The flight control system (FCS) of an aircraft is a sophisticated piece of technology designed to ensure stability and precision during flight. It relies on a wide variety of sensors to gather real-time data about the aircraft’s speed, altitude, orientation, and environmental conditions. So how many sensors does a flight control system have?
A flight control system typically includes 20 to 100 sensors including inertial sensors, position sensors, pressure sensors and other critical sensors with each sensor fulfilling a specific function to ensure the stability, performance, and safety of the aircraft.
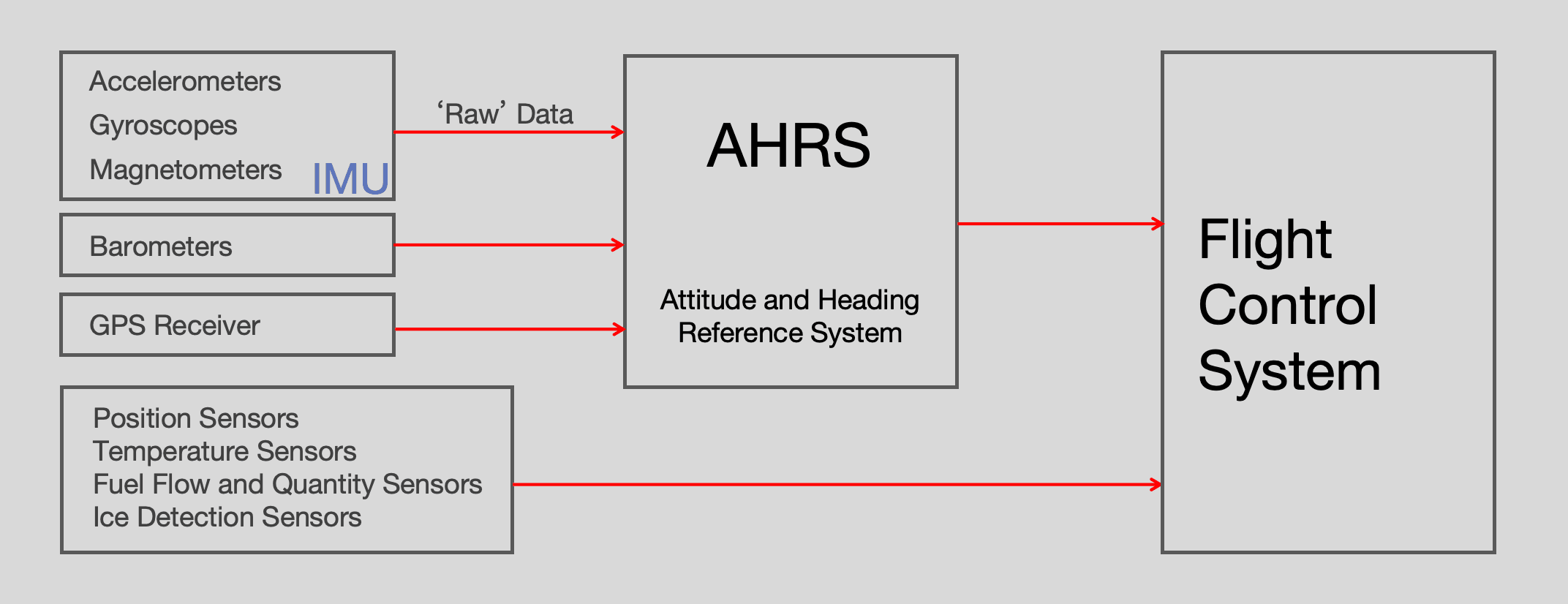
In this article, we’ll explore the types of sensors involved in a flight control system, their functions, and why the number of sensors varies by system design.
Table of contents
What Sensors Are Found in a Flight Control System?
Let’s take a deeper dive into the various sensor categories found in a flight control system.
Key Applications of Fiber Optic Gyroscope
1. Inertial Sensors (Inertial Measurement Unit)
Inertial sensors, such as accelerometers, gyroscopes, and magnetometers, are essential components in any Inertial Measurement Unit (IMU). These sensors measure the aircraft’s movement, rotation, and orientation. They provide the foundation for calculating attitude, position, and velocity.
