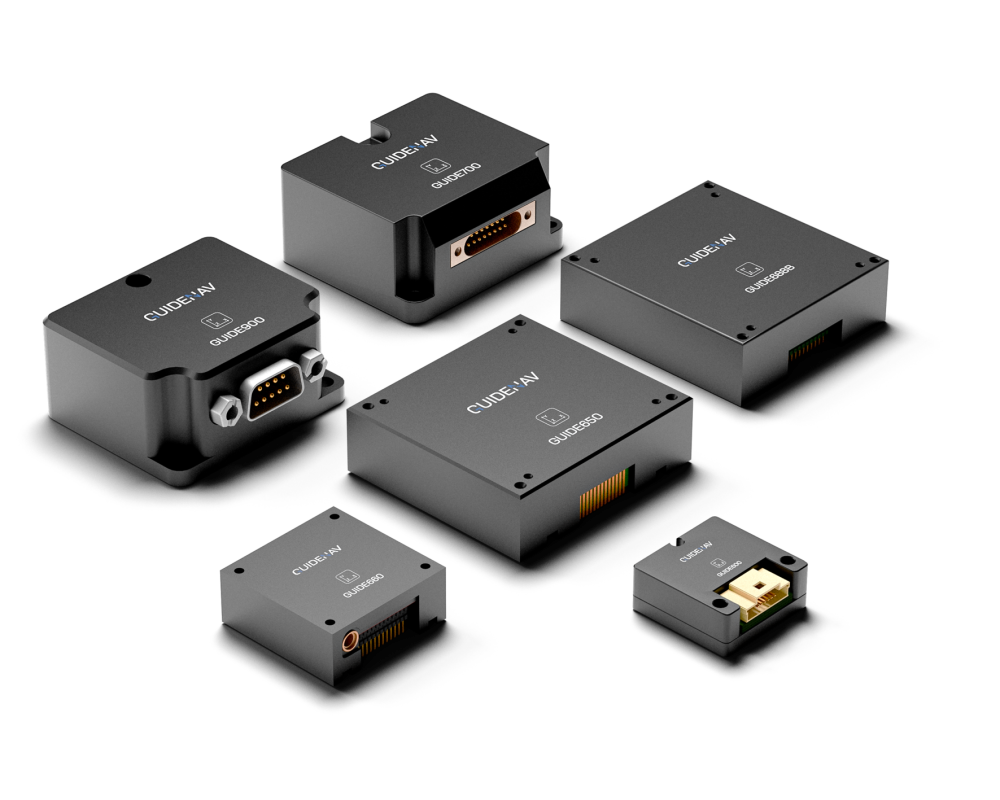
Inertial Measurement Unit (IMU) Trusted Worldwide
Inertial Measurement Unit
15,000+ IMU Systems in Operation in 35+ Countries
Custom Solutions Trusted by Global Key Players
GuideNav’s inertial measurement unit(IMU) solutions are engineered to deliver exceptional performance across aerospace, defense, and industrial applications. Whether you need the compact and cost-effective MEMS IMU or the ultra-high-accuracy FOG IMU, we provide cutting-edge technology trusted in the most demanding environments.
Guidenav‘s Featured MEMS based imu Model
FEATURED MEMS IMU MODELS
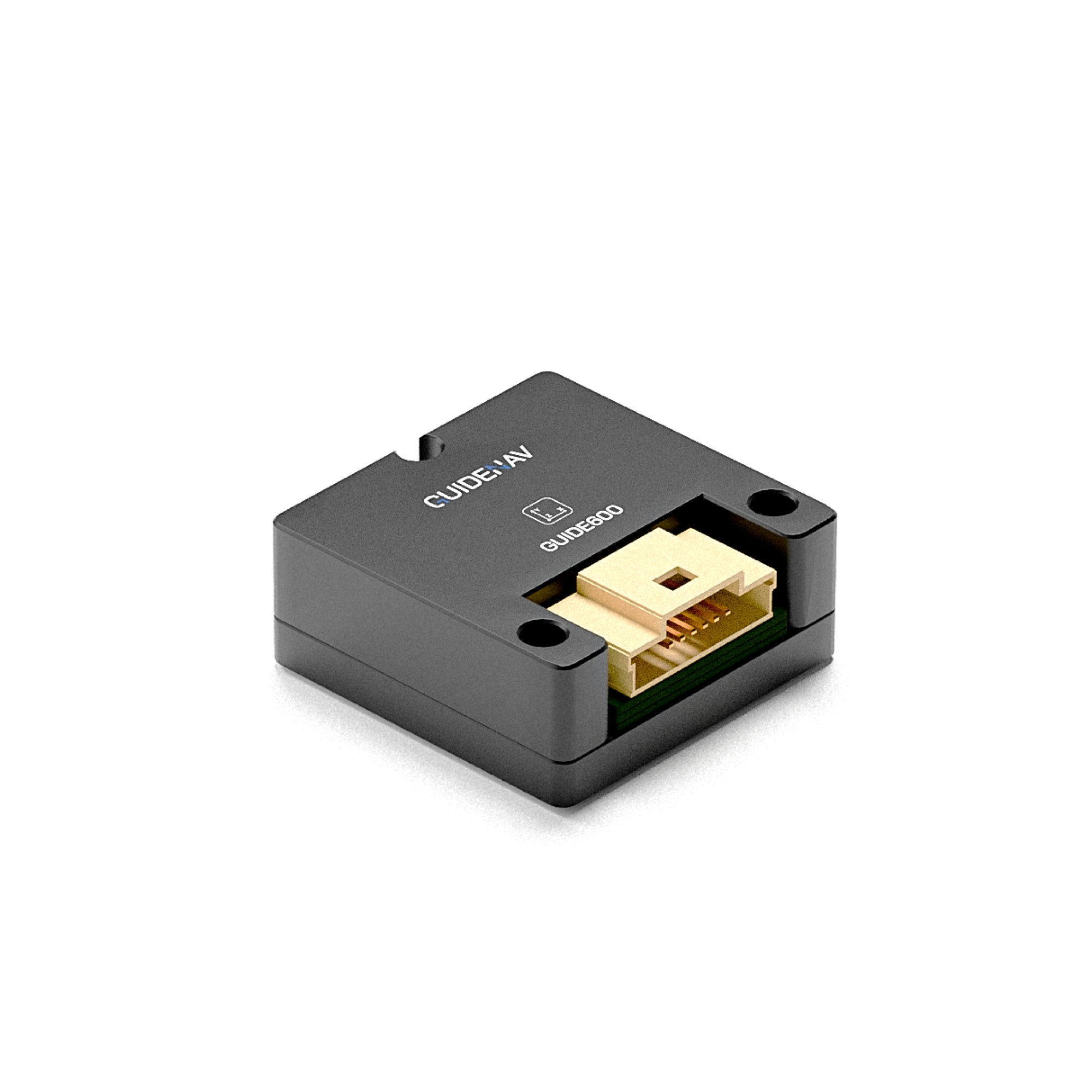
- Cost-effective
- Gyro range: ± 500 °/s
- Bias instability: ≤ 2 °/h
- Bias stability: ≤ 10°/h
- Weight: ≤ 10g
- Protocol: UART
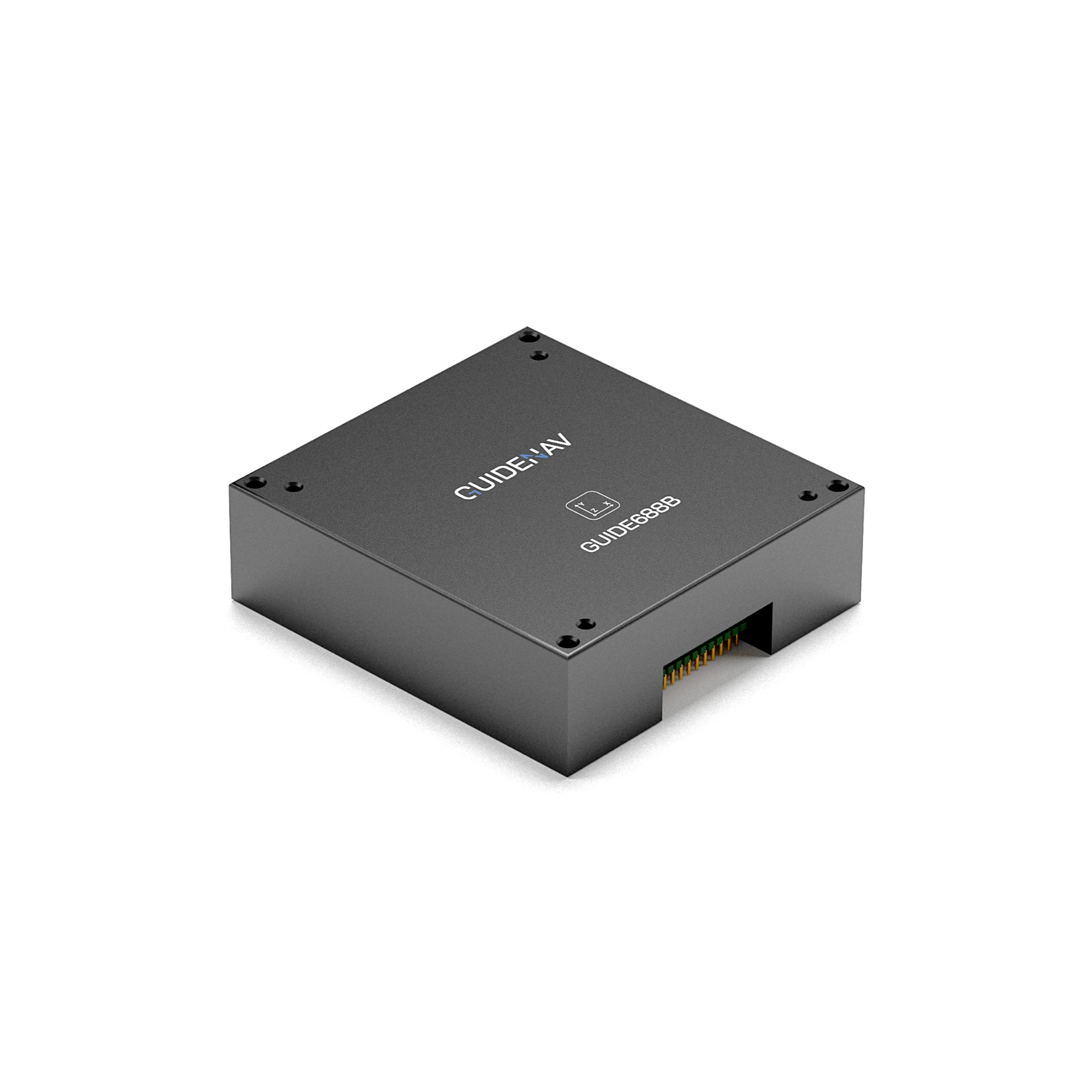
- 10-axis MEMS IMU
- Gyro range: ± 450 °/s
- Bias instability: ≤ 2°/h
- Bias stability: ≤ 4°/h
- Weight: ≤ 40g
- Protocol: SPI
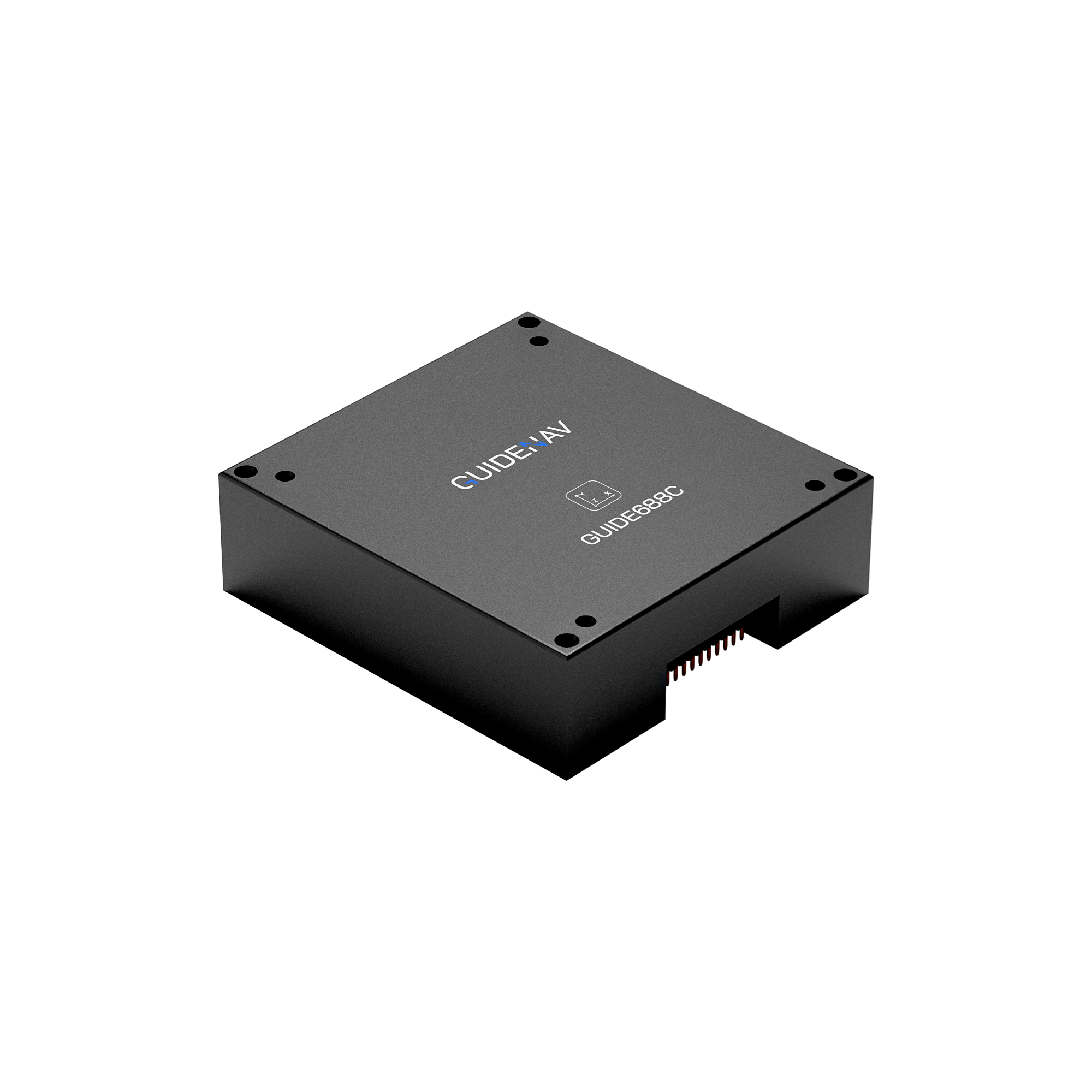
- 10-axis MEMS IMU
- Gyro range: ± 450 °/s
- Bias instability: ≤ 0.8 °/h
