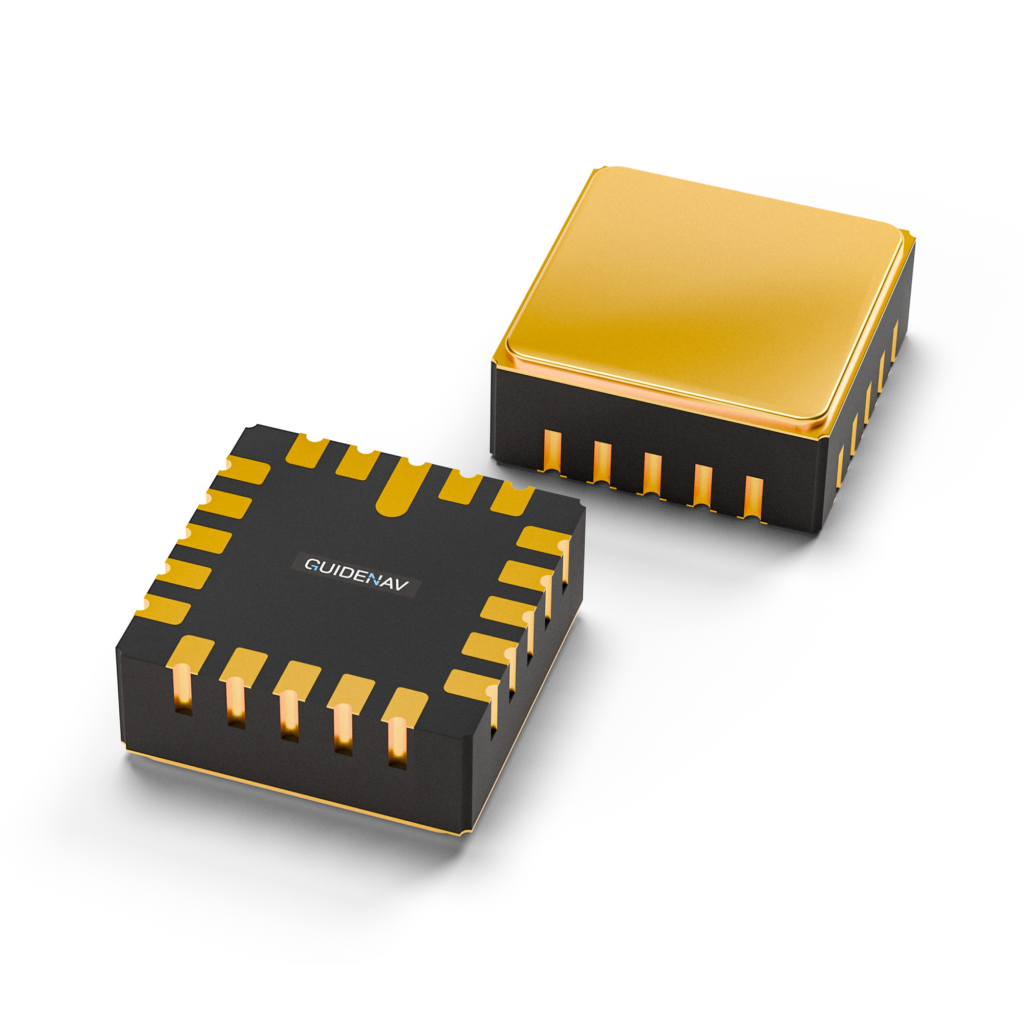
High-Performance MEMS Acceleration Sensors
MEMS Accelerometer
Over 5 Million MEMS Accelerometers Delivered
Custom Solutions Trusted by Global Key Players
GuideNav offers a range of high-precision MEMS accelerometer sensors, designed to meet the stringent requirements of industries such as aerospace, defense, and industrial automation. Our MEMS accelerometers are characterized by their compact size, low power consumption, and exceptional reliability, ensuring stable performance even in the most demanding environments.
Guidenav‘s Featured MEMS Acceleration Sensors
FEATURED MEMS ACCELEROMETER
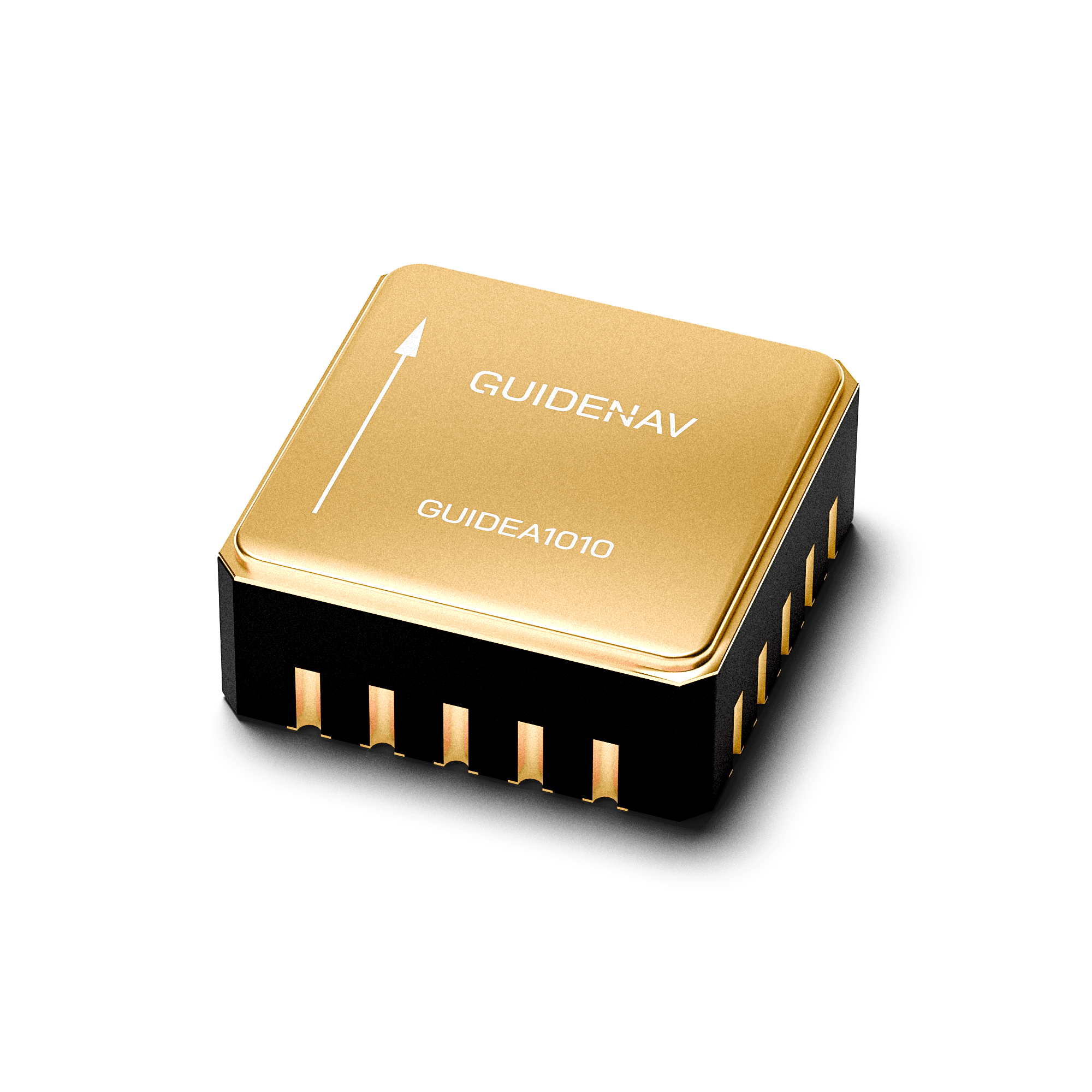
- Full-Scale acceleration: ± 10g
- Bias stability@10s: ≤20µg
- Noise: ≤15 µg/√Hz
- Size(mm): 8.9*8.9*3.1
- Bandwidth(-3db): ≥100Hz
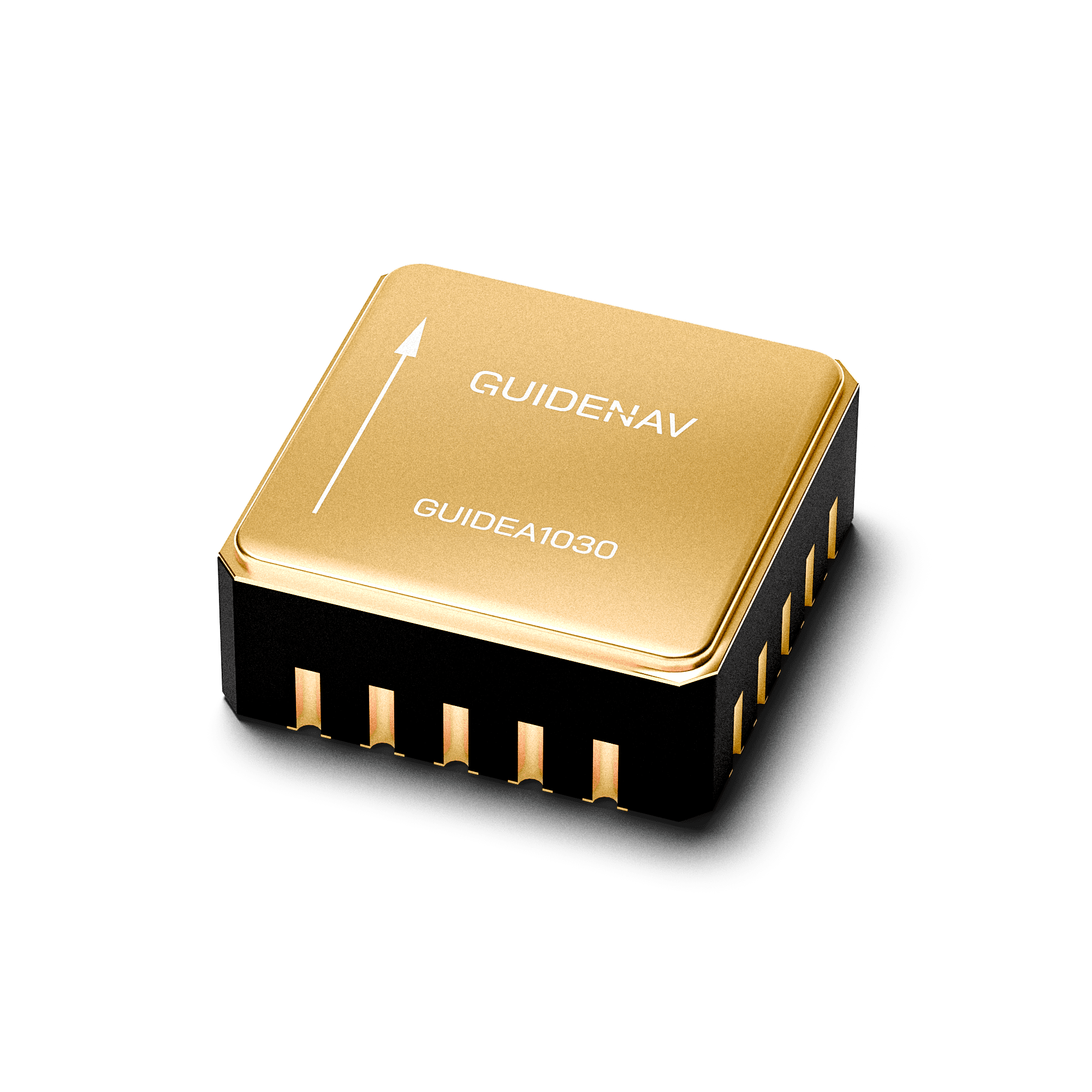
- Full-Scale acceleration: ± 30g
- Bias stability@10s: ≤40µg
- Noise: ≤30 µg/√Hz
- Size(mm): 8.9*8.9*3.1
- Bandwidth(-3db): ≥100Hz