- Accelerometers: Measure linear acceleration along different axes (X, Y, Z) to determine the aircraft’s speed and direction of motion.
- Gyroscopes: Measure angular velocity and help determine the aircraft’s orientation (pitch, roll, and yaw).
- Magnetometers: Measure the strength and direction of the magnetic field, which is crucial for heading determination and used alongside gyroscopes to stabilize the system.
Inertial sensors are responsible for providing precise orientation and movement data, especially when GPS or external signals are unavailable, such as during autonomous operations or fly-by-wire systems.
2. Position Sensors
Position sensors track the location of various components within the aircraft, ensuring the proper alignment and movement of control surfaces and other systems. These sensors are integral to the operation of the flight management system (FMS) and autopilot systems.
- Pitot Tubes: Measure the dynamic pressure to calculate airspeed and determine the velocity of the aircraft.
- Angle of Attack (AoA) Sensors: Measure the angle between the aircraft’s longitudinal axis and the airflow direction. These sensors are crucial for detecting stall conditions and optimizing aerodynamic performance
- GPS Sensors: Provide precise positioning data, particularly during autonomous or navigation phases. GPS data is essential for long-range navigation and aiding inertial navigation systems (INS).
Position sensors give the aircraft the ability to track its trajectory, adjust its flight path, and make real-time corrections to flight surfaces based on the flight plan.
3. Pressure Sensors
Pressure sensors are used extensively in the air data system to monitor and regulate parameters like altitude, airspeed, and climbs/descent rates. These sensors are vital for maintaining flight stability and safety.
- Barometric Pressure Sensors: Measure the atmospheric pressure at the aircraft’s location, which is used to calculate altitude and vertical speed.
- Pitot-Static Pressure System: Combines both static and dynamic pressures to calculate airspeed and altitude
Pressure sensors are integral to the air data computer, which processes the inputs from pitot tubes, angle of attack probes, and other systems to display crucial flight data for the pilot and automation systems.
4. Other Critical Sensors
In addition to inertial, position, and pressure sensors, modern flight control systems rely on a variety of additional sensors for overall aircraft performance:
- Temperature Sensors: Monitor the temperature inside the cabin and the external temperature, which can affect engine performance, fuel management, and de-icing systems
- Fuel Flow and Quantity Sensors: Measure the fuel consumption rate and the amount of fuel in the tank, helping to optimize fuel management
- Engine Monitoring Sensors: These sensors track engine parameters such as fuel flow, temperature, and pressure to ensure efficient and safe operation
- Ice Detection Sensors: Monitor the presence of ice on critical aircraft surfaces like wings and tail. Ice buildup can disrupt airflow and reduce lift, so these sensors trigger de-icing systems when necessary.
Why Do Flight Control Systems Need So Many Sensors?
Each sensor plays a unique role in maintaining flight stability and safety.
The number of sensors is driven by the need to measure various parameters of the aircraft’s state in real-time. The redundancy of sensors also improves safety by ensuring that if one sensor fails, others can take over the measurement task. This is particularly critical in military applications or commercial airliners, where safety is the highest priority.