- Bias stability: ≤ 3°/h
- Weight: ≤ 40g
- Protocol: SPI
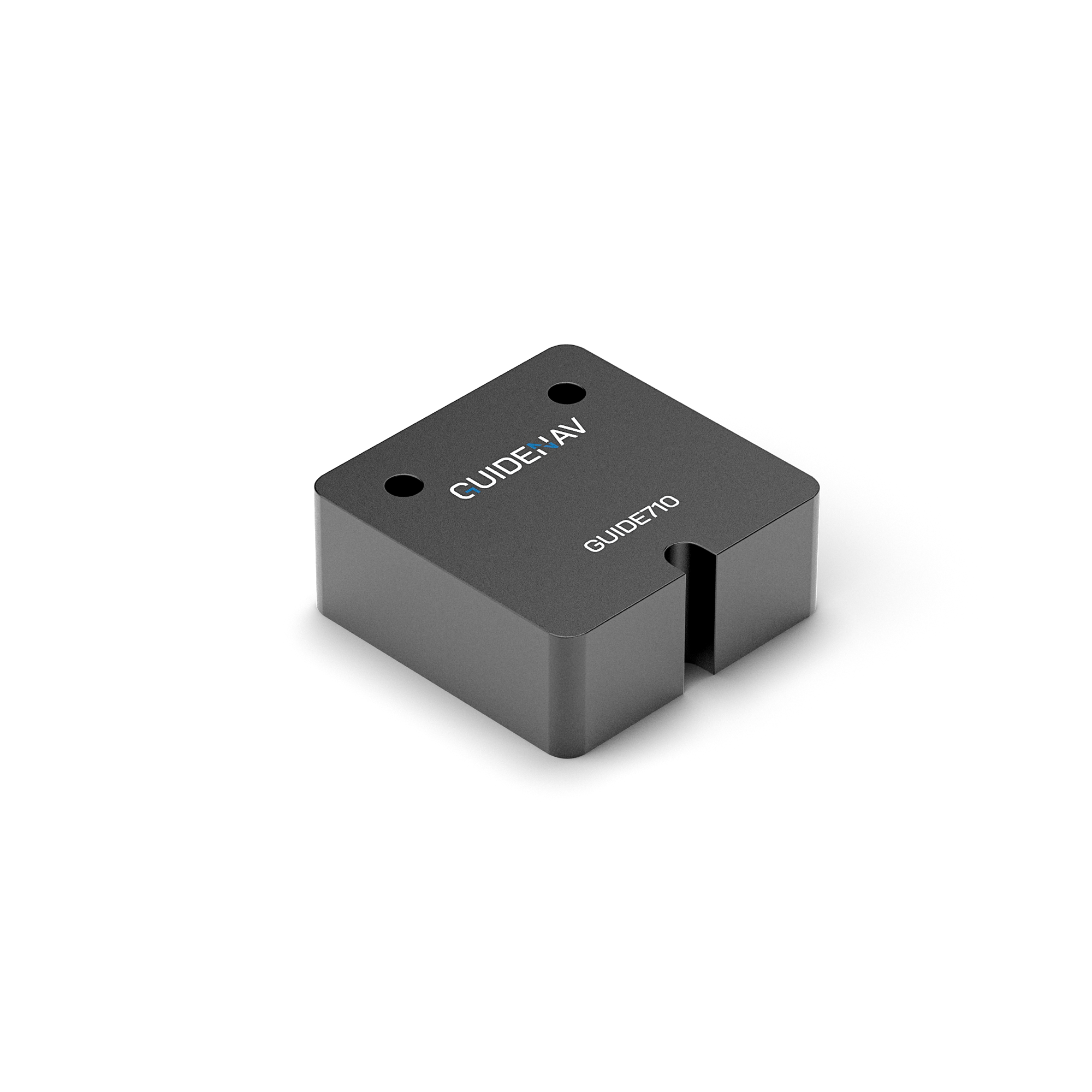
- Medium-High Accuracy
- Gyro range: ± 320 °/s
- Bias instability: ≤ 0.4 °/h
- Bias stability: ≤ 2°/h
- Weight: ≤ 10g
- Protocol: RS422
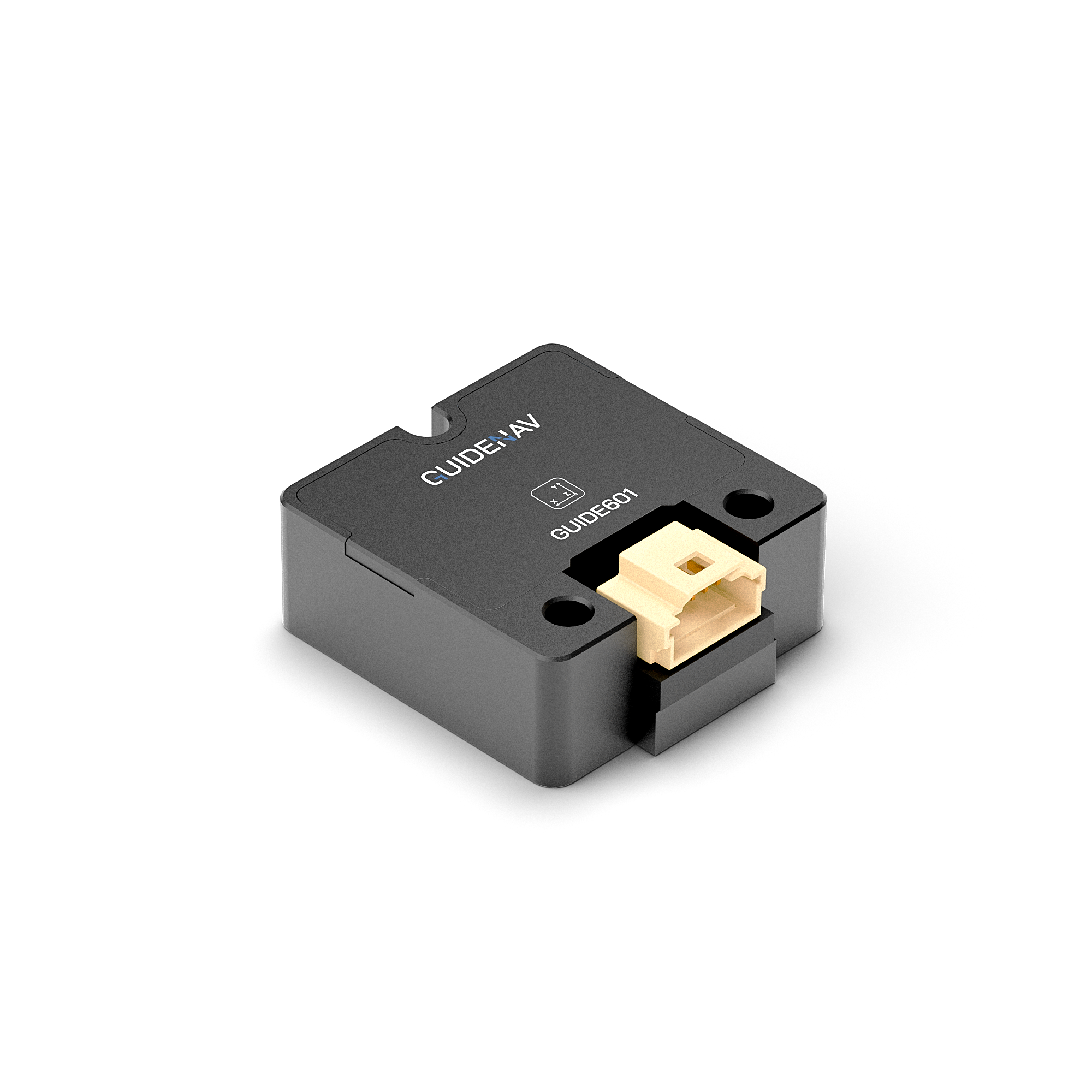
- Wide Gyro Range
- Gyro range: ± 2000 °/s
- Bias instability: ≤ 3 °/h
- Bias stability: ≤ 10°/h
- Weight: ≤ 30g
- Protocol: UART
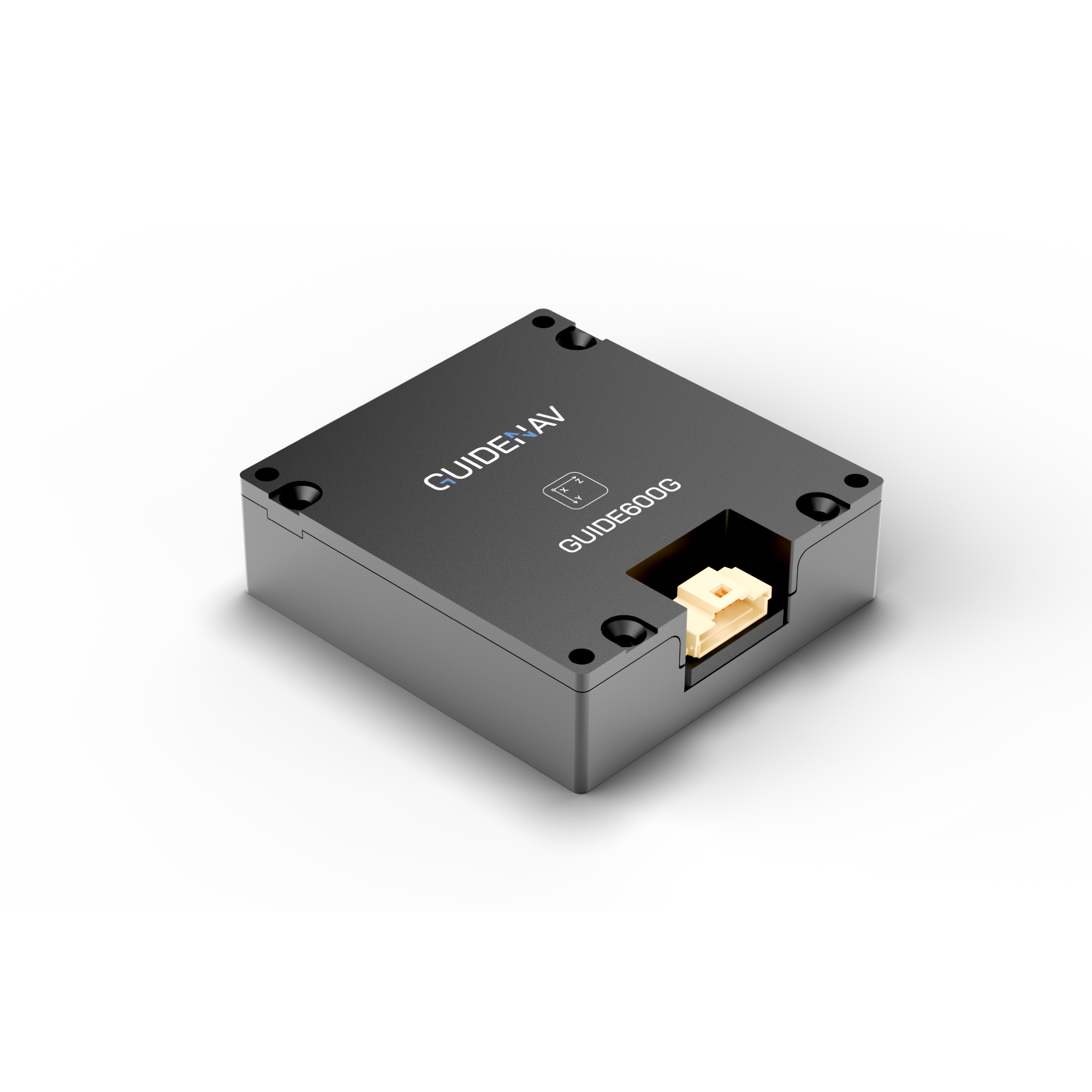
- GUN-HARD to 20,000g
- Gyro range: Up to 6000 °/s
- Bias instability: ≤ 3°/h
- Bias stability: ≤ 10°/h
- Weight: ≤ 50g
- Protocol: UART
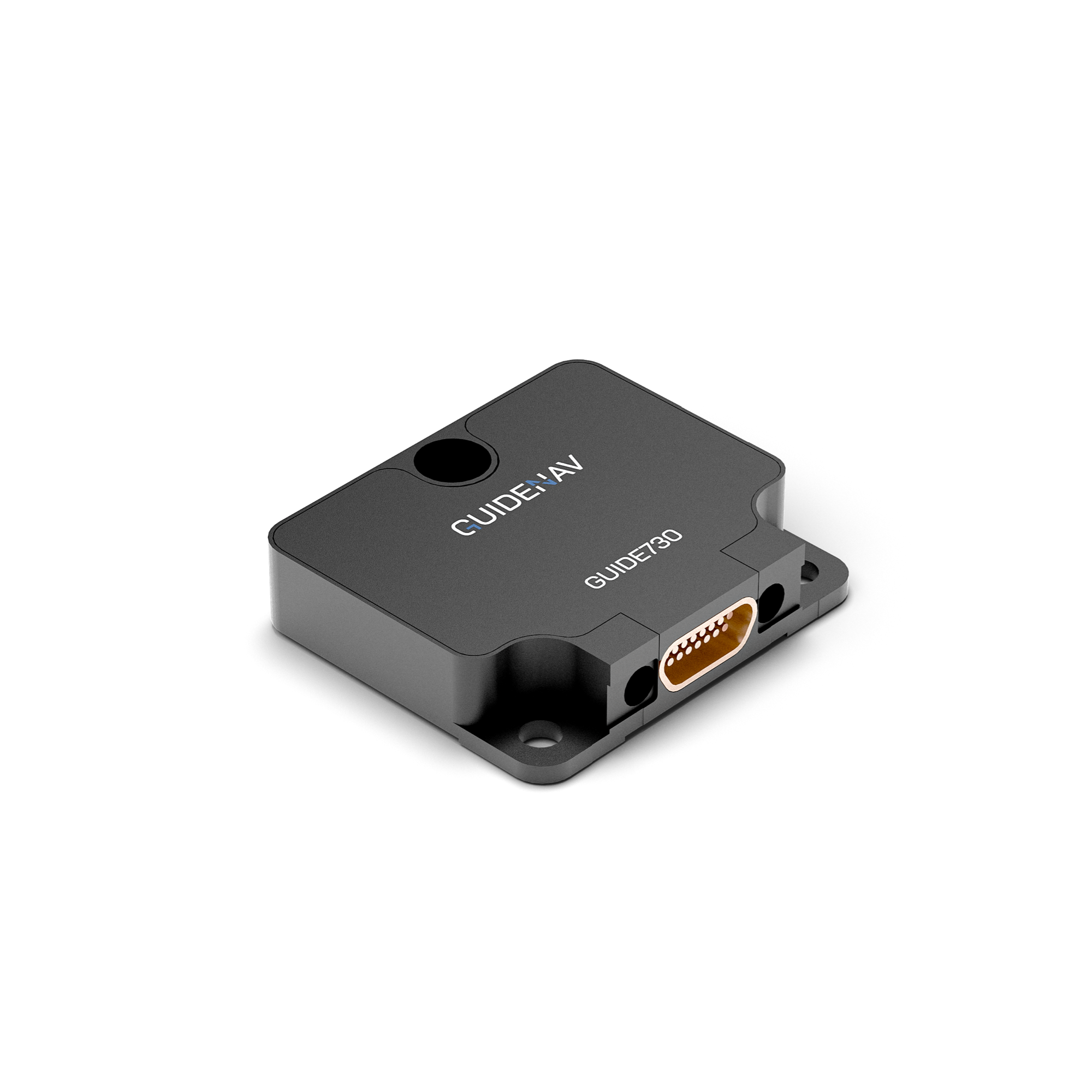
- High-accuracy
- Gyro range: ± 450 °/s
- Bias instability: ≤ 0.2 °/h
- Bias stability: ≤ 1°/h
- Weight: ≤ 40g
- Protocol: RS422
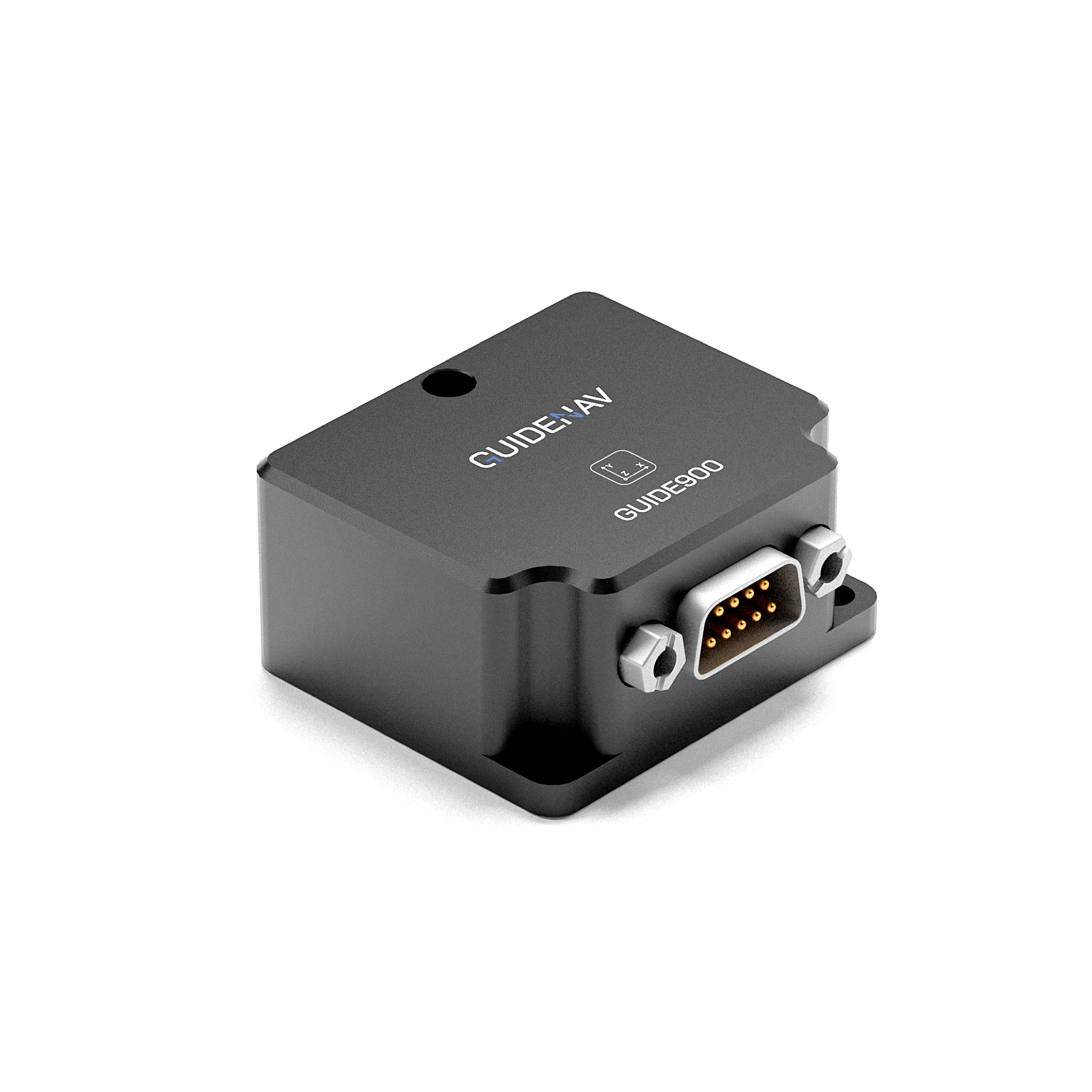
- Ultra-high Accuracy
- Gyro range: ± 400 °/s
- Bias instability: ≤ 0.1 °/h
- Bias stability: ≤ 0.5°/h
- Weight: ≤ 55g
- Protocol: RS422
Guidenav‘s Featured Fiber Optic based inertial measurement unit
FEATURED FOG IMU MODELS
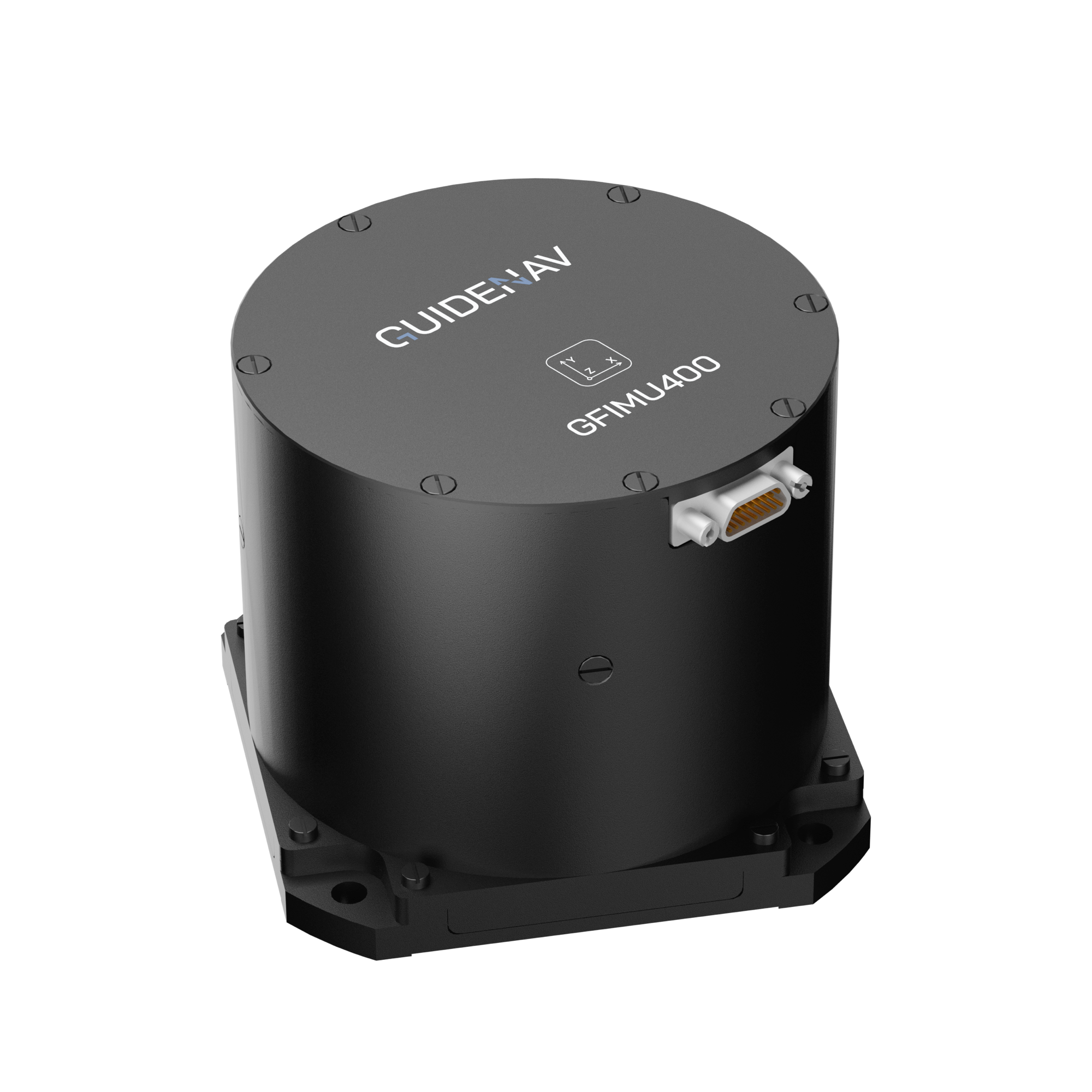
