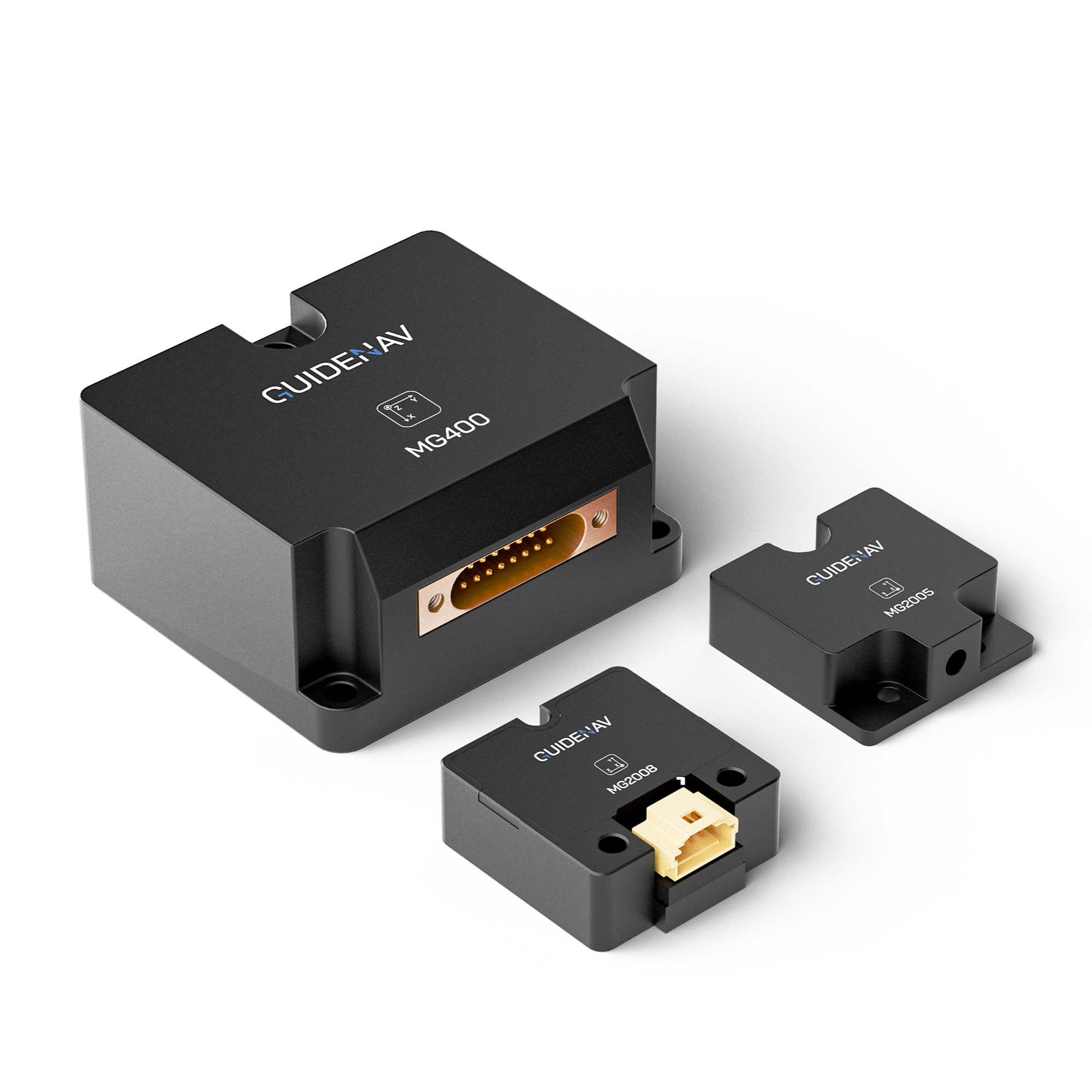
Introducing guidenav's MEMS Gyroscope
MEMS Gyroscope
15,000+ Systems in Operation in 35+ Countries
Custom Solutions Trusted by Global Key Players
Our featured MEMS Gyroscope offers several advantages over traditional gyroscopes, such as fiber optic or ring laser types. It is more compact, lightweight, and cost-effective, making it ideal for space-constrained and budget-sensitive projects. Despite its smaller size, it delivers high accuracy and stability, essential for mission-critical applications.
Trusted by leading aerospace, defense, and industrial organizations across more than 35 countries, our MEMS Gyroscope stands out for its reliability and precision.
MEMS Gyroscopes COVer all your applications
Featured MEMS Gyroscope Model
At GuideNav, we understand that different industries have unique requirements. That’s why we offer a range of MEMS Gyroscopes with varying levels of precision and performance parameters. Whether your project demands ultra-high accuracy for aerospace applications or robust stability for industrial use, we have a model that fits your specific needs.