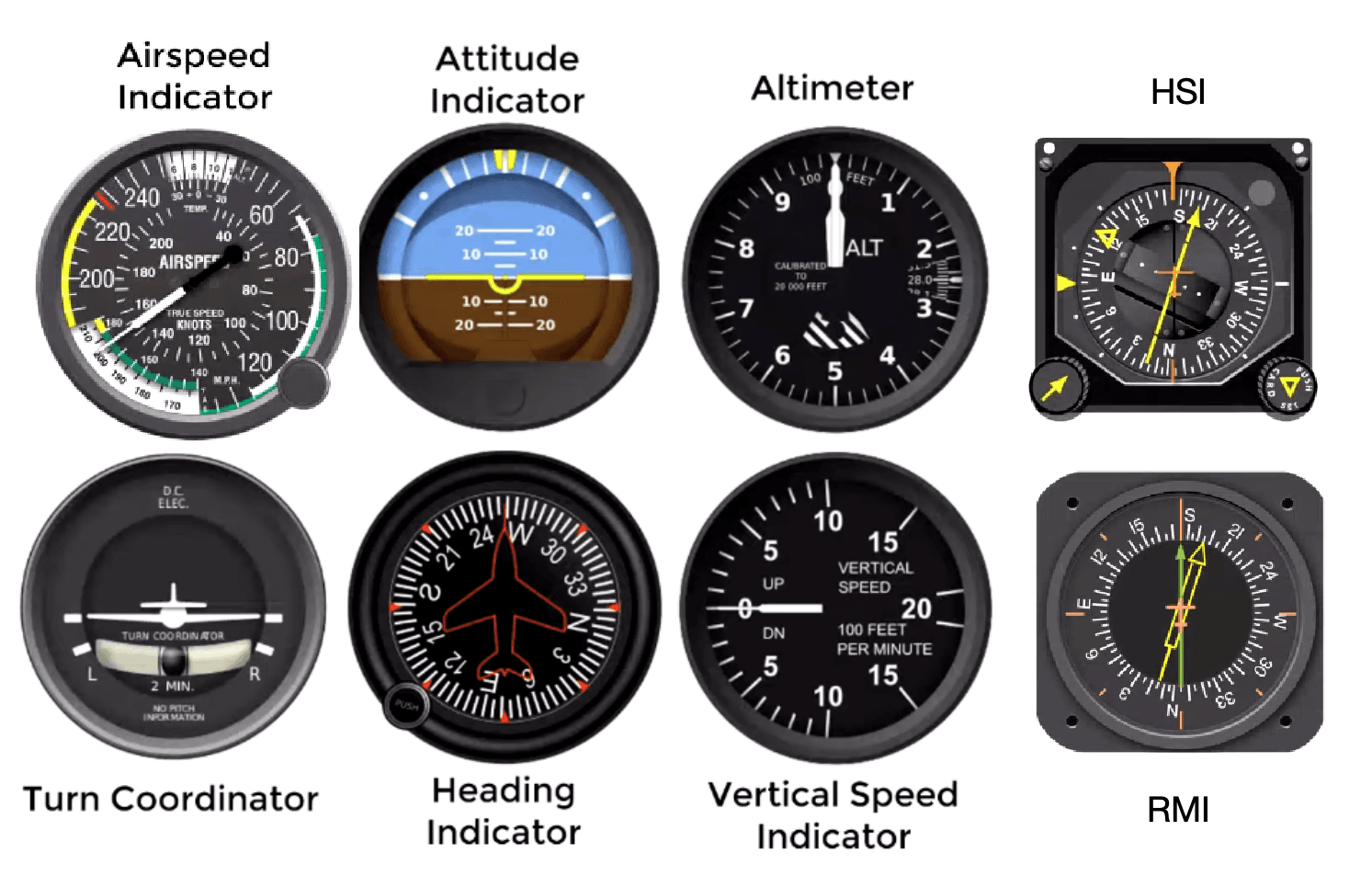
Advanced Flight Control Systems: Sensor Fusion
In more advanced flight control systems, sensor fusion technologies combine data from multiple sensors to provide even more accurate and reliable flight control information. For instance, the data from accelerometers, gyroscopes, and GPS can be merged using algorithms that remove noise and inconsistencies. This process creates a more robust Inertial Navigation System (INS), which is crucial for autonomous flight and high-precision operations.
Modern aircraft, especially autonomous drones and military fighter jets, rely heavily on this sensor fusion to create a more efficient and responsive flight control system.
