In the fast-evolving world of robotics, persistent issues like AGV(Automated Guided Vehicles) drift or unstable robotic arms are rarely caused by flawed software. Instead, they often trace back to inadequate gyroscope performance. Low-grade IMUs introduce drift, latency, and feedback errors—undermining control loops. The solution lies in deploying precision-grade MEMS gyroscopes engineered for real-time stability, responsiveness, and integration into dynamic robotic systems.
MEMS gyroscopes form the inertial core of advanced robotics—delivering precise angular rate sensing, real-time orientation tracking, and reliable motion feedback in compact, power-efficient packages. They are indispensable in enabling stable navigation and dexterous movement for both AGVs and humanoid robotic arms.
Over the past decade, I’ve worked on dozens of robotic deployments—from early IMU evaluation to full-stack integration—and one truth stands out: inertial sensing quality defines whether a robot merely functions or truly performs.
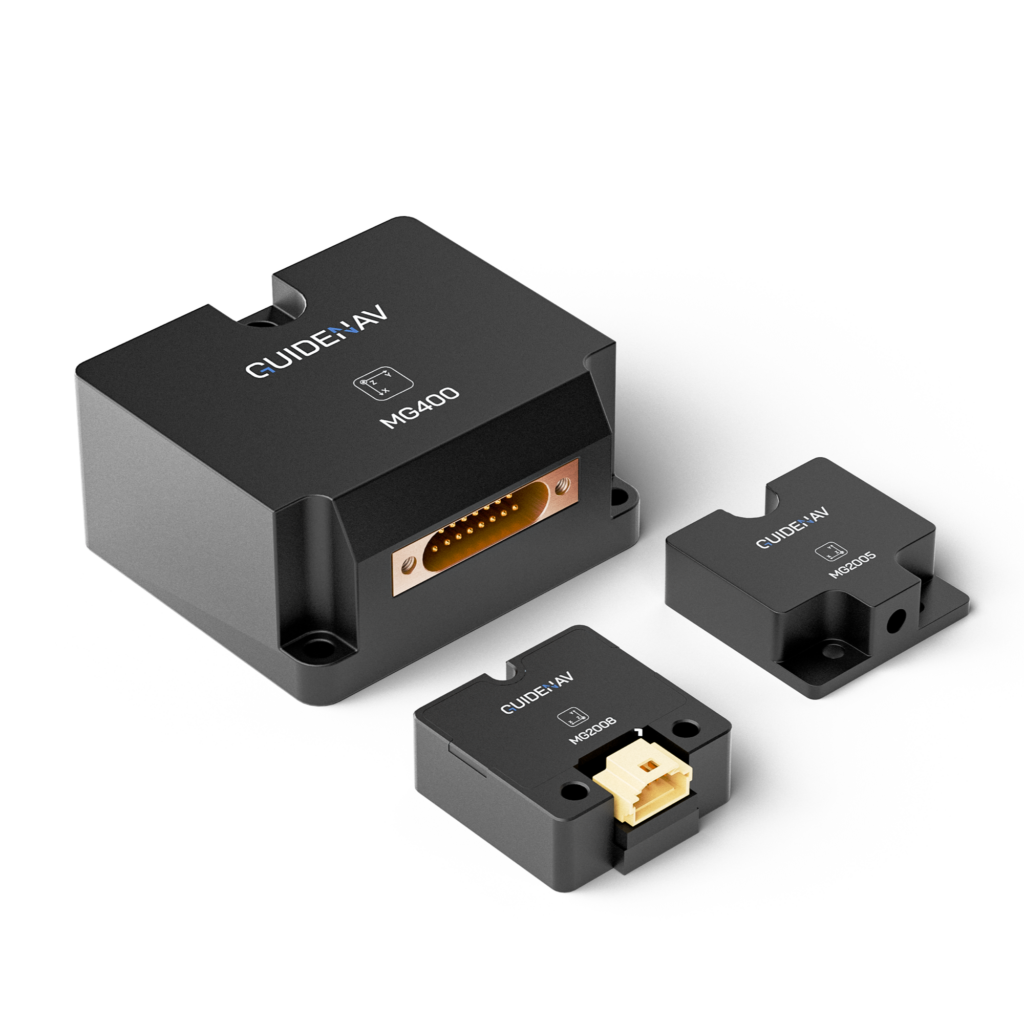
Table of contents
The Industrial Impact of AGVs and Humanoid Robots
AGVs and humanoid robotic arms are no longer futuristic concepts—they’re fast becoming core assets in warehouses, factories, and even hospitals. The AGV market is projected to grow from $4.5B in 2023 to $12B by 2028, while humanoid robotics is expected to jump from $1.6B to $8.9B, reflecting a CAGR of 22% and 41% respectively.
