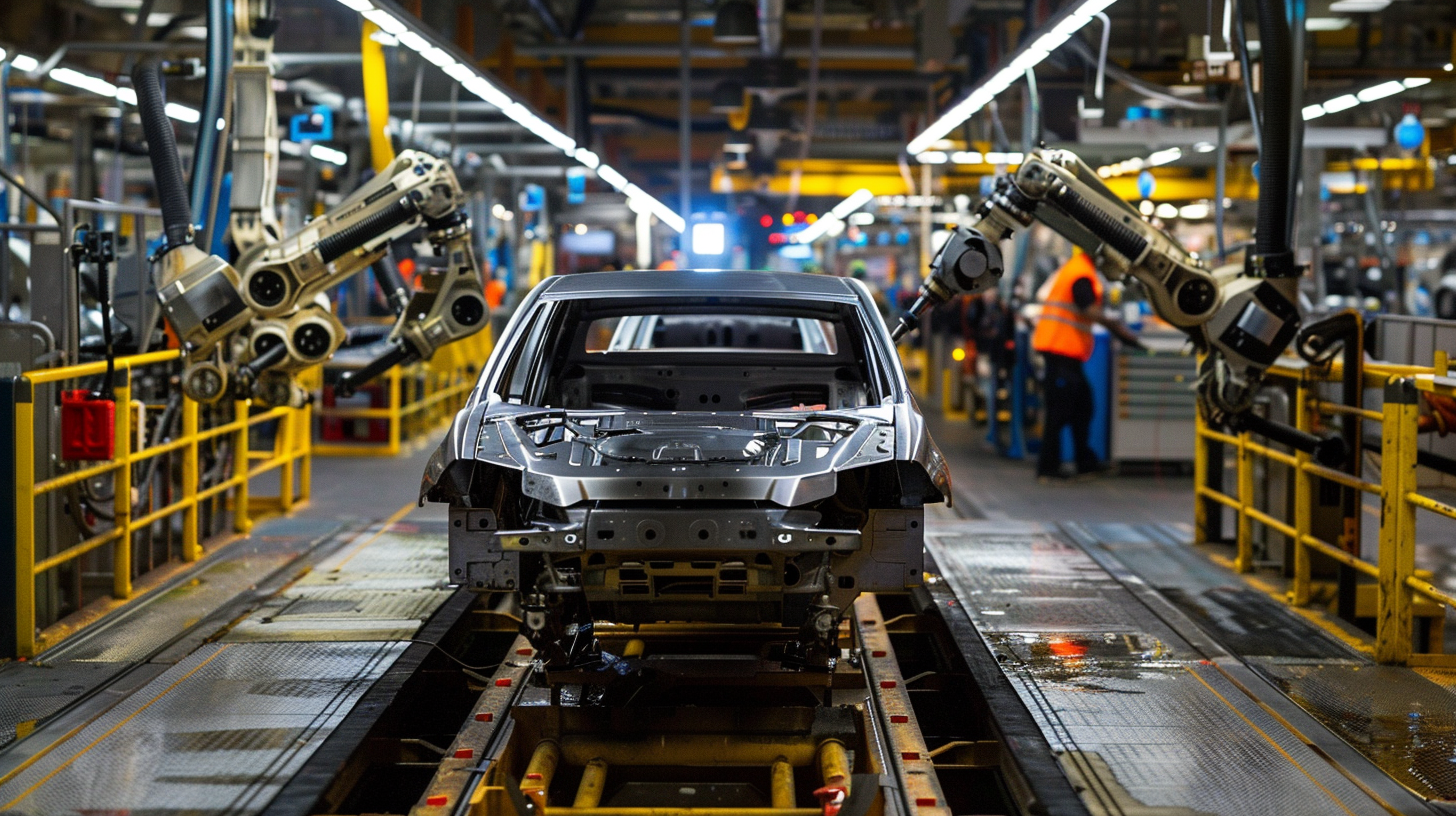
With the rise of autonomous vehicles, IMUs have become essential in the automotive industry. Self-driving cars rely on IMUs to understand their position and movement without human input. The IMU helps the vehicle make critical decisions in real time—whether it’s detecting when to slow down or taking a sharp turn safely.