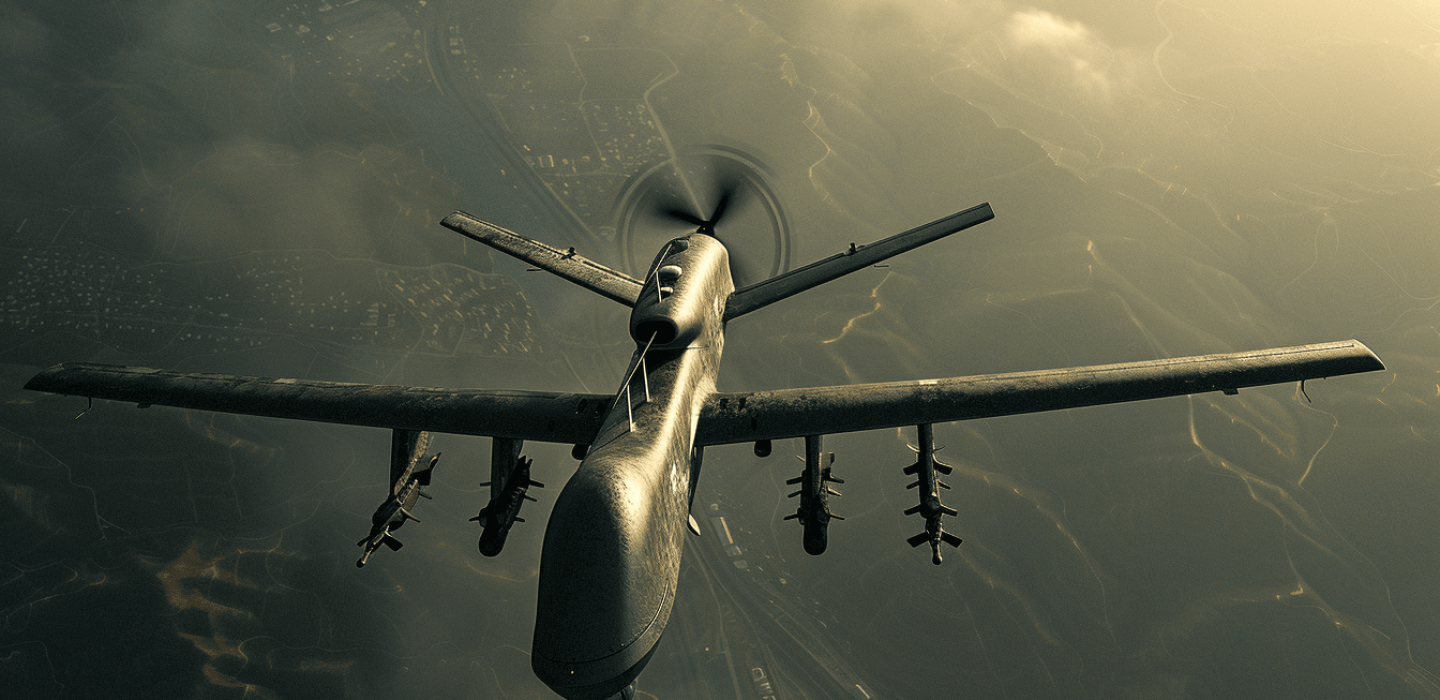
Recommended IMUs for Flight Control Systems: GUIDE688B vs. GUIDE900
When selecting an Inertial Measurement Unit (IMU) for a flight control system, it’s crucial to choose a sensor that meets your system’s performance and precision needs. Two highly effective options from GuideNav are the GUIDE688B and GUIDE900. Both are MEMS-based IMUs, but they cater to different types of flight control systems and applications. Let’s explore these two models and determine which one suits your needs.
GUIDE688B: A Reliable Choice for Medium Precision Applications
The GUIDE688B is a ten-axis MEMS IMU, featuring three-axis gyroscopes, three-axis accelerometers, three-axis magnetometers, and a barometric pressure sensor. This combination makes it ideal for UAVs and small aircraft that need moderate precision in their flight control systems.
