Selecting the right Fiber Optic Gyroscope (FOG) is crucial for the success of any advanced navigation system, especially in industries like aerospace, defense, and industrial applications. However, this process can be overwhelming if you’re not familiar with the key technical specifications, performance metrics, and application requirements.
When selecting a Fiber Optic Gyroscope (FOG), focus on the specific performance requirements of your application, including bias stability, random walk, and environmental conditions. Prioritize long-term reliability and total cost of ownership, while considering customization options for unique needs. These factors will help ensure you choose a gyroscope that integrates seamlessly and delivers the highest performance.
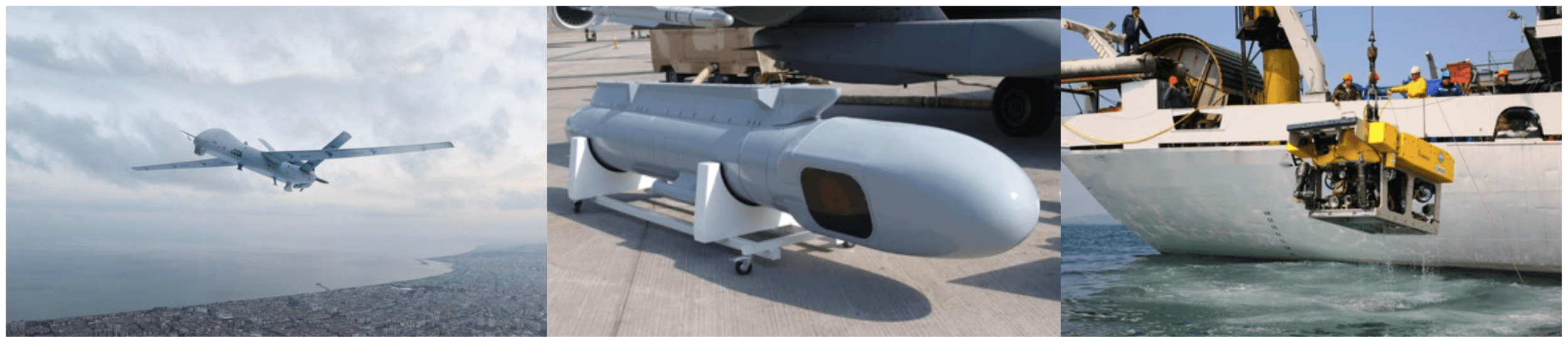
In this article I’ll walk you through how to select the right fiber optic gyros based on your specific requirements and the most important performance indicators.
Table of contents
What Are the Key Performance Specifications of a FOG?
When selecting a Fiber Optic Gyroscope (FOG), understanding the key performance specifications is crucial to ensure the device meets your system’s requirements. Based on my experience working with clients across various industries, the most important specifications to focus on are:
1. Bias Stability
Bias stability is one of the most critical parameters for a FOG, especially in applications that require long-term accuracy, such as aerospace and defense. Bias stability refers to the drift or offset in the gyroscope’s output over time. A low bias stability means less drift and more consistent measurements, which is vital in systems like navigation, where small errors can accumulate and lead to significant inaccuracies. For high-precision applications, we always recommend FOGs with ultra-low bias stability to ensure optimal performance.
2. Random Walk (Noise)
Random walk refers to the level of noise present in the gyroscope’s signal. This is important for systems that require precision over long durations. If your system requires continuous operation, such as in satellites or unmanned aerial vehicles (UAVs), the lower the random walk, the better. This metric essentially indicates how much error will accumulate due to noise in the measurement over time.
3. Scale Factor
The scale factor determines the gyroscope’s sensitivity to rotational movement. It defines how the output signal varies with changes in the input rotation. A high-scale factor is important if your application requires high precision in angular measurements. If you need very precise measurements for positioning or stabilization, such as in guided missiles or advanced robotics, I highly recommend a FOG with a stable and well-calibrated scale factor.
4. Bandwidth
Bandwidth is another key specification that affects how the gyroscope performs at different frequencies. For applications requiring real-time data processing, such as in autonomous vehicles or aerospace navigation systems, a wide bandwidth is essential. It ensures the gyroscope can capture rapid changes in motion and provide accurate feedback without lag. However, for more stable or less dynamic applications, you may not need the widest bandwidth available, which can reduce power consumption and cost.