Each gyroscope is engineered to excel in its intended environment, ensuring you get the exact performance you require, no matter the application. With GuideNav, you gain access to a tailored solution that aligns perfectly with the demands of your industry.
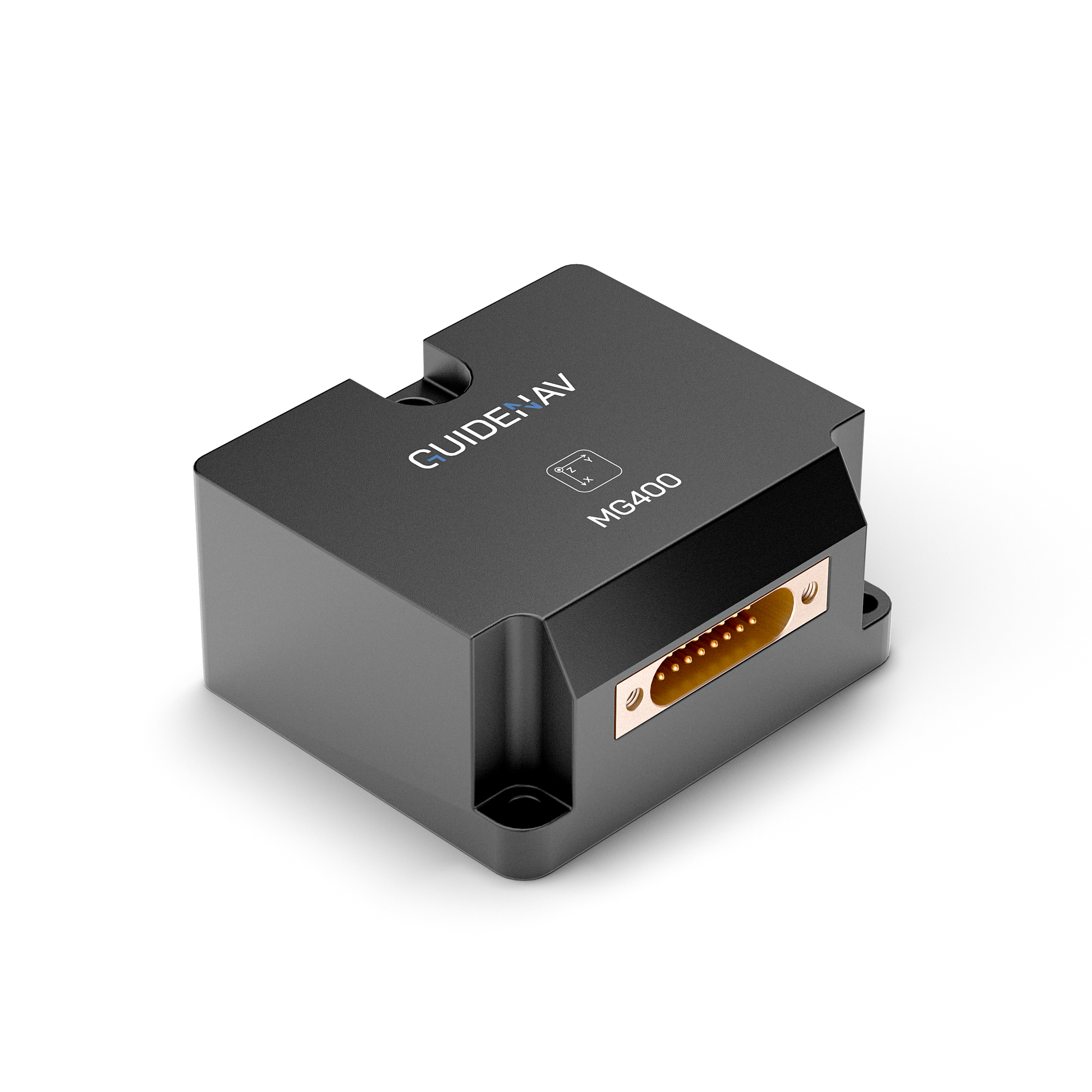
- High accuracy
- Gyro range: ± 400 °/s
- Bias instability: ≤ 0.4 °/h
- Bias stability: ≤ 5°/h
- Weight: ≤ 60g
- Protocol: RS422
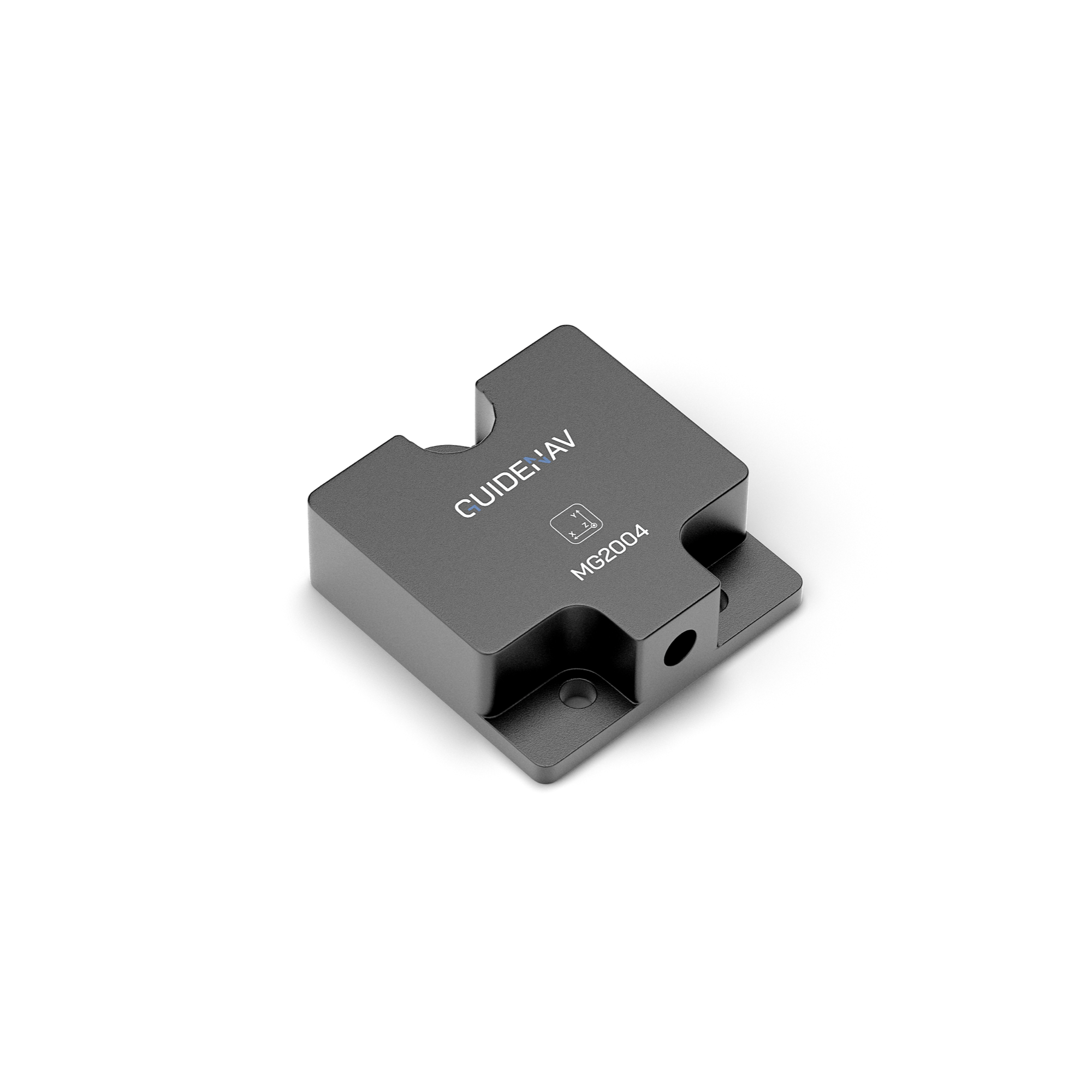
- Wide Gyro Range
- Gyro range: ± 2000 °/s
- Bias instability: ≤ 3°/h
- Bias stability: ≤ 10°/h
- Weight: ≤20g
- Protocol: RS422
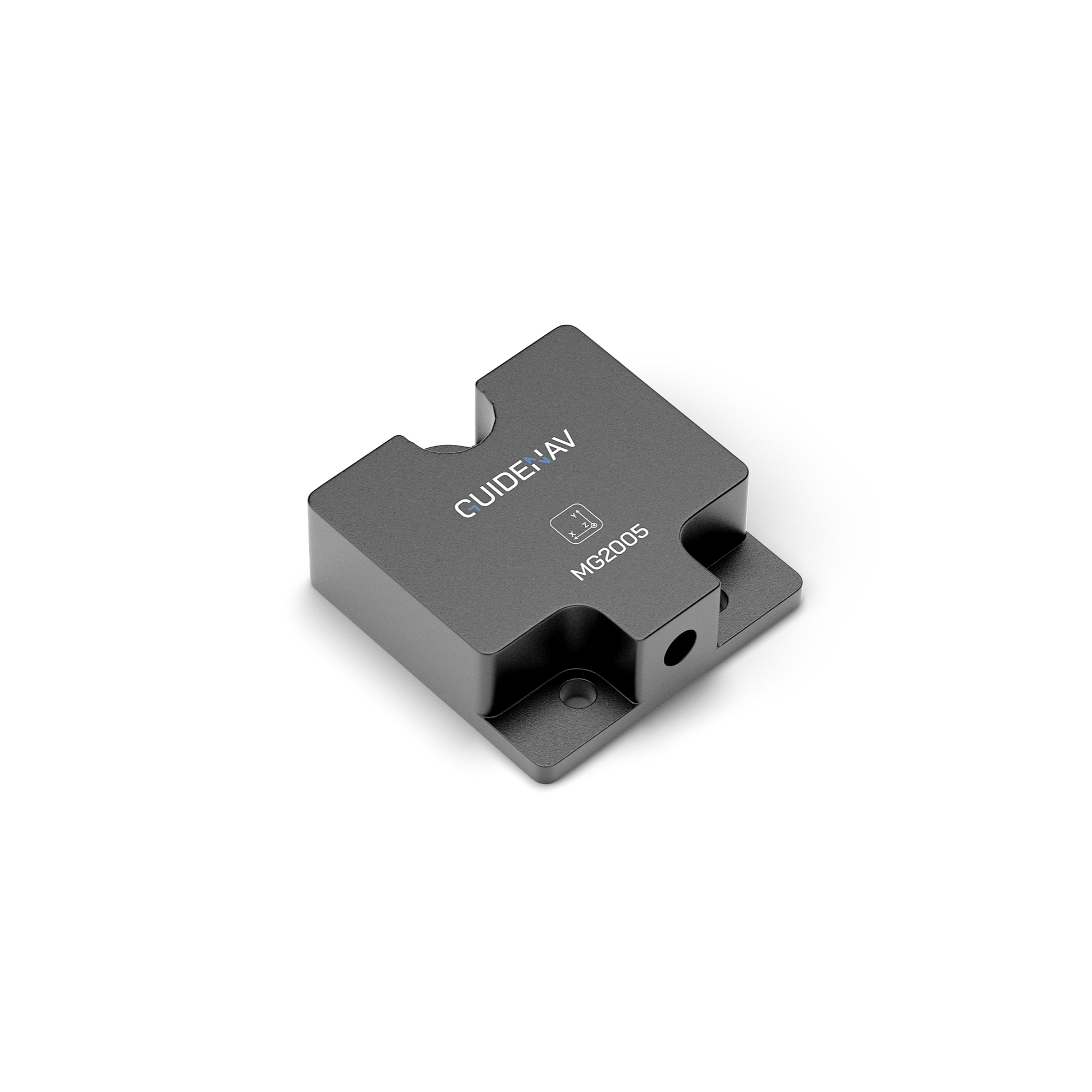
- Wide Gyro Range
- Gyro range: ± 2000 °/s
- Bias instability: ≤ 4 °/h
- Bias stability: ≤ 15°/h
- Weight: ≤40g
- Protocol: RS422
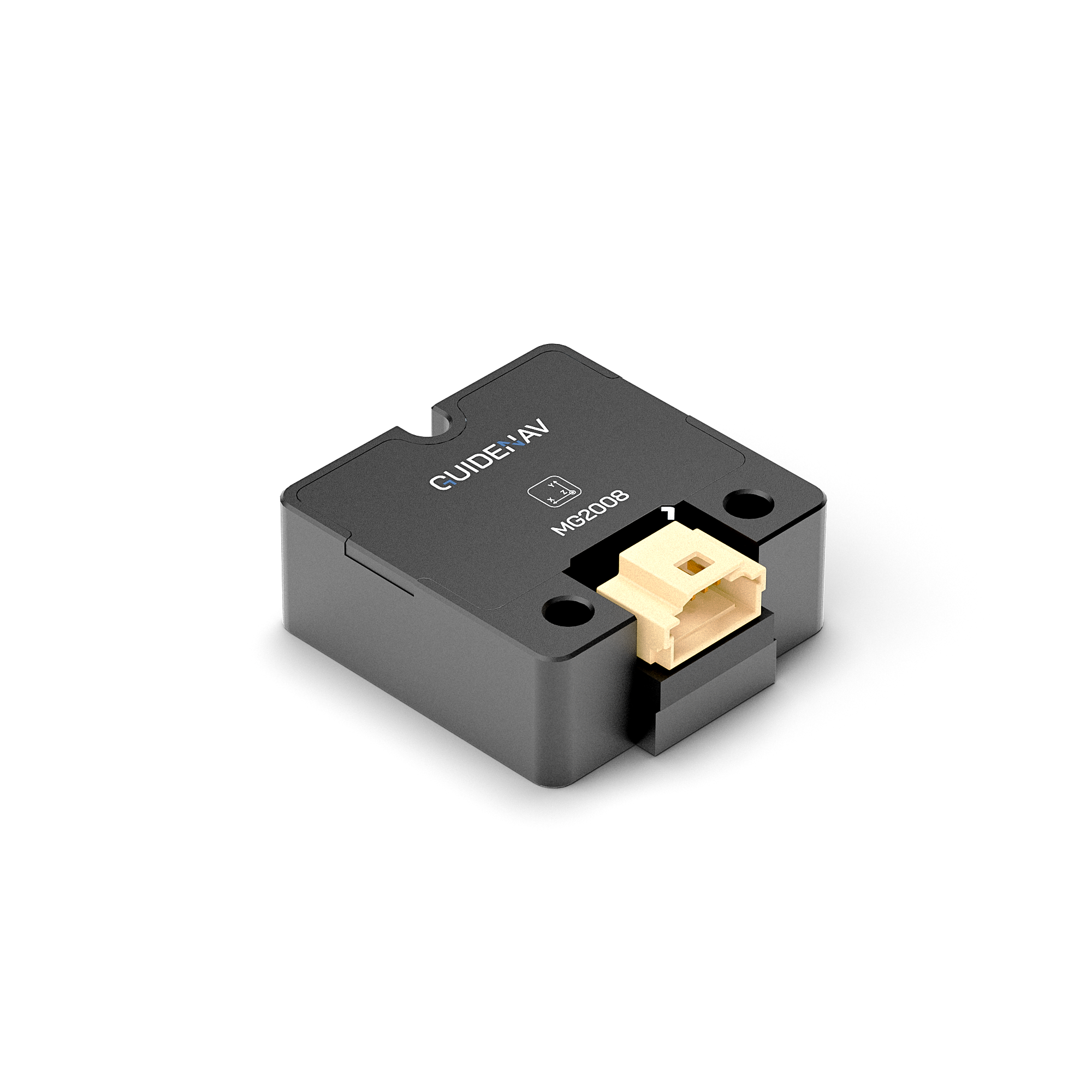
- Wide Gyro Rang
- Gyro range: ± 2000 °/s
- Bias instability: ≤ 3 °/h
- Bias stability: ≤ 10°/h
- Weight: ≤20g
- Protocol: UART
Let's Talk About Your Project
Your project deserves a solution tailored to your exact specifications. To ensure we provide the best MEMS Gyroscope for your needs, we invite you to share the specific parameters and performance requirements of your application. Whether it’s precision, stability, or size constraints, our team is ready to help you find the perfect fit.