Powering this growth behind the scenes are MEMS gyroscopes—essential sensors that provide real-time orientation and angular velocity data. Without them, AGVs lose heading precision, and humanoid arms struggle with balance and responsiveness.
Segment | 2023 Market Size | 2028 Forecast | CAGR (2023–2028) |
---|---|---|---|
Warehouse AGVs | $4.5B | $12.0B | 22% |
Humanoid Robotic Arms | $1.6B | $8.9B | 41% |
At GuideNav, our MEMS gyroscopes are built to meet the demands of this new generation of robotics—combining high bias stability, low latency, and compact form factors ideal for integration into mobile platforms and articulated limbs. From autonomous fleets to dexterous manipulators, we provide the inertial core that keeps robots balanced, accurate, and in control.
How Do MEMS Gyroscopes Actually Work?
MEMS gyroscopes sense angular velocity through the Coriolis effect. Inside each sensor, microscopic structures vibrate along a fixed axis. When rotation occurs, Coriolis force causes a detectable shift in these vibrations, which is then translated into angular rate data.
Thanks to CMOS-compatible fabrication, these structures fit into a tiny chip that is power-efficient, shock-resistant, and ideal for embedded robotics.
But making MEMS gyros viable for real-world robotics takes more than miniaturization. Key advances include:
- Low-noise ASICsfor clean, high-frequency signal output
- Built-in thermal calibrationto stabilize performance over temperature
- Mechanical dampingto withstand vibration and shock
That’s why in real-world robotics—where vibrations, sudden turns, and thermal shifts are the norm—our MEMS gyroscopes stay reliable, responsive, and ready to deploy.
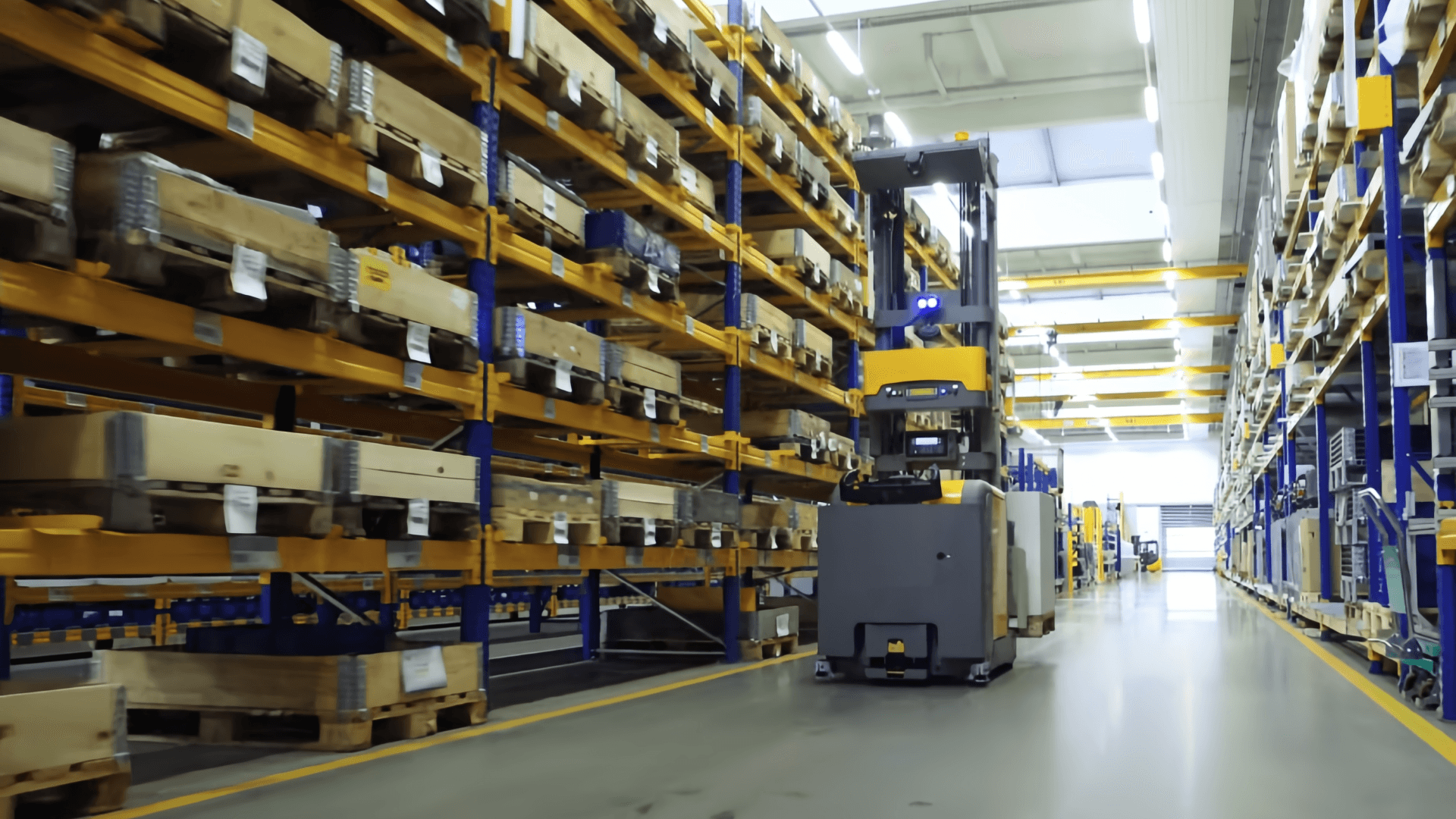
Why Are MEMS Gyroscopes Vital in Robotics?
As robotics systems become faster, more mobile, and more dynamic, precise orientation control is no longer optional—it’s mission-critical. While many sensors can detect motion, only MEMS gyroscopes offer real-time angular velocity measurement independent of external references like GPS or magnetic fields. This makes them irreplaceable in scenarios where timing, stability, and responsiveness directly impact safety and performance.
Their value becomes even more apparent in two high-growth robotic segments:
- In AGVs, MEMS gyros support dead-reckoning during GPS outages, enabling smooth turns, consistent heading, and real-time feedback for SLAM and path planning.