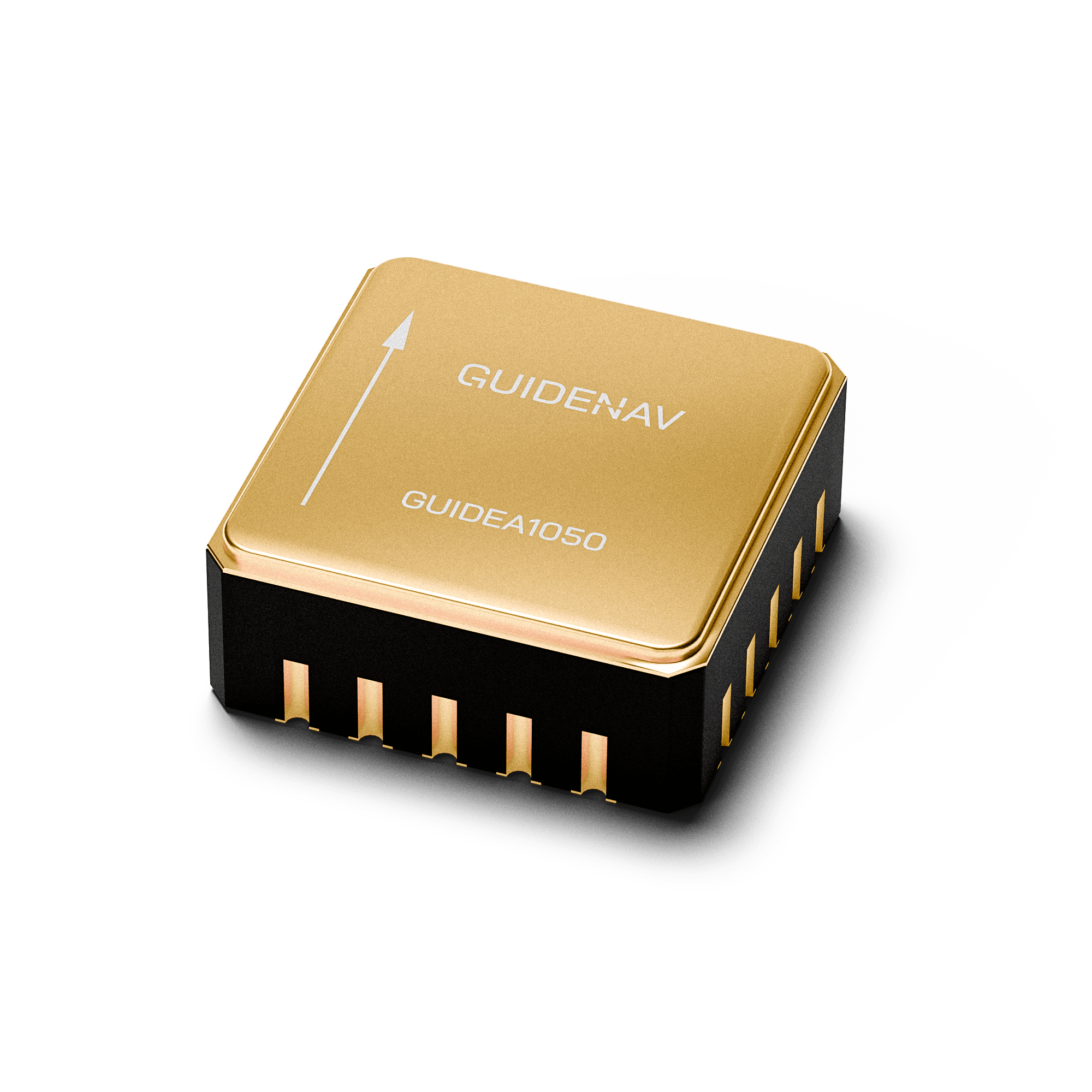
- Full-Scale acceleration: ± 50g
- Bias stability@10s: ≤60µg
- Noise: ≤50 µg/√Hz
- Size(mm): 8.9*8.9*3.1
- Bandwidth(-3db): ≥100Hz
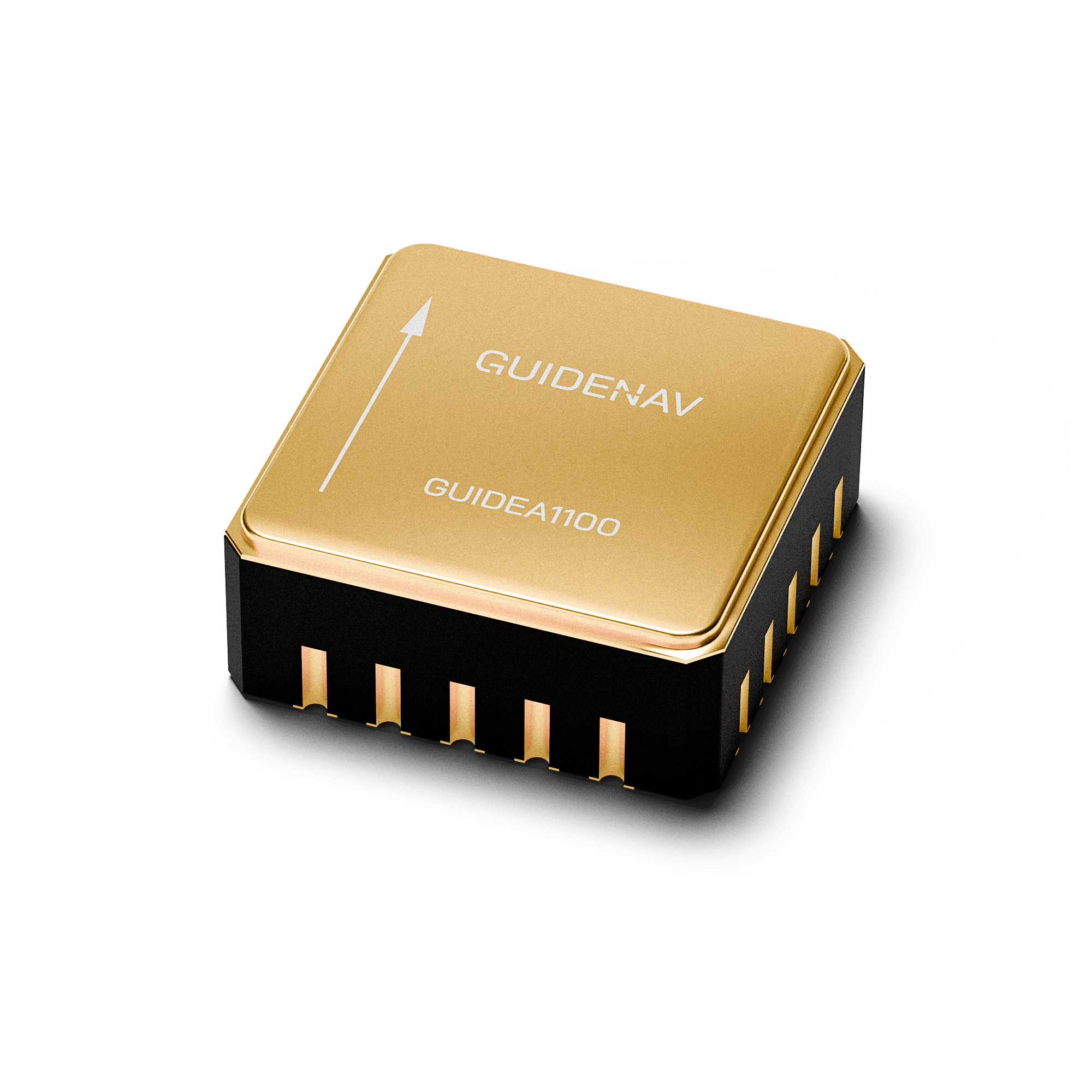
- Full-Scale acceleration: ± 100g
- Bias stability@10s: ≤150µg
- Noise: ≤130 µg/√Hz
- Size(mm): 8.9*8.9*3.1
- Bandwidth(-3db): ≥100Hz
Get Your Custom Solution Now
Your project deserves a solution tailored to your exact specifications. To ensure we provide the best MEMS Acceleration Sensors for your needs, we invite you to share the specific parameters and performance requirements of your applications. Whether it’s precision, stability, or size constraints, our team is ready to help you find the perfect fit.
Table of Contents
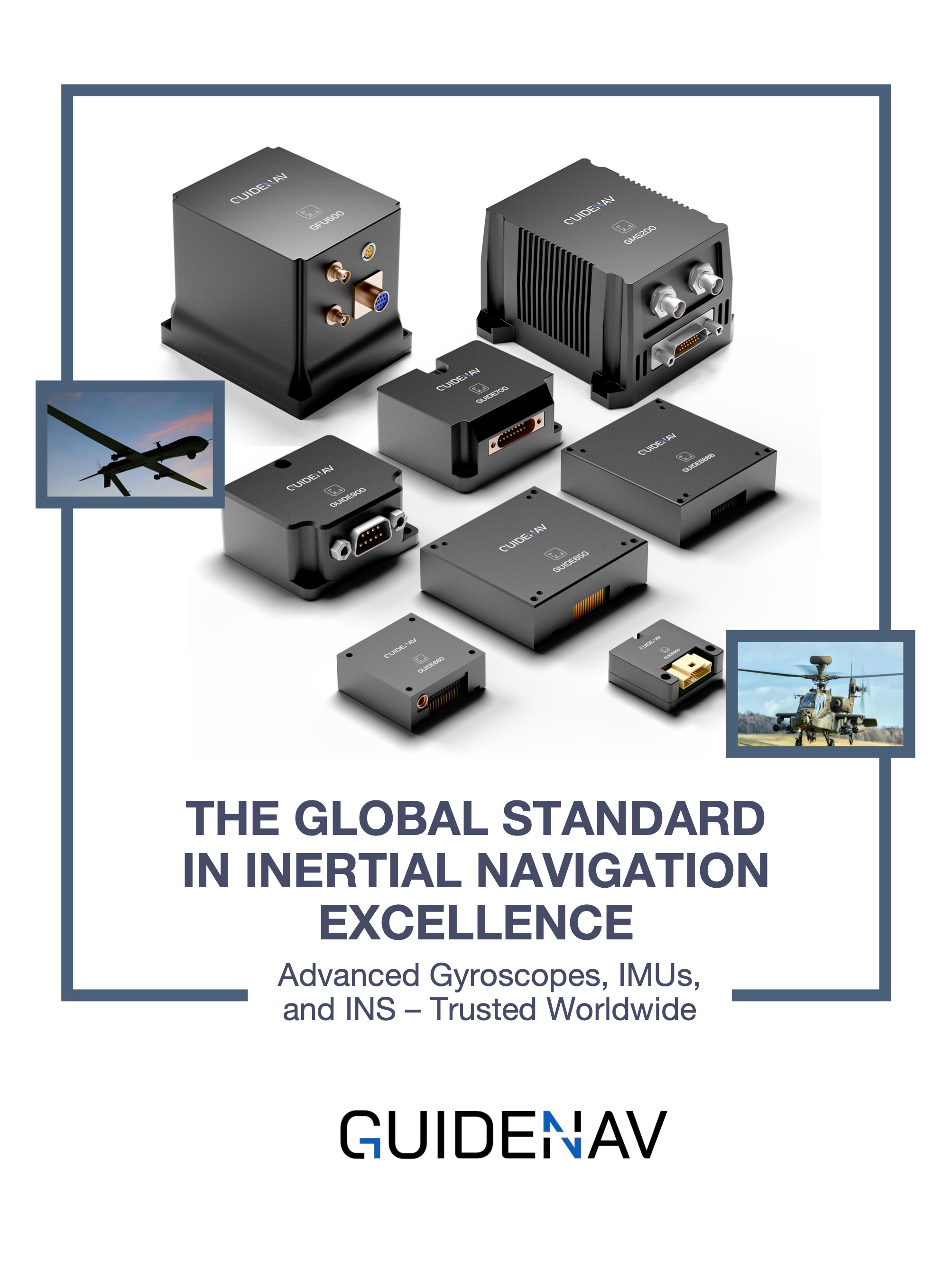
Download this page as a PDF
To save you time, we have also prepared a PDF version containing all the contents of this page, only leave your email and you will get the download link immediately.