In the development of Advanced Driver Assistance Systems (ADAS), IMUs play a pivotal role by feeding data to onboard systems. I’ve seen IMUs used in stability control, where they help detect and correct oversteer or understeer, and in automatic braking systems, where quick deceleration is vital to avoid accidents.
Consumer Electronics

In consumer electronics, IMUs have a more subtle but equally significant presence. They are in your smartphone, ensuring smooth screen rotation or powering motion-based games. In fitness trackers and smartwatches, IMUs track movement, monitor activity, and calculate steps or calories burned.
In several projects involving wearable technology, I’ve seen firsthand how much an IMU contributes to the user experience. The sensors inside fitness devices use accelerometers and gyroscopes to capture movements accurately, be it walking, running, or even swimming. IMUs ensure that these devices work seamlessly, providing users with accurate data they rely on daily.
Robotics
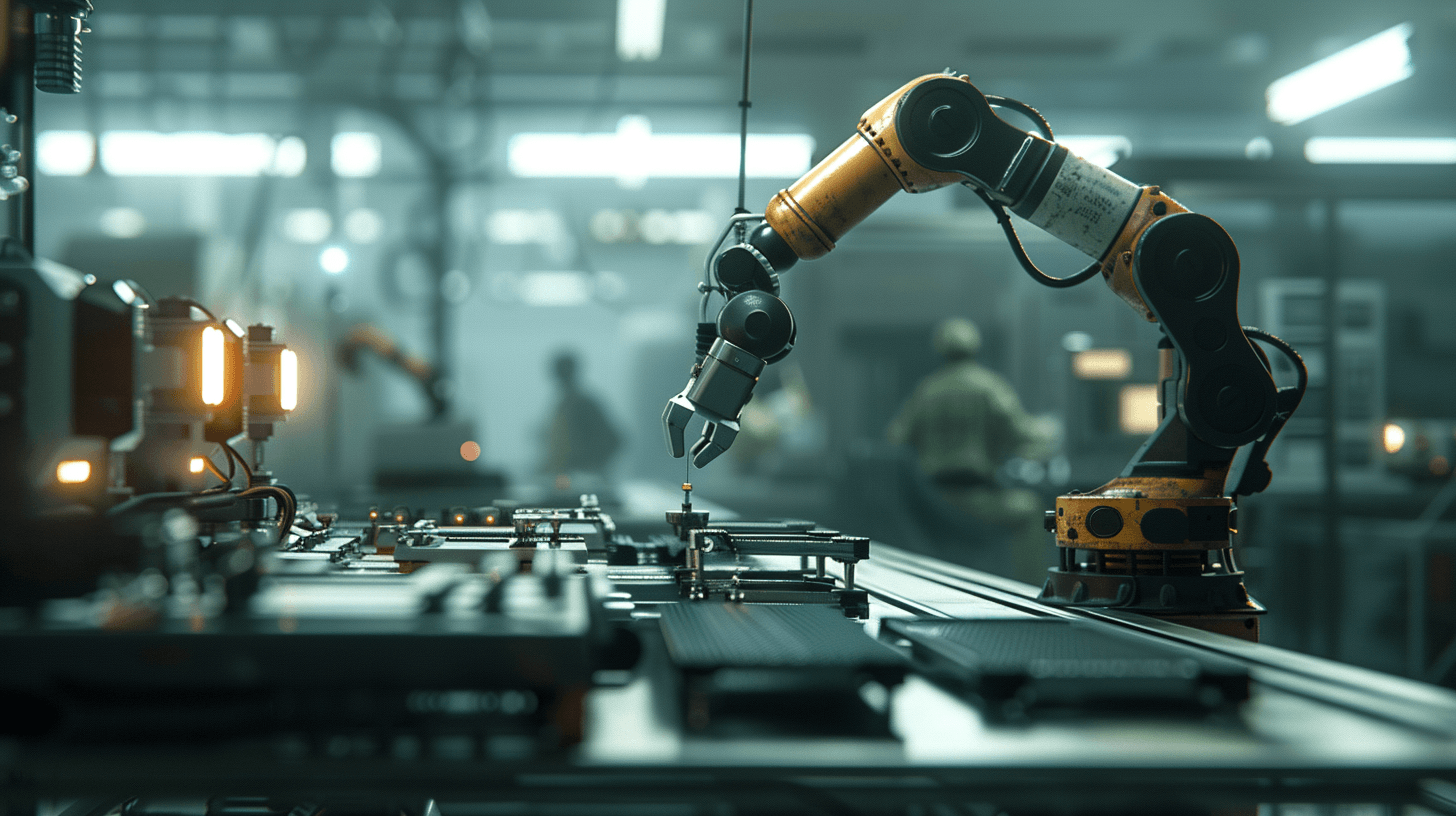
Robots, both industrial and autonomous, depend heavily on IMUs for precise navigation and control. In industrial settings, IMUs allow robots to move with precision on assembly lines, handling delicate parts with the utmost accuracy. For autonomous robots, whether they’re navigating a warehouse or exploring disaster zones, IMUs ensure they stay balanced and on course.
I’ve worked on multiple autonomous robotic systems where IMUs were key for balancing and movement. Without IMUs, these systems would lack the precision required for critical tasks like navigating uneven terrain, making them far less effective and reliable.
Why IMU is important in navigation and positioning systems?
In any system that requires precise navigation or positioning, the IMU is an indispensable tool. Over the years, I’ve seen the crucial role that IMUs play in keeping everything from UAVs to submarines on the right track. The core of its utility lies in its ability to measure movement without relying on external references.
GPS-Denied Environments