Table of Contents
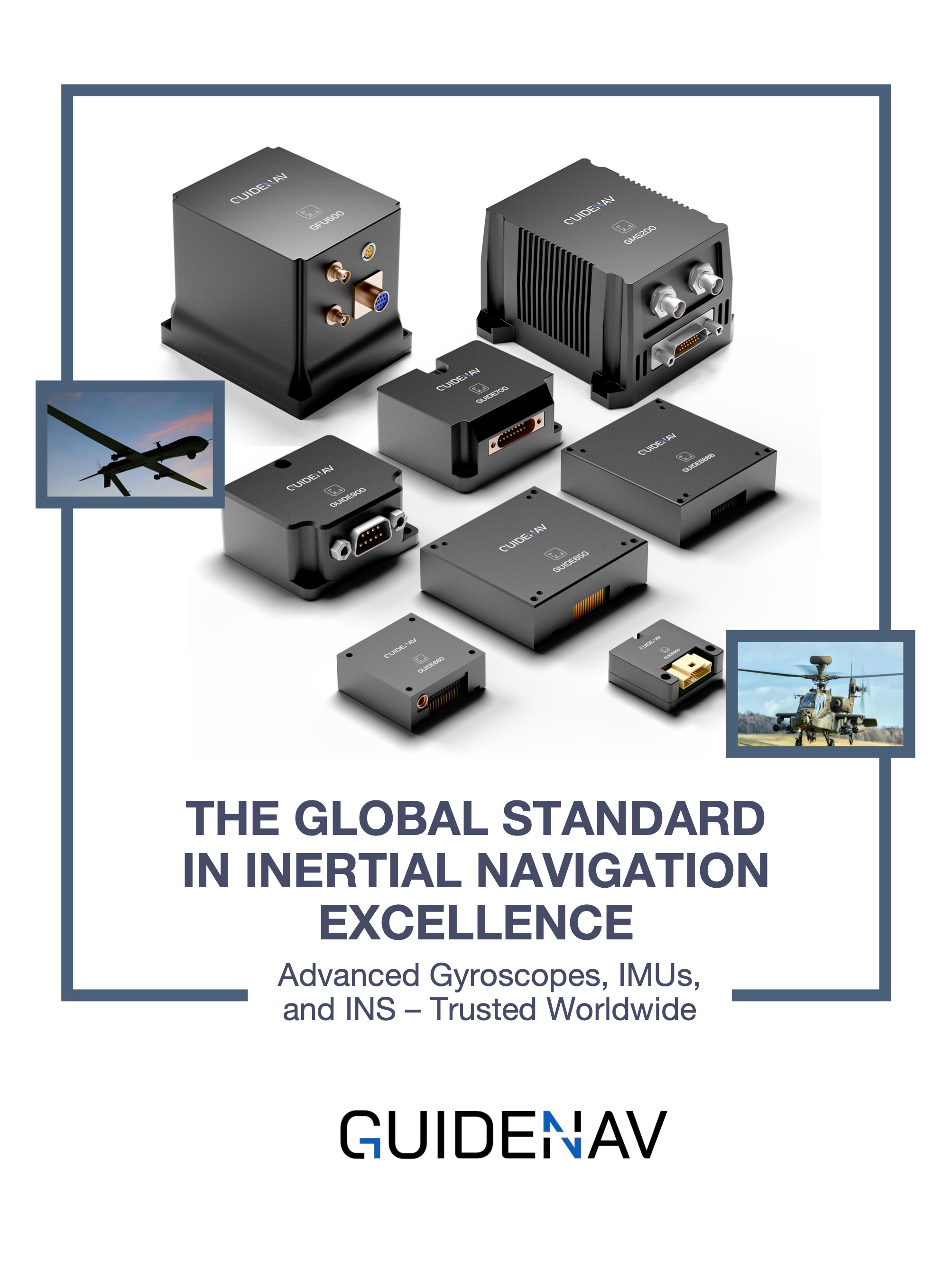
Download this page as a PDF
To save you time, we have also prepared a PDF version containing all the contents of this page, only leave your email and you will get the download link immediately.
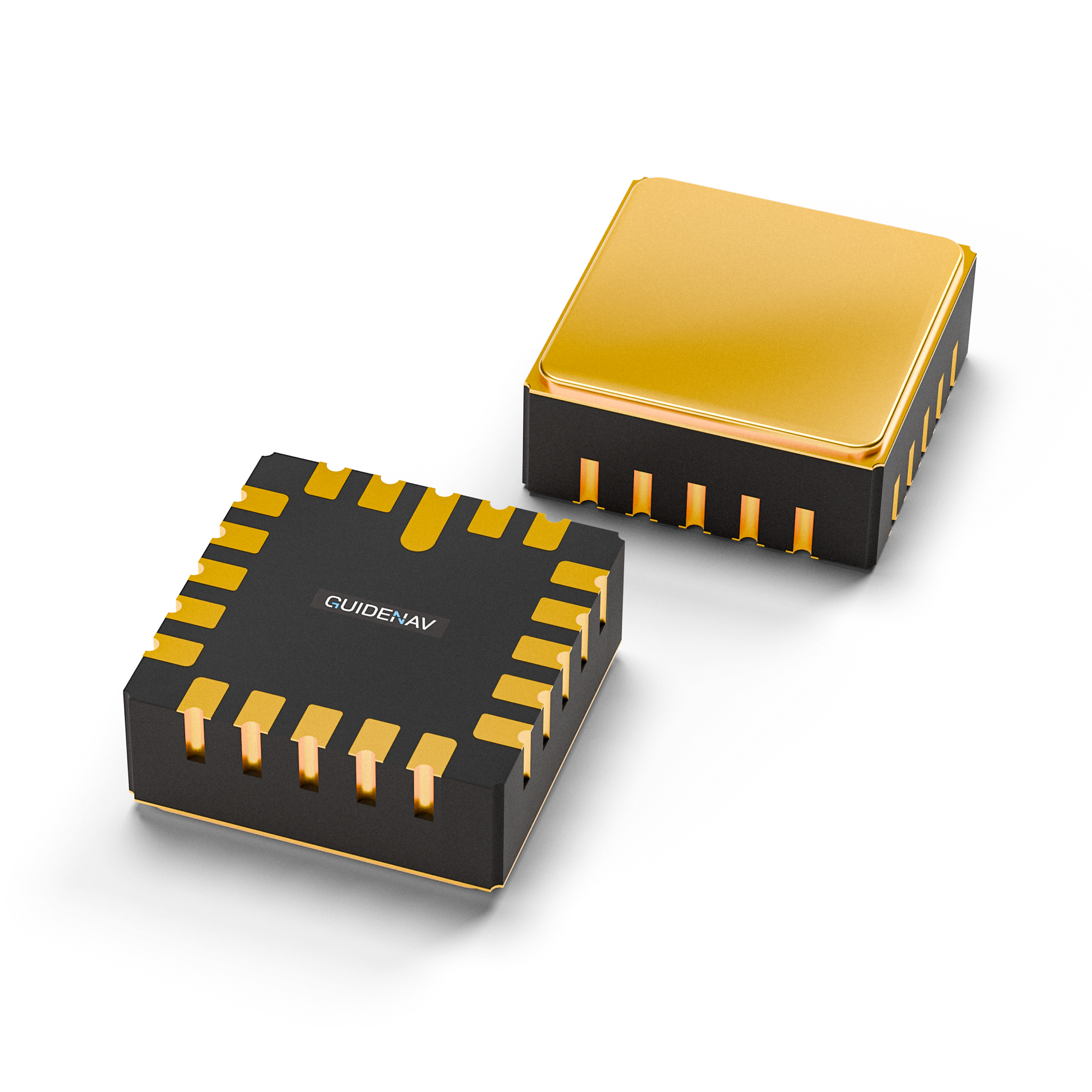
MEMS Gyroscope
What is MEMS Gyroscope ?
A MEMS (Micro-Electro-Mechanical Systems) Gyroscope is a compact, highly reliable device used to measure angular velocity or maintain orientation in a wide range of applications. Unlike traditional gyroscopes, MEMS technology combines mechanical and electrical components at a microscopic scale, resulting in a smaller, more cost-effective solution without compromising on performance.
These gyroscopes are integral to systems where precision and stability are crucial, including in aerospace, defense, and industrial environments. MEMS Gyroscopes are valued for their ability to deliver accurate measurements in even the most demanding conditions, making them an essential component in modern navigation and control systems.