5. Temperature Sensitivity
FOGs, like all precision instruments, are sensitive to temperature variations. Temperature sensitivity refers to how much the gyroscope’s performance changes with fluctuations in ambient temperature. This specification is crucial for high-performance applications in environments where temperature changes are common, such as in space exploration or military systems. The lower the temperature sensitivity, the more stable your FOG will be across different operating conditions. In my experience, aerospace and defense customers prioritize FOGs with excellent temperature compensation to ensure consistent performance in extreme conditions.
6. Power Consumption
If you’re working on a project where power efficiency is a priority—such as in mobile systems or battery-powered equipment—then power consumption becomes a vital specification. Low-power FOGs are designed to minimize energy usage while still providing high accuracy, which is ideal for UAVs or portable navigation systems. In these cases, I would advise selecting a FOG that balances power consumption with the necessary precision.
Precision Requirements for Fiber Optic Gyroscope by Applications
Selecting the right Fiber Optic Gyroscope (FOG) for your application depends heavily on the precision requirements specific to its intended use. For high-precision navigation systems, such as those in aerospace and maritime, gyroscopes with ultra-low bias stability and angular random walk are critical to ensure long-term stability. Conversely, tactical-grade systems balance performance with cost, while industrial applications prioritize robustness. For consumer electronics like smartphones, cost and integration ease often outweigh the need for extreme precision. By understanding these varying requirements, you can make an informed decision to match the gyroscope’s performance with your application’s needs.
Application | Typical Bias Stability (°/h) | Angular Random Walk (°/√h) | Key Priorities | Examples |
---|---|---|---|---|
High-Precision Navigation | ≤0.01 | ≤0.001 | Ultra-high accuracy, long-term stability | Aerospace, maritime navigation |
Tactical-Grade Systems | 0.1–1.0 | 0.01–0.1 | Balance between performance and cost | Defense systems, unmanned vehicles |
Industrial Applications | 1.0–10 | 0.1–1.0 | Robustness, cost-effectiveness | Robotics, platform stabilization |
Consumer Electronics | >10 | >1.0 | Affordability, integration ease | Smartphones, gaming devices |
Fiber Optic Gyroscope Selection Consideration: Size
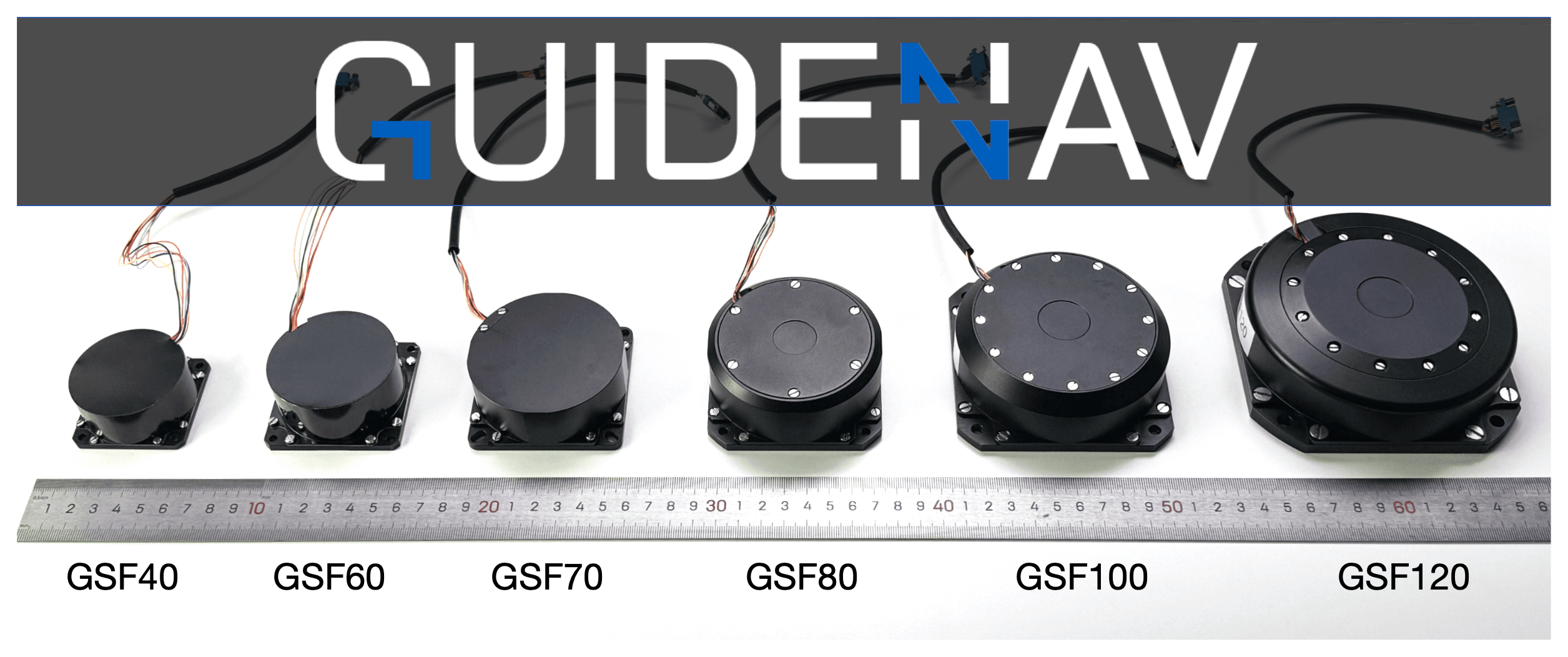
When selecting a Fiber Optic Gyroscope (FOG), size plays a crucial role, especially for applications requiring compact, lightweight, and easily integrable solutions. The size of the gyroscope directly impacts the system design and its overall performance, particularly in sectors like aerospace, defense, autonomous vehicles, and robotics, where space constraints are common.
