Table of Contents
- What is a FOG?
- What are the Basic Components of a FOG?
- Visual Breakdown of FOG Components
- Common Applications of Fiber Optic Gyroscopes (FOGs)
- Why Fiber Optic Gyroscopes (FOGs) Are Crucial in Navigation and Positioning Systems
- Real-World Benefits of FOGs in Navigation and Positioning Systems
- Bias Instability
- Drift
- Size, Power, and Cost Efficiency
- Environmental Resilience and Outdoor Application
- Dynamic Range
- Bias Instability
- Angle Random Walk (ARW)
- Scale Factor Linearity and Repeatability
- Temperature Compensation Range
- Define Your Application Requirements
- Prioritize Bias Instability and Drift Requirements
- Consider Dynamic Range and Angle Random Walk
- Evaluate Temperature Compensation Range
- Balance Size, Power, and Cost Considerations
- Comparison of GuideNav FOG Models
- Related article links
Introduction
Traditional gyroscopes, while serviceable in some settings, often fall short in harsh environments or mission-critical applications. That’s where FOGs truly shine. I’ve spent over 15 years immersed in this field, and I can tell you that few technologies compare to the reliability of fiber optic gyroscopes (FOGs) when accuracy, durability, and stability are on the line.
In this complete guide, I’ll walk you through the basics of FOGs, their core components, and how to choose the right one for your needs. Read on to understand FOG technology’s transformative capabilities and learn how it stands apart from conventional gyroscopes, as well as what factors to consider when selecting a FOG for your specific application.
What is a Fiber Optic Gyroscope (FOG)?
A fiber optic gyroscope (FOG) is a precision sensor that measures rotation using the Sagnac effect, where light in coiled optical fibers detects changes in angular velocity. This non-mechanical gyroscope offers high stability and accuracy in challenging environments, making it ideal for applications like aerospace navigation, satellite attitude control, robotics, and autonomous vehicles.
Unlike traditional gyroscopes that rely on physical spinning parts, FOGs are solid-state devices. They are inherently more robust, withstanding high levels of vibration, shock, and temperature variations. This stability has made FOGs indispensable in fields where dependable, long-term accuracy is crucial.
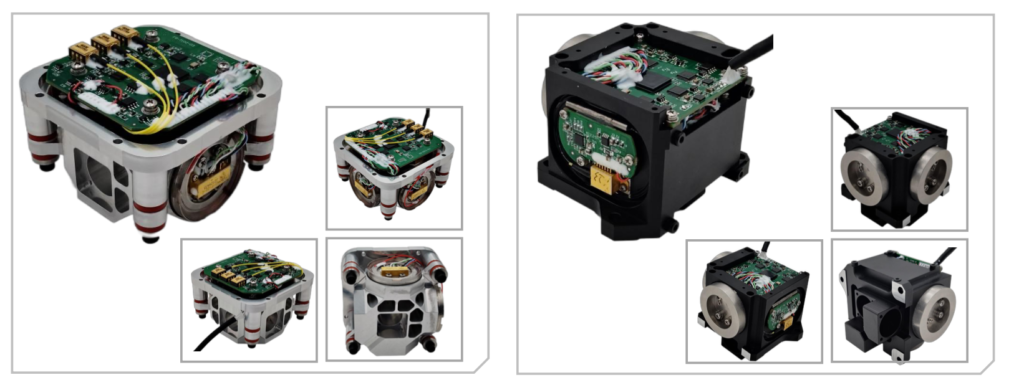
What are the Basic Components of a FOG?
The basic components of a fiber optic gyroscope (FOG) are fascinatingly precise and efficient, designed to provide exact angular velocity measurements with minimal drift. Over my years in this industry, I’ve had the chance to break down these components countless times, and each one plays a vital role in the FOG’s performance. Let me walk you through the essential parts that make up a FOG and explain why they’re so crucial to its function.
Component | Description | Function |
---|---|---|
Optical Fiber Coil | A long, coiled optical fiber where light travels in opposite directions to detect rotation. | Detects phase shifts, allowing precise rotation measurement. |
Laser Diode | The light source, typically a stable laser that produces coherent light. | Provides the consistent light beams needed for accurate measurements. |
Beam Splitter and Couplers | Devices that split the laser light into two beams and direct them through the coil. | Routes light beams in opposite directions for interference measurement. |
Photodetector | A sensor that captures the returning light after it travels through the coil. | Detects any phase shift caused by rotation. |
Signal Processing Unit | System that converts phase shift data into usable angular velocity information. | Processes data for real-time rotational feedback. |
Now, let’s go a bit deeper into each one.
1. Optical Fiber Coil
The optical fiber coil is the heart of a FOG, where the real magic happens. This coil is usually hundreds of meters long and tightly wound. The fiber allows light beams to travel in opposite directions, creating a sensitive measurement system for detecting rotation through the Sagnac effect.
The length of this fiber and its quality directly impact the FOG’s accuracy. Typically, longer fiber coils offer greater sensitivity to rotation because they increase the distance over which the phase shift can occur.
Example: High-end FOGs might use up to 1 km of fiber wound into a compact, stable coil to achieve ultra-low drift.