Key Features of guidenav's mems gyroscope
Key Features of MEMS Gyroscope
Low Cost
Feature
MEMS gyroscopes are much more cost-effective to produce compared to FOG gyroscopes, thanks to large-scale semiconductor manufacturing processes.
Advantage
Suitable for mass-market applications in consumer electronics, automotive, and industrial automation, meeting the needs of cost-sensitive markets.
Miniaturization & Lightweight
Feature
MEMS gyroscopes are significantly smaller and lighter than FOG gyroscopes, making them easy to integrate into compact devices.
Advantage
Ideal for portable devices, smartphones, drones, and wearables where size and weight are critical factors.
Low Power Consumption
Feature
MEMS gyroscopes typically consume less power, making them suitable for battery-operated devices.
Advantage
Extends the battery life of portable and battery-powered devices, making them ideal for long-duration applications such as wearables and mobile devices.
Fast Response & High Integration
Feature
MEMS gyroscopes have fast response times and can be integrated with accelerometers, magnetometers, and other sensors into a single chip or package, forming an IMU.
Advantage
Provides comprehensive attitude and motion measurement solutions, ideal for dynamic applications like drone flight control
Manufacturing Process of mems gyroscope
Manufacturing Process of MEMS Gyroscope
01
STEP 1 :Customer Requirement Analysis and Design
Define Specifications: Work with the customer to define key performance parameters such as drift rate, noise density, temperature stability, and sensitivity. Based on these requirements, design the MEMS structure and associated circuitry, and validate the design through simulations to ensure it meets the desired performance.
02
STPE 2 :MEMS Structure Fabrication
Photolithography and Etching: Utilize photolithography, etching, and material deposition techniques to fabricate the core mechanical structures and electrodes of the MEMS gyroscope on silicon wafers, ensuring that the fabrication process aligns with the customer’s specified performance parameters.
03
STPE 3 :Component Integration
ASIC Integration: Integrate the fabricated MEMS structures with an Application-Specific Integrated Circuit (ASIC) to achieve precise signal processing, amplification, filtering, and analog-to-digital conversion, ensuring accuracy and reliability in line with customer requirements.
04
STPE 4 :Packaging
Encapsulation: Encapsulate the integrated MEMS chip using protective housing and sealing techniques to ensure stability and reliability under various environmental conditions, fully meeting the customer’s environmental and durability requirements.
05
STEP 5 :Calibration and Testing
Calibration: Perform rigorous calibration to adjust and verify the gyroscope’s key performance parameters. Conduct comprehensive functional and environmental testing to ensure that the final product meets the customer’s specifications and performs reliably in the intended application environment.
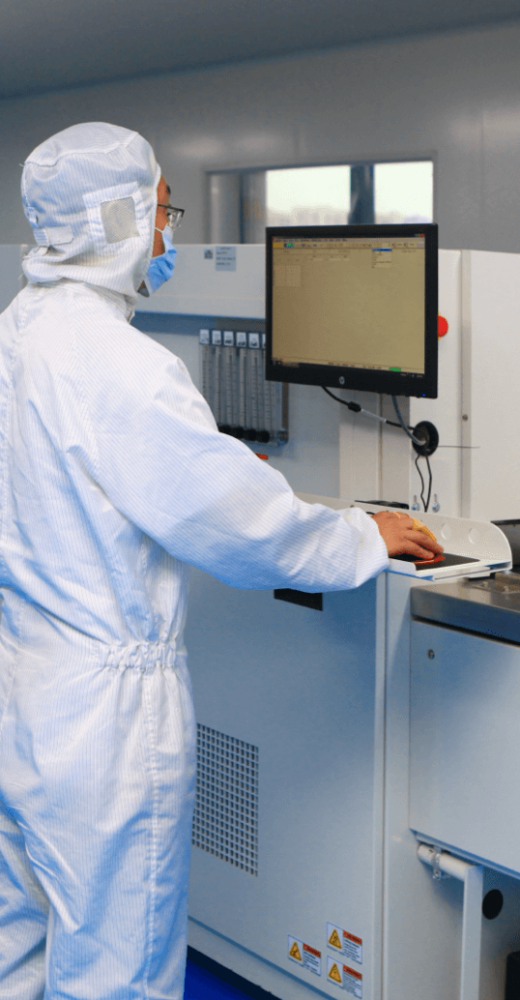
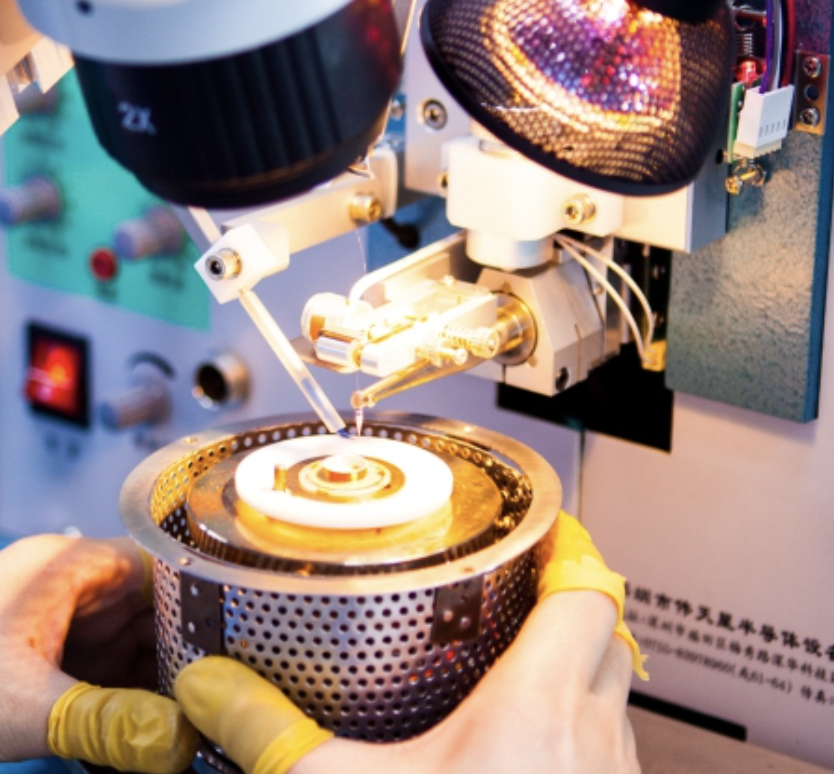
How to select
How to Select the Right
MEMS Gyroscope
STEP 1
Define the Application
Identify the specific application scenario for the MEMS gyroscope. Ensure the selected gyroscope meets the application’s environmental and operational requirements.
STEP 2
Evaluate Accuracy Requirements
Determine the required level of accuracy based on the application needs, including the resolution and precision of angular velocity measurements.
STEP 3
Consider Drift Rate and Temperature Stability
Assess the impact of drift rate and temperature variations on the gyroscope’s performance, particularly in long-term use or environments with significant temperature changes.
STEP 4
Analyze Size and Power Consumption
Consider the size constraints and power consumption requirements, especially in portable or battery-powered devices.
STEP 5
Validate System Compatibility
After selecting a MEMS gyroscope, validate its compatibility with existing system interfaces, protocols, and data processing workflows.
STEP 6
Validation and Performance Testing
Perform experimental validation and performance testing on the selected MEMS gyroscope, including dynamic response, noise levels, and interference resistance.
Compare mems and fiber optics gyroscope
MEMS VS FIBER OPTICS
Which is Better ?
MEMS Gyroscope: With advancements in technology, MEMS gyroscopes have achieved accuracy levels comparable to mid-range FOG gyroscopes in many scenarios. Their strengths lie in miniaturization, low power consumption, and varied production costs, making them widely applicable in consumer electronics, drones, military equipment, industrial automation, and automotive electronics.
FOG Gyroscope: FOG gyroscopes remain the preferred choice for high-precision applications, especially in scenarios requiring long-term stability, such as aerospace, precision navigation, and defense. Despite their larger size and higher cost, FOG gyroscopes excel in performance under extreme environmental conditions.
Feature | MEMS Gyroscope | Fiber Optic Gyroscope |
---|---|---|
Operating Principle | Measures angular velocity through micro-mechanical structures in MEMS technology | Measures angular velocity based on the Sagnac effect in fiber optic interference |
Accuracy | Wide range of accuracy; some high-end MEMS gyroscopes have achieved comparable accuracy to mid-level FOG gyroscopes | High accuracy, ideal for demanding navigation and control applications, especially with long-term stability |
Drift Rate | Drift rate has significantly improved with technological advancements; some high-end models can rival FOG gyroscopes | Typically features very low drift rate, suitable for long-term continuous operation |
Size and Weight | Compact and lightweight, ideal for space-constrained applications, widely used in portable devices and military applications | Larger and heavier, suitable for high-precision applications where space and weight are not constraints |
Power Consumption | Low power consumption, ideal for battery-powered portable devices and long-duration missions | Higher power consumption, suitable for systems where power requirements are not a major concern |
Cost | Varies from low to medium cost, suitable for large-scale consumer, industrial, and military applications | Higher production cost, suited for high-end applications |
Resistance to Interference | Resistance to interference has improved with design and packaging advancements; most MEMS gyroscopes now offer good resistance to electromagnetic interference | Insensitive to electromagnetic interference, ideal for complex electromagnetic environments |
Temperature Stability | With temperature compensation techniques, many high-end MEMS gyroscopes perform stably across a wide range of temperatures | Excellent temperature stability, suitable for extreme environments |
Applications | Widely used in consumer electronics, drones, military equipment, industrial automation, automotive electronics, and more | High-precision navigation, aerospace, marine, defense, and other high-end applications |
Our Adavantages
Why Choose Guidenav?