- Application Requirements:
- Aerospace: For spacecraft or satellites, space is extremely limited. In these applications, FOGs must be small and compact yet offer high-precision navigation capabilities. The need for small-sized, high-performance gyroscopes is a critical factor in space exploration.
- Autonomous Vehicles & Robotics: These systems often require highly integrated FOGs that fit into small spaces, such as in the chassis of autonomous vehicles or within robotic arms. Compact size and lightweight design are essential for these use cases, allowing easy integration without compromising system stability.
- Military and Defense: In defense applications, FOGs must not only offer high precision but also be compact to fit within the limited space available on platforms like fighter jets, missiles, and drones. The size of the gyroscope directly impacts the design and functionality of the entire defense system.
- Weight & Integration: Apart from size, weight is another critical factor. While larger FOGs may offer better stability and a broader range of functions, they can be impractical in mobile devices or smaller systems. A smaller and lighter FOG is often chosen for applications where weight is a significant concern.
- Miniaturization & Technical Challenges: With advancements in technology, the miniaturization of FOGs has become increasingly feasible. However, this presents challenges in maintaining accuracy, power consumption, and durability. Manufacturers must ensure that smaller FOGs continue to deliver high precision without sacrificing performance or reliability.
- Design & Installation Space: The FOG’s size must be compatible with the overall system design. For instance, in compact devices like optical pods, the gyroscope must fit seamlessly with other sensors and components. A large FOG could make installation difficult, while a very small one might not meet the necessary precision requirements.
As an example, GUIDENAV’s GTF40 three-axis Fiber Optic Gyroscope is a representative of miniaturized high-precision FOGs. It has become the go-to solution for a large customer base requiring compact yet highly accurate gyroscopes, particularly for optical pod applications.
Fiber Optic Gyroscope Selection Consideration: Housing
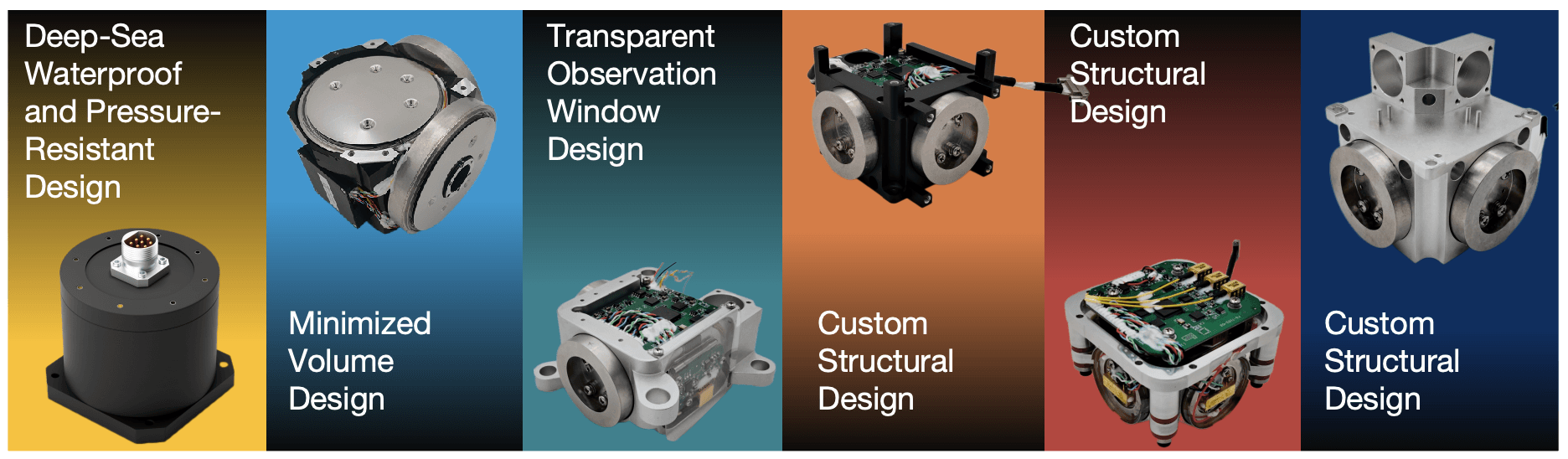
When selecting a Fiber Optic Gyroscope (FOG), the housing is a critical factor that cannot be overlooked. The housing not only provides physical protection for the gyroscope but also significantly influences its ability to perform in specific environmental conditions. The housing material and design vary greatly depending on the application and the environment in which the FOG will operate.