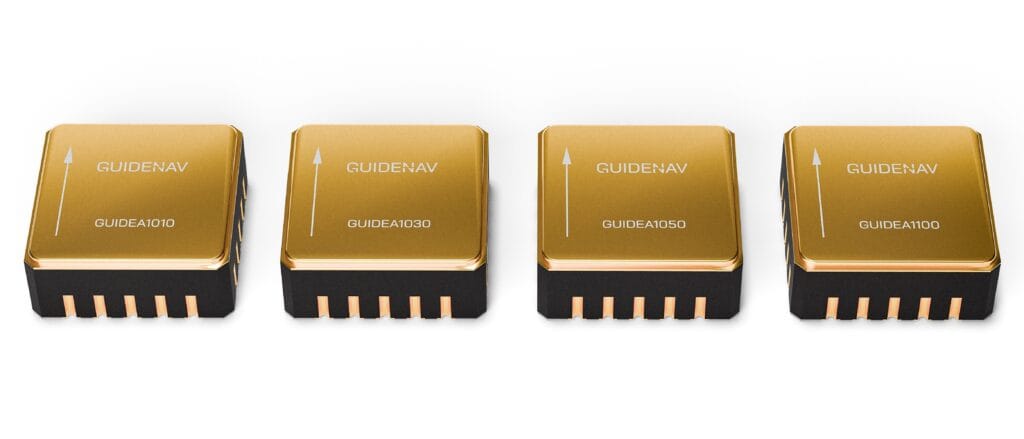
Introducing MEMS Accelerometer
What is a MEMS Accelerometer?
A MEMS (Micro-Electro-Mechanical Systems) accelerometer is a small, highly accurate sensor used to measure acceleration forces. It works by detecting changes in velocity, allowing it to measure movements or vibrations in various directions. MEMS accelerometers are widely used due to their compact size, low power consumption, and high reliability. These sensors are ideal for applications in aerospace, defense, automotive, and consumer electronics, offering precise and real-time data for system performance and stability.
Applications of MEMS Accelerometers
MEMS Accelerometer Applications in System Automation, Drones, and Robotics
01
Aerospace and Aviation
In aerospace, MEMS accelerometers are integral to flight control systems, providing real-time data for stable flight and precise navigation. These sensors help aircraft and spacecraft maintain accurate orientation and motion even in GPS-denied or extreme environments, ensuring reliable performance during high-G maneuvers or space launches.
02
Defense and Military
MEMS accelerometers play a vital role in defense technologies, enabling precise motion tracking and navigation in systems like UAVs, missiles, and tactical equipment. These sensors ensure accurate guidance and targeting, even in harsh environments, by providing real-time acceleration data to maintain system stability and mission success.
03
Industrial Automation
In industrial automation, MEMS accelerometers are used for predictive maintenance, monitoring vibrations, and improving machinery stability. These sensors detect irregular motions or faults in equipment, helping manufacturers optimize performance, reduce downtime, and extend machinery lifespan, ensuring smooth operations on assembly lines and production systems.
04
Robotics
MEMS accelerometers provide essential feedback on movement, enabling precise motion control in robotic arms, mobile robots, and autonomous vehicles. These sensors enhance task execution by ensuring accurate navigation and adjusting movements, vital for complex tasks in industrial settings, autonomous navigation, and robotic surgeries.
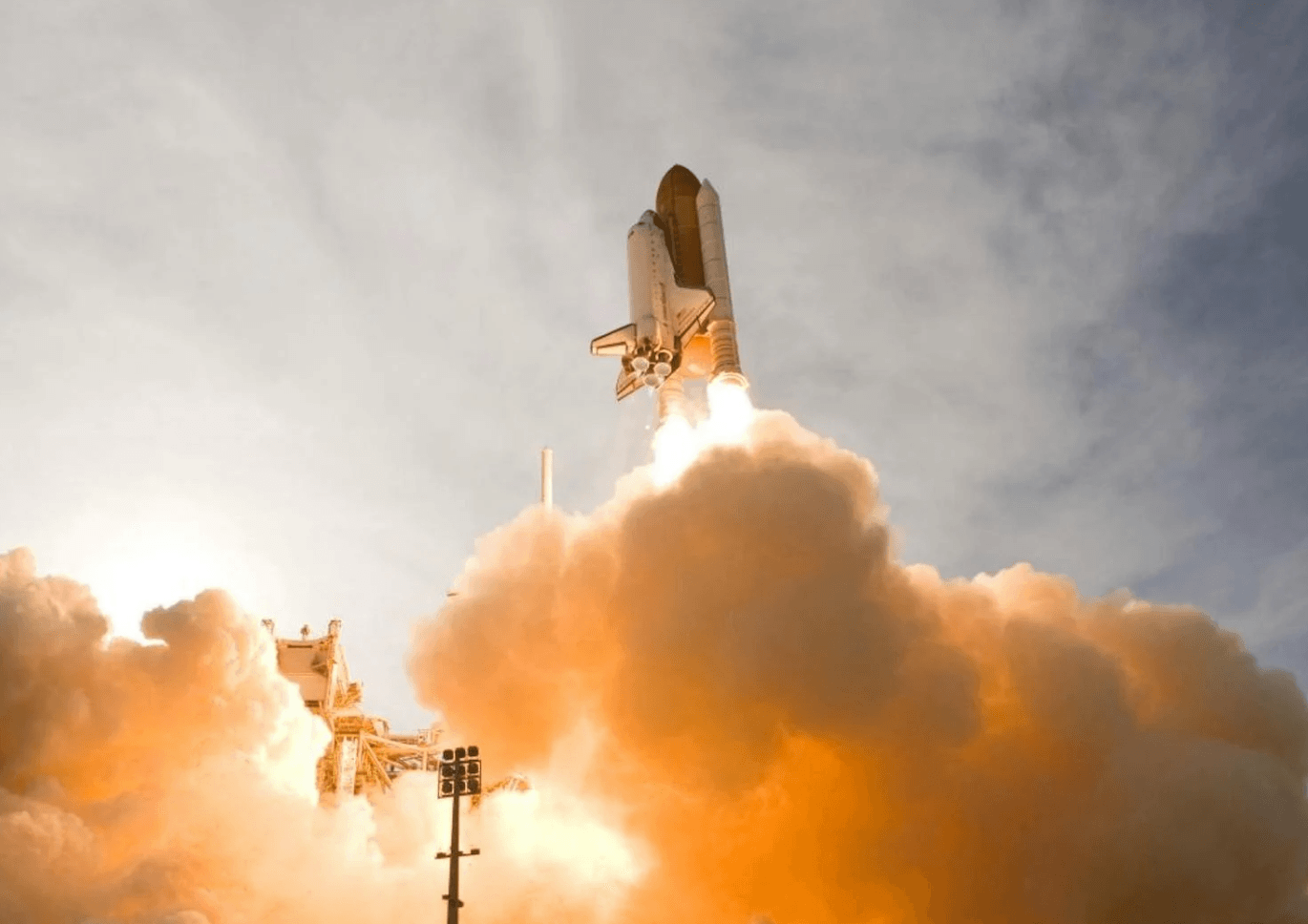
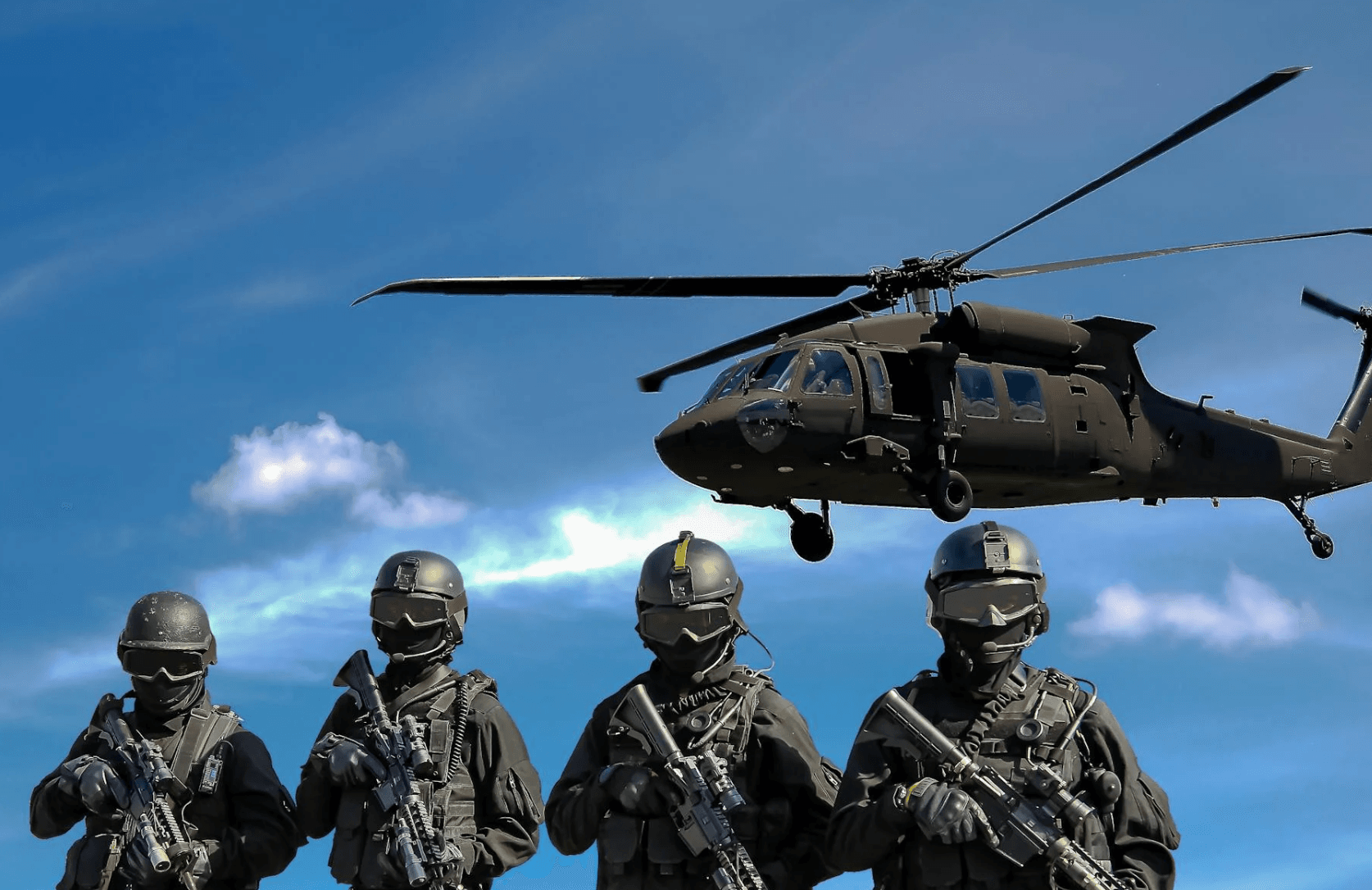
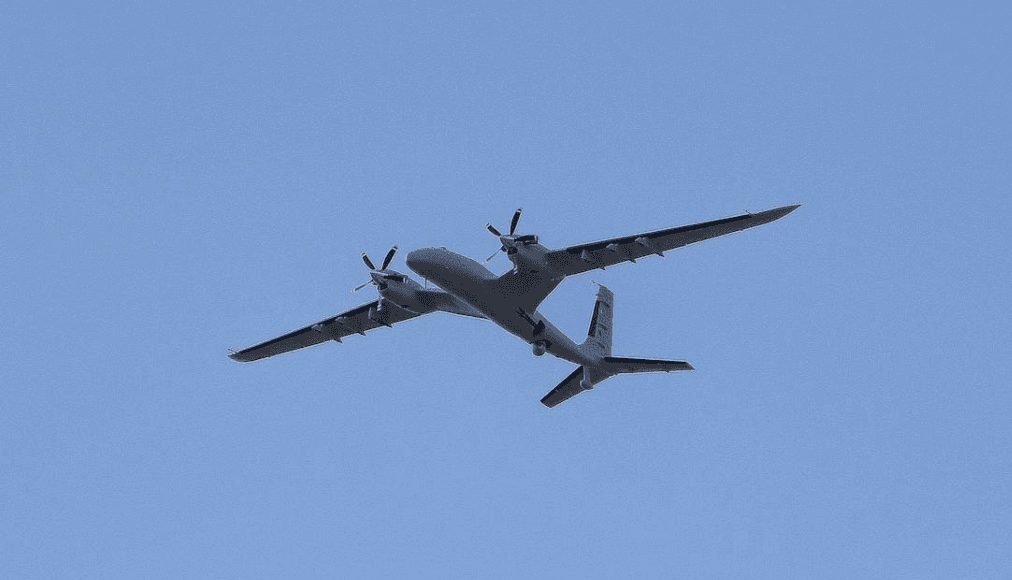
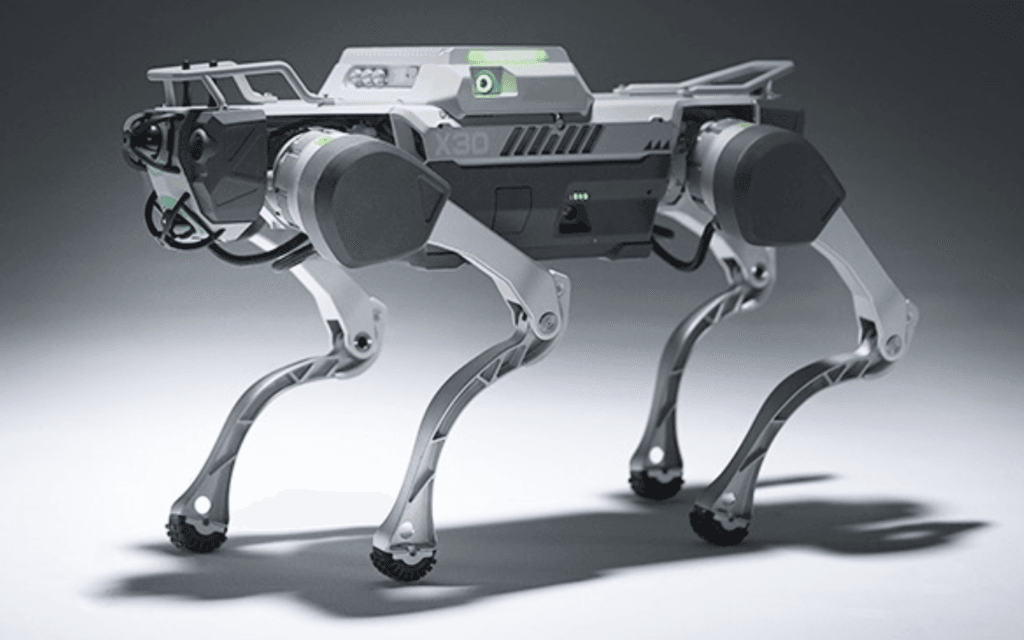
MEMS Accelerometers in inertial measurement unit (IMU)
How MEMS Accelerometer Improve IMU Performance
Accurate Motion Sensing
MEMS accelerometers measure acceleration in multiple axes, while gyroscopes detect angular velocity. Together, they enable the Inertial Measurement Unit to accurately track movement, orientation, and velocity changes in real time. This combined data provides a more complete picture of an object’s motion.Improved Navigation and Positioning
Integrating MEMS accelerometers with gyroscopes helps improve the accuracy of navigation systems, especially in GPS-denied environments. While the accelerometer provides data on linear motion, the gyroscope tracks rotational movements, allowing the MEMS IMU to calculate precise position and orientation, even without external signals.Enhanced Stability and Reliability