Trusted by keyplayers
Our advanced inertial navigation products are trusted by leading organizations in the aerospace, defense, commercial, and industrial sectors from over 25 countries. Our reputation for reliability and precision sets us apart.
Top Performance
Our products deliver top-tier performance with excellent bias stability. Designed for the most demanding applications, they ensure precise navigation and control.
Proven in Harsh Environment
Our solutions are built to withstand extreme conditions, providing consistent performance in harsh environments. The typical working temperature with our inertial navigation sensors and systems are -40℃~+60℃
Excellent Performance under Vibrations
Our technology excels in high-vibration settings, ensuring accuracy and stability even in the most challenging operational environments.
PLUG & PLAY System
Our systems are designed for easy integration, offering plug-and-play solutions that simplify installation and reduce setup time, allowing you to focus on your mission.
ITAR-FREE
Our products are ITAR-free, offering you the advantage of easier international transactions and fewer regulatory hurdles. Choose GuideNav for seamless global operations.
Our Factory - See to Believe
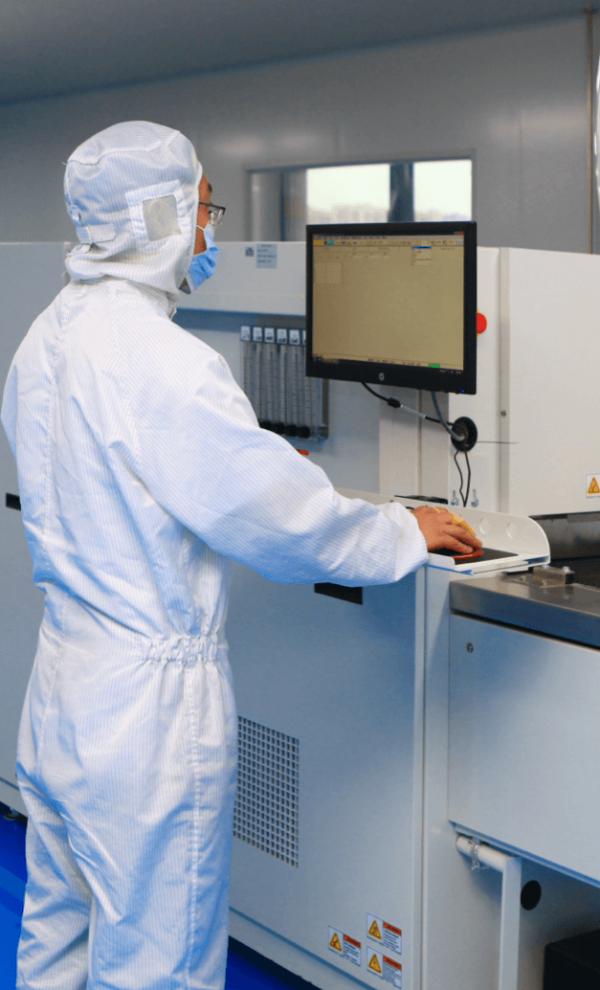
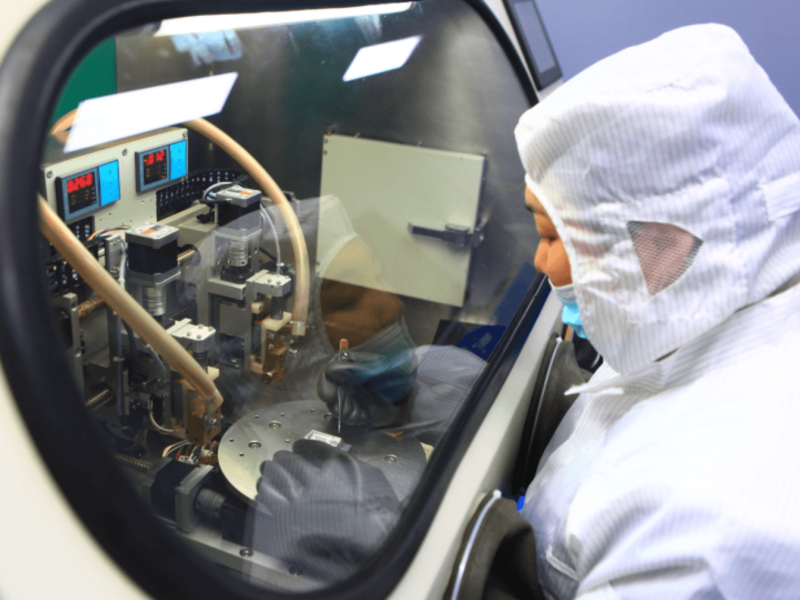
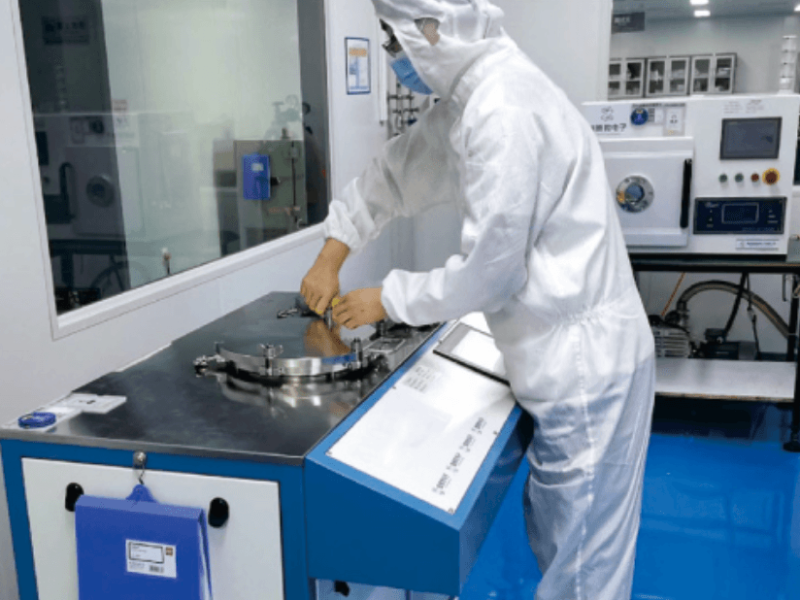
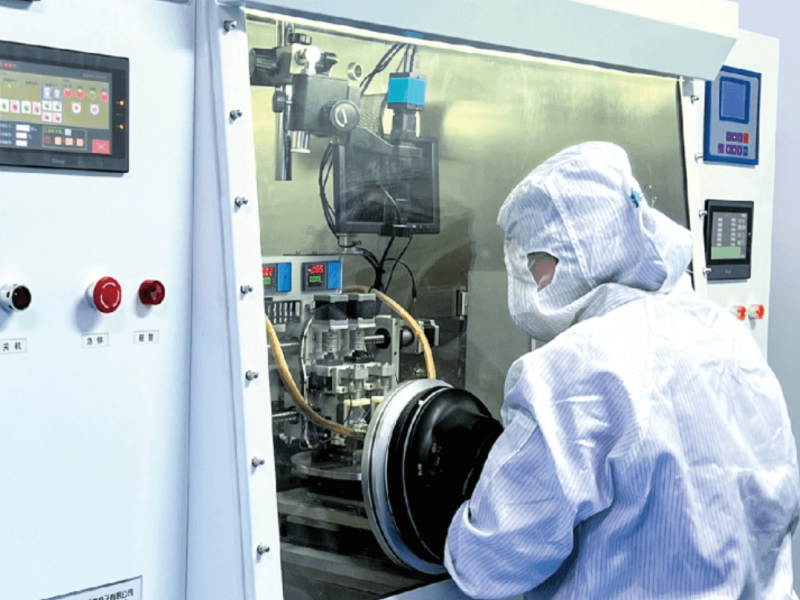
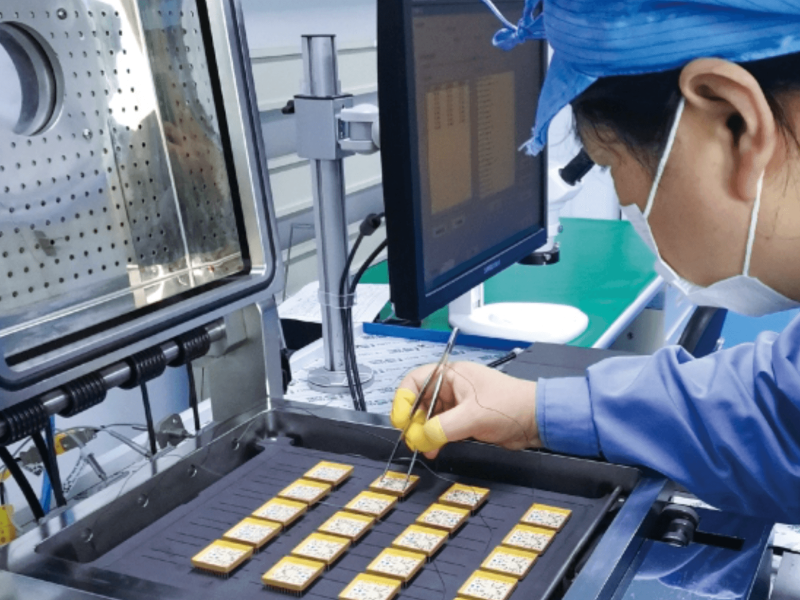
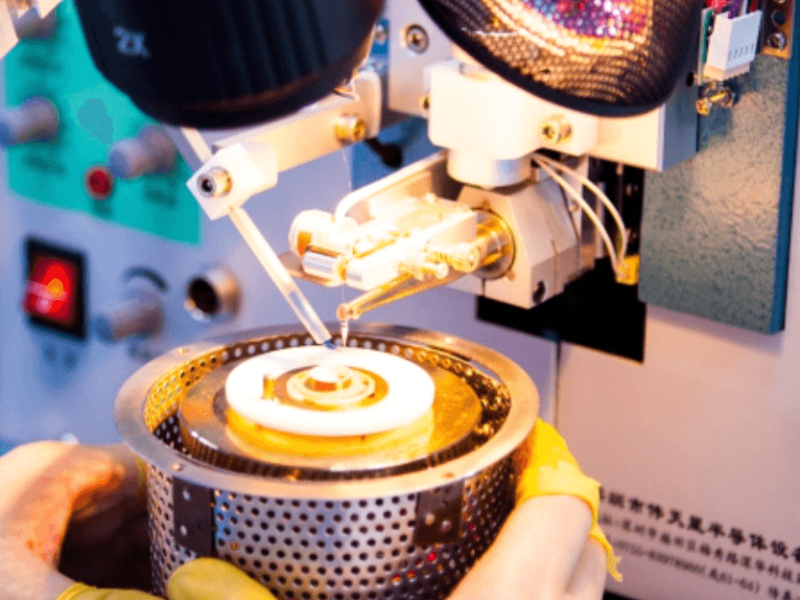
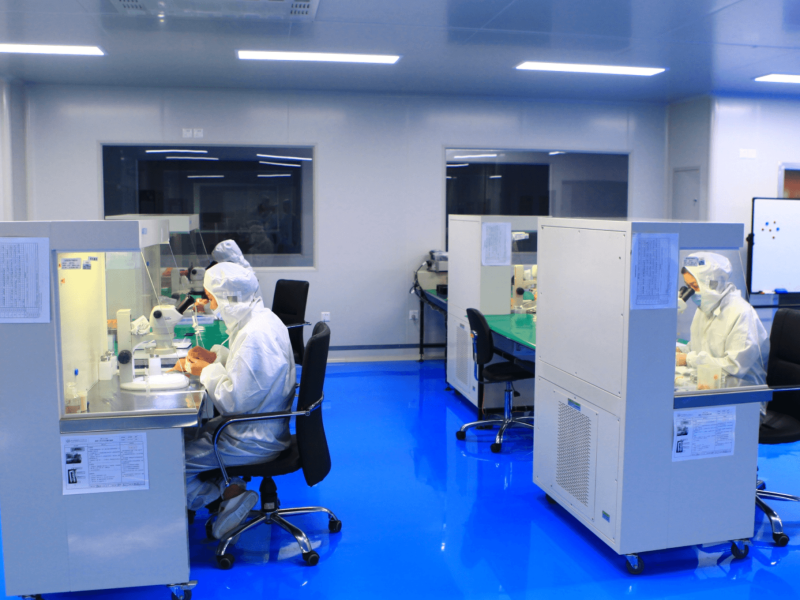
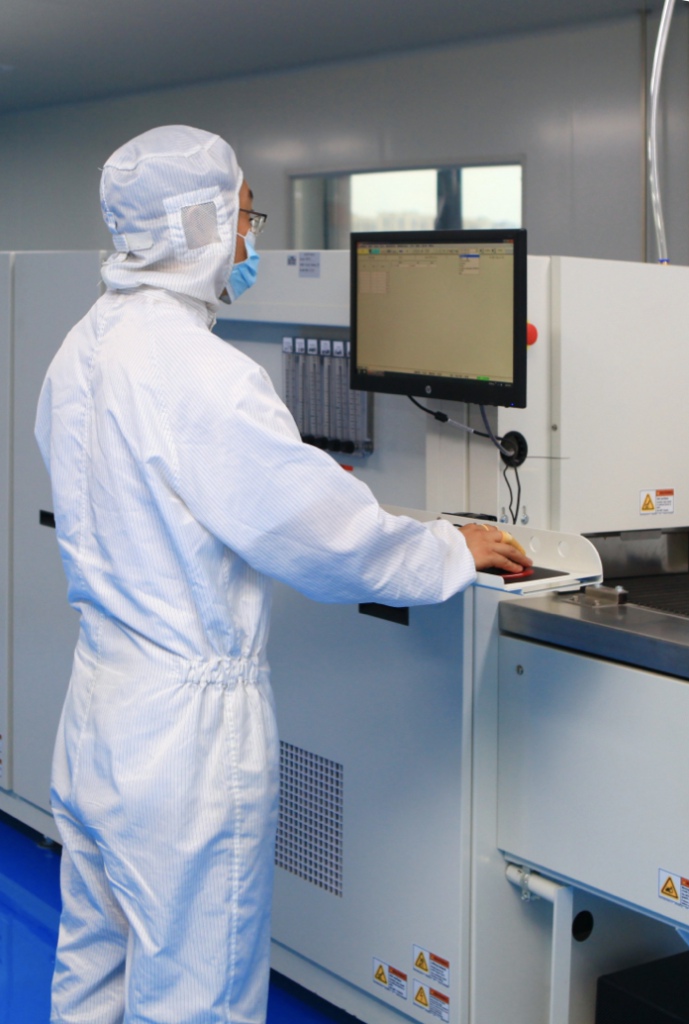
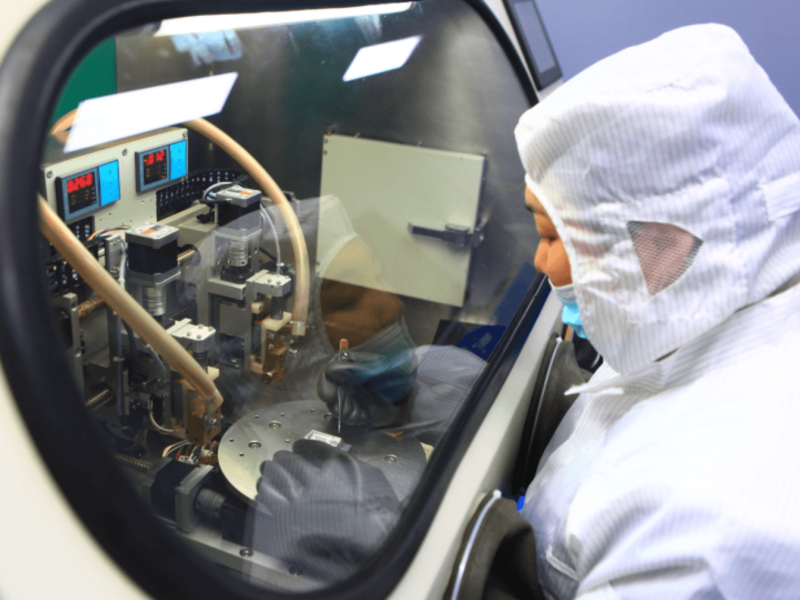
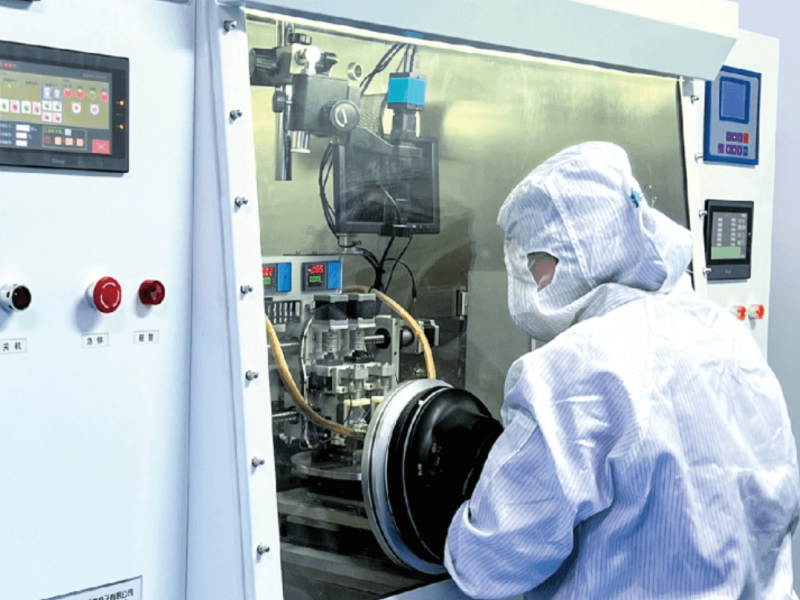
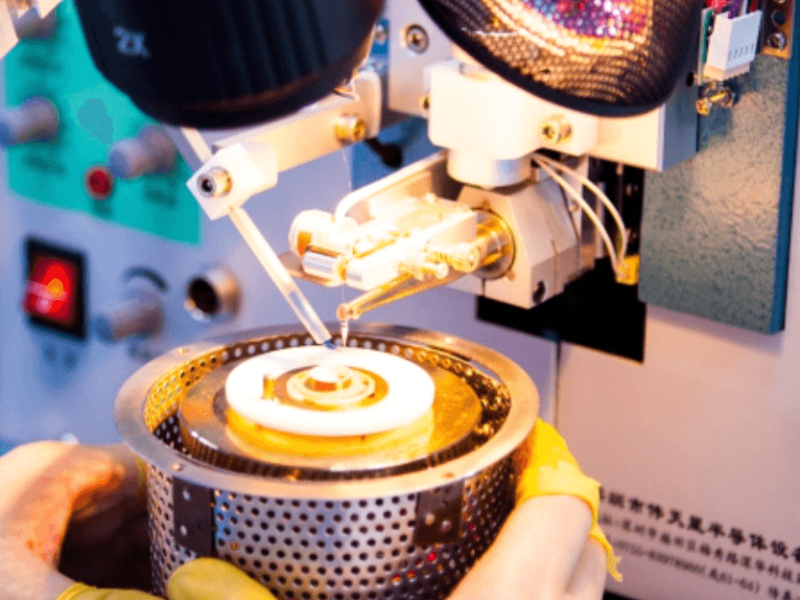
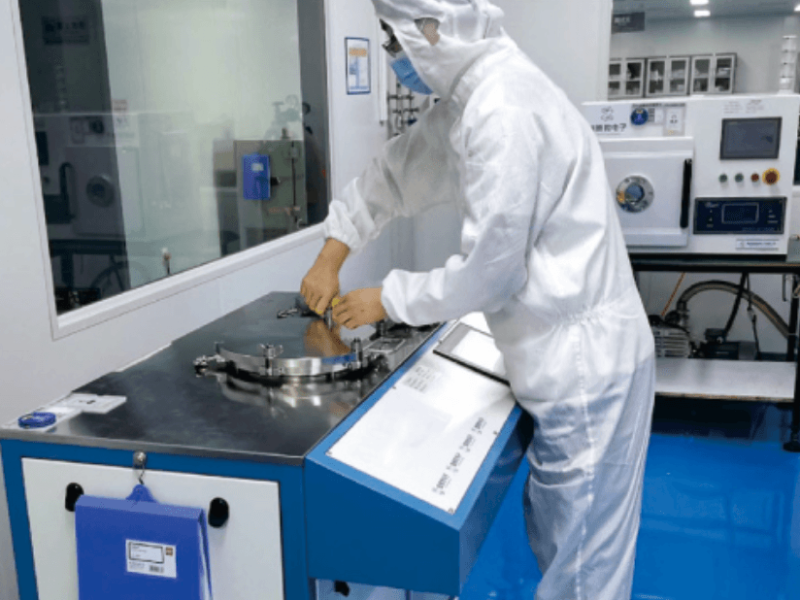
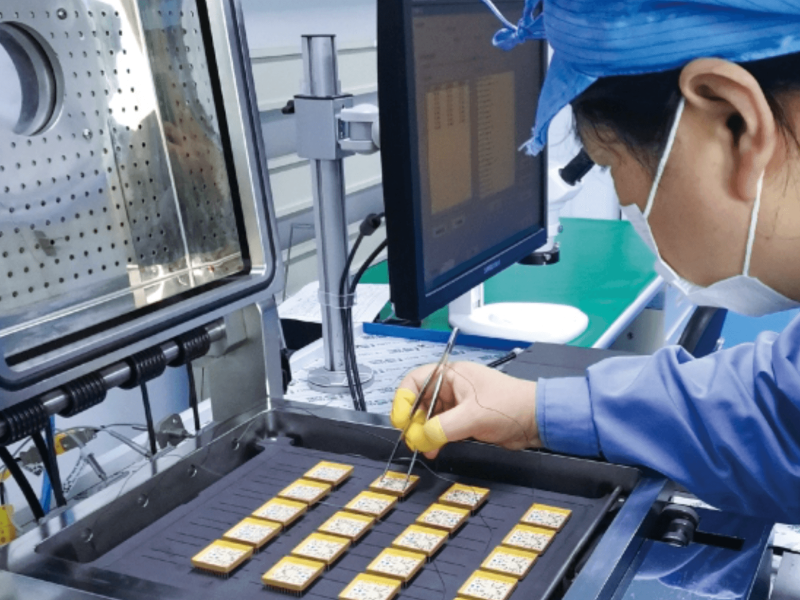
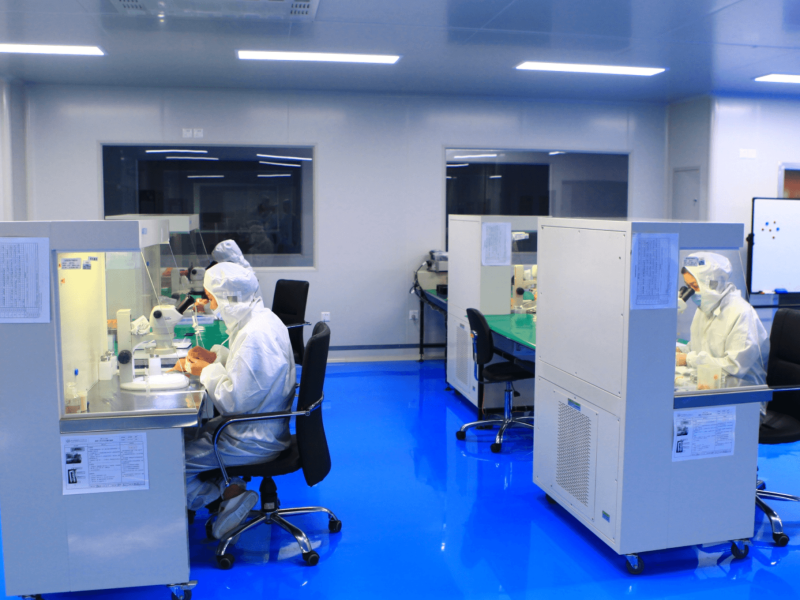
Why Choose Us
Comprehensive Solutions for All Your Navigation Needs
Commercial Grade Coverage
Bias Stability: >0.2°/h
Solution: MEMS based Gyroscope/IMU/INS
Applications: car navigation, unmanned aerial vehicles, transportation, robotics etc.
Tactical Grade Coverage
Bias Stability: 0.05°/h-0.2°/h