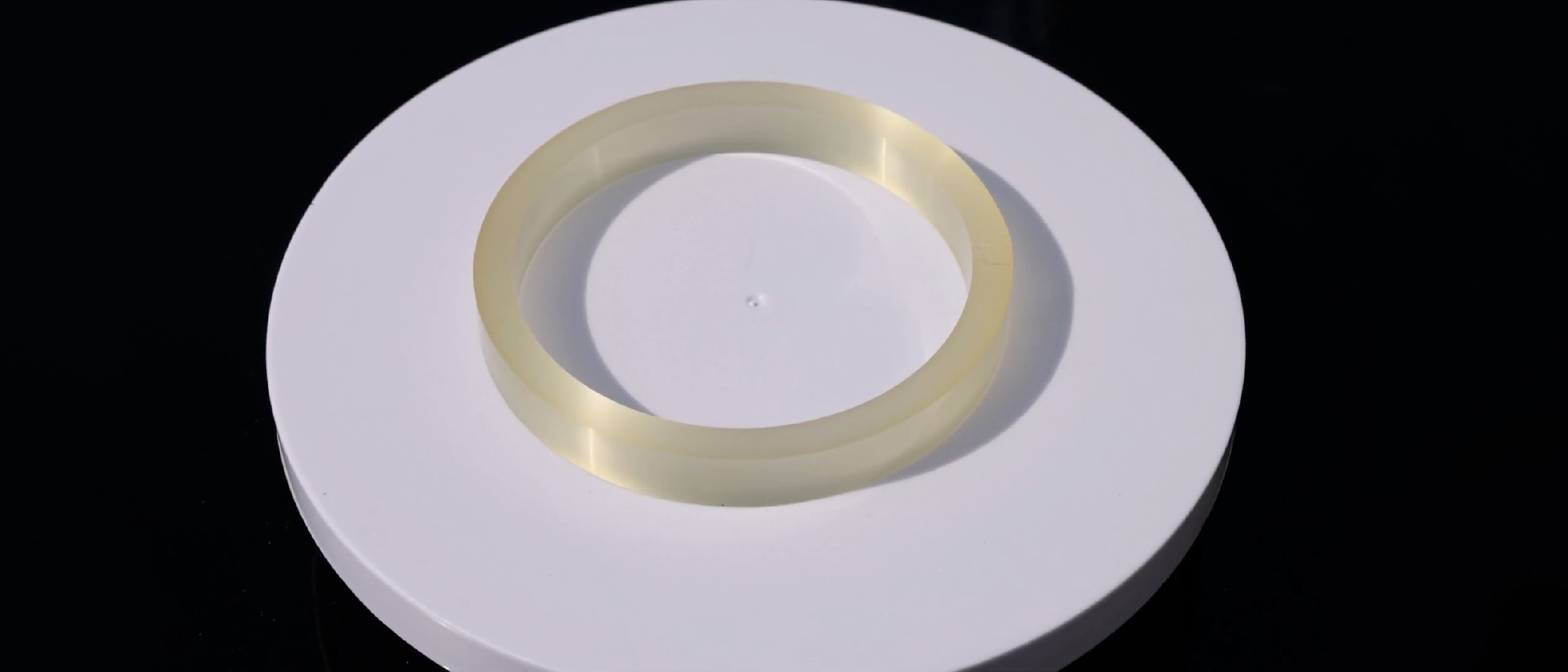
2. Laser Diode
The laser diode serves as the FOG’s light source. It emits a stable, coherent beam necessary for precise phase measurements. The stability and consistency of this laser are critical, as any variation in the light source could introduce noise, affecting the gyroscope’s accuracy.
Technical Insight: The wavelength stability of the laser directly affects the phase shift detection. For this reason, many FOGs use lasers with strict wavelength controls to keep readings consistent.
3. Beam Splitter and Couplers
The beam splitter divides the laser light into two identical beams. One beam travels clockwise, while the other travels counterclockwise through the optical fiber. Couplers then direct these beams into the optical fiber coil. These components must be precisely aligned to ensure that each beam follows the correct path without loss or interference.
Real-World Example: In defense or aerospace applications, beam splitters and couplers are carefully selected and tested to maintain alignment in harsh conditions, like high-vibration environments or extreme temperatures.
4. Photodetector
The photodetector captures the two light beams as they exit the fiber coil. Here, it detects any phase difference between the clockwise and counterclockwise beams—a difference that indicates the rate of rotation. This component must be highly sensitive to detect even the smallest phase shifts, which are often in the range of nanometers.
Expert Tip: A high-quality photodetector is essential for applications requiring low drift. Even minor inaccuracies in phase detection can accumulate over time, affecting the FOG’s stability.
5. Signal Processing Unit
The signal processing unit is where data becomes meaningful. It converts the phase shift detected by the photodetector into a rotation rate, often using advanced algorithms to filter noise and provide accurate readings. This processed data is then output to the system in real time.
For precision applications, signal processors are often equipped with error-compensation algorithms. This allows the FOG to self-correct, accounting for environmental factors that might impact accuracy.
Number | Content |
---|---|
01 | Recursive Least Squares Method, Derivation of the Kalman Filter Equations |
02 | Discretization of Continuous-Time Systems, Continuous-Time Kalman Filtering, Kalman Filtering under Noise Correlation Conditions, Sequential Filtering |
03 | Information Filtering and Information Fusion, Square Root Filtering |
04 | Forgetting Filtering, Adaptive Filtering, Measurement Fault Detection and Robust Tracking Filtering, Filtering Smoothing, Extended Kalman Filtering/Second-Order Filtering/Iterative Filtering |
05 | Unscented Kalman Filtering, Federated Filtering |
06 | Filter Stability Analysis, Error Distribution and Observability Analysis of State Estimation, Minimum Variance Estimation and Linear Minimum Variance Estimation |