MEMS accelerometers and gyroscopes complement each other by correcting individual sensor errors. The accelerometer’s sensitivity to linear acceleration helps compensate for the gyroscope’s drift, while the gyroscope’s high-frequency data corrects the accelerometer’s low-frequency inaccuracies, resulting in a more stable and reliable Inertial Measurement Unit system.
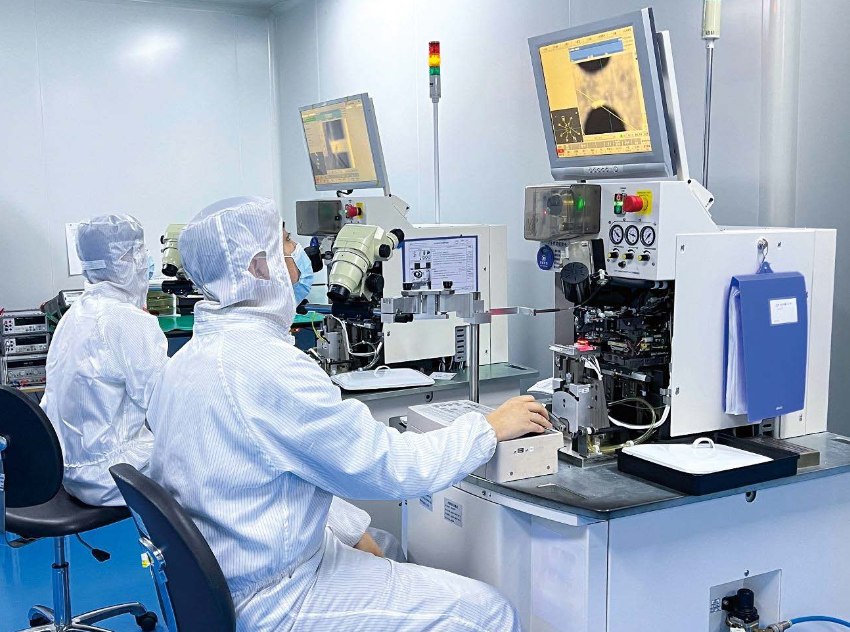
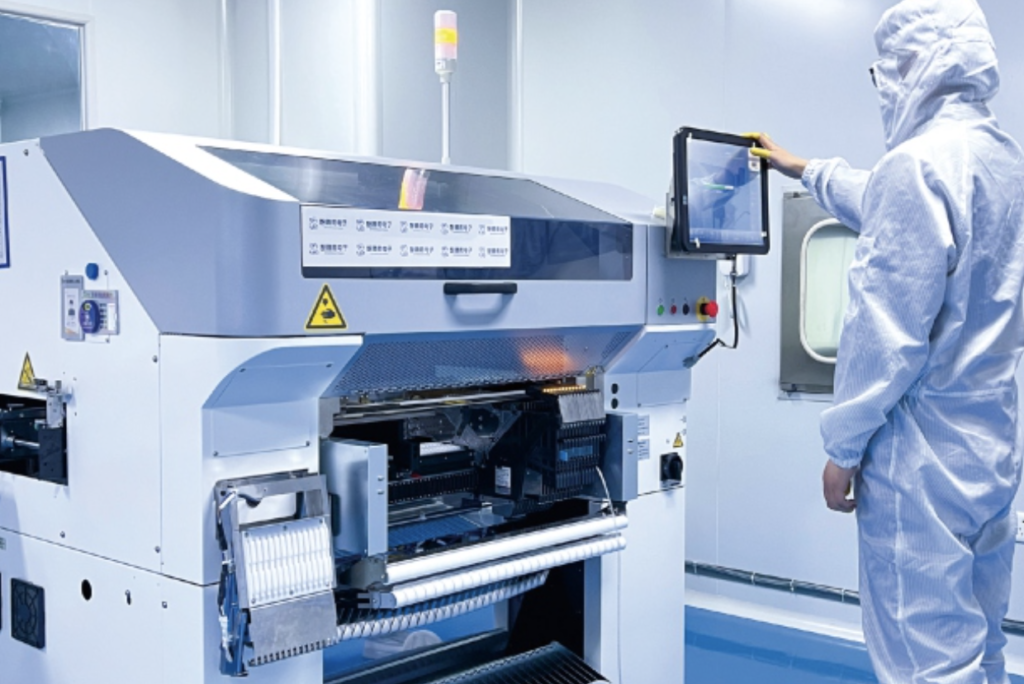
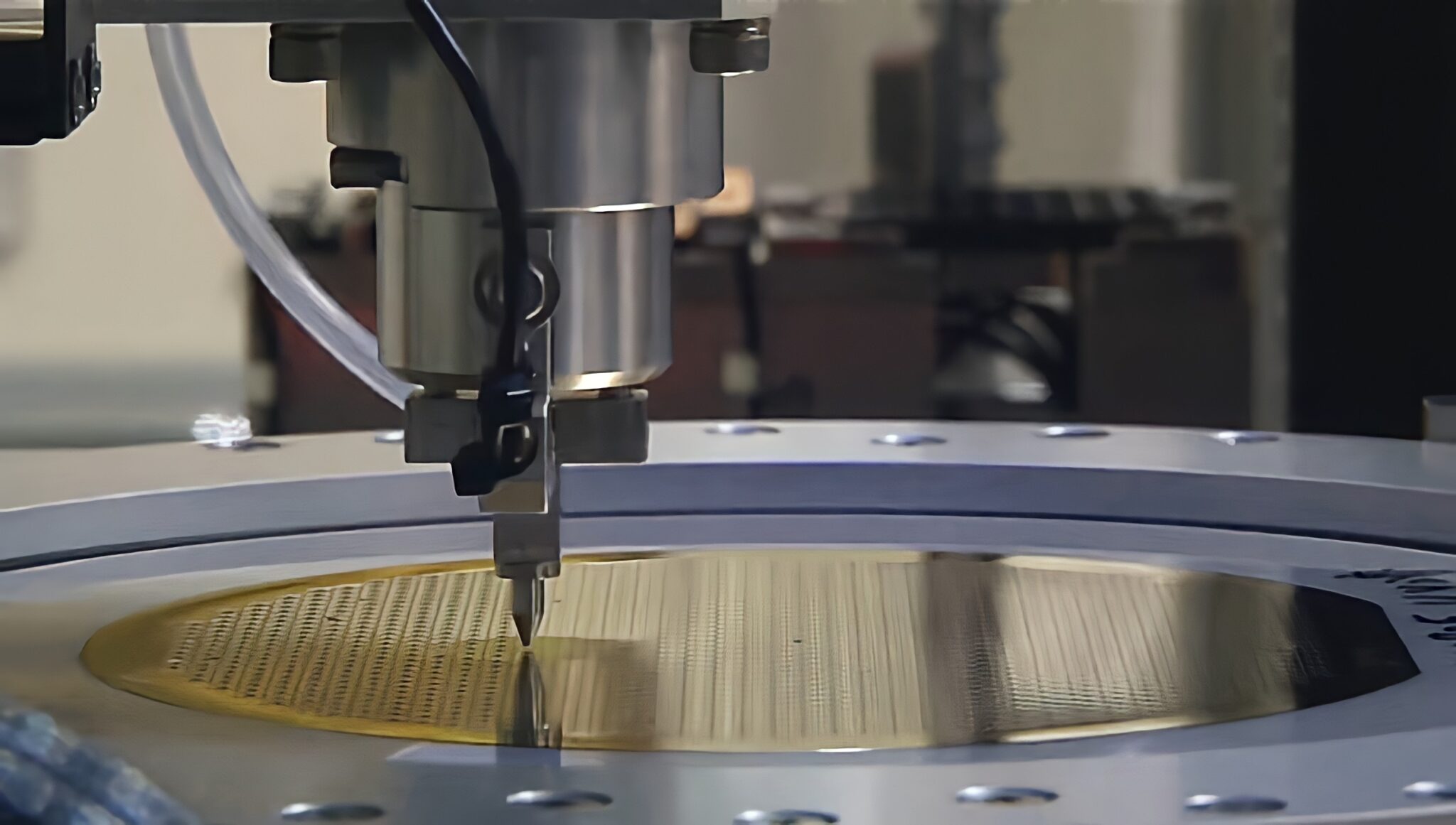
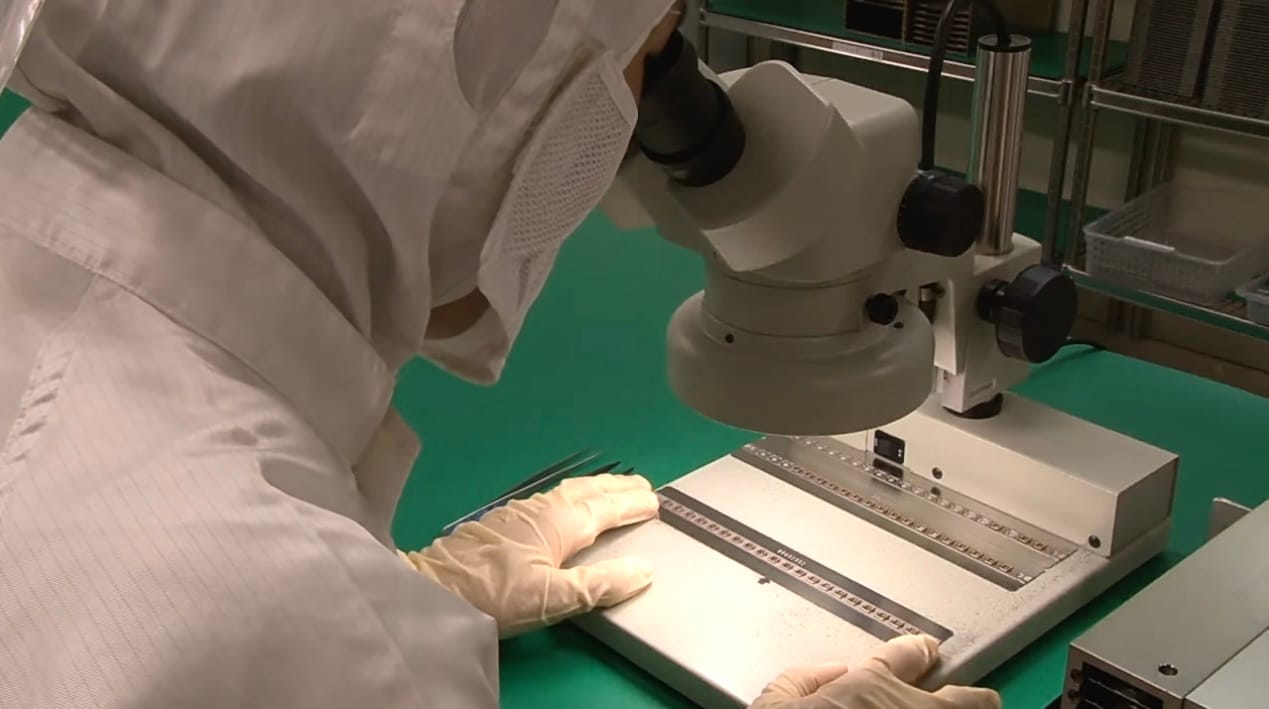
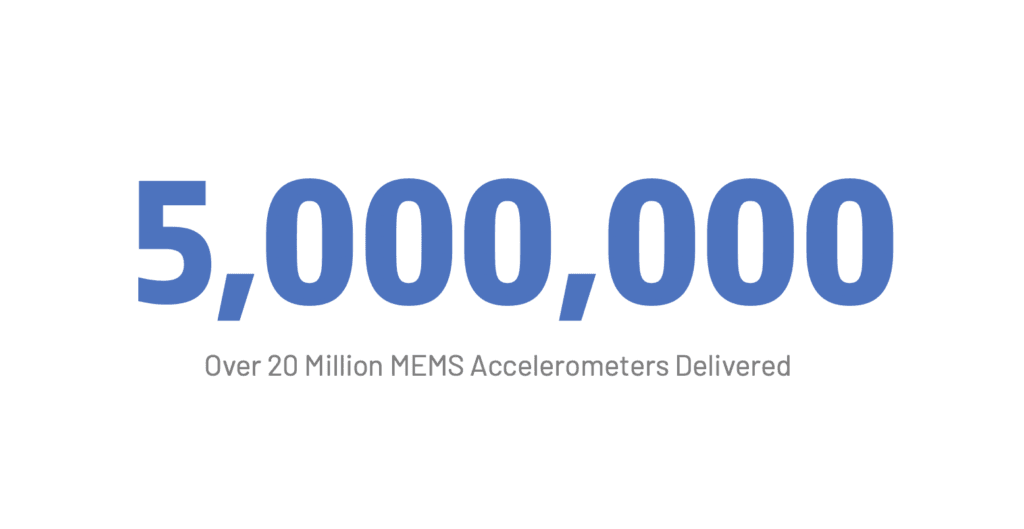
Key parameters of MEMS Accelerometer
Main Specifications of MEMS Accelerometers: Top 3 Key Parameters
1. Measurement Range
- Definition: The range of acceleration the accelerometer can measure.
- Example: ±2g, ±5g, ±10g.
- Relevance: Ensures the sensor can handle the forces in the application, from consumer electronics to aerospace.
2. In-Run Bias Stability (@10s)
- Definition: Stability of the accelerometer’s zero point over time.
- Example: 20 μg @10s.
- Relevance: Ensures long-term stability and accuracy, essential for navigation and high-precision applications.
3. Noise Density
- Definition: The noise in the accelerometer’s output per unit bandwidth.
- Example: 20 μg/√Hz.
- Relevance: Determines the sensor’s sensitivity and accuracy, especially important for applications needing low-noise performance.
MEMS Accelerometer vs Quartz Accelerometer: Which is Better?
MEMS Accelerometers: With advancements in MEMS technology, these accelerometers are now not only prevalent in consumer electronics but are also integral to military, aerospace, and industrial applications. They are commonly used in MEMS IMUs (Inertial Measurement Units), offering a compact, low-power, and cost-effective solution without compromising on performance. When integrated into MEMS IMUs, MEMS accelerometers enable high-precision navigation, guidance, and control systems for drones, autonomous vehicles, missile guidance systems, and space exploration. This integration allows systems to achieve real-time data processing with enhanced performance, even in constrained environments where size and power are critical factors.
Quartz Accelerometers: Quartz accelerometers still provide superior accuracy and temperature stability, making them the preferred choice for the highest-precision applications in aerospace, defense, and scientific research. Their durability and stability in extreme conditions remain unmatched, making them ideal for geophysical research, military-grade instrumentation, and space missions.
Feature | MEMS Accelerometer | Quartz Accelerometer |
---|---|---|
Size | Extremely small, ideal for compact systems | Larger, bulkier design |
Power Consumption | Very low, suitable for portable and wearable devices | Higher, needs more power, less suitable for battery-powered systems |
Cost | Low cost, mass production advantages | High cost, especially for high-precision versions |
Accuracy | High accuracy, suitable for high-performance applications | Exceptional accuracy, ideal for extreme precision in scientific and military uses |