Solution: Fiber Optics and MEMS based Gyroscope/IMU/INS
Applications: armored vehicles operations, anti-aircraft artillery, precision targeting etc.
Navigation Grade Coverage
Bias Stability: ≤0.05°/h
Solution: Fiber Optics & Ring Laser Gyroscope/IMU/INS
Applications: medium and long-range guidance, military aviation, satellites
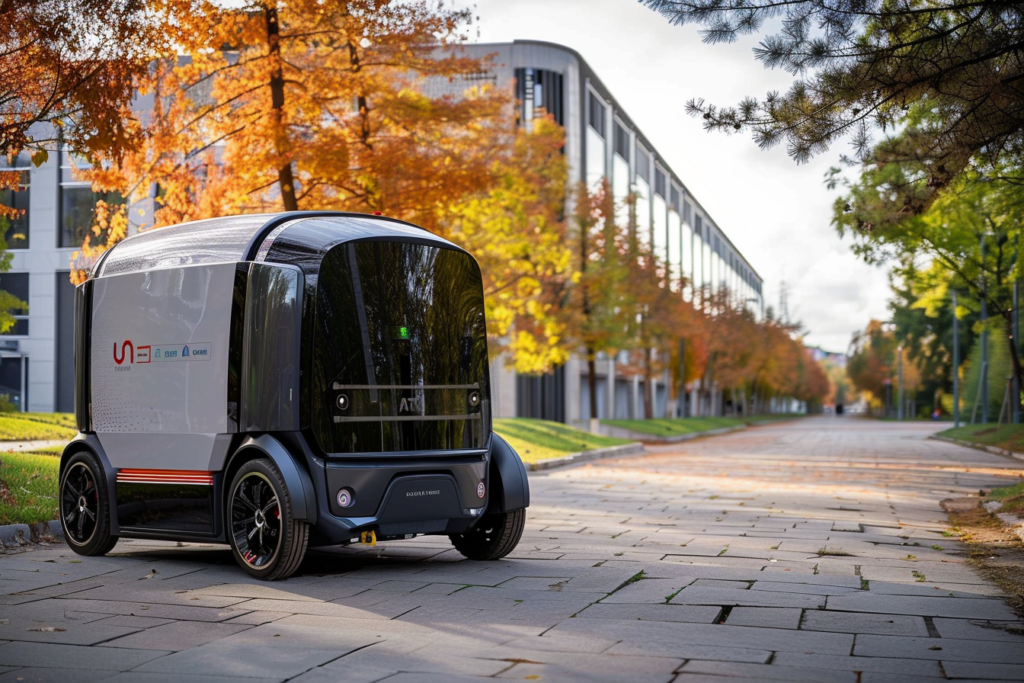
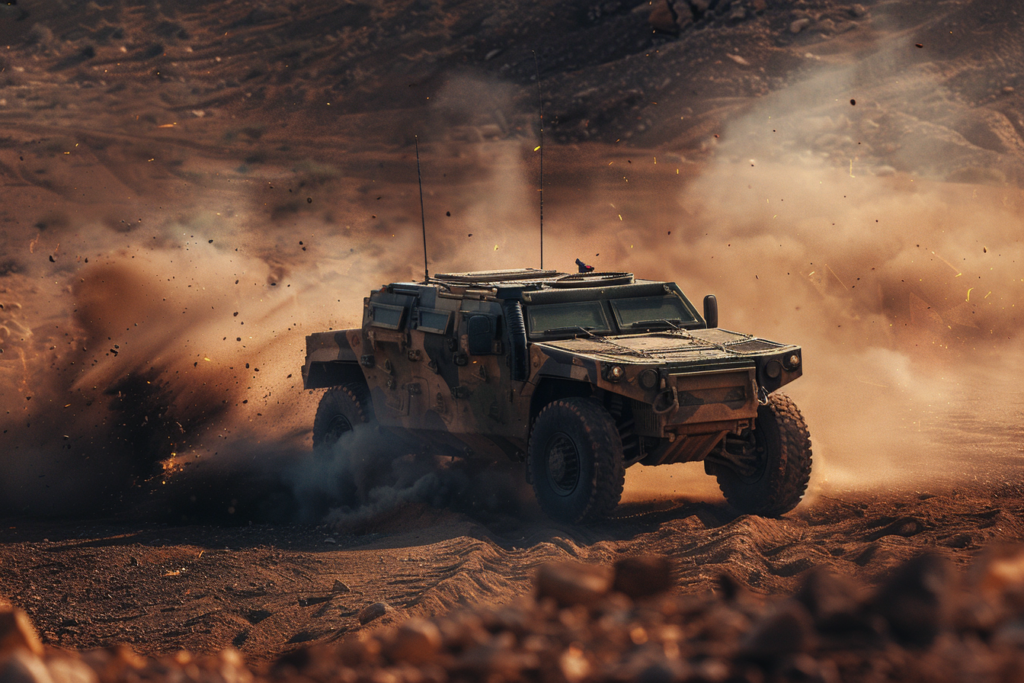
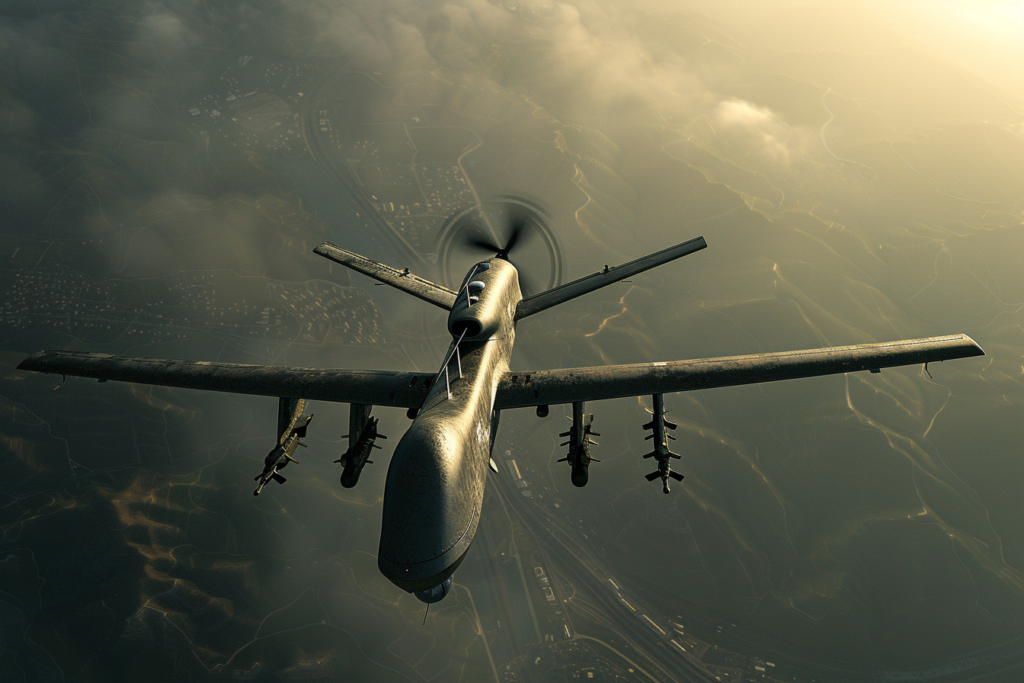
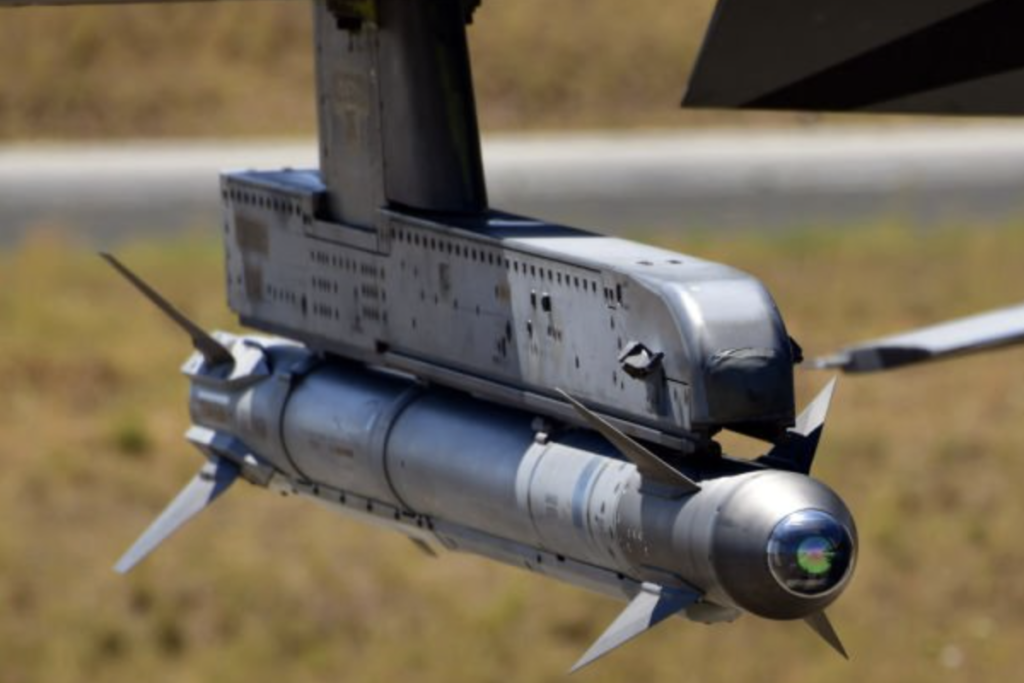
FAQS
Answers to Your Questions
An Inertial Navigation System (INS) uses inertial sensors to measure changes in motion, which helps determine the velocity, orientation, and position of an object.
The IMU, a component of the inertial navigation system, consists of sensors such as accelerometers, gyroscopes, and sometimes magnetometers.
More details:
- Accelerometers gauge an object's acceleration, tracking its changing velocity.
- Gyroscopes detect changes in angular velocity.
- Magnetometers assess the Earth’s magnetic field's strength and direction, determining orientation relative to magnetic north. The system adjusts for the discrepancy between true north and magnetic north. However, magnetic interference sources can affect a magnetometer's accuracy in most vehicles.
These sensors each have limitations, but they work better when combined. By measuring these three sensors, the inertial navigation system calculates traveled distance and heading.
An inertial navigation system measures:
- Pitch
- Roll
- Heading
An INS also incorporates a GNSS receiver, adding another sensor. This provides an absolute position rather than a relative one. While an INS alone can determine position relative to the inertial frame of reference, combining it with GNSS provides an accurate global position.
An inertial navigation system is self-contained and doesn't need satellite signals or base stations to determine position.
GNSS relies on satellite information for positioning. It's widely used in civilian, commercial, and defense applications, though it can be disrupted by atmospheric conditions and multipathing. GNSS signals can also be obstructed by tunnels or intentionally interfered with through jamming and spoofing, especially in military scenarios.
