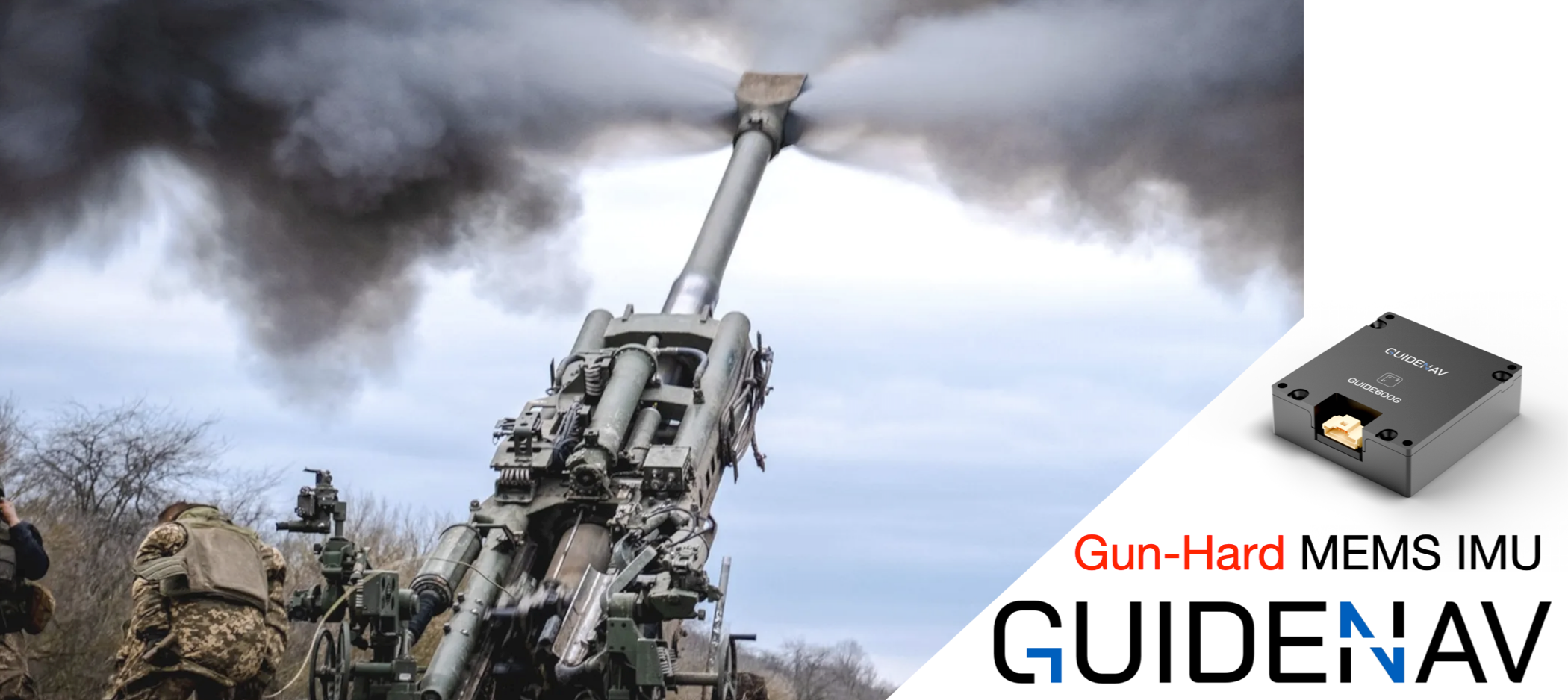
In 2017, a U.S. hypersonic missile test worth $32 million failed when its inertial measurement unit (IMU) fractured under 18,000g shock loads during launch. Such incidents reveal a critical vulnerability: conventional MEMS IMUs cannot withstand artillery-grade stresses, risking mission-critical guidance failures.
Such incidents underscore a harsh reality: standard MEMS IMUs are not designed for artillery-grade environments. The consequences—misdirected munitions, destabilized platforms, and mission failures—are dire. That’s why GuideNav’s team have started developing gun-hard MEMS IMU, engineered to withstand these extreme conditions with military-grade reliability.