Temperature Stability | Can be sensitive to temperature changes, but modern MEMS designs have improved stability | Excellent temperature stability, retains high accuracy across extreme ranges |
Durability | Robust, increasingly suited for military and aerospace environments | Extremely durable, ideal for high-shock, extreme environments |
Bandwidth and Response Time | Fast response, suitable for real-time control and feedback | Excellent bandwidth and stability, optimized for precision |
Applications | Aerospace, defense, drones, industrial automation, consumer electronics | Aerospace, defense, geophysical research, high-precision instrumentation |
MEMS Accelerometer Selection Guide
6 Steps to Select the Right
MEMS Accelerometer
STEP 1
Define Your Application
- Purpose: Are you measuring basic motion or precise acceleration?
- Environment: Will it be exposed to extreme temperatures, shock, or vibration?
- Precision: Do you need high accuracy or general motion detection?
STEP 2
Key Performance Specifications
- In-Run Bias Stability: Ensures consistent output over time.
- Measurement Range: Match to expected forces.
- Noise Density: Affects accuracy, especially for small accelerations.
STEP 3
Consider Environmental Factors
- Temperature Range: Ensure the sensor handles your operating conditions.
- Shock Resistance: Important for impact-prone environments (e.g., automotive).
- Vibration Resistance: For industrial or high-vibration applications.
STEP 4
Power Consumption
- Why: Crucial for battery-powered applications like drones or wearables.
- What to look for: Low power consumption for extended battery life.
STEP 5
Interface Type
- Why: Choose based on your system’s design.
- What to look for: I2C or SPI for high-speed data, analog output for simpler systems.
STEP 6
Vendor Support and Customization
- Why: For specialized applications, vendor support and customization options are crucial.
- What to look for: Check if the vendor offers custom solutions and strong technical support.
MEMS Accelerometer Manufacturer
Why Choose Guidenav?
Trusted by keyplayers
Our advanced inertial navigation products are trusted by leading organizations in the aerospace, defense, commercial, and industrial sectors from over 25 countries. Our reputation for reliability and precision sets us apart.
Top Performance
Our products deliver top-tier performance with excellent bias stability. Designed for the most demanding applications, our MEMS based IMU can reach bias instability as precise as ≤0.1°/h.
Proven in Harsh Environment
Our solutions are built to withstand extreme conditions, providing consistent performance in harsh environments.
Excellent Performance under Vibrations
Our MEMS and FOG IMU technology excels in high-vibration settings, ensuring accuracy and stability even in the most challenging operational environments.
PLUG & PLAY System
Our systems are designed for easy integration, offering plug-and-play solutions that simplify installation and reduce setup time, allowing you to focus on your mission.
ITAR-FREE
Our products are ITAR-free, offering you the advantage of easier international transactions and fewer regulatory hurdles. Choose GuideNav for seamless global operations.