When used together, these two systems provide highly accurate positioning, with the inertial navigation system maintaining accuracy in GNSS-denied environments, enhancing GNSS navigation data.
An INS includes an Inertial Measurement Unit (IMU) and a computational unit. Starting from a known position and orientation (the inertial frame of reference), the IMU tracks changes in velocity and rotation, sending raw data to the INS computational unit, which then accurately determines the new position and orientation.
Inertial navigation systems reliably provide position data. They range from lightweight MEMS (micro-electromechanical systems) to dynamic fiber optic gyroscopes (FOG), and advanced digital fiber optic gyroscopes (DFOG).
INS is especially beneficial in environments where GNSS (global navigation satellite system) is unavailable. GNSS can be disrupted in tunnels or underwater. It can also suffer from multi-pathing or atmospheric interference. While this is a minor issue for phone navigation, precise positioning is critical for aerial surveying or defense applications.
Combining INS with GNSS is more reliable, as INS mitigates errors that GNSS alone might encounter. INS can operate effectively without base station communication, making it suitable where GNSS is inaccurate or unavailable.
Various inertial navigation systems offer different levels of accuracy.
High-end INS using fiber optic gyroscopes (FOG) are accurate within centimeters, suitable for aerospace exploration, AUVs, and defense applications. Unlike GNSS, INS is immune to jamming or spoofing as it doesn't rely on external references like satellites or base stations. GuideNav also offer cost-effective MEMS based INS for applications with less accuracy requirements.
Calibrating an INS ensures that sensor output results are accurate and consistent within specified operating conditions. Calibration involves comparing INS outputs with reference information and adjusting co-efficiency factors to match the two.