- In humanoid robots, they allow coordinated joint motion, fast reaction to external forces, and continuous balance control during walking or manipulation.
Compared to legacy inertial sensors, MEMS gyros bring three key advantages:
- Miniaturization– easily embedded in compact mobile robots and articulated joints
- Scalability– cost-effective enough for fleet-wide or multi-joint integration
- Low-latency performance– enabling tight feedback loops essential for dynamic movement
Instead of treating MEMS gyros as generic components, GuideNAv engineer them specifically for robotic platforms—refining not just the sensor hardware, but also the firmware, filter design, and mechanical integration. This application-driven approach is why our gyroscopes consistently outperform off-the-shelf options in demanding robotics environments.
How to Select the Right MEMS Gyroscope for Robotics
Not all MEMS gyroscopes are created equal—and choosing the wrong one can lead to performance drift, system instability, or energy inefficiency. The ideal gyro depends heavily on the robotic platform’s form factor, motion dynamics, and control loop sensitivity.
Here’s how I typically approach MEMS gyro selection for different robotic systems:
For AGVs (Automated Guided Vehicles):
- Bias Stability: Moderate (<10 °/h) is sufficient for short to mid-range dead-reckoning.
- Bandwidth: 50–100 Hz for smooth heading updates without excessive noise.
- Shock Tolerance: Must withstand >5000 g for mechanical durability during motion events.
- Power: Below 100 mW to maintain system-wide energy efficiency.
For Humanoid Robotic Arms:
- Bias Stability: High precision (<3 °/h) is critical for joint-level accuracy.
- Bandwidth: 200+ Hz to track rapid articulation and fine motor commands.
- Form Factor: Ultra-compact, as sensors are embedded in each joint.
- Power Budget: <50 mW per joint to avoid heat buildup and battery drain.
Parameter | AGV Application | Humanoid Application |
---|---|---|
Bias Stability | <10 °/h | <3 °/h |
Bandwidth | 50–100 Hz | 200+ Hz |
Shock Tolerance | >5000 g | >3000 g |
Size | Compact | Ultra-compact |
Power | <100 mW | <50 mW per joint |
With hundreds of deployments behind us, we understand that spec sheets alone don’t guarantee success. That’s why we work closely with robotic system engineers to translate real-world motion profiles into sensor configurations that deliver lasting performance and reliability—not just in the lab, but on the warehouse floor and in the field.