07 |
Maximum Likelihood Estimation, Maximum A Posteriori Estimation, Weighted Least Squares Estimation, Wiener Filtering, Recursive Bayesian Estimation Strapdown Inertial Navigation Section: Vectors and Their Skew-Symmetric Matrices, Direction Cosine Matrices, Equivalent Rotation Vectors |
08 | Differential Equations of Attitude Matrices and Their Solutions, Differential Equations of Quaternions and Their Solutions, Differential Equations of Equivalent Rotation Vectors and Their Taylor Series Solutions |
09 | Multi-Subsample Optimization Algorithms under Conical Motion Conditions, Earth's Shape and Gravity Field |
10 | Complete Numerical Update Algorithms for Strapdown Inertial Navigation, Error Propagation Equations, Initial Alignment, SINS/GNSS Integrated Navigation |
Visual Breakdown of FOG Components
Here’s a simplified diagram to illustrate how these components interact within a FOG:
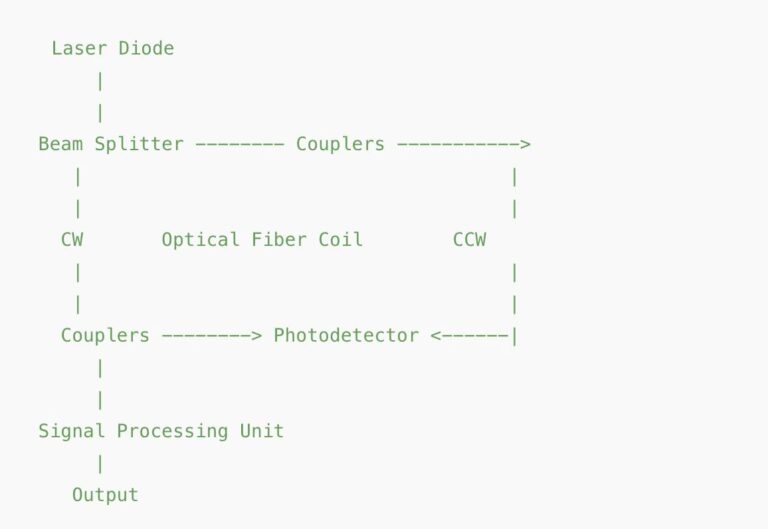
Common Applications of Fiber Optic Gyroscopes (FOGs)
Application Area | Specific Uses | Key FOG Benefits in This Field |
---|---|---|
Aerospace & Aviation | Aircraft navigation, satellite stabilization | High accuracy, low drift, resilience in extreme conditions |
Defense & Military | Missile guidance, tank navigation, UAVs and drones | Shock resistance, reliability, precise orientation |
Marine & Submarine | Submersible navigation, ROVs, ships | Low maintenance, accuracy in GPS-denied environments |
Autonomous Vehicles | Self-driving cars, industrial drones | Accurate, drift-free orientation, critical for complex environments |
Industrial Robotics | Robotic arms, automated machinery | Precision and stability during high-speed operations |
1. Aerospace & Aviation
FOGs have become essential in aviation, where reliability and precision are non-negotiable. In aircraft, for instance, navigation and orientation must remain stable regardless of rapid altitude changes or turbulence. FOGs, with their low drift and high precision, deliver consistent data essential for flight control systems. In satellites, FOGs maintain orientation in the vacuum of space, where temperature and vibration resistance are vital.
- Key Features for Aviation:
- Low driftensures data accuracy over extended flight times.
- Temperature resiliencehandles extreme fluctuations in altitude.
- Long operational lifereduces the need for maintenance, which is crucial in high-altitude or orbital applications.
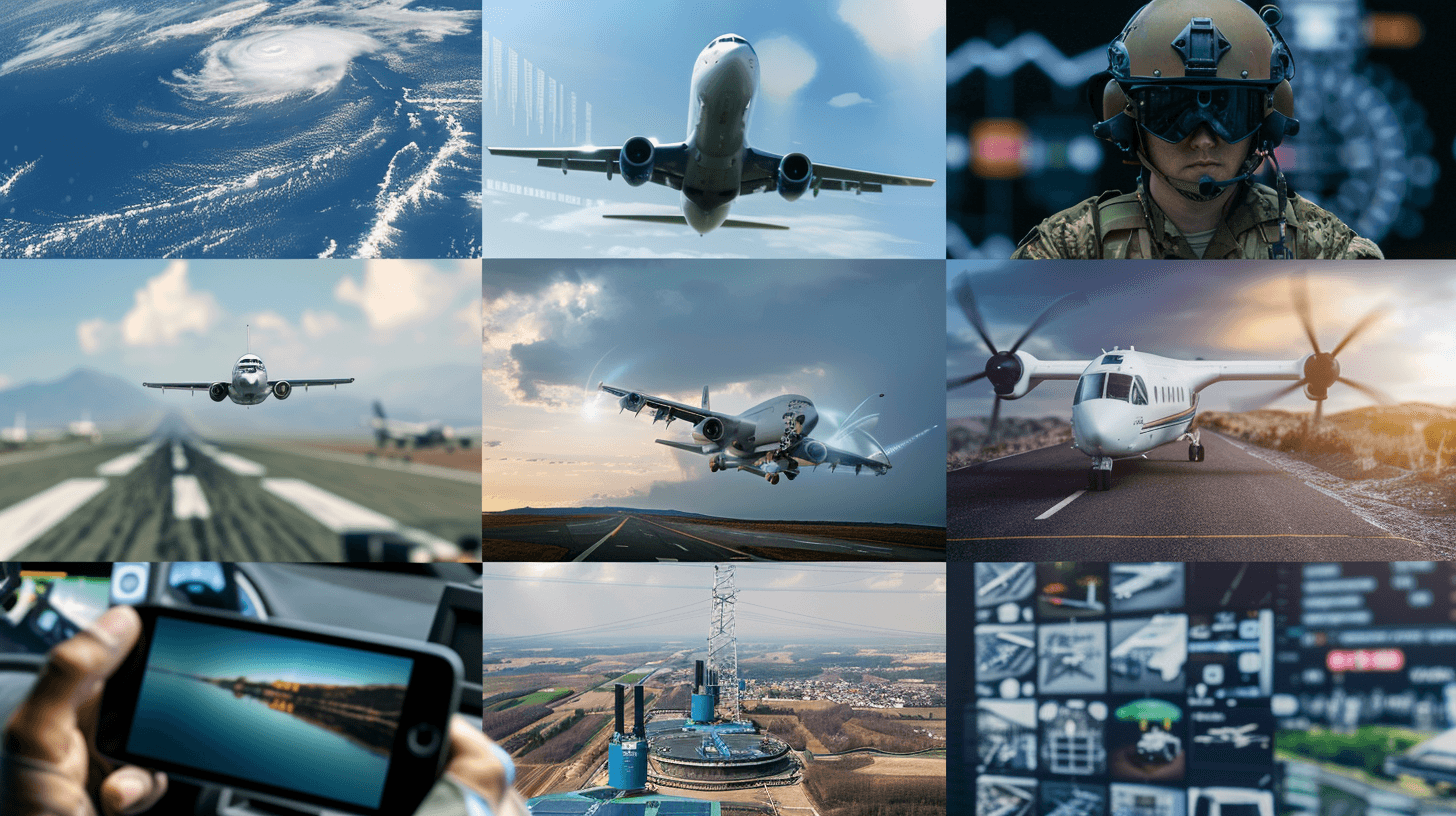
2. Defense & Military
From my experience working with military applications, I can say that FOGs are an irreplaceable asset in defense. They provide critical guidance data for everything from armored vehicles and tanks to missiles and UAVs. FOGs are designed to withstand intense shocks and vibrations, making them suitable for the rapid maneuvers and high-impact scenarios common in military operations.