- Medium Precision
- Bias stability(10s) ≤0.1°/h
- Gyro angular random walk:≤0.02 deg/√h
- ± 500 °/s range
- Weight:<900 grams
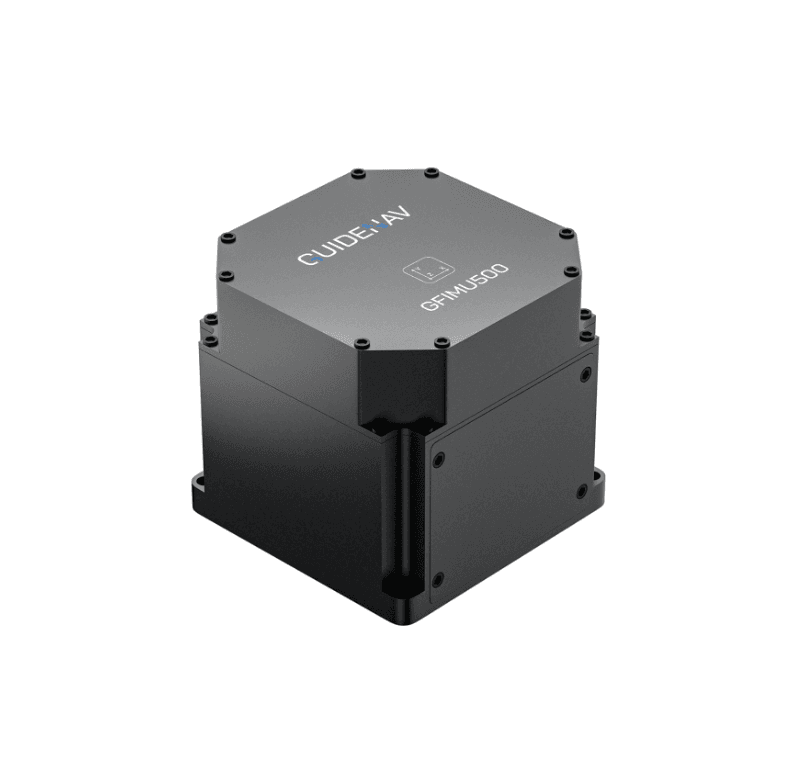
- Medium-High Precision
- Bias stability(10s) ≤0.05°/h
- Gyro angular random walk: ≤0.005 deg/√h
- ± 500 °/s range
- Weight:<1200 grams
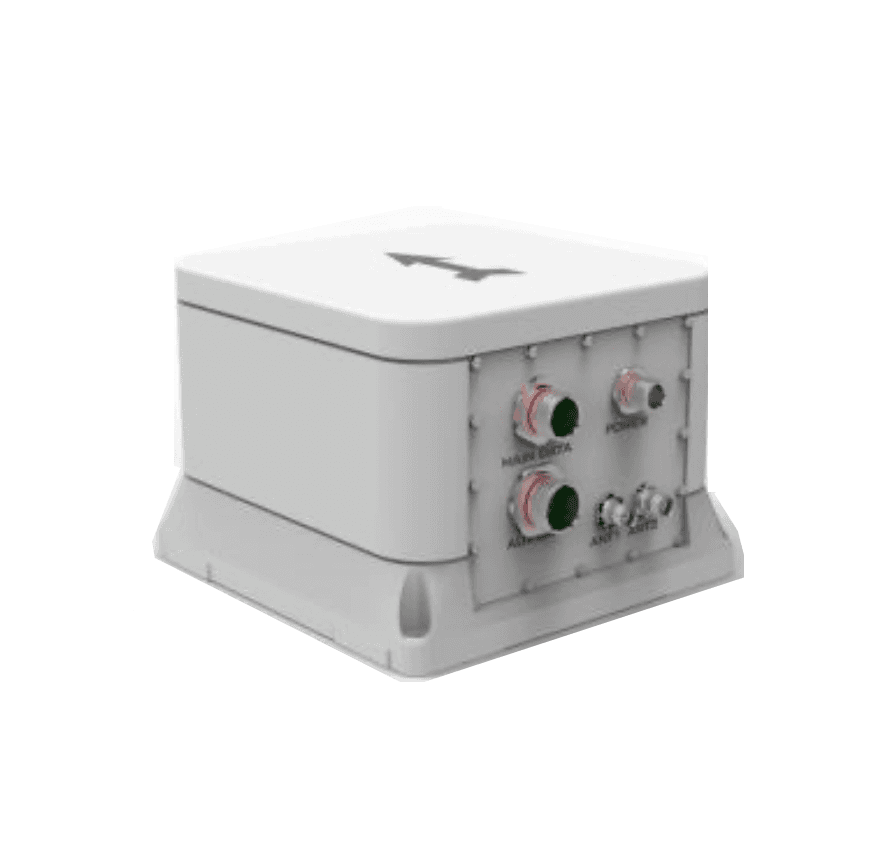
- High precision
- Bias stability(10s) ≤0.01°/h
- Gyro angular random walk:≤0.0005 deg/√h
- ± 300 °/s range
- Weight:<5000 grams
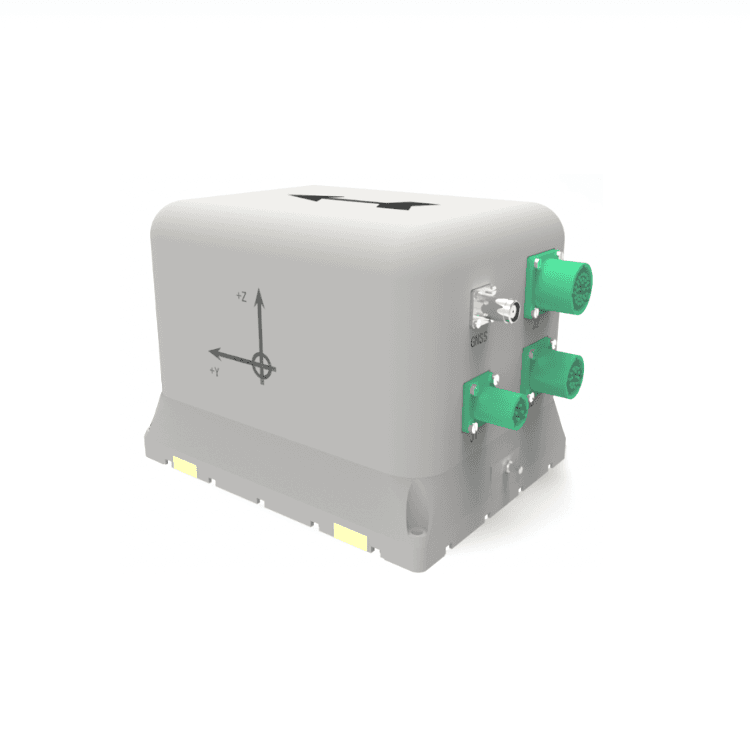
- Ultra-High precision
- Bias stability(10s) ≤0.005°/h
- Gyro angular random walk:≤0.0003 deg/√h
- ± 500 °/s range
- Weight:<5000 grams
Get Your Custom Solution Now
Your project deserves a solution tailored to your exact specifications. To ensure we provide the best Inertial Measurement Units (IMU) for your needs, we invite you to share the specific parameters and performance requirements of your applications. Whether it’s precision, stability, or size constraints, our team is ready to help you find the perfect fit.