One of the most important aspects of an IMU is its capability to function in GPS-denied environments. Whether you’re deep underwater, underground, or in a dense urban area where GPS signals are unreliable, an IMU can still track movement with incredible accuracy. I’ve seen systems that continue to operate seamlessly in these environments, thanks to the IMU, which measures the changes in velocity and orientation continuously.
In aerospace, particularly with UAVs or military drones, relying solely on GPS can be risky. IMUs provide an additional layer of reliability by offering inertial navigation when GPS signals are lost or jammed. This redundancy is critical for both civilian and defense applications.
Positioning and Stabilization
Stabilization is another area where IMUs excel. Many systems, especially in aerospace and maritime sectors, require real-time adjustments to maintain stability. Whether it’s keeping a drone stable during flight or ensuring a camera gimbal remains steady while capturing footage, IMUs are the technology behind the scenes making it all possible.
We’ve worked with IMUs in many systems where real-time corrections are essential. For instance, in helicopters or aircraft, IMUs are constantly providing feedback to the autopilot, helping make micro-adjustments to compensate for wind gusts or turbulence.
Precision and Autonomy
In autonomous systems, like self-driving cars or robots, the need for precise navigation is paramount. IMUs help these systems understand their orientation, speed, and trajectory, even when external conditions are challenging. By feeding data to control algorithms, the IMU allows these machines to “know” exactly where they are and where they’re headed. This real-time awareness is what makes true autonomy possible.
In our work with autonomous systems, especially UAVs, we’ve seen how IMUs help calculate position accurately over time. Combined with sensor fusion technologies, the IMU enables these systems to adjust their paths and keep them on course without human intervention.
What Does IMU Look Like?