- Key Features for Defense:
- High shock resistanceensures operational stability even under extreme forces.
- Precise guidanceimproves target accuracy in missiles and drones.
- Reliabilityunder extreme environmental conditions is essential for military missions.
3. Marine & Submarine Applications
In the depths of the ocean, traditional navigation tools like GPS become ineffective. FOGs, however, maintain their precision and stability even in GPS-denied environments, making them crucial for submersibles, ROVs (remotely operated vehicles), and marine vessels. Since these systems often run for long periods in remote locations, FOGs’ low maintenance needs and resilience to pressure changes make them an ideal choice.
- Key Features for Marine:
- Independent of GPSsignals, allowing reliable navigation underwater.
- Low maintenancemakes them suitable for long-term deployments.
- Environmental resilienceprotects against corrosion and pressure shifts in deep-sea operations.
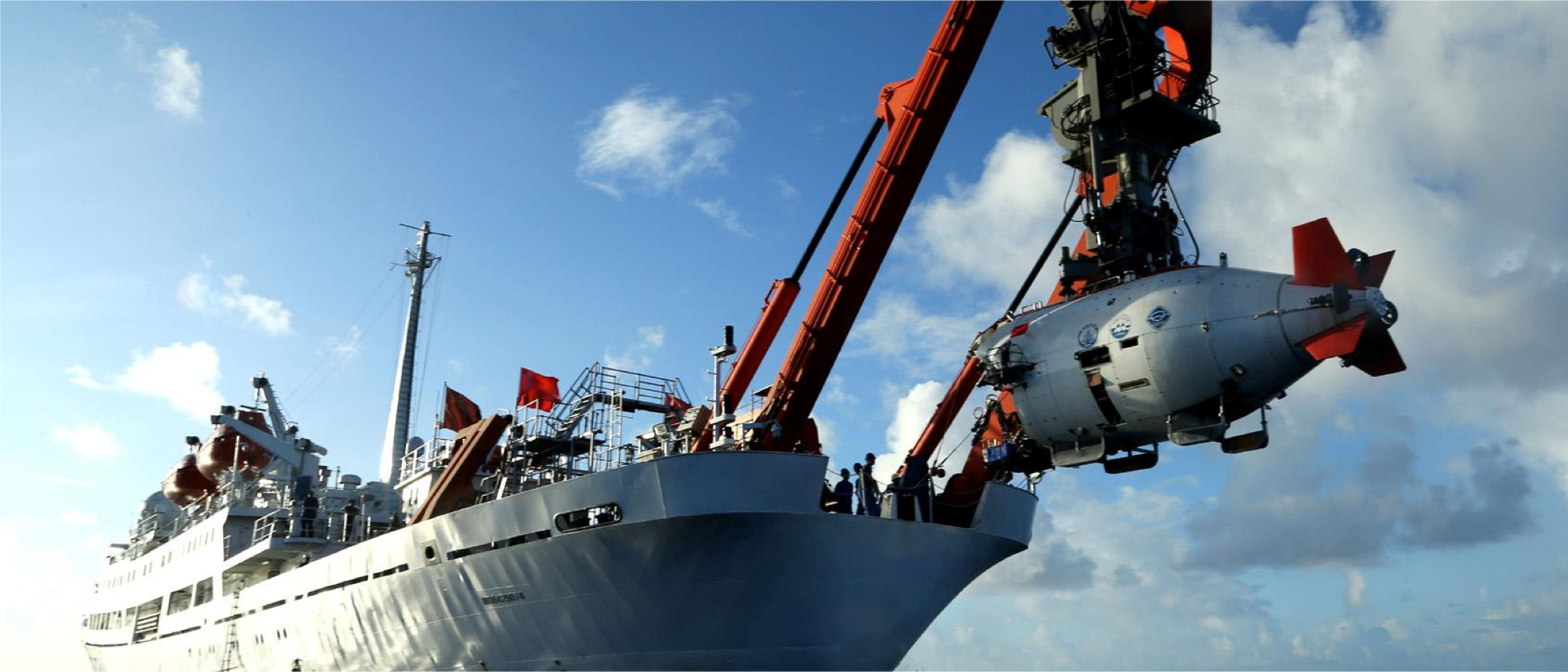
4. Autonomous Vehicles
For autonomous vehicles—whether ground-based, aerial, or underwater—navigation systems must be both highly accurate and resistant to drift. In self-driving cars, for example, precise orientation data is crucial for maintaining a steady path, recognizing obstacles, and responding to sudden movements. Drones and other industrial UAVs also rely on FOGs to provide stable orientation, even during rapid maneuvers.
- Key Features for Autonomous Vehicles:
- Stable, drift-free orientationenables consistent navigation in dynamic environments.
- Fast response timesare critical for split-second adjustments in real time.
- Compact designallows easy integration into various autonomous platforms.
5. Industrial Robotics
In the robotics industry, FOGs play a significant role in enhancing the precision and stability of robotic systems, particularly those involved in high-speed or high-stakes operations. Whether it’s a robotic arm performing delicate assembly work or automated machinery handling heavy loads, FOGs provide the steady, accurate feedback necessary to maintain control.
- Key Features for Robotics:
- Precision dataenables accurate positioning in tasks requiring fine control.
- High stabilityis crucial for consistent performance during rapid, repetitive movements.
- Durabilityreduces the need for maintenance, keeping operational costs low.