Table of Contents
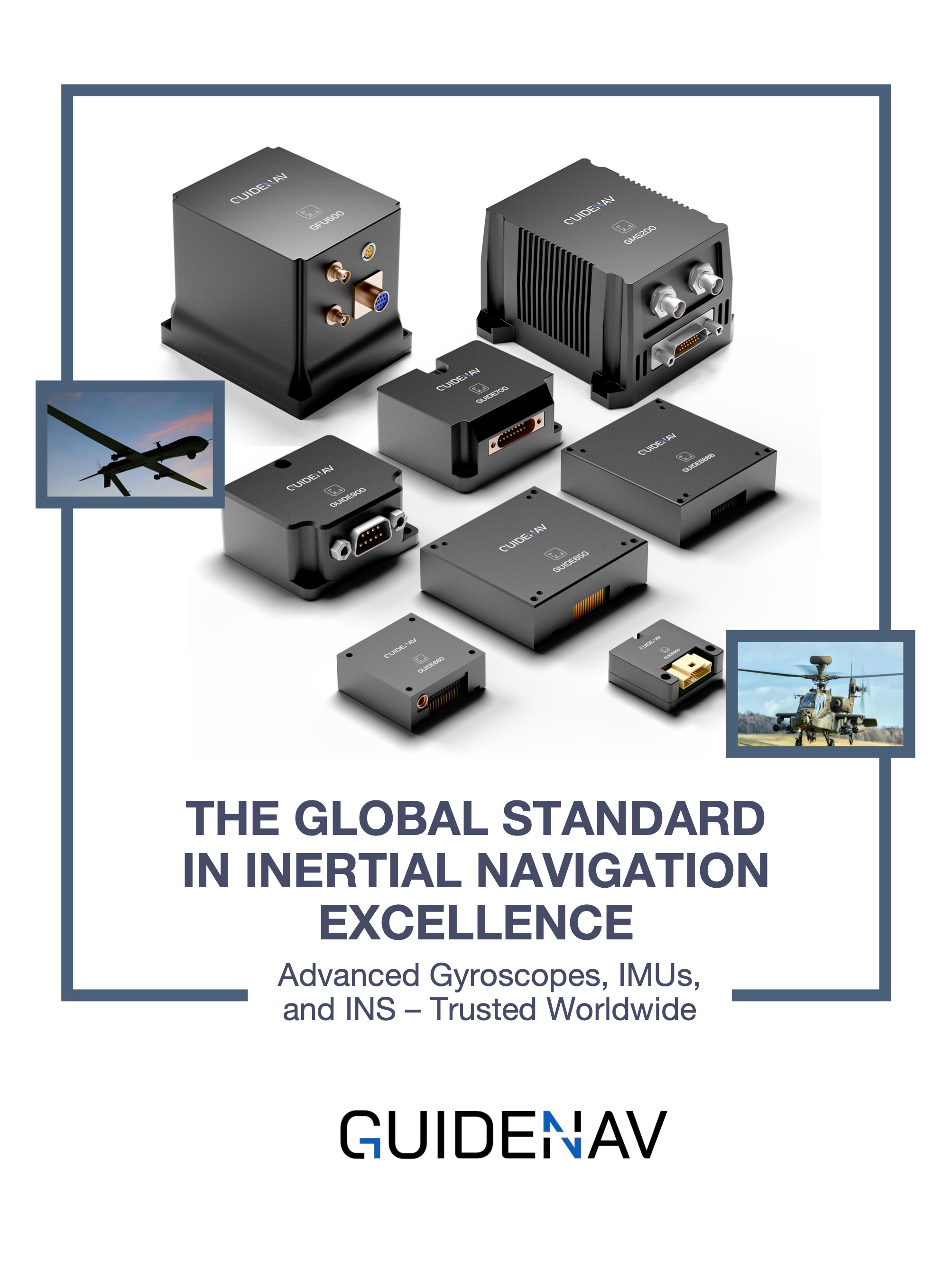
Download this page as a PDF
To save you time, we have also prepared a PDF version containing all the contents of this page, only leave your email and you will get the download link immediately.
Introducing Inertial Measurement Unit (IMU)
What is Inertial Measurement Unit?
An Inertial Measurement Unit (IMU) is a device that measures an object’s acceleration, angular rate, and sometimes magnetic field, providing data on its movement and orientation. It typically consists of accelerometers, gyroscopes, and sometimes magnetometers. IMUs are crucial for systems requiring precise navigation, such as aerospace, defense, and robotics, where they help maintain accurate positioning and stability without relying on external references like GPS.
Applications of Inertial measurement unit (IMU)
Applications of Inertial Measurement Unit(IMU)
01
Aerospace and Aviation
IMUs are vital for aircraft navigation and control. They help maintain orientation and provide real-time data for autopilot systems, helping aircraft stay on course and improve flight safety.
02
Defense and Military
IMUs are widely used in missiles, drones, and military vehicles to provide precise motion tracking, navigation, and target guidance. They enable autonomous systems to function accurately even in GPS-denied environments.
03
Autonomous Vehicles and Drones
In self-driving cars and drones, IMUs provide continuous feedback on orientation, velocity, and movement, helping to stabilize flight and ensure accurate navigation in complex environments.
04
Robotics
IMUs are critical in robotics for precise motion control. They are used in robots to track position and orientation, enabling efficient and autonomous movement in industrial, medical, and service robots.
05
Geophysical Surveying
In geophysical exploration, IMUs are used in equipment to detect and measure seismic movements, providing valuable data for scientific research and resource exploration.
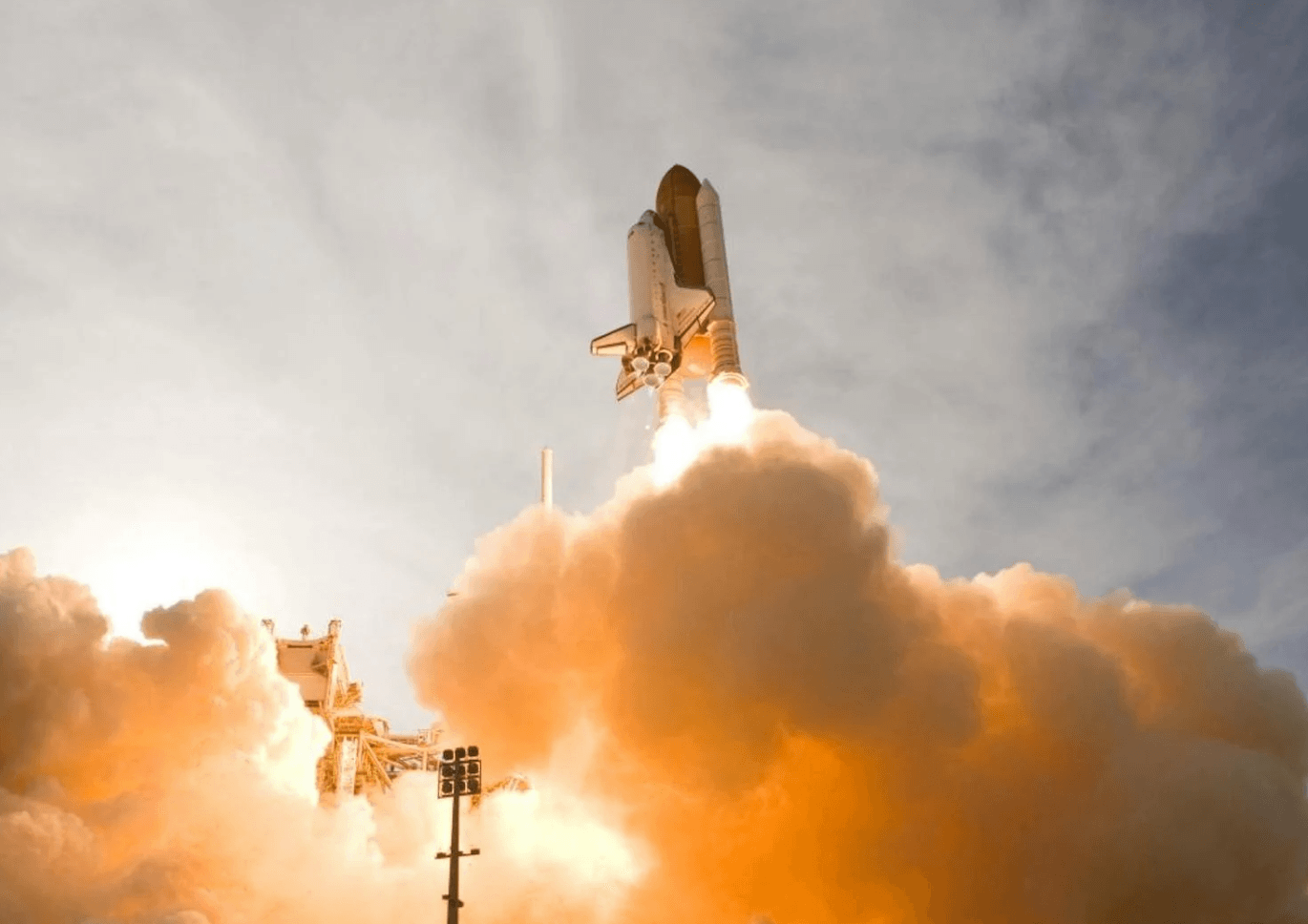
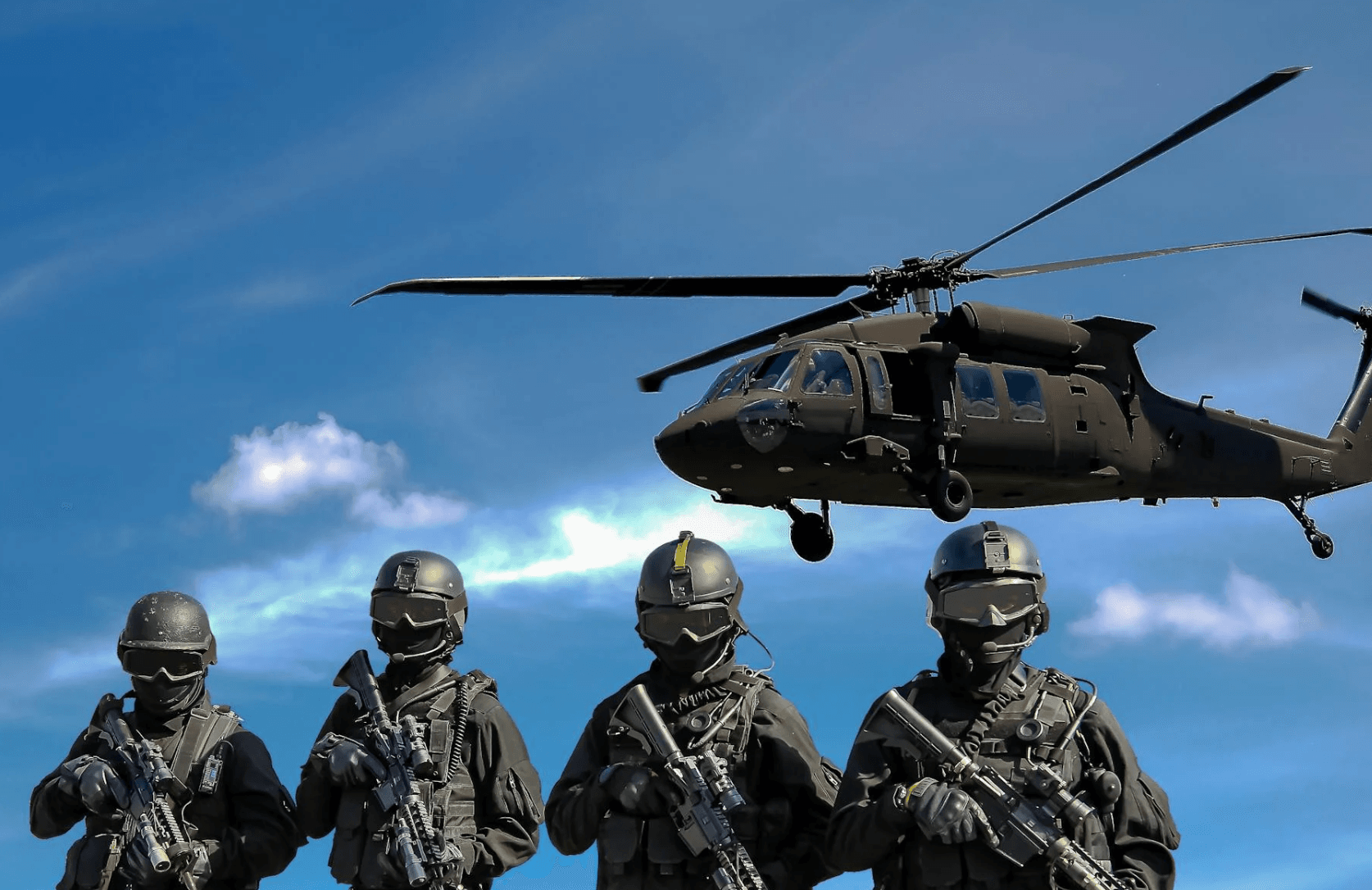
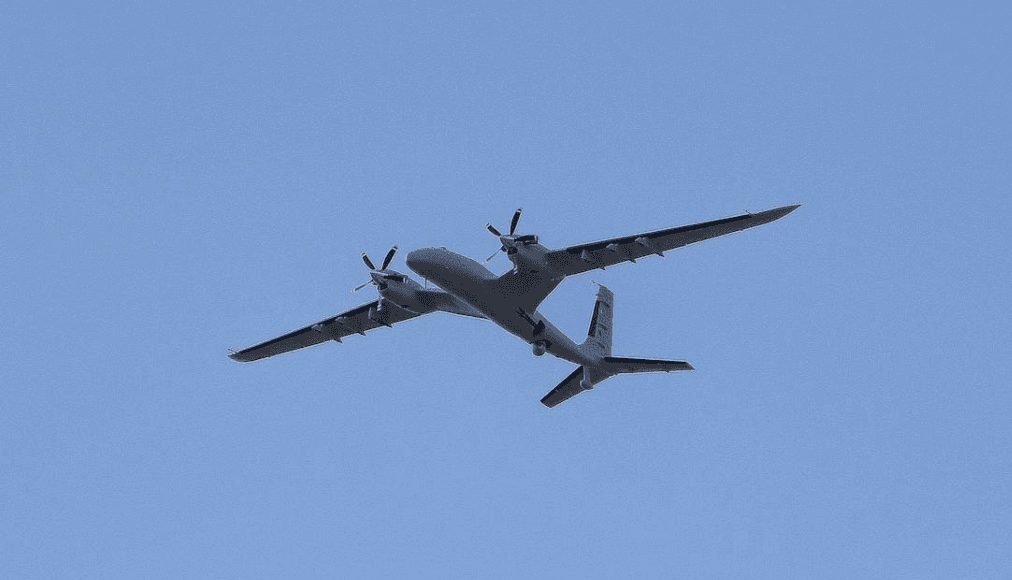
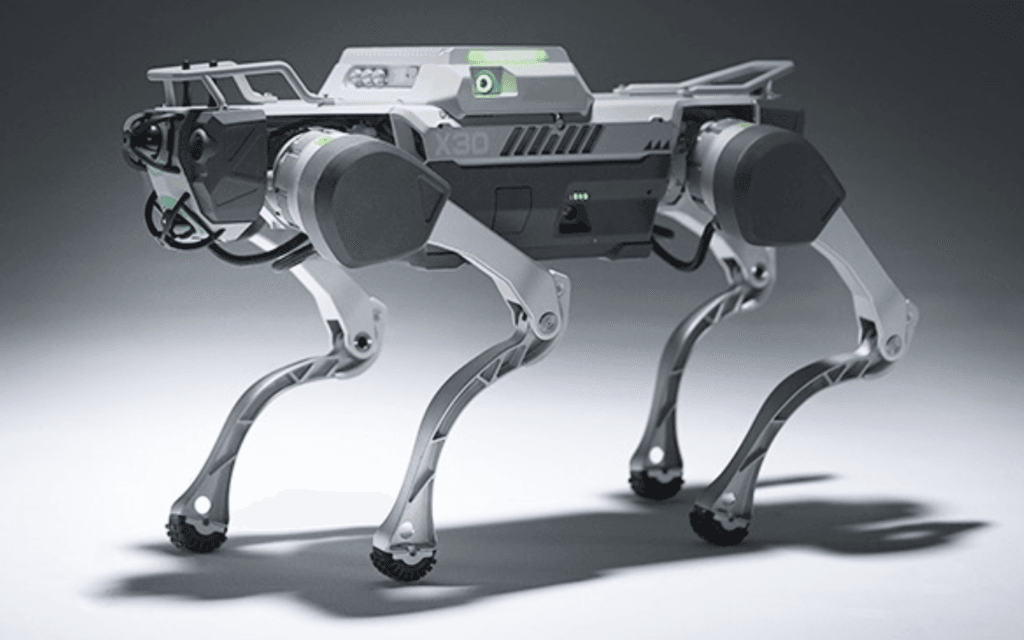
why inertial measurement unit
Why Choose an IMU Instead of Only a Gyroscope?
While both Inertial Measurement Units (IMUs) and gyroscopes measure angular velocity, an IMU provides a more comprehensive solution by combining multiple sensors to offer a broader range of motion and orientation data. Here are the main reasons
Comprehensive Motion Tracking
While a gyroscope measures only angular velocity, an IMU combines accelerometers and sometimes magnetometers to track both linear acceleration and angular rotation, offering a full 3D motion profile.More Accurate Positioning
Gyroscopes can suffer from drift over time. An IMU corrects this by using accelerometer data, providing more stable and accurate orientation and positioning over longer periods.Better Performance in GPS-Denied Environments
IMUs are ideal for applications where GPS isn’t available, such as indoors, underwater, or in space, since they measure both acceleration and rotation, offering complete navigation data.Simplified System Design
An IMU integrates multiple sensors into one compact unit, reducing system complexity and the need for separate accelerometers and gyroscopes.
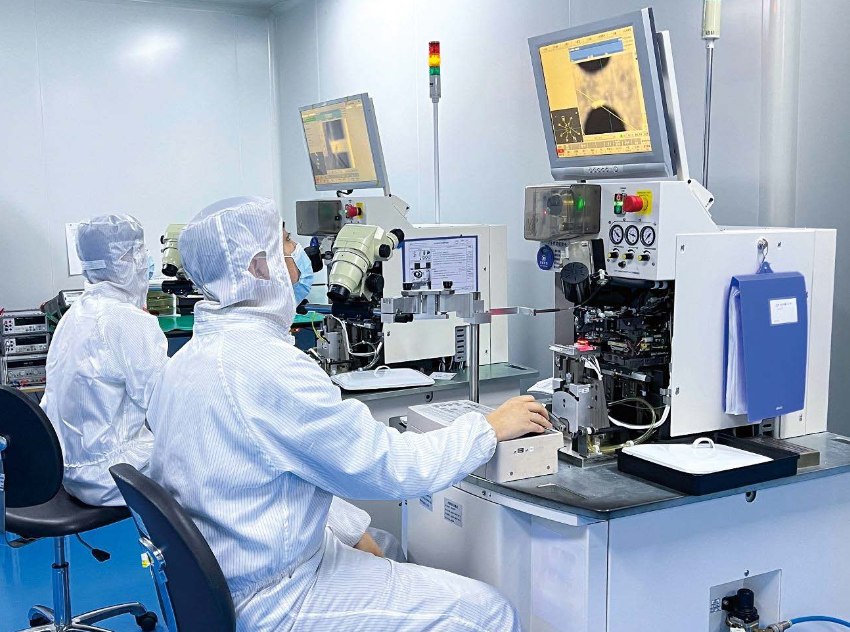
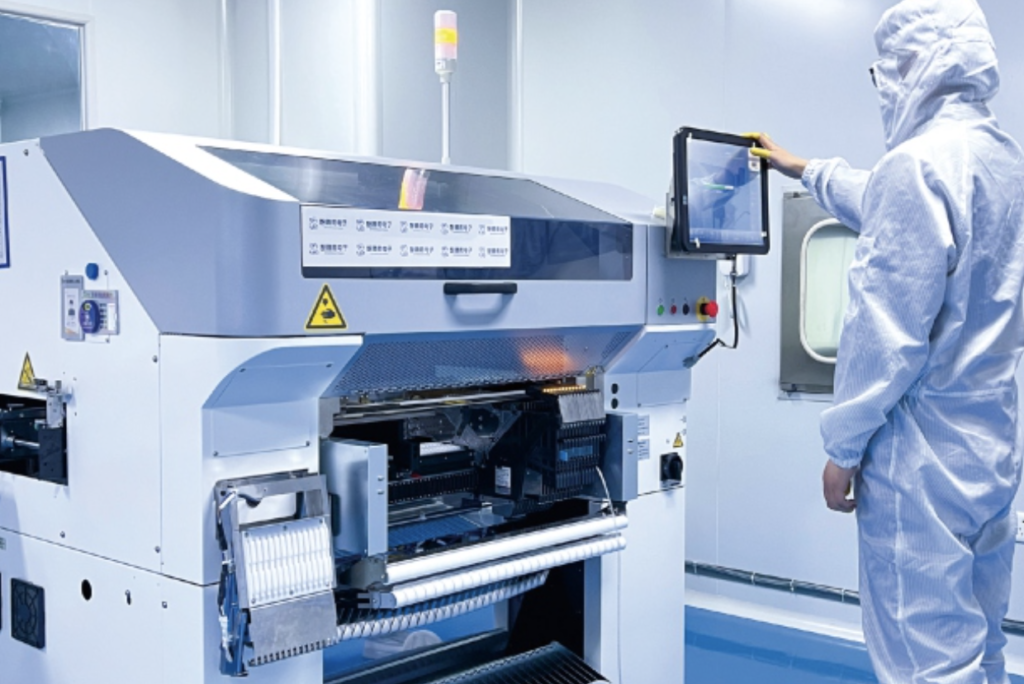
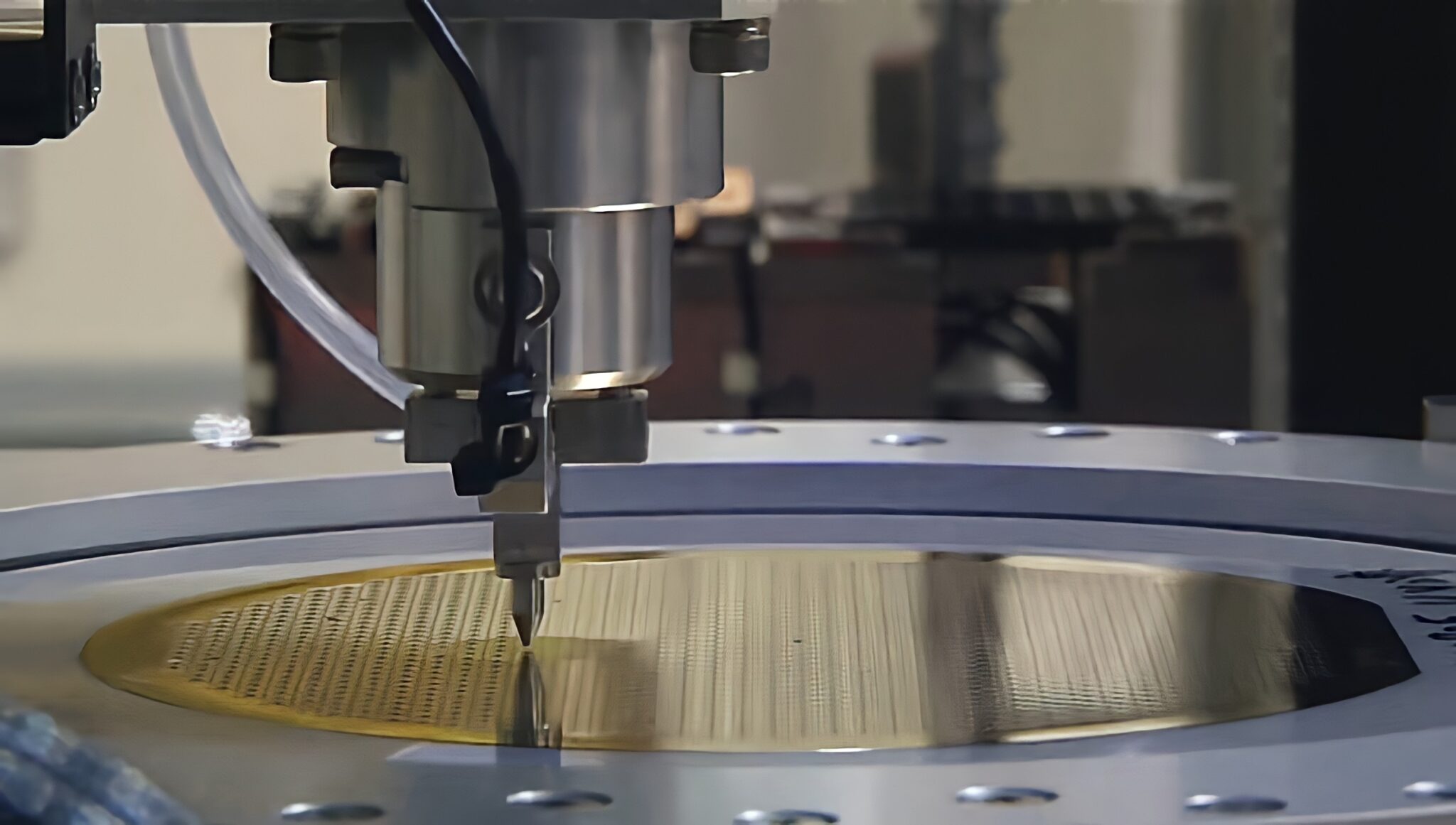
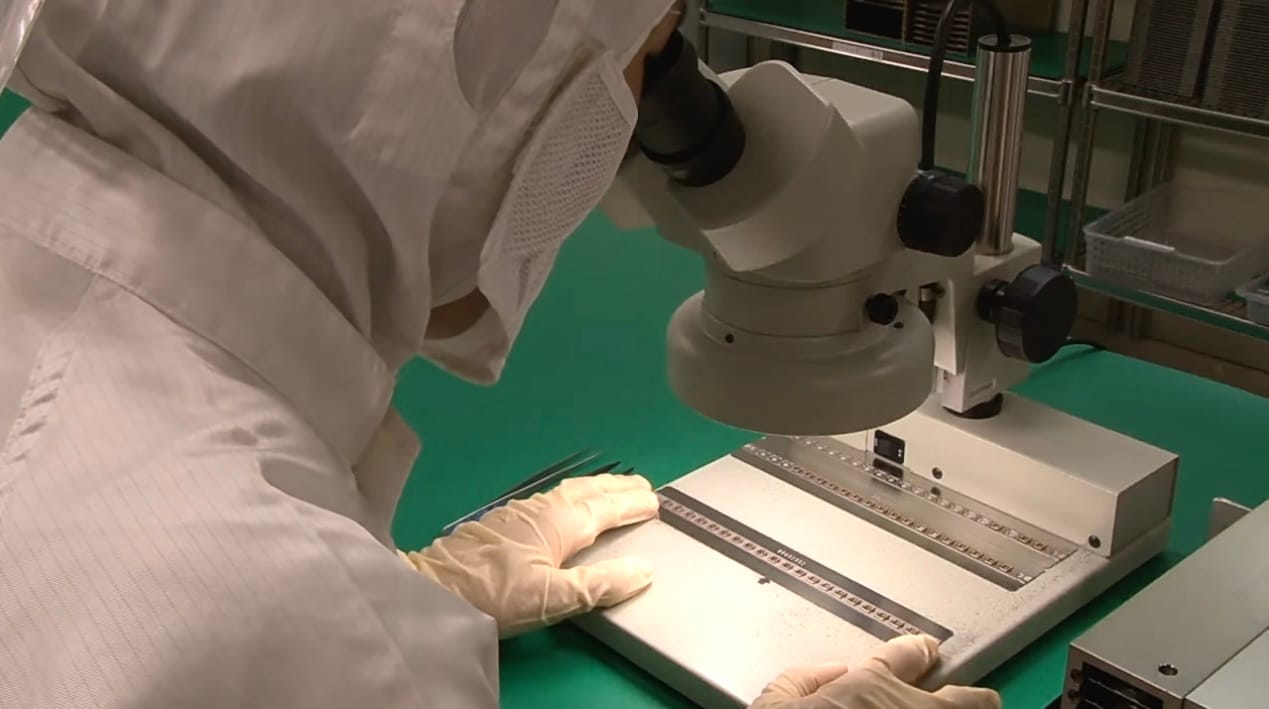
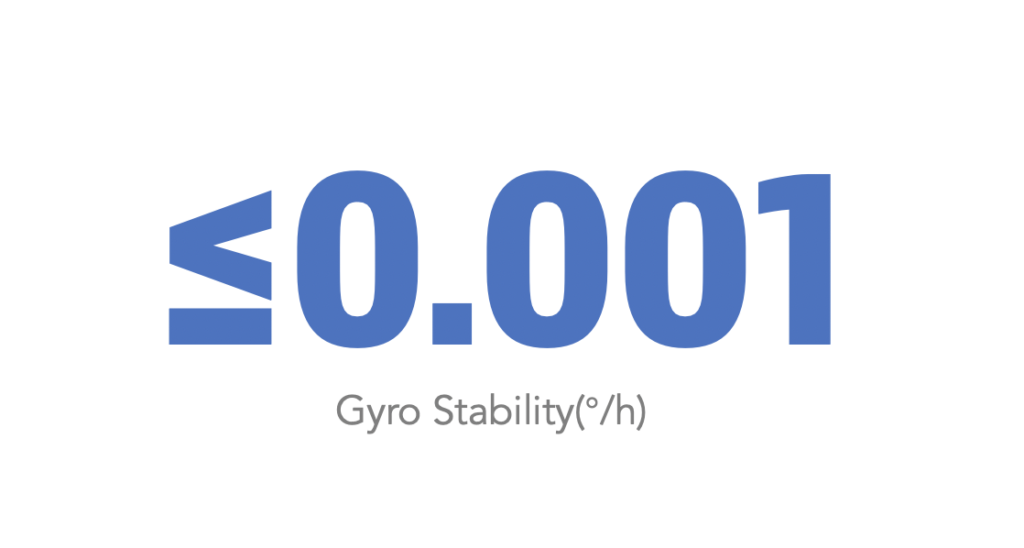
Key parameters of Inertial Measurement Unit (IMU)
Main Specifications of an Inertial Measurement Unit (IMU)
Bias Instability (Gyroscope)