Our Factory - See to Believe
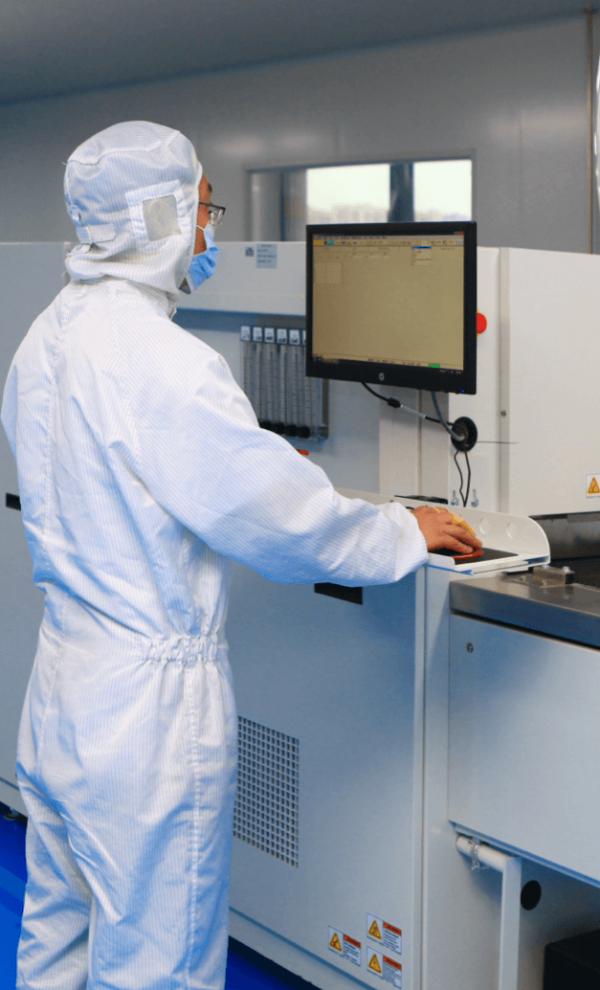
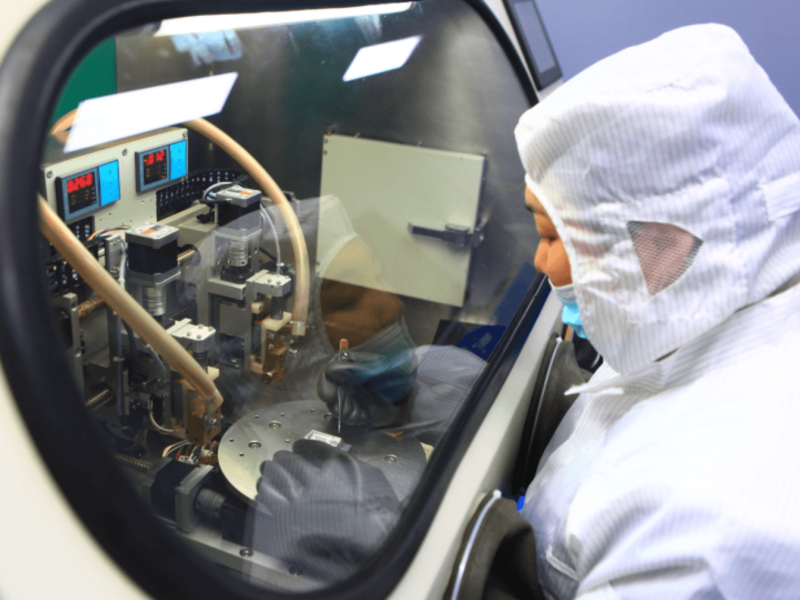
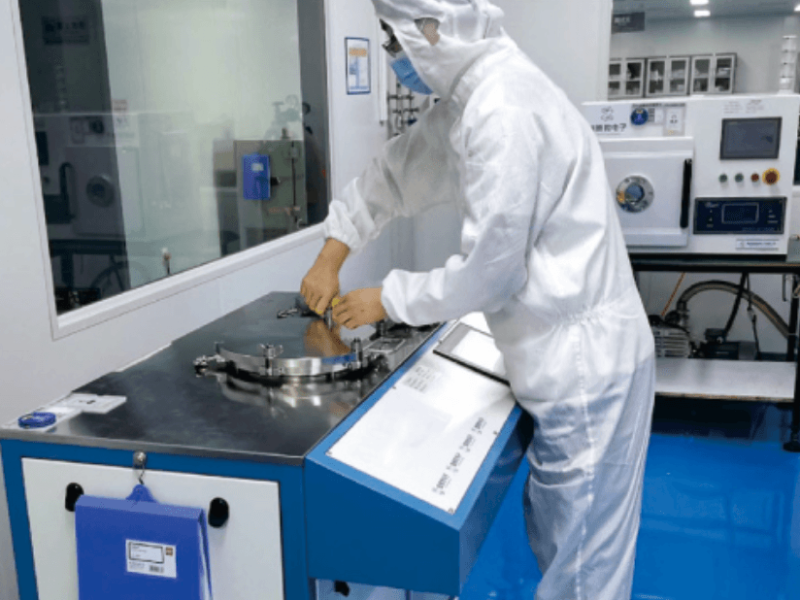
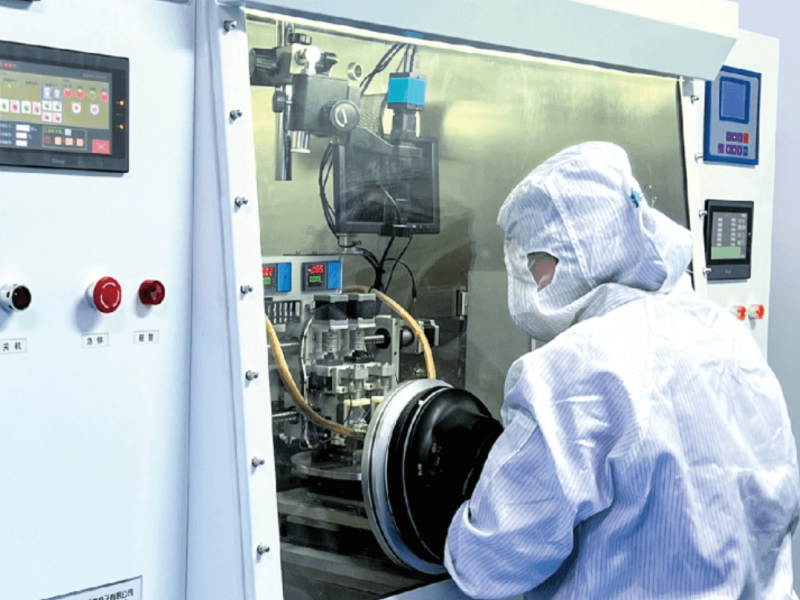
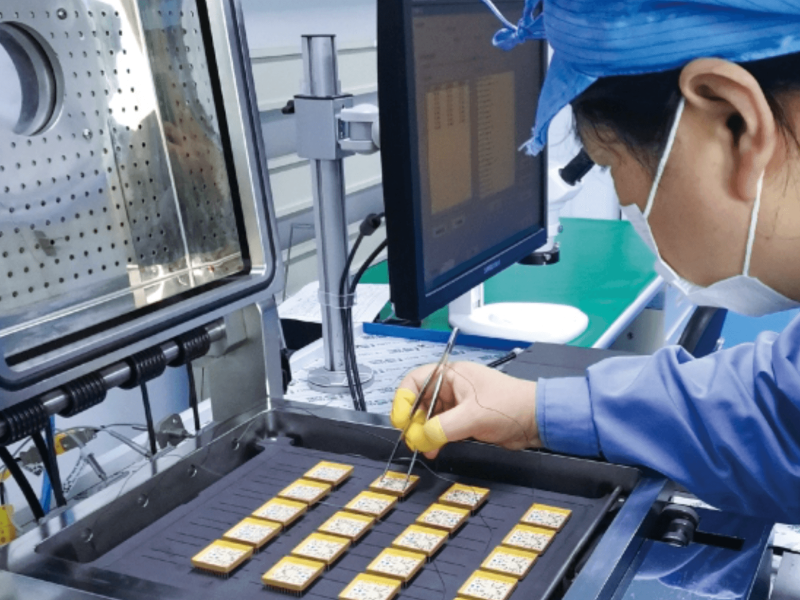
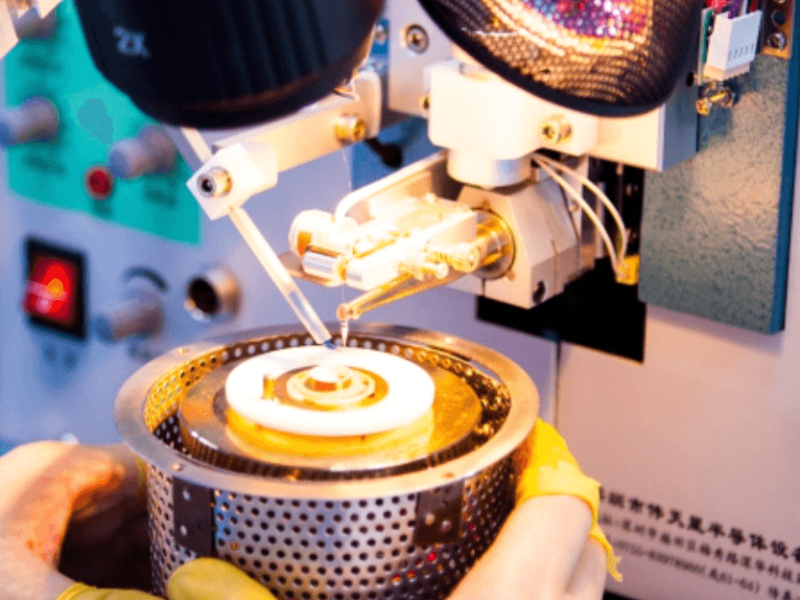
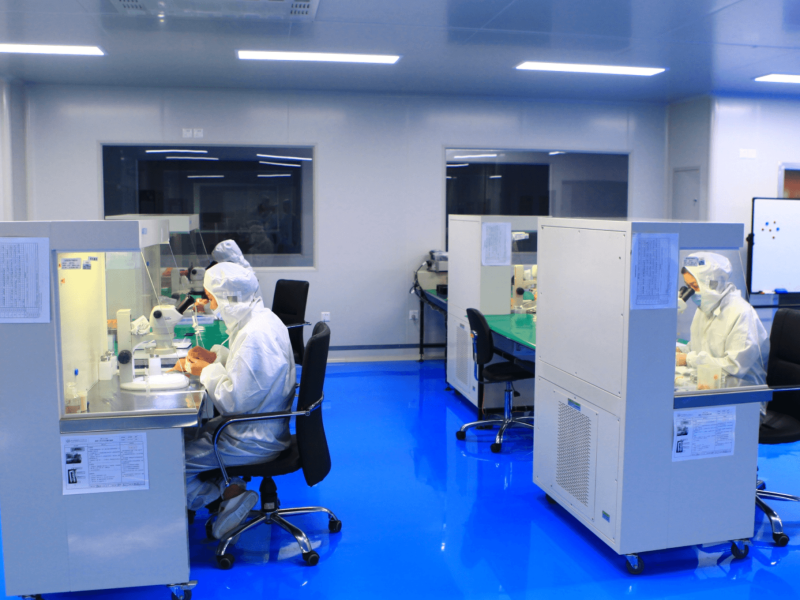
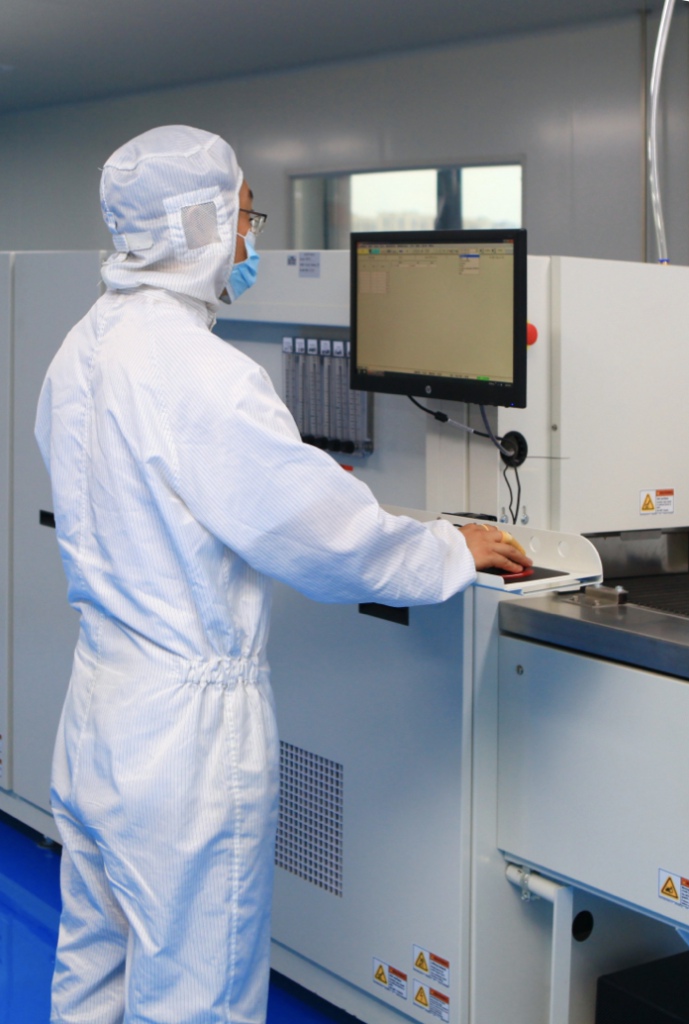
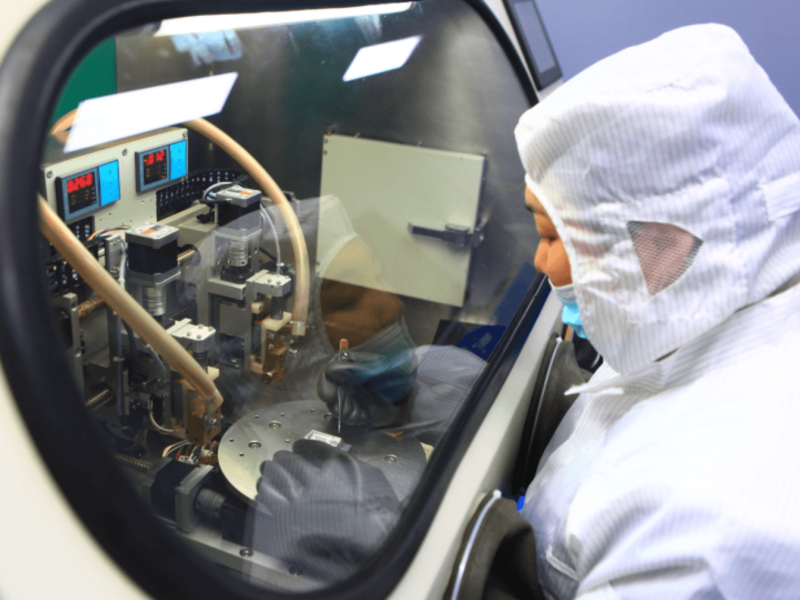
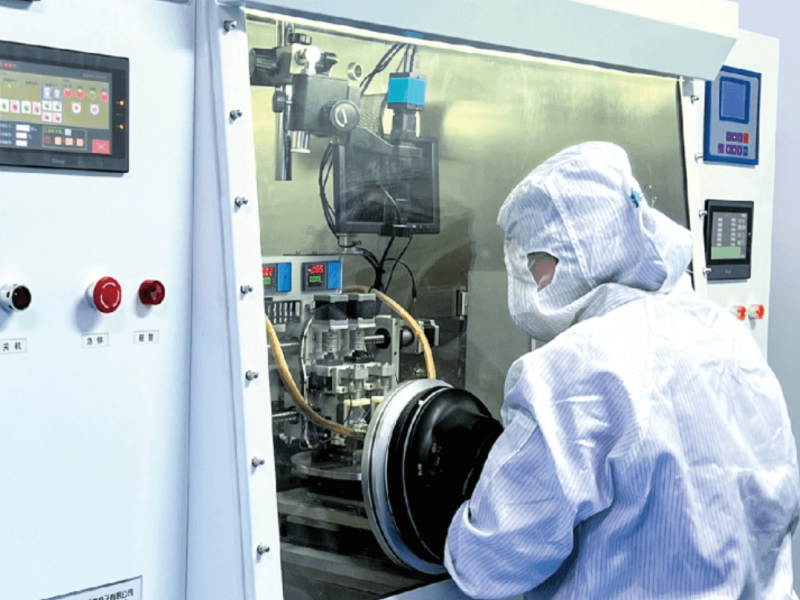
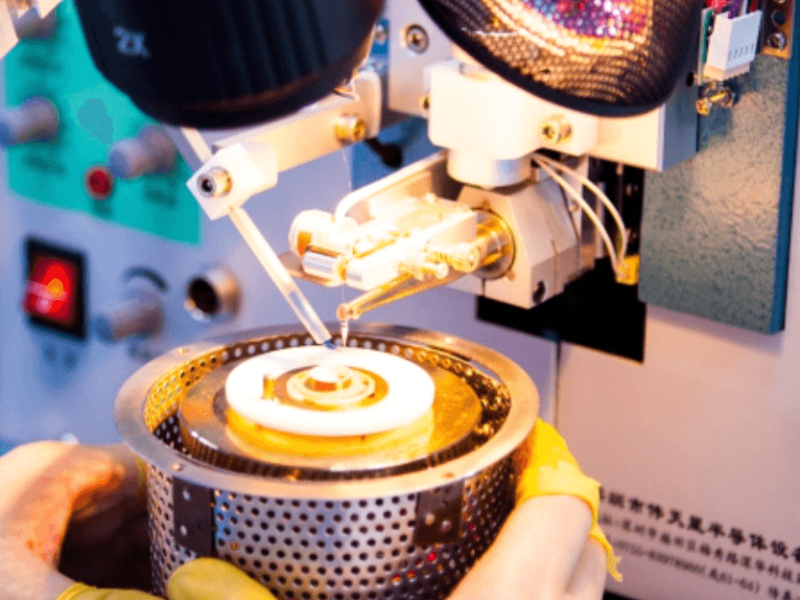
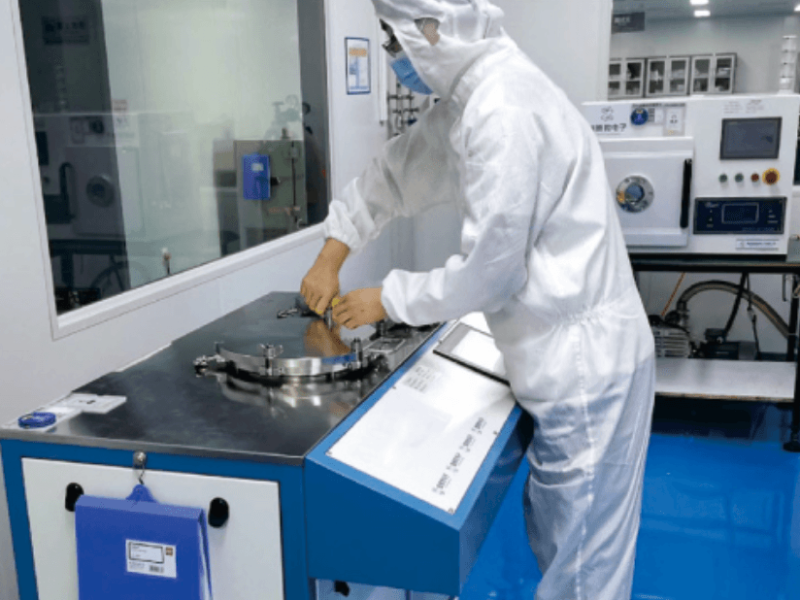