- Standard Housing vs. Specialized Housing:
- Standard Housing: For many general applications, such as industrial platforms, automation systems, or routine commercial uses, FOGs typically come with standard housings made from materials like aluminum alloys or plastics. These housings provide basic protection against dust, moisture, and mild vibrations.
- Specialized Housing: In certain specialized environments, FOGs may require custom housing materials. These applications could include extreme temperatures, high vibration, corrosive environments, or high-pressure scenarios.
- Deep Sea Applications: For example, in ROVs (Remotely Operated Vehicles) used for deep-sea exploration, FOGs need to withstand pressures at depths of over 3,000 meters. The housing material must be highly resistant to pressure and corrosion, with titanium alloys being a common choice. Titanium alloys not only offer high resistance to extreme water pressure but are also lightweight and corrosion-resistant, making them ideal for deep-sea environments where high-precision instruments are crucial.
- High-Temperature and Low-Temperature Environments: FOGs used in environments with extreme temperatures, such as aerospace, high-temperature industrial processes, or polar exploration, require special housings. Materials like stainless steel or titanium alloys are often used for high-temperature applications, as they can withstand the severe conditions of space or high-altitude flights. For low-temperature environments, such as polar research, the housing must provide excellent insulation and be able to operate in sub-zero temperatures.
- Corrosive and Waterproof Applications: In chemically corrosive environments (such as oil drilling rigs, chemical plants, etc.), the housing must be made of corrosion-resistant materials like stainless steel or specially coated plastic housings. Waterproofing is also a key consideration, especially for underwater equipment or devices operating in high-humidity environments. A sealed housing ensures that no moisture or water vapor penetrates and interferes with the gyroscope’s performance.
- Electromagnetic Shielding: For applications sensitive to electromagnetic interference (EMI), such as military, communications, or high-precision measurement systems, the housing may require some form of electromagnetic shielding. Using conductive materials or incorporating electromagnetic shielding layers within the housing can significantly reduce electromagnetic interference, ensuring stable and reliable performance of the FOG.
- Impact of Housing Design: The housing design also impacts the weight, size, and heat dissipation of the FOG. In high-power applications, housing designs must account for adequate heat management to prevent the device from overheating, which could lead to performance degradation or damage. Therefore, the housing material should also provide good thermal conductivity to dissipate heat efficiently.
GuideNav’s Custom Housing Experience
GuideNav has extensive experience in customizing housings to meet specific customer needs. Over the years, we have tailored FOG housings using various materials and shapes to suit a broad range of industries and applications. Whether it’s designing ultra-durable titanium housings for deep-sea exploration, heat-resistant housings for aerospace, or lightweight and compact designs for robotics, GuideNav works closely with clients to ensure the housing material and design are perfectly aligned with the operational environment. This level of customization ensures that our FOGs not only perform at their best but also endure the harshest conditions.
References
The scale factor determines the gyroscope’s sensitivity to rotational movement[^1].
[^1]: Exploring the impact of rotational movement on gyroscopes can enhance accuracy in motion tracking and stabilization technologies.
Bandwidth is another key specification that affects how the gyroscope performs at different frequencies[^2].
[^2]: Understanding gyroscope performance across frequencies can optimize its application in various technologies, enhancing precision and reliability.