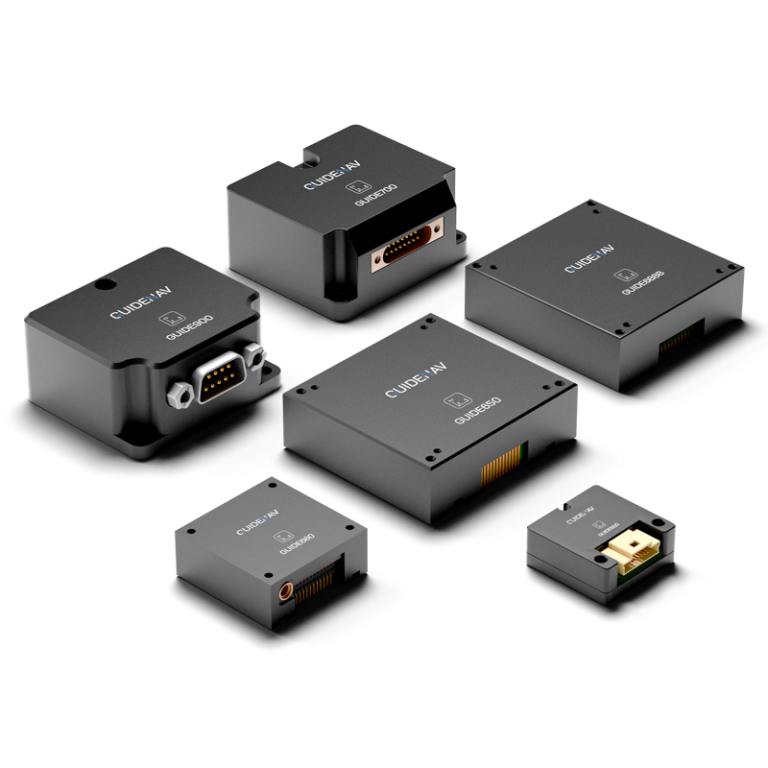
An Inertial Measurement Unit (IMU) is typically a compact device that integrates several sensors to measure an object’s acceleration, angular velocity, and sometimes magnetic fields. While the specific appearance of an IMU can vary depending on the manufacturer, model, and intended use, there are some general characteristics that most IMUs share.
Here’s a breakdown of what an IMU typically looks like:
1. Size and Shape
Most Inertial Measurement Unit (IMU) are relatively small and often rectangular or cuboid in shape. The dimensions can vary depending on the precision and application, but a general IMU used in consumer electronics might be about the size of a small coin or a thick matchbook. Industrial or aerospace IMUs can be larger, sometimes the size of a small laptop or a hard disk drive, depending on the complexity of the system.
2. External Housing
IMUs are usually housed in rugged, often sealed casings to protect the internal sensors from environmental factors such as moisture, dust, or impacts. The casing material is typically metal alloy or high-strength plastic, ensuring durability for harsh conditions (e.g., aerospace, military applications).
- Industrial and Aerospace IMUs may have a more robust, metallic casing to withstand extreme conditions.
- Consumer-grade IMUs (used in devices like smartphones or drones) tend to be housed in lighter, plastic enclosures.
3. Connectors and Ports
IMUs generally include connectors for power, data output, and sometimes communication interfaces (e.g., UART, I2C, SPI, or RS-232). These connectors allow the IMU to interface with other systems, whether it’s a drone’s flight controller, a robot, or an aircraft navigation system.
- For more complex systems, multiple ports for various signals may be visible.
- In some cases, wireless IMUs are used, reducing the need for visible connectors.
4. Sensor Placement
The internal components of an IMU—accelerometers, gyroscopes, and magnetometers—are typically embedded within the body of the unit. If you were to look at an IMU under a microscope or in a detailed schematic, you’d see tiny sensor chips (MEMS or piezoelectric devices) embedded within the device.
Types of Sensors in an IMU
When it comes to Inertial Measurement Units (IMUs), the sensors inside them are what really drive performance. Over the years, we’ve seen several sensor types used in IMUs, but MEMS and FOG technologies stand out due to their broad application across industries. Each sensor type comes with its own strengths and weaknesses, depending on the application and environment in which it’s being used. Below, I’ll break down both MEMS IMUs and FOG IMUs, then compare the two in terms of performance, cost, and reliability.