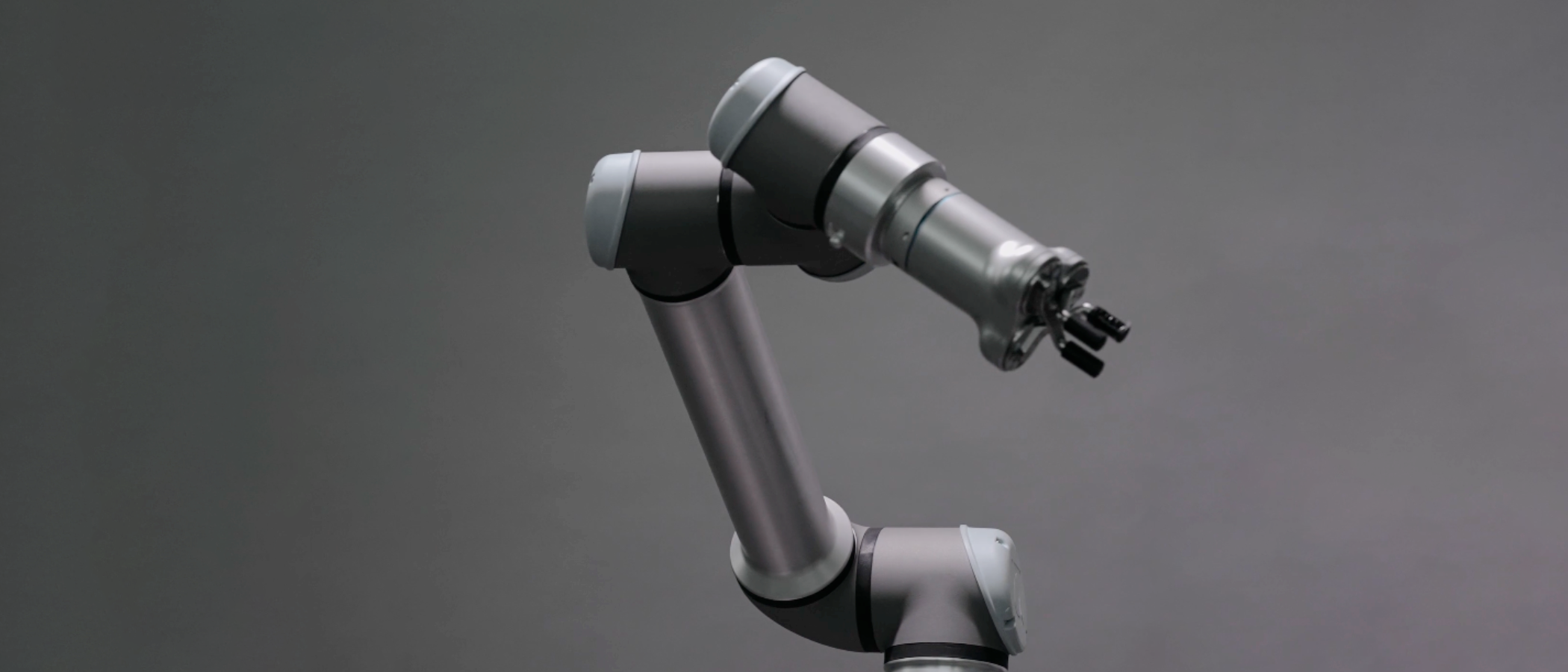
Why Fiber Optic Gyroscopes (FOGs) Are Crucial in Navigation and Positioning Systems
1. Unmatched Precision and Stability
FOGs are built for high-stakes accuracy. Unlike traditional gyroscopes, which can accumulate drift over time, FOGs have extremely low drift rates, which is vital for long-duration applications. In fields like aviation or marine navigation, small errors can quickly compound, leading to significant deviations. FOGs, with bias instability often below 0.001°/hr, provide the precision needed to keep systems on track over extended periods.
Performance Metric | Fiber Optic Gyroscopes (FOGs) | Traditional Gyroscopes |
---|---|---|
Drift | Minimal drift (±0.001°/hr) | High drift over time |
Long-Term Stability | Consistent | Degrades with mechanical wear |
Suitability | Ideal for extended missions | Limited to short durations |
2. Reliability in GPS-Denied Environments
One of the most compelling reasons to use FOGs is their reliability when GPS signals are weak or unavailable, such as in deep-sea or dense urban environments, or even in space. In these scenarios, dead reckoning—where the system calculates current position based on its last known position and motion—is essential. FOGs deliver the steady, continuous orientation data that keeps navigation systems accurate without needing an external signal.
Take submarines, for example. They frequently operate out of GPS range. Here, FOGs enable the precise, autonomous navigation needed for safe operation in GPS-denied environments.