Measures how stable the gyroscope is over time without external inputs, typically given in °/h. Lower values indicate higher stability, which is critical for precision applications like navigation and guidance.Angle Random Walk
Indicates the noise level in angular velocity measurements, given in °/√h. A lower random walk ensures better performance in long-term operations.Measurement Range
Specifies the maximum acceleration (g) or angular rate (°/s) the IMU can measure. A wider range allows it to handle more dynamic environments.Bandwidth
Defines how quickly the IMU can respond to changes, typically measured in Hz. Higher bandwidth supports applications requiring rapid data updates, such as drones or robotics.Environmental Tolerance
Includes operating temperature range and resistance to vibration or shock. This ensures the IMU performs reliably in harsh conditions like aerospace or military applications.
MEMS IMU vs. Fiber Optic IMU: Which is Better?
The choice between MEMS and Fiber Optic Gyroscope (FOG) IMUs depends on your project’s specific requirements. Standard MEMS IMUs are compact, cost-effective, and ideal for applications with moderate accuracy needs. However, advancements in technology now enable high-precision MEMS IMUs to achieve bias instability as low as 0.1°/hr, making them suitable for some military and aerospace applications traditionally dominated by FOG IMUs.
FOG IMUs, however, remain the preferred choice for applications that demand ultra-high accuracy, long-term stability, and reliability in extreme environments. Below is a detailed comparison to help you decide:
Feature | MEMS IMU | FOG IMU |
---|---|---|
Accuracy | Standard MEMS IMUs offer moderate accuracy. High-precision MEMS IMUs can achieve bias instability as low as 0.1°/hr, comparable to entry-level FOG IMUs. | Offers ultra-high accuracy with bias instability as low as 0.001°/hr, making them ideal for long-duration, mission-critical operations. |
Size & Weight | Compact and lightweight, making them suitable for systems with strict size and weight constraints, such as UAVs or robotics. | Larger and heavier, designed for systems where performance outweighs size concerns. |
Environmental Tolerance | Improved robustness in shock, vibration, and temperature variations, especially in advanced MEMS designs. Reliable for most industrial and military applications. | Exceptional reliability under extreme conditions, including high shock, vibration, and prolonged operational demands. |
Cost | More cost-effective, particularly for applications where standard accuracy suffices. High-precision MEMS IMUs are more affordable than FOG IMUs for comparable accuracy. | Higher cost due to the complex optical technology, but justified for systems requiring unparalleled stability and precision. |
Applications | Suitable for general-purpose navigation in UAVs, robotics, industrial systems, and some military-grade applications if using high-precision MEMS. | Preferred for aerospace, missiles, submarines, and critical defense systems requiring long-term stability and ultra-high precision. |
Introducing Inertial Measurement Unit (IMU)
Six-Axis vs Nine-Axis Inertial Measurement Unit
When exploring Inertial Measurement Units (IMUs), you will frequently come across terms like “six-axis IMU” and “nine-axis IMU.” These descriptions refer to the number and type of sensors integrated within the device. Understanding the difference between six-axis and nine-axis IMUs can help you select the right sensor for your specific application.
Feature | Six-Axis IMU | Nine-Axis IMU |
---|---|---|
Components |
3-axis Accelerometer 3-axis Gyroscope |
3-axis Accelerometer 3-axis Gyroscope 3-axis Magnetometer |