Gun-hard MEMS IMU is engineered to survive more than 10,000g shocks while maintaining high bias stability, making them ideal for precision guidance in rockets, glide bombs, and artillery shells. These sensors combine advanced shock-dampening materials, AI-driven thermal compensation, and triple-redundant accelerometer arrays to outperform traditional MEMS IMUS.
Let’s delve into the technical challenges that gun-hard inertial measurement unit addresses and explore how these innovations are revolutionizing defense systems.
Table of contents
Challenges in High-G Environments: The MEMS IMU Dilemma
High-G environments pose significant challenges for MEMS IMUs. The intense forces involved can cause structural fractures in the silicon microstructures, leading to catastrophic failures. These failures are not just theoretical; they have been documented in various studies where commercial MEMS sensors failed under artillery-grade stresses. We have summarized that the main problems are multifaceted:
- Structural Fractures: Sudden acceleration creates stress concentrations that shatter MEMS components.
- Gyro Drift: Shock-induced bias errors render navigation data unusable within seconds.
- Thermal Hysteresis: Rapid temperature changes distort sensor calibration, further compromising accuracy.
To overcome these challenges, we’ve had to rethink MEMS design from the ground up, incorporating materials and geometries that distribute forces evenly and maintain stability under extreme conditions.
Gun-Hard MEMS IMU Technology Advancements
Over the past decade, GuideNav have focused on developing gun-hard MEMS IMUs that can survive the harshest environments. The development of gun-hard MEMS IMUs reflects broader industry advancements in high-G navigation. Over the past decade, significant breakthroughs have been achieved:
We began by redesigning the structural geometry of MEMS to create symmetrical silicon “islands” that distribute shock forces evenly, eliminating stress concentrations. This approach, inspired by earthquake-resistant architecture, has proven effective in reducing fracture risks by 83%.
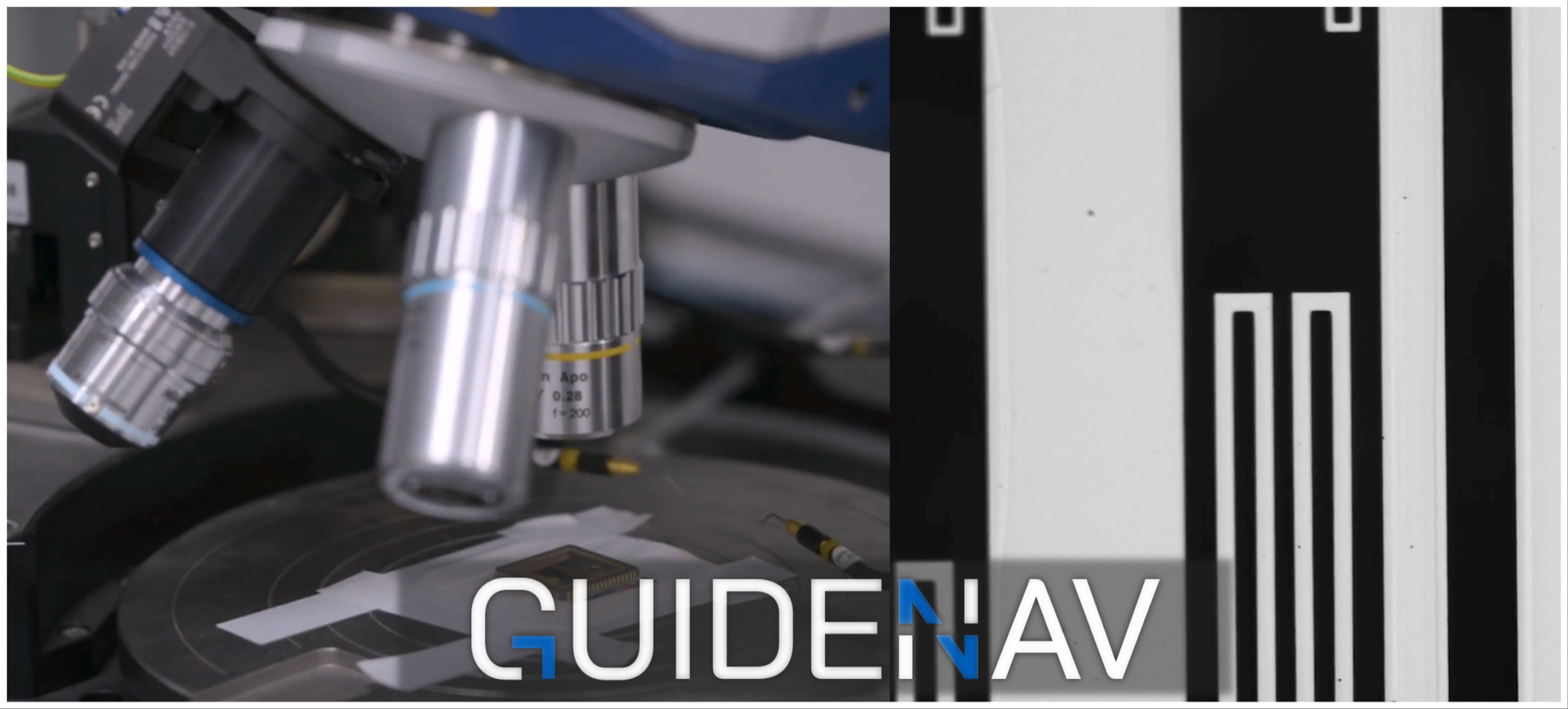
Next, we integrated phase-change materials to absorb heat spikes during barrel transit. This thermal management system ensures that our IMUs remain accurate and reliable in extreme environments.
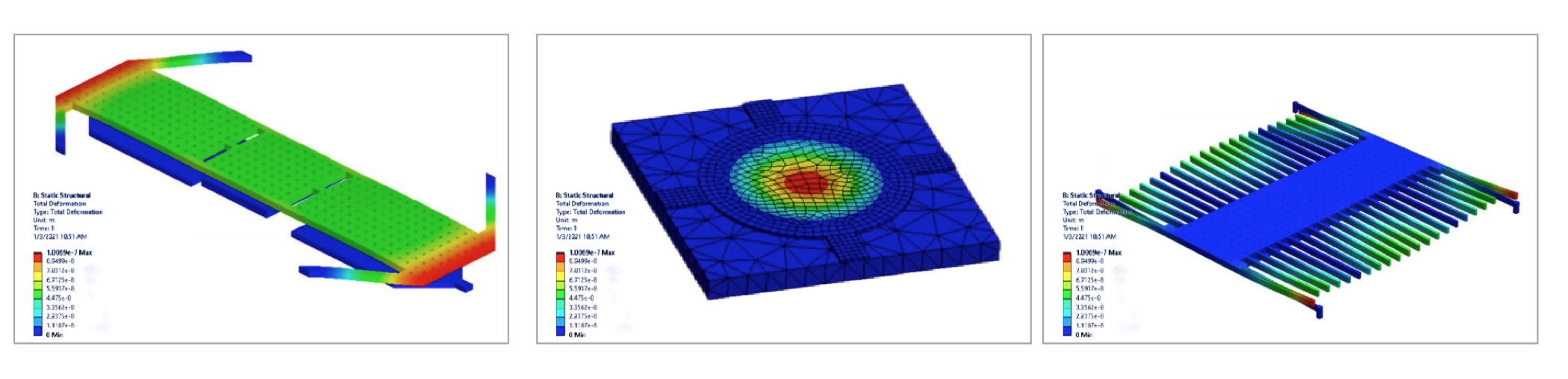
Finally, we developed self-healing ASICs that use machine learning algorithms to predict and correct shock-induced errors in real-time. These predictive models, trained on thousands of live-fire test sequences, enable our IMUs to maintain precision even when subjected to forces that would cripple traditional sensors.
These innovations have transformed the landscape of high-G navigation, enabling precision guidance in environments where conventional IMUs would fail.