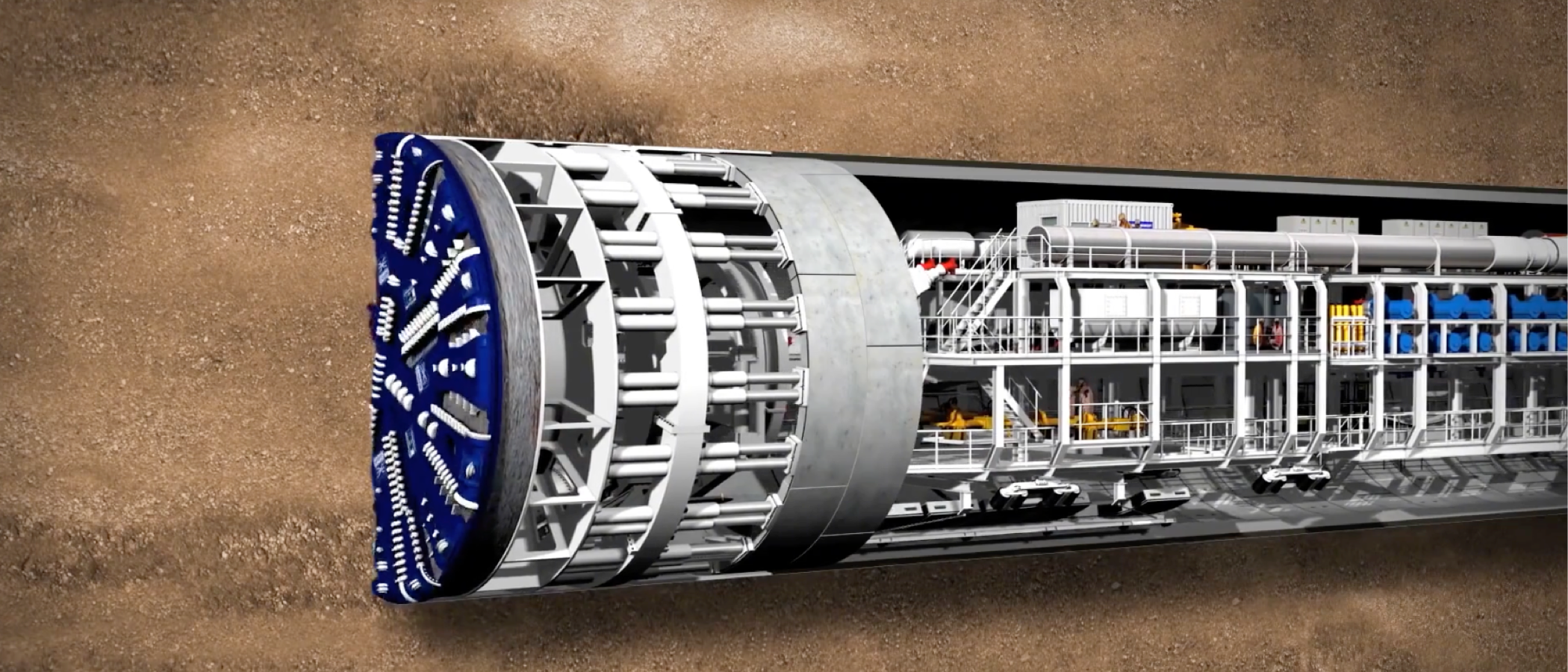
3. Environmental Resilience
In aerospace and military applications, environmental conditions are anything but predictable. Rapid temperature changes, vibrations, and shocks are all part of the equation. FOGs are incredibly resilient to these factors. They use solid-state design—meaning no moving parts—which makes them far less susceptible to wear compared to mechanical gyroscopes.
Environmental Factor | Fiber Optic Gyroscopes (FOGs) | Mechanical Gyroscopes |
---|---|---|
Temperature | Tolerant to extreme shifts | Limited range |
Vibration | High resistance | Performance degrades with shock |
Shock | Excellent resilience | Risk of mechanical failure |
4. Minimal Maintenance and Long Operational Life
FOGs offer long operational life with virtually no maintenance requirements. This is a significant advantage for systems operating in remote or hard-to-access locations, such as satellites or military drones. Since FOGs lack moving parts, there is little to no risk of mechanical wear, making them a low-maintenance solution that reduces overall operating costs.
Real-World Benefits of FOGs in Navigation and Positioning Systems
Let’s summarize how FOGs solve key challenges in various environments:
Environment | Conventional System Issues | FOG Solution |
---|---|---|
Deep-Sea Operations | GPS unavailable, drift accumulates rapidly | Low-drift data enables accurate dead reckoning |
Space Exploration | Extreme temperature fluctuations, signal loss | Reliable data, temperature resilience |
Urban Navigation | GPS signal loss in dense areas | Continuous data without reliance on external signals |
Military Field Ops | Shock and vibrations degrade accuracy | Shock-resistant, stable performance |
FOG vs High-Precision MEMS Gyroscope: A Comprehensive Comparison
1. Bias Instability
Bias instability is a measure of how stable the gyroscope’s bias is over short periods, usually in the range of seconds to minutes. Today’s high-precision MEMS gyroscopes can achieve bias instability values as low as 0.1°/hr, which is competitive with some low- to mid-end FOGs, particularly in commercial and industrial applications. Low- to mid-end FOGs generally have bias instability values ranging from 0.001°/hr to 0.1°/hr, making them suitable for applications where high short-term stability is critical.
Metric | High-Precision MEMS Gyroscopes | Low- to Mid-End FOGs |
---|---|---|
Bias Instability | 0.1°/hr to 1°/hr | 0.001°/hr to 0.1°/hr |
Application Suitability | Suitable for most mid-precision tasks | Preferred for high-stakes navigation |
2. Drift
Drift is the cumulative deviation in the gyroscope’s output over time, often caused by temperature changes, vibration, and sensor noise. For applications that require long-duration stability, such as satellite or deep-sea navigation, drift is a major factor to consider.
FOGs are known for their very low drift rates, which makes them highly suitable for extended operations in high-stakes environments. MEMS gyroscopes, while improving, still typically exhibit higher drift over long periods, which can limit their use in applications that demand ultra-high precision over hours or days without recalibration.
In practice, this means that for systems where positional accuracy needs to be maintained over long periods, FOGs are preferred. MEMS gyroscopes, however, can work well in applications where occasional recalibration is possible, such as UAVs and industrial equipment.
Metric | High-Precision MEMS Gyroscopes | Low- to Mid-End FOGs |
---|---|---|
Drift | Moderate, higher over long durations | Very low, stable for extended periods |
Application Suitability | Short-term precision with possible recalibration | Long-term, high-stability missions |
3. Size, Power, and Cost Efficiency
MEMS gyroscopes are generally smaller, lighter, and consume less power than FOGs. This makes MEMS ideal for applications where space and power are limited. Furthermore, MEMS manufacturing benefits from established semiconductor processes, enabling higher scalability and lower production costs. This is a major factor driving MEMS adoption in cost-sensitive markets like consumer electronics, automotive, and portable industrial devices. FOGs, with their complex optical assemblies, remain more costly and are often reserved for applications where their superior precision justifies the investment.
Feature | High-Precision MEMS Gyroscopes | Low- to Mid-End FOGs |
---|---|---|
Size & Weight | Compact, suited for small devices | Larger, due to optical components |
Power Consumption | Lower, efficient | Higher, especially in continuous use |
Cost | Lower, mass-produced | Higher, due to complex assembly |
4. Environmental Resilience and Outdoor Application
Modern high-precision MEMS gyroscopes are highly adaptable to outdoor environments and can operate reliably under various conditions, including moderate temperature fluctuations and vibrations. Although FOGs still offer superior temperature resilience and stability under extreme shock, high-precision MEMS gyroscopes are now rugged enough to support demanding outdoor applications such as unmanned aerial vehicles (UAVs), autonomous driving systems, and industrial machinery.