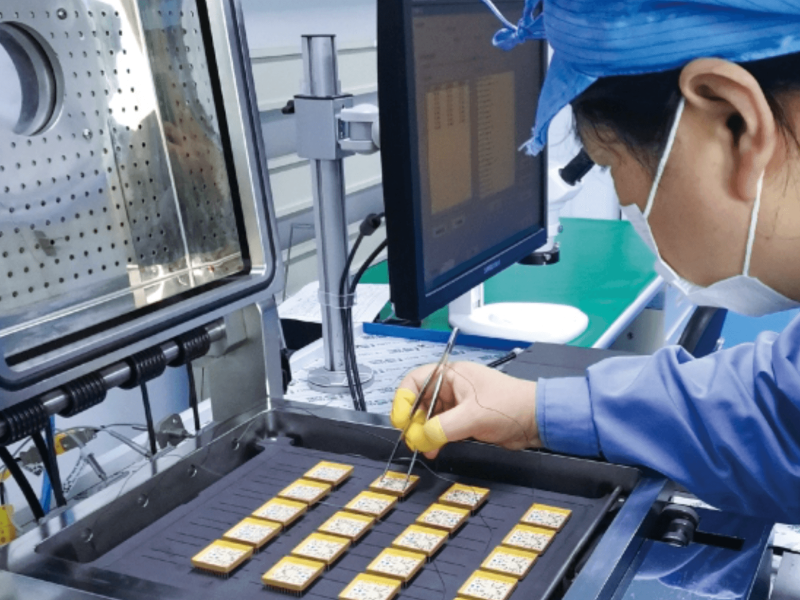
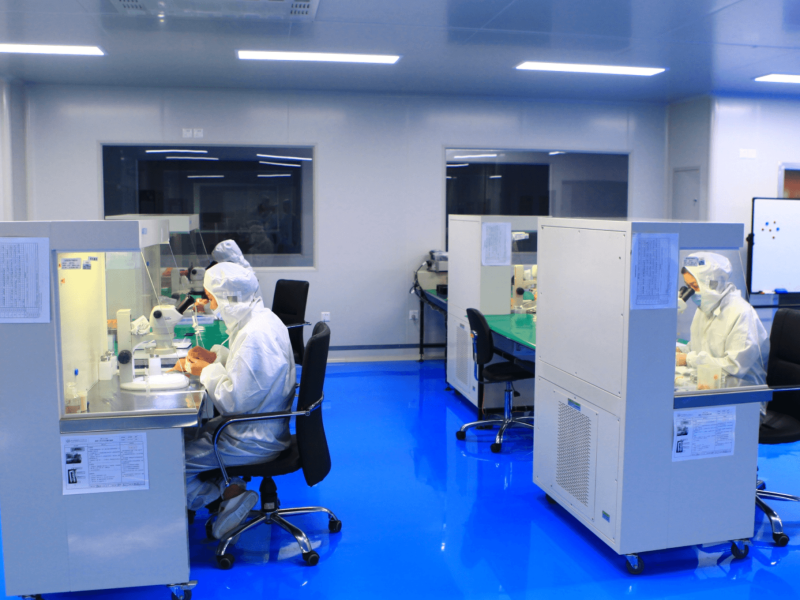
Why Choose Us
Comprehensive Solutions for All Your Navigation Needs
Commercial Grade Coverage
Bias Stability: >0.2°/h
Solution: MEMS based Gyroscope/IMU/INS
Applications: car navigation, unmanned aerial vehicles, transportation, robotics etc.
Tactical Grade Coverage
Bias Stability: 0.05°/h-0.2°/h
Solution: Fiber Optics and MEMS based Gyroscope/IMU/INS
Applications: armored vehicles operations, anti-aircraft artillery, precision targeting etc.