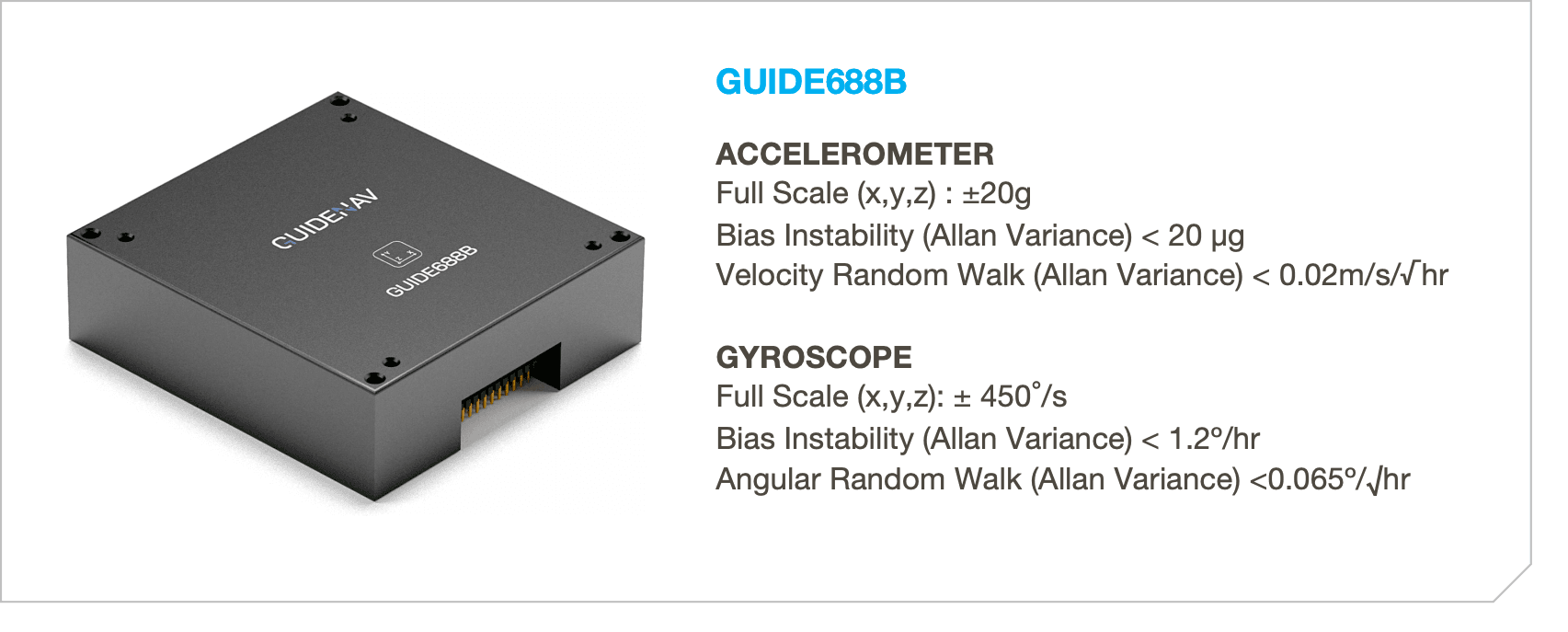
Key Features:
- Ten-Axis Sensor Configuration: Includes essential sensors for precise motion tracking.
- Compact and Cost-Effective: Ideal for smaller systems with medium precision requirements.
- High Performance for Budget-Conscious Systems: Delivers excellent performance for its cost, particularly in commercial-grade UAVs.
Best Applications: The GUIDE688B is best suited for UAVs, drones, and small aircraft with medium precision needs. It’s a cost-effective solution without compromising on performance for real-time flight control.
GUIDE900: High-Precision IMU for Critical Flight Control Systems
The GUIDE900 is a six-axis MEMS IMU known for its superior precision and low drift performance. It delivers accuracy comparable to low-end fiber optic gyroscopes (FOG), making it ideal for high-performance flight control systems such as military aircraft, advanced UAVs, and aerospace applications.