Functionality | Measures linear acceleration and angular velocity | Measures linear acceleration, angular velocity, and absolute heading |
Accuracy | Good for short-term stability | Enhanced accuracy with reduced drift over time |
Applications | Drones, Robotics, Consumer Electronics | Navigation Systems, Augmented Reality, Autonomous Vehicles |
Cost | Generally more affordable | Typically higher due to additional sensor |
Inertial Measurement Unit Calibration
What is Inertial Measurement Unit Calibration?
Proper calibration of an Inertial Measurement Unit is critical to ensuring that it performs with the required level of accuracy for its specific application. Without calibration, the data from the IMU could be inconsistent, leading to faulty system behavior. This could impact navigation accuracy in drones, trajectory tracking in aerospace applications, or stability in robotics.
IMUs typically consist of accelerometers, gyroscopes, and sometimes magnetometers. Each of these sensors can suffer from various sources of error, such as temperature fluctuations, mechanical stress, or manufacturing tolerances. Calibration methods help mitigate these issues to ensure precise and reliable data output.
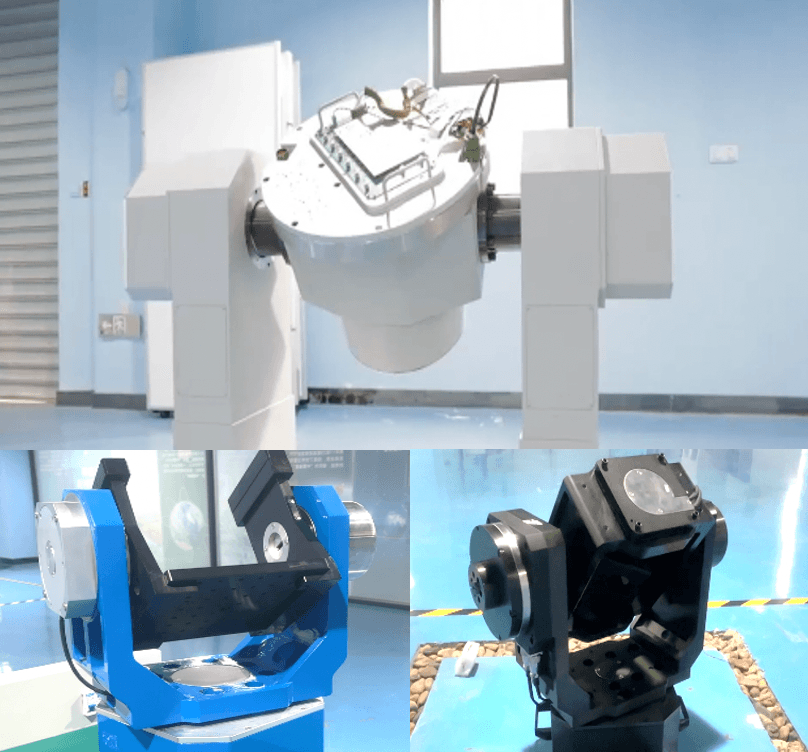
Inertial Measurement Unit vs AHRS vs INS
IMU vs AHRS vs INS: What’s the Difference?
- IMU (Inertial Measurement Unit): Measures acceleration and angular velocity. It provides raw data on motion but does not calculate orientation or position.
- AHRS (Attitude and Heading Reference System): Expands on the IMU by providing real-time orientation (pitch, roll, yaw) and heading information, often by incorporating magnetometers and GPS.
- INS (Inertial Navigation System): Combines the functions of the IMU and advanced algorithms to provide position, velocity, and orientation data without relying on external references like GPS.
Feature | IMU | AHRS | INS |
---|---|---|---|
Purpose | Measures acceleration and angular velocity | Provides real-time orientation (pitch, roll, yaw) and heading information | Provides full navigation data: position, velocity, and orientation |
Sensors | Accelerometer, Gyroscope (sometimes magnetometer) | IMU + Magnetometer (sometimes GPS) | IMU + Advanced algorithms (often with GPS or external inputs) |
Data Output | Raw data (acceleration, angular velocity) | Orientation (pitch, roll, yaw), heading | Position, velocity, and orientation over time |
External | Requires external systems (GPS, magnetometers) for full orientation | Uses magnetometers and GPS to correct drift | Works independently (can be augmented with GPS) |
FOG IMU Type | Price Range | Application |
---|---|---|
Entry-Level FOG IMUs | $10,000 - $30,000 | General commercial or industrial use, drones, basic autonomous vehicles |
Mid-Range FOG IMUs | $30,000 - $70,000 | Military-grade applications, aerospace, high-precision marine navigation |
High-End FOG IMUs | $70,000 - $100,000+ | Critical applications (missile guidance, aerospace, high-precision defense systems) |
What is the price range of FOG IMUs
Price Range of
FOG-based Inertial Measurement Unit (IMU)
The price of a Fiber Optic Gyroscope (FOG)-based Inertial Measurement Unit (IMU) can vary significantly depending on the specific application, performance requirements, and additional features. Factors influencing the price include:
- Performance Specifications (e.g., accuracy, stability)
- Size, Weight, and Power Consumption (SWaP-C)
- Environmental Protection (e.g., ruggedization for harsh conditions)
- Customization for specific application needs
For price info about MEMS IMU, please visit our MEMS IMU page.