MEMS IMU: Overview of MEMS IMU and Its Applications
Micro-Electro-Mechanical Systems, or MEMS IMUs, have revolutionized the sensor world. By using tiny mechanical components on silicon chips, MEMS technology allows for highly integrated IMUs that combine accelerometers, gyroscopes, and sometimes magnetometers into one small, affordable package. This is why you’ll find MEMS IMUs in nearly every consumer device today, from smartphones to fitness trackers. In fact, they’ve become so prevalent that it’s hard to imagine modern electronics without them.
MEMS sensors are popular because they strike a balance between performance, size, and cost. They’re compact and energy-efficient, making them ideal for devices where space is at a premium. I’ve worked on several projects where MEMS-based IMUs were used in consumer electronics, wearable technology, and automotive systems—areas where you need good accuracy but not necessarily the highest precision available on the market.
However, MEMS IMUs have their limitations. While they are effective for many applications, they tend to drift over time and can be affected by environmental conditions like temperature fluctuations. For instance, in automotive safety systems, MEMS IMUs work well for short-term tasks like detecting sharp turns or sudden stops, but they may struggle in more demanding environments like aerospace, where precision over long durations is critical. That’s where we start to look at other technologies, such as FOG IMUs, when higher precision is necessary.
FOG IMU: Fiber-Optic Gyroscope IMU – Use Cases in High-Precision Applications
When we need to move beyond MEMS in terms of performance and precision, Fiber-Optic Gyroscopes (FOG) come into play. FOG IMUs are often used in aerospace, defense, and other fields where even the smallest error in measurement can lead to major consequences. These sensors are known for their high accuracy and long-term stability, characteristics that are crucial in environments where external forces like vibration or temperature shifts can severely impact performance.
Unlike MEMS, FOG IMUs use the properties of light to detect changes in angular velocity. A beam of light is passed through coils of optical fiber, and when the IMU rotates, this path changes, which allows the system to measure rotation with incredible precision. The key advantage of FOG technology is that there are no moving parts. This means fewer components that can wear down over time, which is why FOG IMUs are highly reliable and tend to last longer than MEMS-based systems.
FOG IMUs are perfect for missile guidance systems, unmanned aerial vehicles (UAVs), and even satellite navigation. In my experience working with high-precision aerospace projects, we often turn to FOG IMUs when we need a system that can function flawlessly in GPS-denied environments or under extreme conditions. The price point for FOG systems is higher, but for critical applications where failure isn’t an option, they’re worth every penny.
MEMS and FOG Gyroscopes – A Brief Comparison
Now, let’s look at how MEMS and FOG gyroscopes stack up against each other. Over the years, I’ve had the opportunity to work with both technologies, and it’s clear that each has its place depending on the use case.
- Precision: This is where FOG clearly shines. FOG gyroscopes are far more accurate, especially over long durations. They exhibit minimal drift, making them ideal for applications requiring sustained high precision, such as in aerospace or defense. On the other hand, MEMS gyroscopes offer good accuracy but can suffer from drift over time, which means they need recalibration more often in high-precision tasks.
- Size and Cost: MEMS IMUs are far more compact and cost-effective than FOG IMUs. This makes them the obvious choice for consumer electronics, automotive, and other commercial applications where size and budget are critical factors. FOG systems, while more expensive and bulkier, are preferred when absolute accuracy is required, and performance can’t be compromised.
- Durability: In terms of robustness, FOG systems have an edge, especially in harsh environments. Since they don’t have moving parts, they’re less prone to wear and tear, making them perfect for long-term deployments in rough conditions. MEMS, with its mechanical components, is durable enough for most consumer and industrial applications but tends to degrade faster under extreme conditions.