Environmental Factor | High-Precision MEMS Gyroscopes | Low- to Mid-End FOGs |
---|---|---|
Temperature Tolerance | Good for moderate extremes | Excellent for extreme conditions |
Shock & Vibration | High resistance, durable in moderate shock | Superior for harsh environments |
Outdoor Applications | Widely used (e.g., drones, vehicles) | Ideal for high-impact and high-stakes outdoor systems |
FOG Performance Specifications Explained
Fiber optic gyroscopes (FOGs) stand out for their precise and stable performance, making them a trusted choice in critical navigation systems. When evaluating FOGs, certain performance specifications become essential to understand—each specification plays a crucial role in determining whether a particular FOG model fits the needs of a high-stakes application. I’ll walk you through the key FOG specifications, explaining how each impacts functionality and performance in real-world conditions.
1. Dynamic Range
Dynamic range represents the maximum angular velocity a gyroscope can measure accurately, typically expressed in degrees per second (°/s). FOGs often feature dynamic ranges between ±300°/s and ±500°/s, which allows them to handle high-speed rotations while maintaining precision. For applications like aerospace and defense, this range is essential because sudden, rapid changes in orientation require gyroscopes that can keep up without losing accuracy.
Specification | Typical Value | Application Example |
---|---|---|
Dynamic Range | ±300°/s to ±500°/s | Aerospace systems, where high-speed rotation is common |
2. Bias Instability
Bias instability is a critical measure of a gyroscope’s short-term stability, typically reported in degrees per hour (°/hr). Low bias instability means minimal drift over time, which is essential for long-duration missions where positional data must remain accurate without external recalibration. High-end FOGs can achieve bias instability as low as 0.001°/hr, making them ideal for applications requiring ultra-stable output over extended periods, such as satellites and high-precision inertial navigation.
Specification | High-End FOG Value | Mid-Range FOG Value | Application Example |
---|---|---|---|
Bias Instability | 0.001°/hr to 0.05°/hr | 0.1°/hr to 0.5°/hr | Space and defense applications requiring continuous accuracy |
3. Angle Random Walk (ARW)
Angle random walk is an indicator of noise in the gyroscope’s output, often measured in degrees per square root of hour (°/√hr). Lower ARW values indicate a cleaner, more stable signal with less random fluctuation. High-precision FOGs typically offer ARW values below 0.01°/√hr, which is critical for applications like robotics and precision-guided systems, where even slight noise can lead to cumulative errors over time.
Specification | Typical FOG Value | Importance in Application |
---|---|---|
Angle Random Walk | 0.01°/√hr or lower | Reduces cumulative errors in high-precision systems like robotics |
4. Scale Factor Linearity and Repeatability
Scale factor linearity indicates how accurately the gyroscope’s output corresponds to actual angular rate changes, typically expressed in parts per million (ppm). High-precision FOGs achieve scale factor linearity values under 20 ppm, ensuring that readings remain consistent and reliable across a wide range of rotations. Scale factor repeatability measures the gyroscope’s ability to deliver consistent output across repeated tests, usually falling within ±10 ppm in high-end models. These metrics are essential for systems where consistent output is critical for feedback and control loops, such as in stabilization platforms.
Metric | High-End FOG Value | Impact on Performance |
---|---|---|
Scale Factor Linearity | < 20 ppm | Ensures reliable data across various rotation rates |
Scale Factor Repeatability | ±10 ppm | Key for consistent performance in control systems |
5. Temperature Compensation Range
FOGs are often deployed in environments with extreme or fluctuating temperatures. High-quality FOGs typically offer temperature compensation ranges from -40°C to +85°C, allowing them to maintain accuracy in both high-altitude aerospace settings and sub-sea applications. Consistent performance across this range prevents signal drift or fluctuations due to thermal expansion or contraction of internal components.
Specification | Typical Range | Key Application Examples |
---|---|---|
Temperature Compensation Range | -40°C to +85°C | Aerospace, maritime, and other extreme environments |
Key Factors to Consider When Selecting a FOG
Choosing the right fiber optic gyroscope (FOG) for an application can be a complex process. Over my 15 years working with FOG systems, I’ve found that the key lies in aligning specific FOG specifications with the operational requirements of your system. From bias instability to environmental resilience, each aspect plays a critical role in determining whether a FOG model is up to the task. Below, I’ll walk you through the essential factors to consider, along with a structured approach to making the best choice for your unique application.
1. Define Your Application Requirements
First, it’s essential to have a clear understanding of what your application demands. Does it require high stability over long durations, or will it operate under extreme environmental conditions? Start by listing the specific needs in terms of accuracy, operational duration, environmental factors, and available space. Let’s break down these considerations in the table below:
Requirement Aspect | Key Questions | Example Applications |
---|---|---|
Accuracy | What level of bias instability and drift is acceptable? | Aerospace, autonomous navigation |
Environmental Resilience | Will the FOG be exposed to high vibrations, shocks, or temperature extremes? | Military, industrial robotics |
Size and Power Constraints | Is the system size or power-limited? | Portable devices, UAVs |
2. Prioritize Bias Instability and Drift Requirements
In high-precision applications, bias instability and drift are critical. If your system needs long-term accuracy, choose a FOG with low bias instability (e.g., 0.001°/hr for high-end applications) to minimize drift over time. Applications in aerospace and deep-sea navigation, for example, benefit greatly from FOGs with minimal drift.
Requirement | Recommended FOG Specification | Example Application |
---|---|---|
Bias Instability | 0.001°/hr to 0.05°/hr | Satellite and submarine navigation |
Drift | Very low, stable over long periods | High-stakes, long-duration missions |
3. Consider Dynamic Range and Angle Random Walk
The dynamic range of a FOG indicates the maximum angular rate it can measure accurately, while angle random walk (ARW) reflects the noise level in the sensor’s output. For applications like UAVs or robotics, where sudden rotations and precise corrections are necessary, a higher dynamic range (e.g., ±500°/s) and low ARW (e.g., < 0.01°/√hr) will improve control and response.