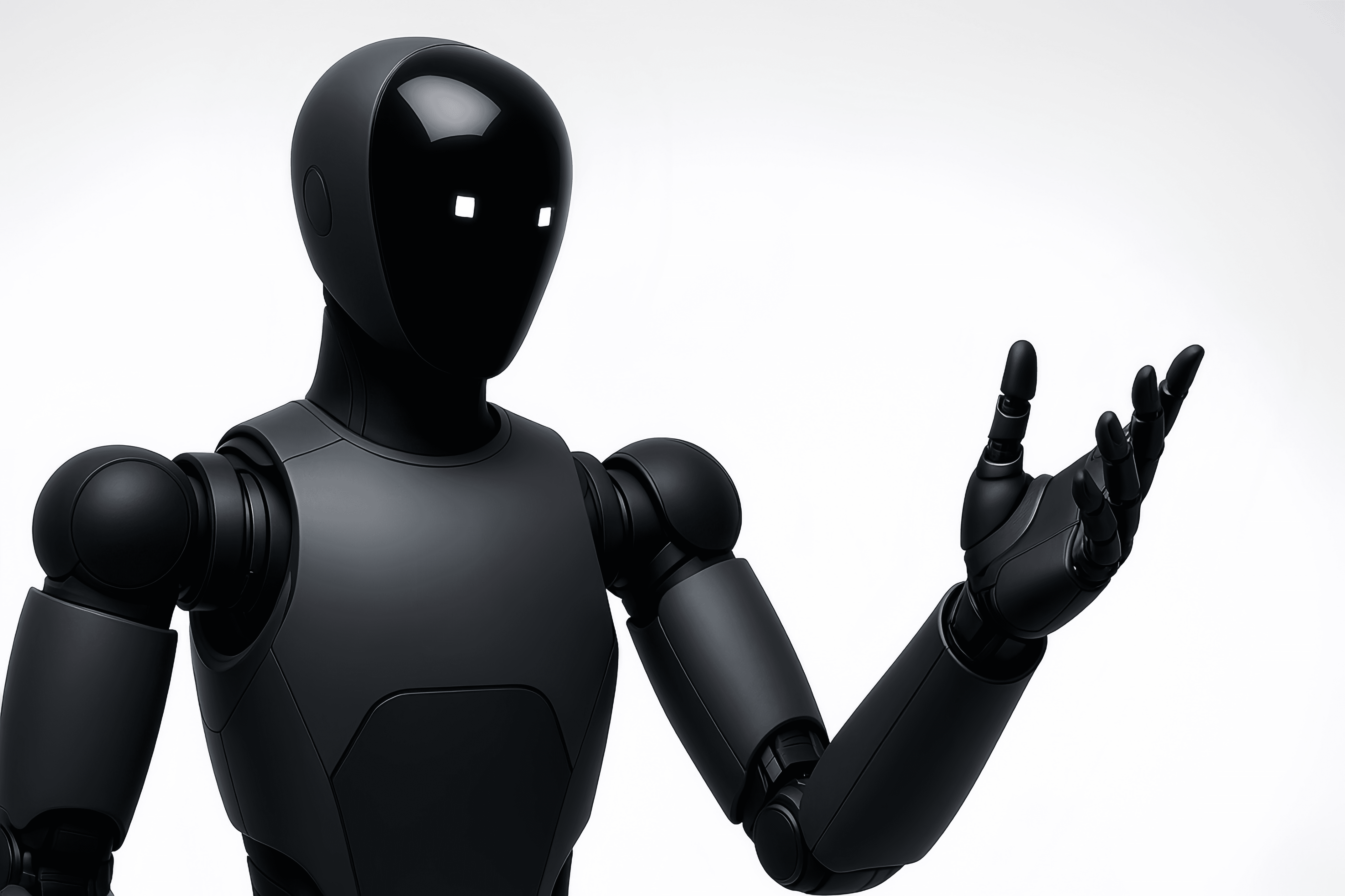
Use Case 1: MEMS Gyros in Warehouse AGVs
Autonomous Guided Vehicles (AGVs) operate in dense indoor environments where GPS signals are unreliable or entirely absent. In these conditions, precise heading estimation is critical—especially over long paths or tight corners. But even small sensor drift can accumulate rapidly, leading to navigation errors, path deviation, and degraded SLAM accuracy—ultimately resulting in task-level failure or operational breakdown.