- Power Consumption: MEMS IMUs are more power-efficient, which is why they’re often found in portable electronics like smartphones and fitness trackers. FOG IMUs, on the other hand, consume more power due to the optical systems they use, making them less suitable for low-power applications but perfectly acceptable in areas like aerospace or defense, where power isn’t as limited.
IMU Performance Specifications Explained
When it comes to selecting the right Inertial Measurement Unit (IMU) for any given application, understanding its performance specifications is crucial. These specifications determine how well the IMU will perform in real-world conditions, particularly when accuracy and stability are key requirements. Over the years, we’ve seen firsthand how certain performance factors, like bias instability or noise density, can make or break a project—especially in fields like aerospace, defense, and high-precision robotics. Let’s walk through some of the key specifications that need to be carefully evaluated.
1. Bias Instability
Bias instability is one of those factors that often gets overlooked but has a significant impact in high-precision applications. Essentially, bias instability refers to the small, random variations in the sensor’s output when it should be reading zero. In simple terms, it’s the IMU’s “drift” when stationary.
In practical applications, bias instability matters because it affects how well the system can maintain accuracy over time. Imagine a missile guidance system or a satellite operating in space. Both rely on extremely accurate data over extended periods. Any drift caused by bias instability can lead to serious cumulative errors, resulting in the system veering off course. This is why, when working with clients in aerospace, we always place high importance on low bias instability—particularly for long-duration missions where even the smallest errors can have significant consequences.
2. Initial Bias
Initial bias is another critical factor that directly affects the long-term accuracy of an IMU. This refers to the sensor’s offset error at the moment of startup. Essentially, it’s the baseline error that exists before any measurements are even taken. If the initial bias is too high, it will impact the accuracy of all subsequent readings, making the entire system prone to errors.
This is especially important for applications where the IMU needs to run over long periods without recalibration. In systems like autonomous vehicles or drones, the IMU must provide accurate data throughout the duration of operation. Even a small initial bias can lead to significant errors over time if it’s not accounted for. That’s why, in high-precision systems, we always recommend calibrating the IMU at startup to correct for initial bias before it becomes a problem.
3. Range and Resolution
When selecting an IMU, range and resolution are two specifications that must always be considered together. The range defines the maximum measurable acceleration or angular velocity, while the resolution is the smallest change the sensor can detect.
If you’re working on a project where the IMU will experience high forces, such as in an automotive crash detection system or high-speed aerospace applications, a sensor with a large range is critical. The system needs to handle extreme conditions without saturating the sensor. On the other hand, if the IMU will be used in precision-guided equipment, such as surgical robots or UAVs, a high resolution is necessary to capture the smallest changes in movement.
We often need to strike the right balance between range and resolution depending on the application. In some cases, a wider range sacrifices resolution, which means fine details may be missed. However, for certain projects where precision is the top priority, we prioritize higher resolution, even if it means working within a more limited range.
4. Scale Factor and Scale Error
The scale factor is essentially the ratio between the output of the IMU and the actual physical input. Ideally, this should be a perfect match, but in reality, every sensor has a degree of scale error, which is the deviation from this ideal ratio.
Why does this matter? Because the scale factor directly influences the measurement accuracy. When the scale error is too high, it skews the readings, leading to inaccurate data being fed into the system. For instance, in a drone’s autopilot system, if the scale factor is off, the system might believe it’s flying level when, in fact, it’s slowly banking to one side. Over time, these errors accumulate, causing the drone to drift off course.
When we’re developing systems where precision is a top priority, we ensure that the IMUs we choose have a low scale error and high scale-factor stability. That way, we know that the measurements we’re relying on are accurate and consistent, even over long periods of operation.
5. Noise and Noise Density
Noise is an inherent characteristic of any sensor, and IMUs are no exception. It refers to the random fluctuations in sensor output that can obscure the actual signal. Noise density measures the level of this noise over a specific bandwidth.
In high-precision applications, such as robotics or satellite navigation, minimizing noise is critical. If the noise level is too high, it becomes difficult to distinguish between small, real movements and random fluctuations in the data. This is where noise density becomes a key specification—especially in dynamic environments where subtle movements need to be captured accurately.