INS output can vary due to several factors, such as:
- Temperature – Affects INS output across a range of temperatures.
- Systematic error sources from accelerometers and gyroscopes including:
- Sensor bias
- Sensor output scale factor
- Sensor cross-axis sensitivity
- Sensor axis misalignment
- MEMS gyroscope G sensitivity
- Magnetic Field – INS units with magnetometers for heading determination can be affected by magnetic field changes (e.g., ferrous objects or magnets causing static interference). This error is typically calibrated once the INS is installed in its final position on a vehicle to account for static magnetic interference sources. All GuideNav products have built-in magnetic calibration software to address this issue.
INS calibration involves equipment like temperature chambers, leveling tables, rate tables, and gimbals. All GuideNav products are calibrated, tested, and conform to relevant industry standards before shipping.
INS sensors fall into five performance grades, mainly based on gyroscope performance.
While INS also uses accelerometers and magnetometers, gyroscope cost vs. performance primarily determines the performance grade. MEMS-based INS performance ranges from consumer to tactical grade, but advances in MEMS and data fusion technologies have pushed MEMS-based INS performance towards high-end tactical grade.
Performance grade: Consumer
- Gyro Bias Stability: over 20 °/h
- Cost: $
- Example Applications: Motion detection
- Sensor Technology: MEMS
Performance grade: Industrial/Tactical
- Gyro Bias Stability: 5 – 20 °/h
- Cost: $$
- Example Applications: Robotics
- Sensor Technology: MEMS Based
Performance grade: High-End Tactical
- Gyro Bias Stability: 0.1 – 5 °/h
- Cost: $$$
- Example Applications: autonomous systems
- Sensor Technology: MEMS / FOG (Fiber-optic gyroscope) /RLG (Ring laser gyroscope)
Performance grade: Navigation
- Gyro Bias Stability: 0.01 – 0.1 °/h
- Cost: $$$$
- Example Applications: Aircraft navigation
- Sensor Technology: FOG/RLG
Performance grade: Strategic
- Gyro Bias Stability: 0.0001 – 0.01 °/h
- Cost: $$$$$
- Sensor Technology: FOG/RLG