This is where MEMS gyroscopes become essential. By delivering continuous, real-time angular rate data, they support:
- Dead-reckoningwhen GNSS is unavailable
- Sensor fusionwith wheel encoders and vision-based SLAM
- Stabilityin motion control and route re-planning under dynamic layouts
In one deployment, we replaced a legacy gyro with our tactical-grade MEMS IMU across a warehouse AGV fleet. During repeated mission cycles totaling several hours of runtime, heading drift was reduced by 38%, and localization errors consistently stayed within sub-20 cm—even without reliance on external markers.
For robotics teams working on AGV fleets, the lesson is clear: navigation robustness starts with inertial accuracy—and that starts with a high-quality MEMS gyro.
Use Case 2: MEMS Gyros in Humanoid Arms
Humanoid robots require precise joint coordination and constant balance adjustment—often across dozens of axes simultaneously. In this setting, even slight sensing delays can lead to instability or motion failure.
By embedding MEMS gyroscopes directly into each joint, robots gain:
- High-speed angular feedbackfor reflex-level joint control
- Stability during gait and manipulation, even on uneven surfaces
- Low-latency responseto external forces and motion transitions
In one project, replacing generic IMUs with GuideNav’s tactical-grade MEMS gyros cut fall rates by 42%, and improved joint positioning accuracy to within 1.2° RMS—even during fast, load-varying motion.
When it comes to dynamic movement, the difference between smooth and unstable often lies in the quality of the MEMS gyro.
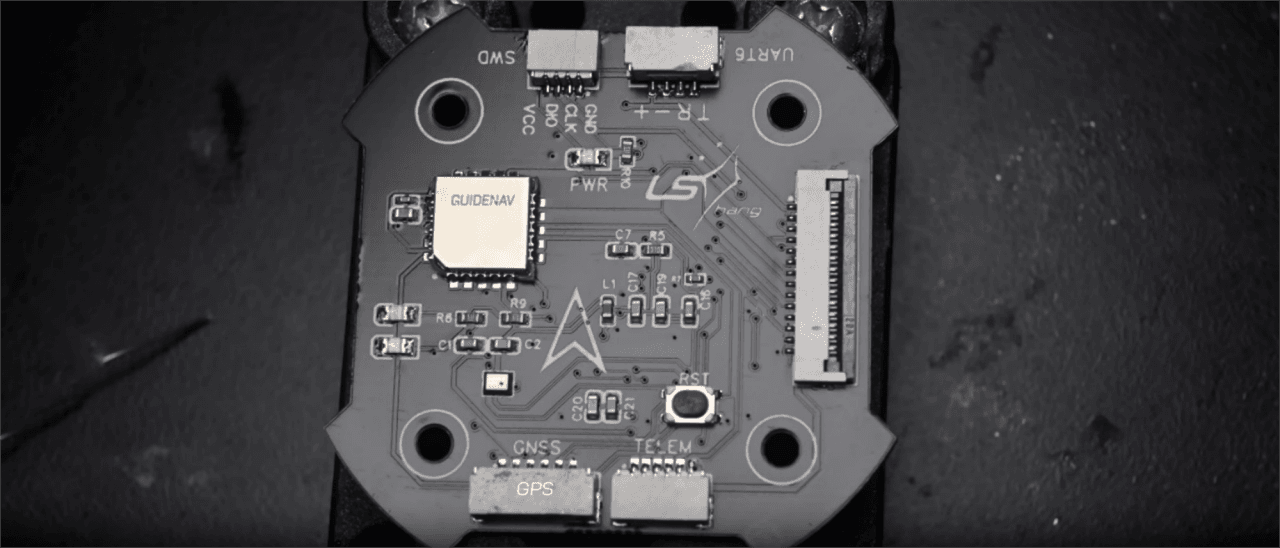
Why GuideNav?
Precision motion in robotics starts with reliable inertial sensing. At GuideNav, we design MEMS gyroscopes specifically for robotic platforms—built to withstand shocks, minimize latency, and fit within space-constrained environments.
For compact integration needs such as robotic joints, we offer chip-level solutions like the GUIDEG4000—a sub-9 mm MEMS gyro with <1 °/h bias instability and up to 400 Hz bandwidth. When higher-level integration is required, our tactical-grade IMUs provide robust, low-drift performance across full systems.
From early prototyping to volume deployment, we’ve helped robotics teams worldwide turn sensing precision into real-world performance. Because when movement matters, the right gyro isn’t just a spec—it’s a foundation.