Inertial Measurement Unit Selection Guide
How to Select
Inertial Measurement Unit?
STEP 1
Define Your Application
What is your primary use case? (e.g., aerospace, defense, robotics, automotive, consumer electronics)
What level of accuracy and precision is required? (e.g., sub-degree, high-precision)
STEP 2
Type of IMU: MEMS vs. FOG-Based
- MEMS: Affordable, compact, and ideal for low-to-medium accuracy.
- FOG: High-precision, reliable, and suited for demanding applications.
STEP 3
Determine Accuracy Requirements
Choose the level of accuracy needed (e.g., degrees per hour for gyroscopes) based on your application.
STEP 4
Size and Weight
Ensure the IMU fits your system’s space and power constraints, especially for drones or portable devices.
STEP 5
Assess Environmental Conditions
Select an IMU that can withstand environmental factors like temperature extremes, shock, and vibration.
STEP 6
Customization and Integration Options
Make sure the IMU supports the right interfaces and data output for seamless integration into your system.
Inertial Measurement Unit Manufacturer
Why Choose Guidenav?
Trusted by keyplayers
Our advanced inertial navigation products are trusted by leading organizations in the aerospace, defense, commercial, and industrial sectors from over 25 countries. Our reputation for reliability and precision sets us apart.
Top Performance
Our products deliver top-tier performance with excellent bias stability. Designed for the most demanding applications, our MEMS based IMU can reach bias instability as precise as ≤0.1°/h.
Proven in Harsh Environment
Our solutions are built to withstand extreme conditions, providing consistent performance in harsh environments.
Excellent Performance under Vibrations