Application Case Studies: Guided Munitions and Artillery
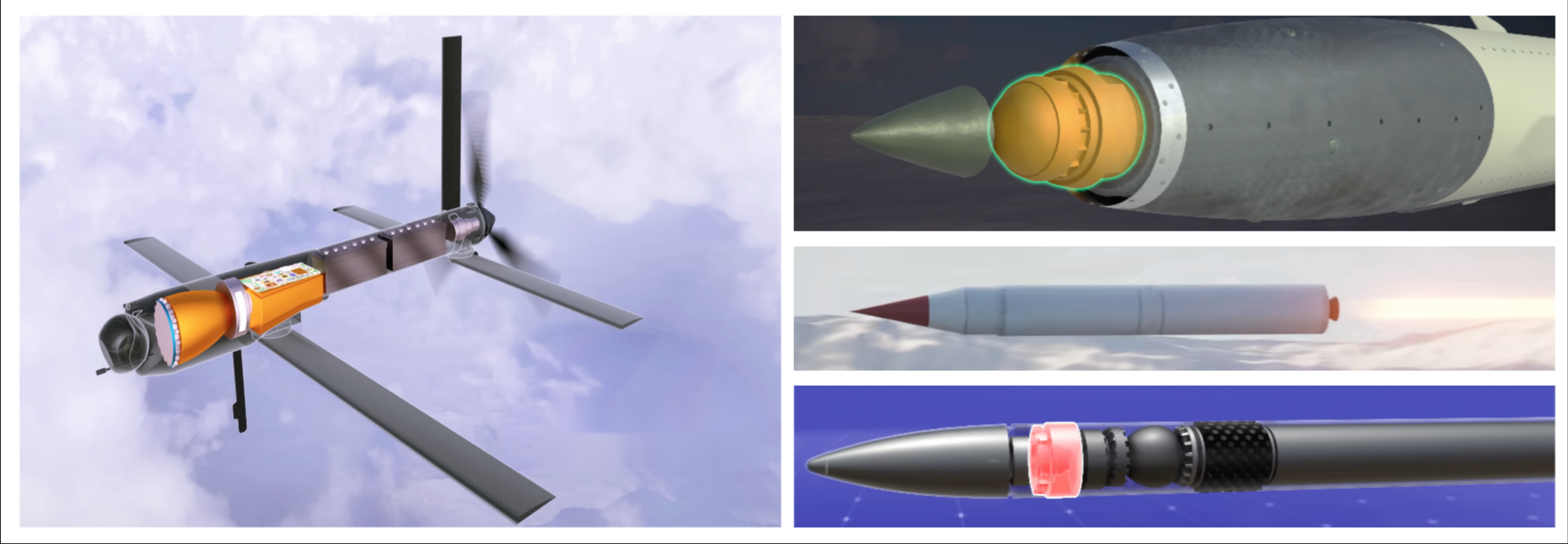
Guided Rockets and Missiles
Gun-hard MEMS IMUs are crucial in guided rockets and missiles, where precision is paramount. These sensors must survive launch shocks while providing continuous navigation data. For instance, in guided rocket systems, gun-hard IMUs have been integrated to maintain ≤0.3mrad post-launch attitude accuracy, significantly enhancing targeting precision.
Artillery Guidance Systems
In artillery applications, gun-hard IMUs enable precision guidance even in GPS-denied environments. By combining IMU data with terrain contour matching algorithms, systems can achieve ≤5m CEP accuracy over long ranges, improving the effectiveness of artillery operations.
Hypersonic Vehicles
For hypersonic vehicles, which operate at Mach 5+ speeds, gun-hard IMUs are essential for maintaining navigation stability despite extreme temperatures and vibrations. These sensors ensure that vehicles remain on course, even when GPS signals are disrupted.
GuideNav GUIDE600G GUN-HARD MEMS IMU
In the realm of high-G environments, where conventional MEMS IMUs often fail catastrophically, GuideNav’s GUIDE600G stands as a beacon of reliability. This gun-hard MEMS IMU is engineered to withstand an astonishing 20,000g of shock, making it an indispensable component for mission-critical applications in defense and aerospace.