For instance, in surgical robots that rely on sub-millimeter precision, high noise levels can introduce errors that compromise the entire operation. We’ve learned from experience that even a seemingly small amount of noise can snowball into bigger issues when accuracy is vital. Choosing an IMU with low noise density ensures that the sensor can pick up on the smallest changes without interference.
6. Bandwidth and Sample Rate
Bandwidth refers to the range of frequencies an IMU can accurately measure, while the sample rate is how frequently the IMU takes measurements. Together, these parameters determine how well the sensor can capture fast-moving, dynamic events.
For high-speed applications—think of drones or autonomous vehicles navigating through complex environments—higher sample rates and wider bandwidth are crucial. A low sample rate might miss critical details in fast-moving scenarios, leading to delayed or incorrect responses from the system. Imagine a self-driving car that doesn’t pick up a sudden swerve due to a low sample rate—it could be catastrophic.
In contrast, in less dynamic applications, such as structural health monitoring, the bandwidth and sample rate don’t need to be as high. The key here is to match the specifications of the IMU with the operational demands of the system. We’ve often found that too low of a sample rate results in missed details, while too high of a rate can overwhelm the system with unnecessary data. Striking that balance is crucial.
7. Random Walk
Random walk describes the small, random errors that accumulate in the IMU’s output over time. Even though each error might seem insignificant on its own, when aggregated, they can drift the system away from its true position or orientation.
Over long-term missions, like those involving UAVs or satellites, random walk can introduce significant positional errors. I’ve seen cases where a small random walk in an IMU sensor caused navigation systems to drift far off course after only a few hours of operation. In these types of projects, selecting an IMU with a low random walk is crucial to maintaining long-term accuracy.
Random walk becomes particularly problematic in GPS-denied environments, where the IMU can’t rely on external references to correct its drift. This is why we always recommend testing and evaluating the random walk performance of an IMU before deploying it in any high-precision, long-duration system.
How to Select the Right IMU for Your Application
Selecting the right Inertial Measurement Unit (IMU) can be tricky. Over the years, we’ve seen firsthand how choosing the wrong IMU can lead to significant project delays, cost overruns, or even failure. The key is understanding the specific needs of your application and aligning those with the performance specifications of the IMU. There isn’t a one-size-fits-all IMU—each project requires careful consideration of several factors. Let’s break down what you should look at when selecting the best IMU for your needs.
Factors to Consider: Performance Specs, Environment, Size, Cost
The first thing we always look at is the performance specifications. Not all IMUs are built the same, and understanding the specifications is critical to ensure the IMU can handle the requirements of your project. Key specs such as bias instability, noise density, sample rate, and range must align with your application’s demands. For instance, if you’re working on a high-precision aerospace project, you’ll need an IMU with minimal bias drift and high stability. On the other hand, if the IMU is going into a consumer electronics device, you might prioritize cost and size over extreme accuracy.
Equally important is the environment in which the IMU will operate. Will it be exposed to extreme temperatures, vibrations, or moisture? In defense or aerospace applications, where the IMU may be used in harsh or unpredictable environments, robustness becomes a key factor. Ruggedized IMUs are built to withstand these conditions, but they come at a higher cost and larger footprint. On the flip side, for more controlled environments, like inside a factory or consumer device, you may be able to use a lighter, less expensive IMU without sacrificing performance.
Size and cost are also crucial factors, particularly when dealing with compact or cost-sensitive applications. If you’re developing a wearable device or a compact drone, for example, the IMU’s size and power consumption are critical concerns. We’ve worked on plenty of projects where space constraints were non-negotiable, and selecting a smaller MEMS-based IMU was the right call. But remember, the trade-off with smaller, cheaper IMUs is often in performance—particularly in terms of long-term stability and precision.