Specification | Typical Value | Key Benefit |
---|---|---|
Dynamic Range | ±300°/s to ±500°/s | Suitable for fast rotation scenarios |
Angle Random Walk (ARW) | < 0.01°/√hr | Reduces cumulative noise for precision |
4. Evaluate Temperature Compensation Range
For applications exposed to extreme temperatures—such as high-altitude drones, military equipment, or deep-sea exploration vehicles—ensure the FOG’s temperature compensation range covers your operational environment. High-quality FOGs typically offer ranges from -40°C to +85°C, which ensures consistent performance in various climates.
Temperature Range | Application Suitability |
---|---|
-40°C to +85°C | Aerospace, military, maritime |
-20°C to +60°C | Industrial robotics, standard outdoor applications |
5. Balance Size, Power, and Cost Considerations
For portable or battery-operated systems, FOG size and power consumption are often key constraints. High-precision FOGs tend to be larger due to optical fiber requirements, but some models offer a good balance of compact size and power efficiency. Additionally, keep in mind that while high-end FOGs are more expensive, they often provide higher reliability and precision, making them cost-effective for critical applications.
Factor | High-Precision FOG | Compact, Efficient FOG |
---|---|---|
Size & Weight | Larger, suited for high-stakes, high-precision systems | Compact, ideal for portable devices |
Power Efficiency | Moderate to High, requires external power source | High, suited for battery-powered devices |
Cost | Higher, ideal for mission-critical systems | Moderate, balances cost and performance |
Introduction of GuideNav’s FOG Technology
GuideNav’s Fiber Optic Gyroscopes are trusted by clients in over 25 countries for their reliability, accuracy, and endurance in high-stakes environments. Each FOG is meticulously engineered and rigorously tested to meet the highest standards, ensuring consistent performance where it matters most. Whether you need precise orientation in a spacecraft, robust navigation in an autonomous vehicle, or stability in a deep-sea vessel, GuideNav’s FOGs deliver the performance you can rely on.
GuideNav is more than just a provider; we’re a partner in precision navigation, offering tailored solutions that meet the unique needs of each application.
Comparison of GuideNav FOG Models
Model | Type | Bias Instability | Dynamic Range | Angle Random Walk (ARW) | Temperature Range | Best Applications |
---|---|---|---|---|---|---|
GFS40B | Single-Axis | 0.001°/hr | ±300°/s | 0.005°/√hr | -40°C to +85°C | Aerospace, defense, satellite systems |
GFS70A | Single-Axis | 0.01°/hr | ±500°/s | 0.01°/√hr | -40°C to +85°C | UAVs, robotics, industrial automation |
GFS120B | Single-Axis | 0.05°/hr | ±400°/s | 0.02°/√hr | -40°C to +85°C | Marine navigation, offshore platforms, rugged industrial equipment |
GTF40 | Three-Axis | 0.01°/hr (per axis) | ±300°/s per axis | 0.01°/√hr (per axis) | -20°C to +70°C | Autonomous vehicles, drones, robotics |
GTF70A | Three-Axis | 0.005°/hr (per axis) | ±400°/s per axis | 0.005°/√hr (per axis) | -40°C to +85°C | Precision navigation, high-speed robotics |
GTF120 | Three-Axis | 0.001°/hr (per axis) | ±500°/s per axis | 0.002°/√hr (per axis) | -40°C to +85°C | Aerospace, defense, complex robotic systems |
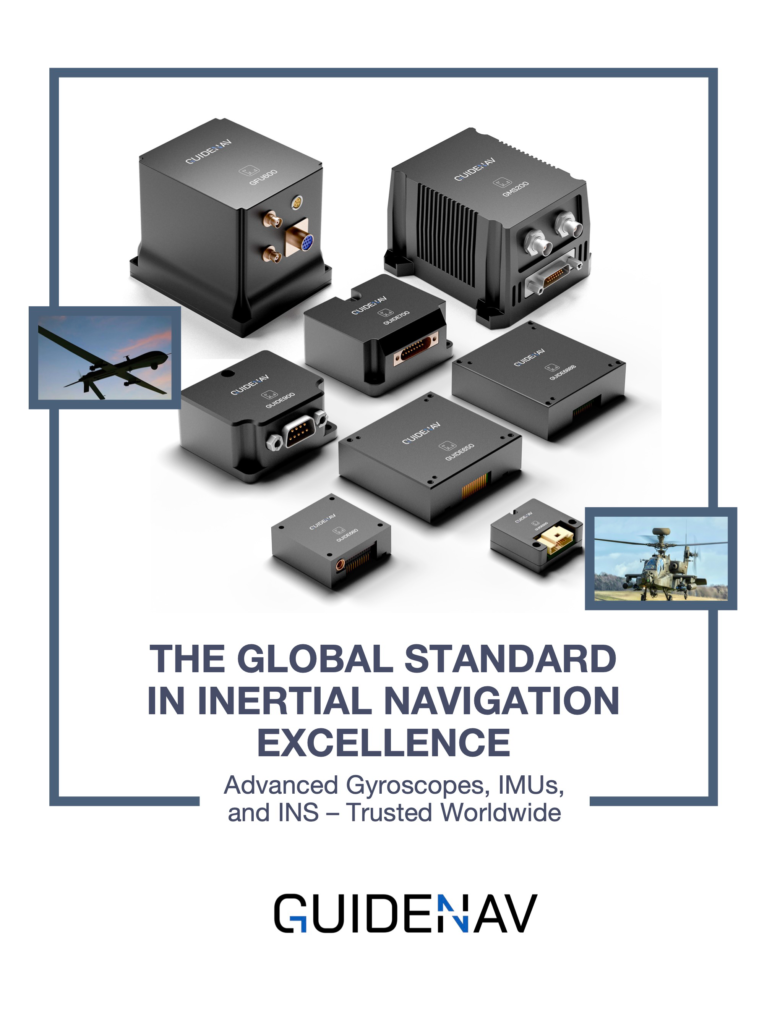