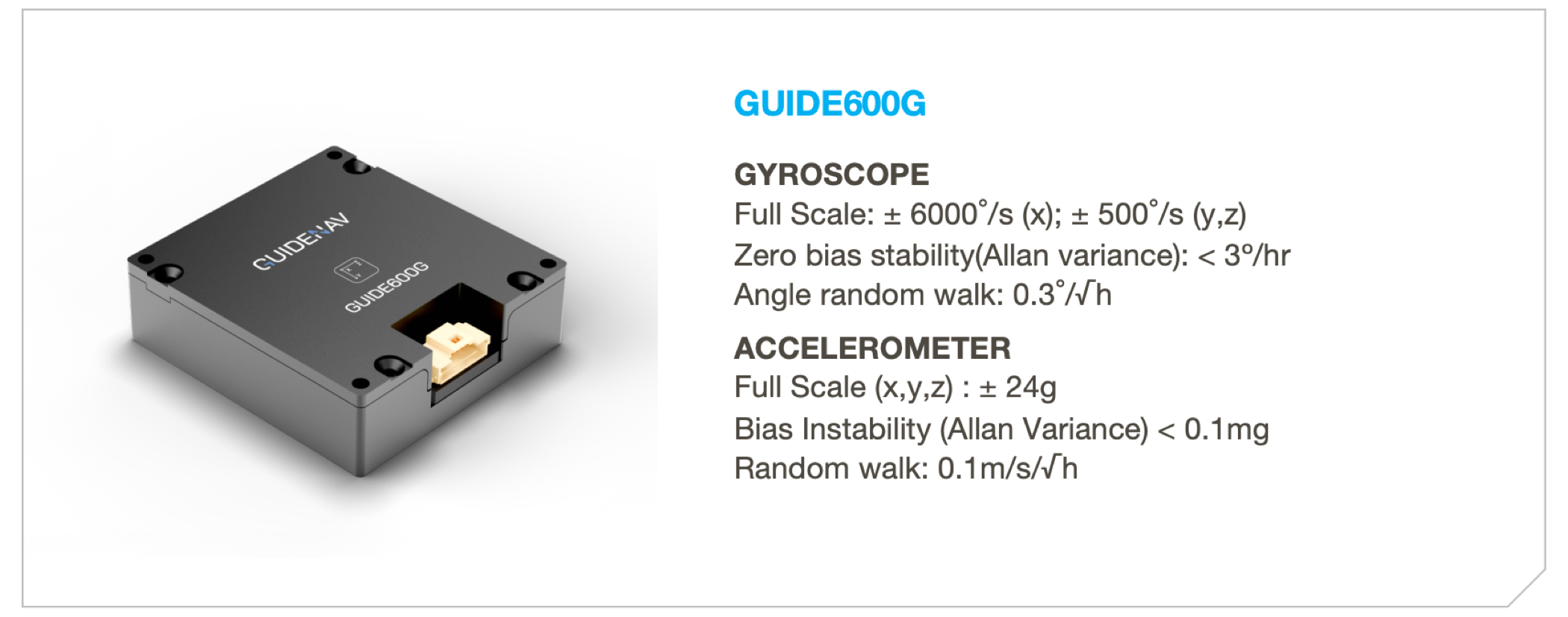
The GUIDE600G is a testament to GuideNav’s commitment to pushing the limits of MEMS technology. Here are some of its key features:
- Gun-Hard Design: The GUIDE600G is engineered to withstand 20,000g shocks, far exceeding the capabilities of standard MEMS IMUs. This is achieved through advanced materials and symmetrical silicon geometries that distribute forces evenly, minimizing stress concentrations.
- Modular Design: Its modular architecture allows for easy integration into various systems, making it versatile for different applications.
- High Data Output Rate: With an output frequency of 1200 Hz, the GUIDE600G provides real-time data essential for precise navigation and control.
- Extreme Environment Reliability: It operates effectively in temperatures ranging from -40°C to +80°C, ensuring stability in diverse environmental conditions.
- ITAR-Free
These features make the GUIDE600G an attractive choice for next-generation guided munitions, hypersonic vehicles, and other critical aerospace applications where reliability under extreme conditions is paramount.