Cost always comes into play, too. While high-end fiber-optic gyroscope (FOG) IMUs offer unmatched precision, they’re much more expensive than MEMS-based systems. Understanding the cost-performance trade-off is essential. If your application can tolerate some drift or needs recalibration over time, a less expensive MEMS IMU could be sufficient. But if you’re building something like a missile guidance system or a satellite, you’ll want to invest in the highest-performance IMU you can afford.
Understanding Your Application’s Requirements
Before making any decisions, we always advise taking a deep dive into the specific requirements of your application. Each industry and use case has its own set of demands, and the IMU should be selected accordingly. Here’s a quick breakdown of what to look for in different sectors:
- Industrial Applications: In industrial environments, robustness and durability are often key. IMUs used in machinery, manufacturing, or heavy equipment must withstand vibrations, dust, and wide temperature ranges. You also want an IMU that can provide real-time data with high precision to improve automation and control systems. We’ve found that for most industrial projects, a mid-range MEMS IMU can often hit the sweet spot between durability and performance.
- Consumer Electronics: For consumer devices like smartphones, fitness trackers, or VR headsets, the focus is usually on cost, size, and power consumption. These applications don’t need military-grade precision, but they do require small, low-power IMUs that can perform consistently. MEMS IMUs dominate this space because they’re inexpensive and energy-efficient, making them ideal for battery-powered devices. We’ve worked with a range of manufacturers in this sector and can confidently say that, for most consumer electronics, the biggest challenges are around power management and integration—not necessarily extreme accuracy.
- Automotive: In the automotive world, IMUs are becoming increasingly important for Advanced Driver Assistance Systems (ADAS) and autonomous vehicles. Here, precision and reliability are paramount, but so is cost-efficiency, given the scale of the industry. For these applications, you’ll need an IMU that can withstand temperature fluctuations and vibrations from the road while providing stable, real-time data. We often recommend automotive-grade MEMS IMUs that are specifically designed for these conditions, striking a balance between cost and reliability.
- Aerospace and Defense: For aerospace and defense, there’s no room for error. Whether guiding a missile, stabilizing a satellite, or navigating a UAV in GPS-denied environments, you need high-performance IMUs that can provide data with minimal drift over long periods. Fiber-optic gyroscope (FOG) IMUs or ring-laser gyroscopes (RLG) are typically used in these applications for their precision and long-term stability. These systems are more expensive and bulkier, but in high-stakes environments, they are worth the investment.
Common Mistakes to Avoid When Choosing an IMU
Over the years, we’ve seen some common mistakes that people make when selecting an IMU. Avoiding these pitfalls can save both time and money in the long run.
- Over-specifying or under-specifying the IMU: One of the most frequent issues we’ve encountered is the tendency to either over-specify or under-specify the IMU for the project. Some teams opt for the highest-end IMU on the market, thinking it will cover all bases, but that often leads to unnecessary costs and complexity. On the flip side, going for the cheapest option can result in performance issues, especially in high-demand environments. It’s crucial to balance the IMU’s specifications with the real needs of the application, rather than opting for extremes.
- Ignoring environmental factors: We’ve seen projects fail because teams didn’t account for the operating environment. IMUs are sensitive to temperature changes, vibrations, and other external conditions. Selecting an IMU that isn’t designed to operate in your specific environment can lead to calibration drift, failure, or inaccurate data. Always ensure that the IMU is built to handle the conditions it will face in real-world use.
- Not considering future scalability: It’s easy to focus on immediate project needs, but if the application is part of a larger system or product line, scalability should be considered. Whether you’re planning to expand into higher precision tasks or integrate with more advanced control systems, choosing an IMU that can scale with future demands can save time and resources later.
- Overlooking data processing requirements: A mistake that often comes up is failing to consider the computational load required to process the IMU’s data. High-performance IMUs generate a significant amount of data that needs to be processed in real-time. If the system’s computational resources aren’t prepared for this, the IMU’s full potential won’t be realized. Ensure that your application has the necessary processing power and algorithms to handle the incoming data.