Navigation Grade Coverage
Bias Stability: ≤0.05°/h
Solution: Fiber Optics & Ring Laser Gyroscope/IMU/INS
Applications: medium and long-range guidance, military aviation, satellites
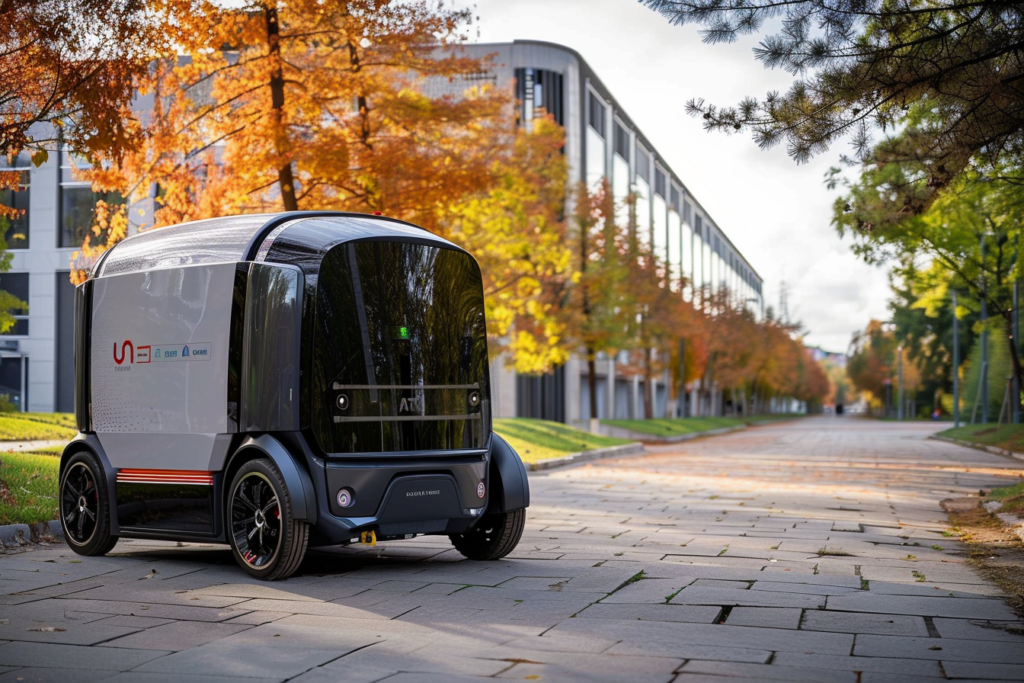
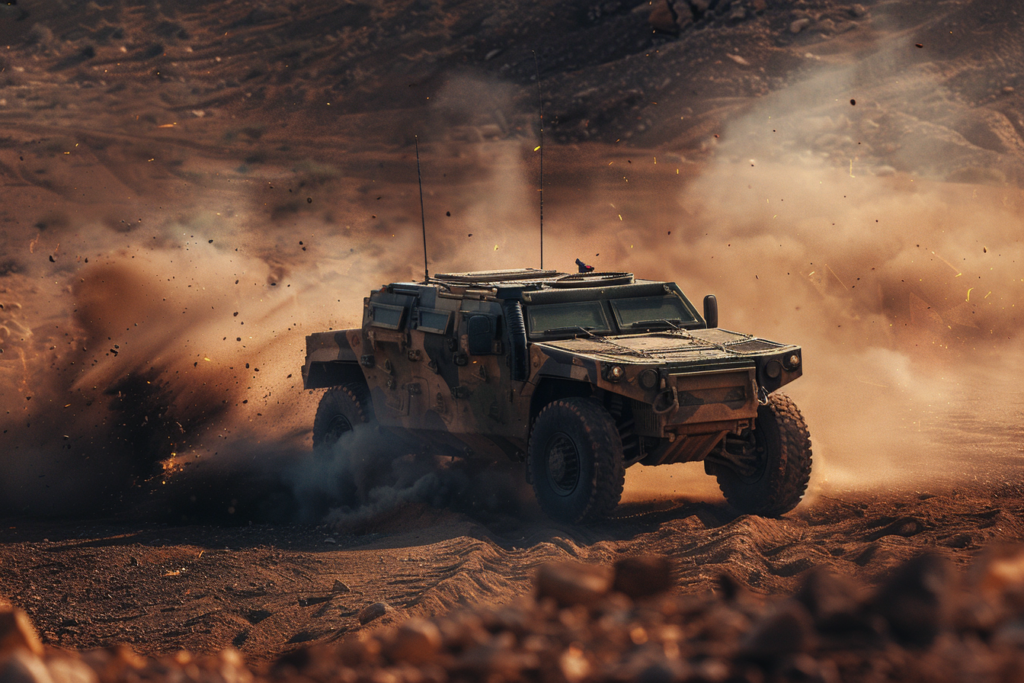
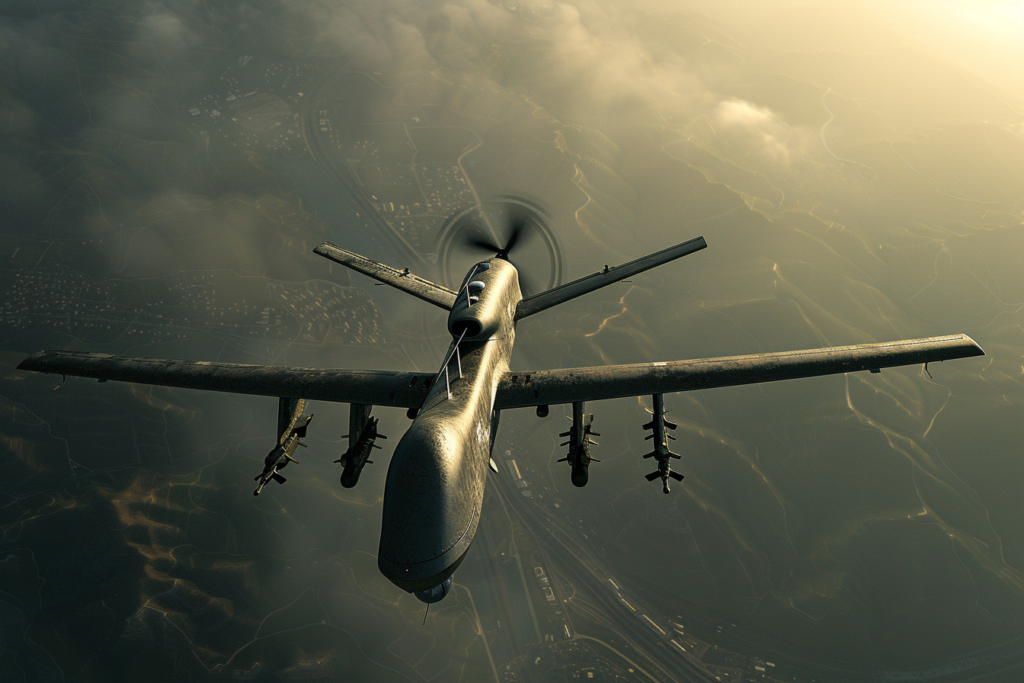
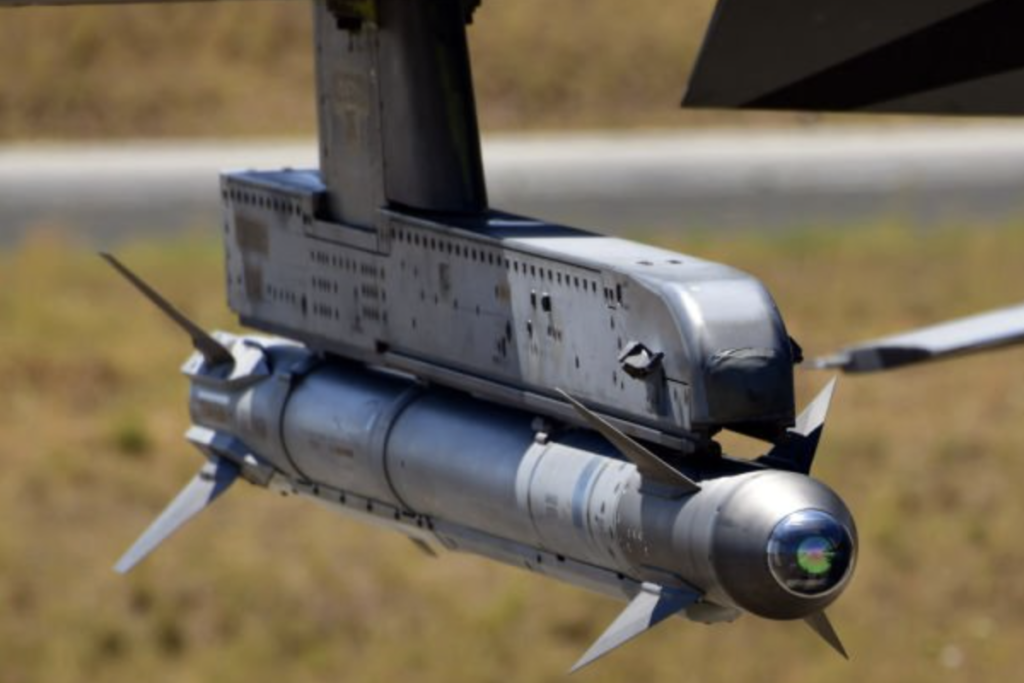
FAQS MEMS Accelerometer
Answers to Your Questions
A MEMS accelerometer is a type of sensor that uses Micro-Electro-Mechanical Systems (MEMS) technology to measure acceleration forces. These sensors detect changes in movement or vibration along one or more axes, offering real-time feedback in a compact and low-power format. MEMS accelerometers are commonly used in applications such as consumer electronics, automotive systems, robotics, and aerospace.
- Size & Weight: MEMS accelerometers are extremely small, allowing them to be integrated into compact devices.
- Low Power Consumption: These sensors are energy-efficient, ideal for battery-powered or portable applications.
- Cost-Effective: MEMS sensors are generally more affordable than traditional accelerometers, especially for large-scale production.
- Durability: MEMS accelerometers are more robust and less sensitive to external shock or environmental conditions compared to some traditional sensors.
- In-Run Bias Stability: Measures the consistency of the sensor’s output over time, which is crucial for high-precision applications.
- Measurement Range: Defines the maximum acceleration the sensor can measure without distortion. Match the range to your application's expected forces.
- Noise Density: Determines the amount of random error in the sensor output, affecting precision, especially for small or low-frequency movements.
Yes, GuideNav offers custom MEMS accelerometers tailored to meet specific needs, such as:
- Custom measurement ranges (e.g., ±2g, ±50g, ±100g, or other specialized ranges).
- Enhanced bias stability for applications requiring extremely precise measurements.
- Specialized packaging for environmental conditions like high shock resistance or extreme temperatures.
- Integration with existing systems
If you have unique requirements or need a customized solution, feel free to contact us to discuss your specifications.
Yes.
- For high-precision applications (e.g., navigation systems, IMUs), MEMS accelerometers from GuideNav can potentially replace the MS1000 series if the performance specifications (e.g., In-Run Bias Stability, noise density, and measurement range) align.
- If you are considering a replacement, we recommend discussing your exact needs to ensure the MEMS accelerometer meets or exceeds the required performance. We can also customize MEMS accelerometers to provide similar or better performance.
For applications requiring extremely high accuracy and long-term stability, high-end MEMS accelerometers can meet the demand, but each replacement case should be evaluated individually to ensure compatibility with your system.
MEMS accelerometers are widely used across many industries, including:
- Aerospace & Defense: For navigation, missile guidance, flight control systems, and unmanned vehicles.
- Automotive: For collision detection, airbag deployment, and driver assistance systems.
- Industrial Automation: For vibration monitoring, predictive maintenance, and motion sensing in machinery.
- Consumer Electronics: In smartphones, wearables, and gaming controllers to measure movement and orientation.
- Robotics: For motion control and stabilization in robotic arms and autonomous systems.
To learn more about GuideNav's MEMS accelerometers, or to discuss custom solutions for your specific application, simply submit your inquiry or contact our sales team at [email protected]. Our team is ready to assist you with technical specifications, pricing, and integration support.