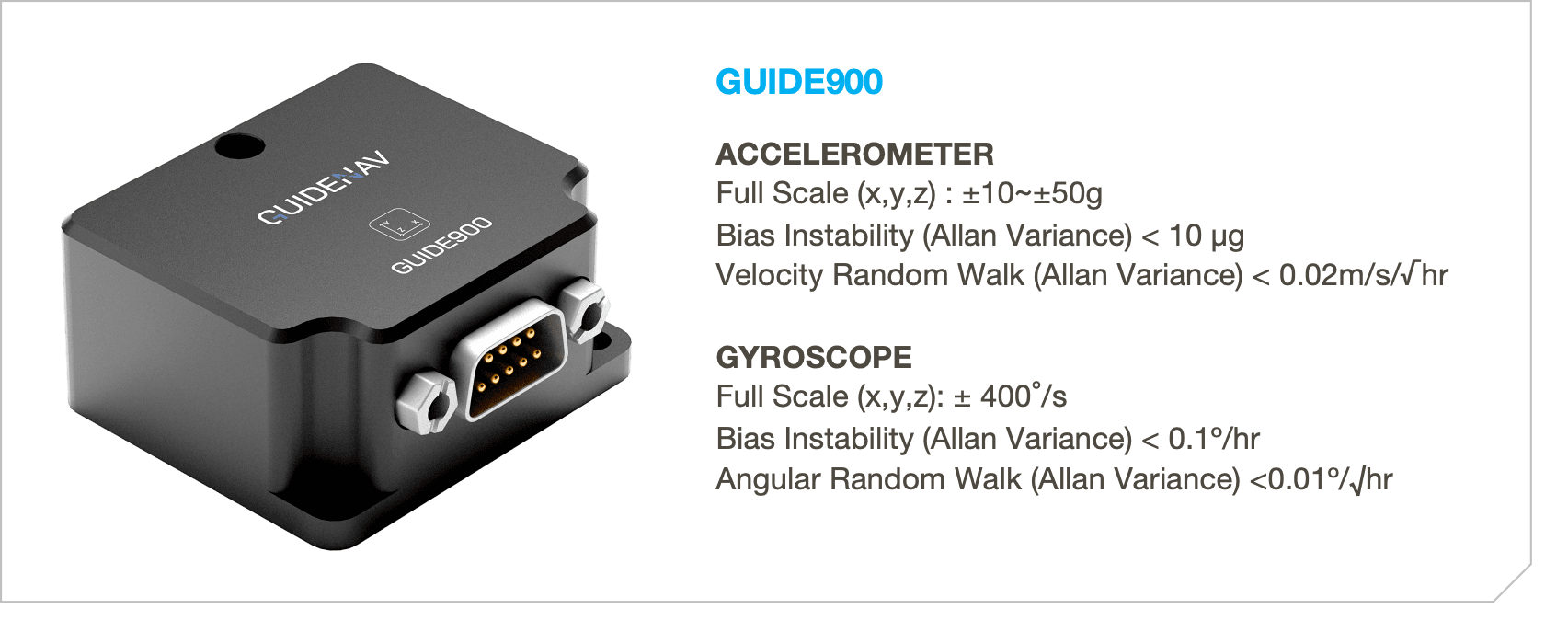
Key Features:
- Six-Axis Sensor Configuration: Provides high-precision motion tracking with low drift.
- FOG-like Performance: Despite being MEMS-based, it offers performance similar to fiber optic gyroscopes.
- STIM300 Compatibility: Compatible with industry-standard protocols, making it easy to integrate into high-precision flight systems.
Best Applications: The GUIDE900 excels in military, aerospace, and high-end UAVs requiring superior accuracy and long-term stability. It’s the go-to choice for high-precision flight control systems in demanding environments.
Key Features:
- Six-Axis Sensor Configuration: Provides high-precision motion tracking with low drift.
- FOG-like Performance: Despite being MEMS-based, it offers performance similar to fiber optic gyroscopes.
- STIM300 Compatibility: Compatible with industry-standard protocols, making it easy to integrate into high-precision flight systems.
Best Applications: The GUIDE900 excels in military, aerospace, and high-end UAVs requiring superior accuracy and long-term stability. It’s the go-to choice for high-precision flight control systems in demanding environments.
References
The flight control system[^1] (FCS) of an aircraft is a sophisticated piece of technology designed to ensure stability and precision during flight.
[^1]: Understanding the flight control system’s role can enhance your knowledge of aircraft safety and performance, crucial for aviation enthusiasts and professionals.
Pressure sensors are used extensively in the air data system[^2] to monitor and regulate parameters like altitude, airspeed, and climbs/descent rates. These sensors are vital for maintaining flight stability and safety.
[^2]: Learn how air data systems contribute to safer flights by monitoring critical flight parameters.