Our MEMS and FOG IMU technology excels in high-vibration settings, ensuring accuracy and stability even in the most challenging operational environments.
PLUG & PLAY System
Our systems are designed for easy integration, offering plug-and-play solutions that simplify installation and reduce setup time, allowing you to focus on your mission.
ITAR-FREE
Our products are ITAR-free, offering you the advantage of easier international transactions and fewer regulatory hurdles. Choose GuideNav for seamless global operations.
Our Factory - See to Believe
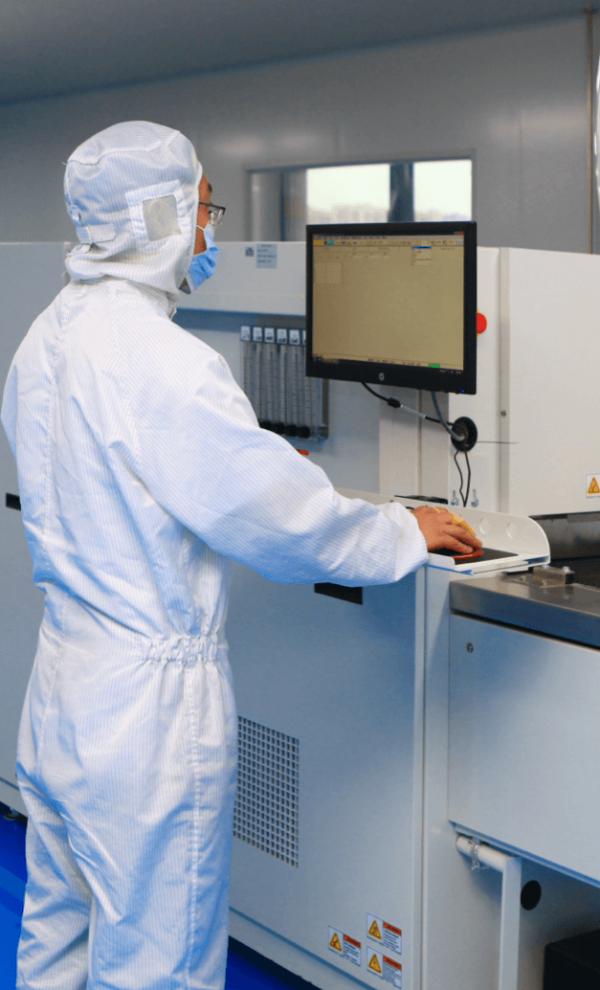
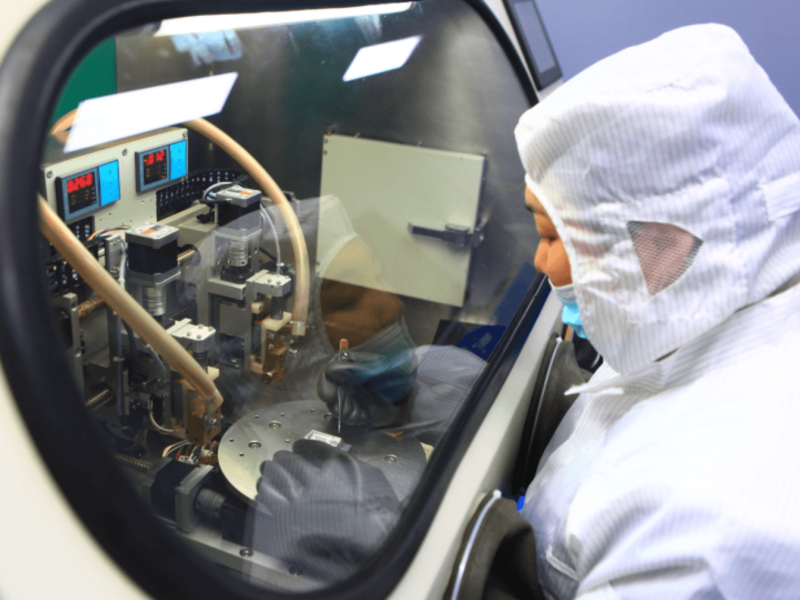
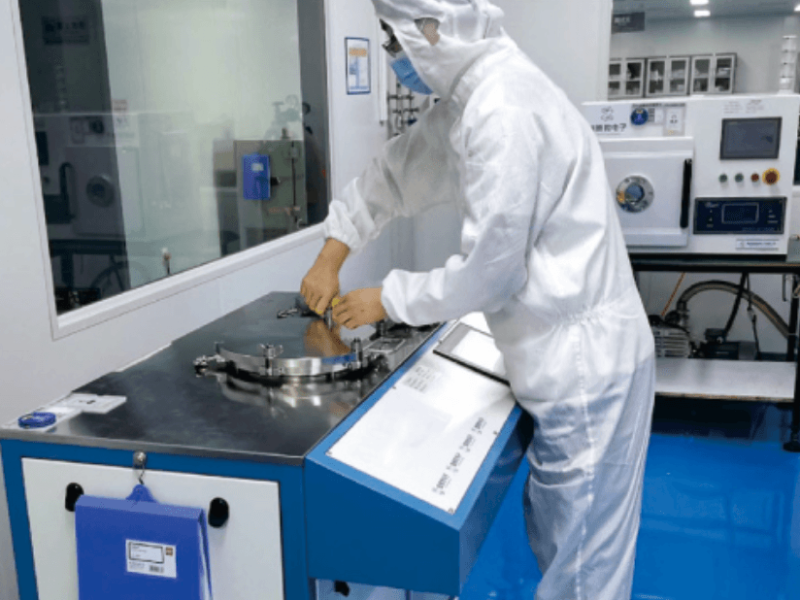
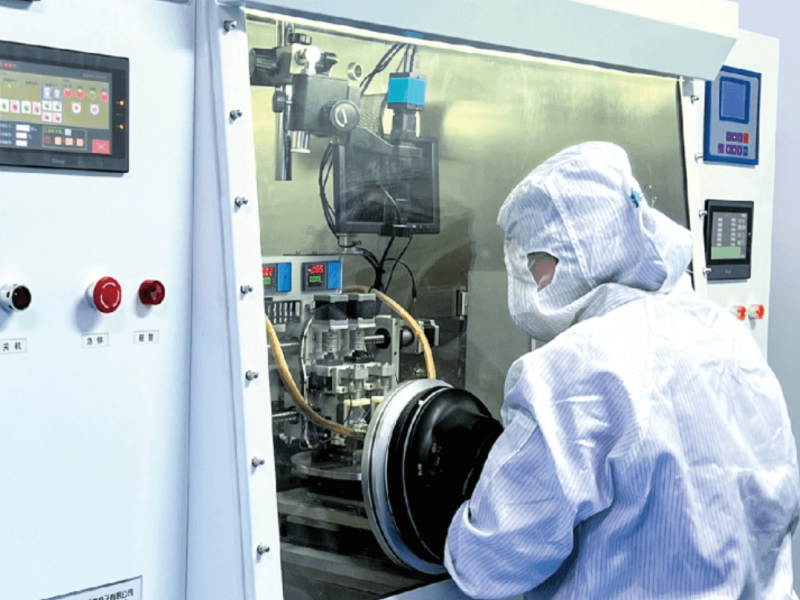
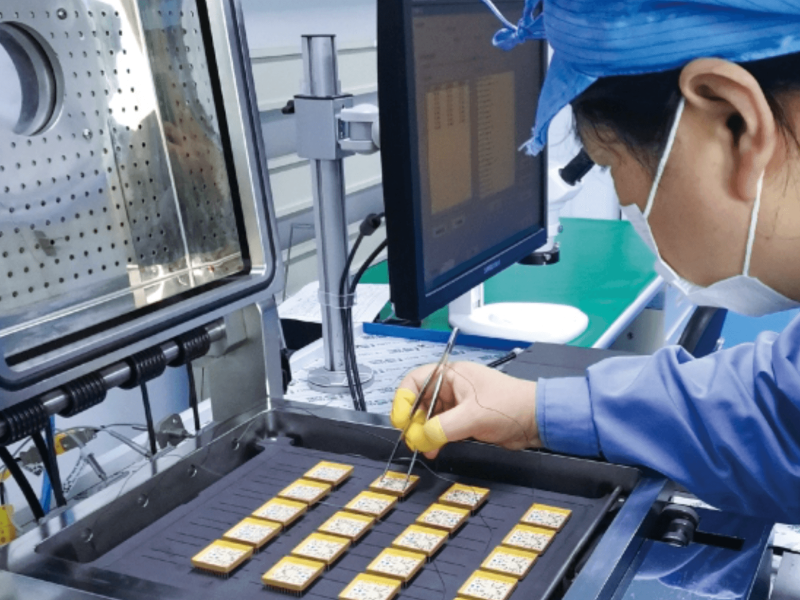
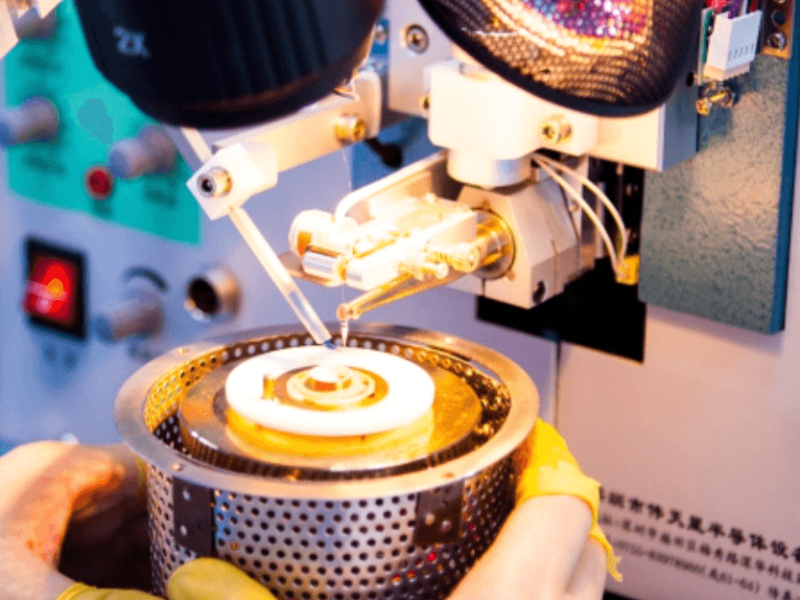
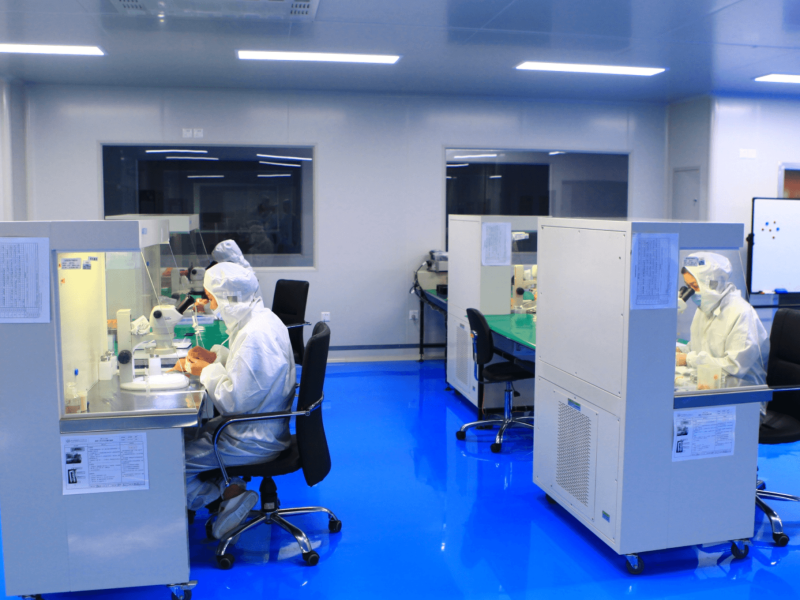
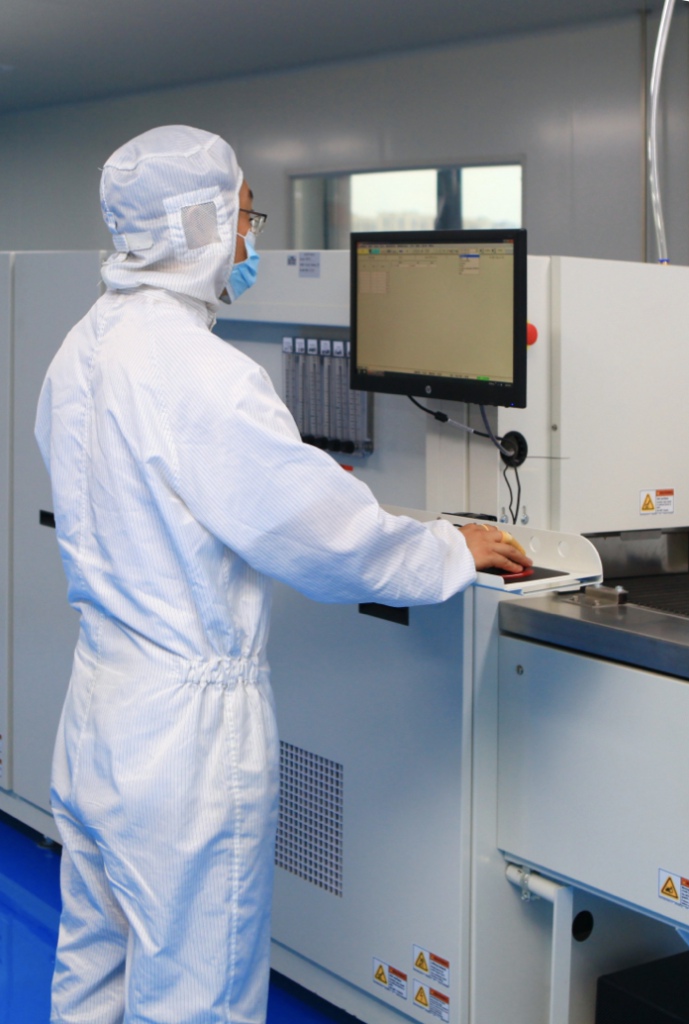
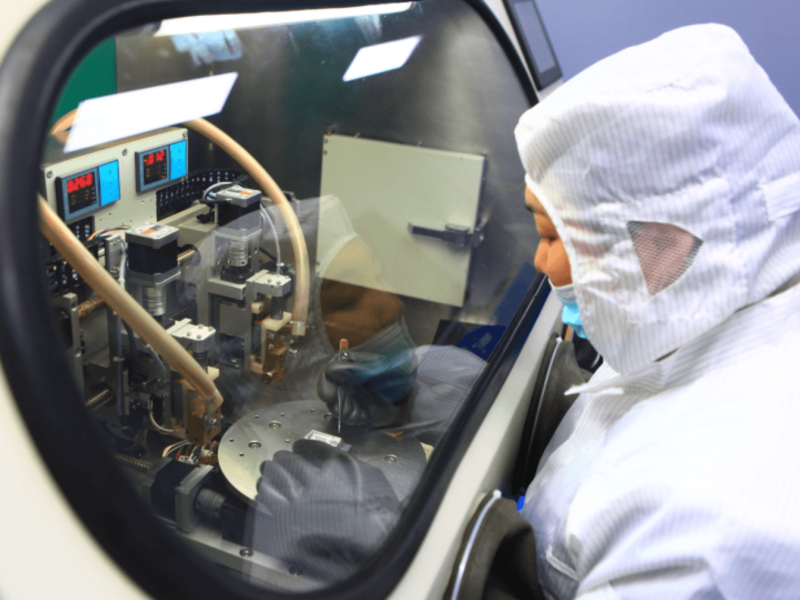
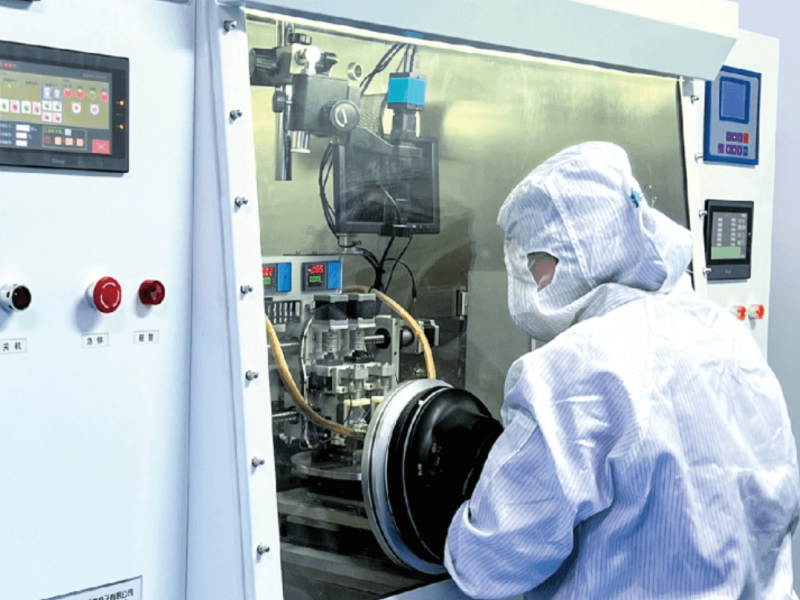
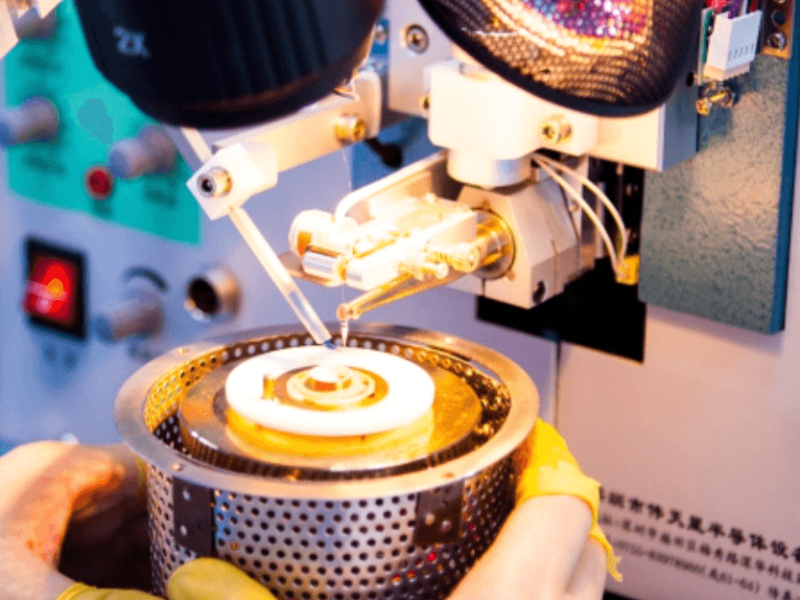
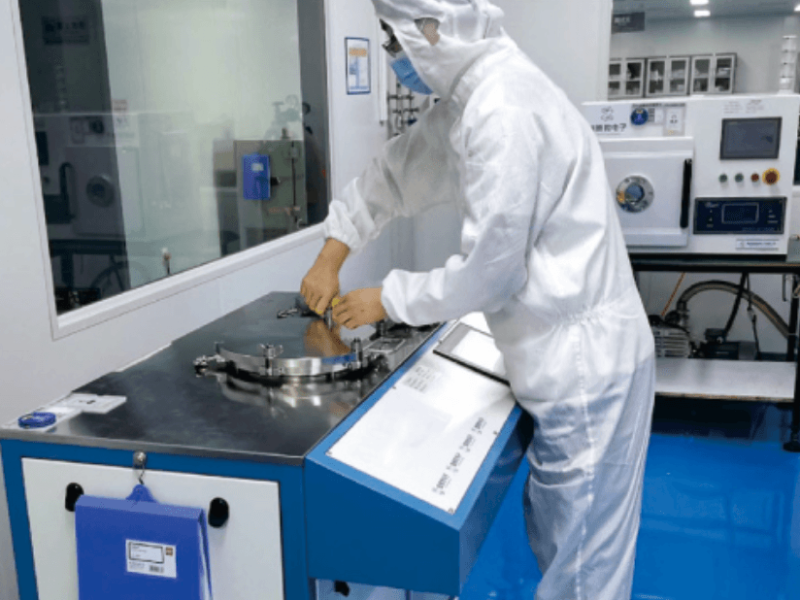
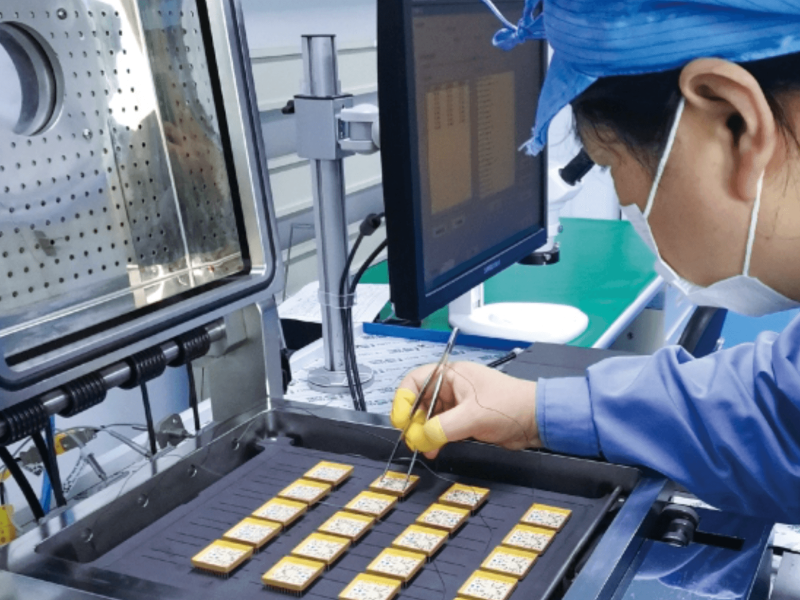
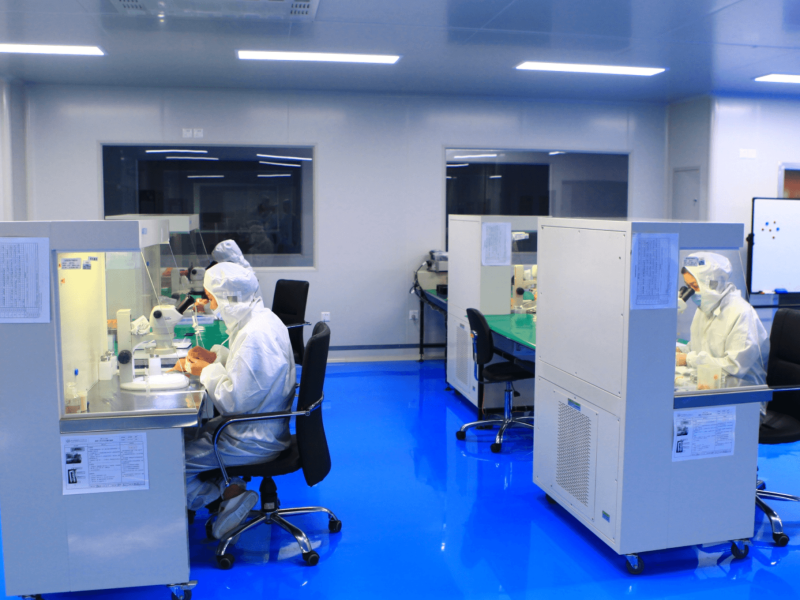
Why Choose Us
Comprehensive Solutions for All Your Navigation Needs
Commercial Grade Coverage
Bias Stability: >0.2°/h
Solution: MEMS based Gyroscope/IMU/INS
Applications: car navigation, unmanned aerial vehicles, transportation, robotics etc.
Tactical Grade Coverage
Bias Stability: 0.05°/h-0.2°/h
Solution: Fiber Optics and MEMS based Gyroscope/IMU/INS
Applications: armored vehicles operations, anti-aircraft artillery, precision targeting etc.
Navigation Grade Coverage
Bias Stability: ≤0.05°/h
Solution: Fiber Optics & Ring Laser Gyroscope/IMU/INS
Applications: medium and long-range guidance, military aviation, satellites
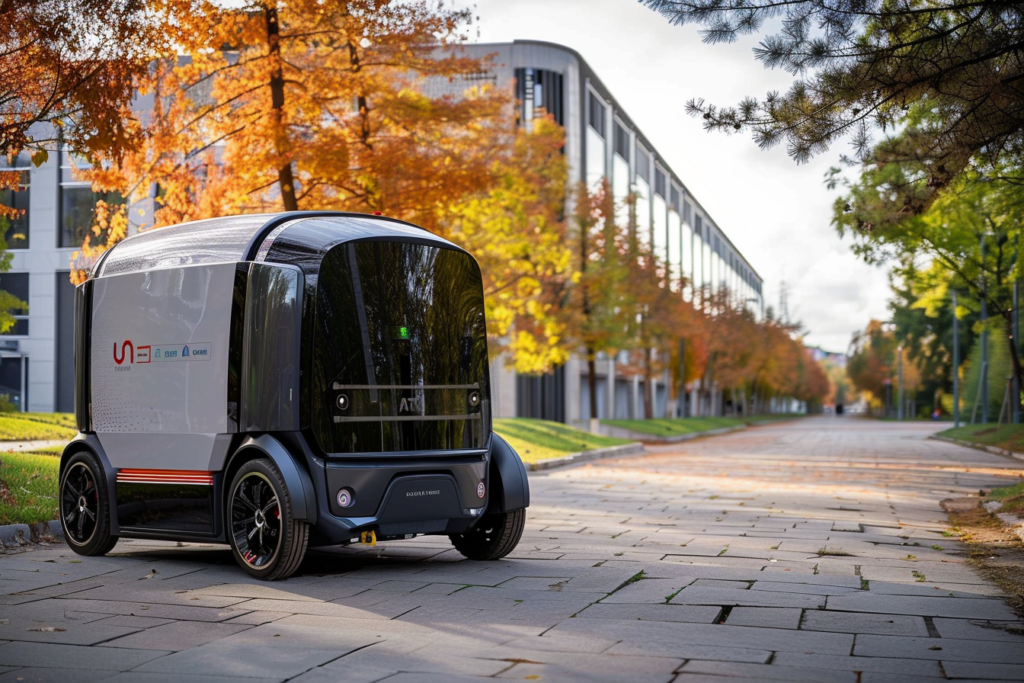
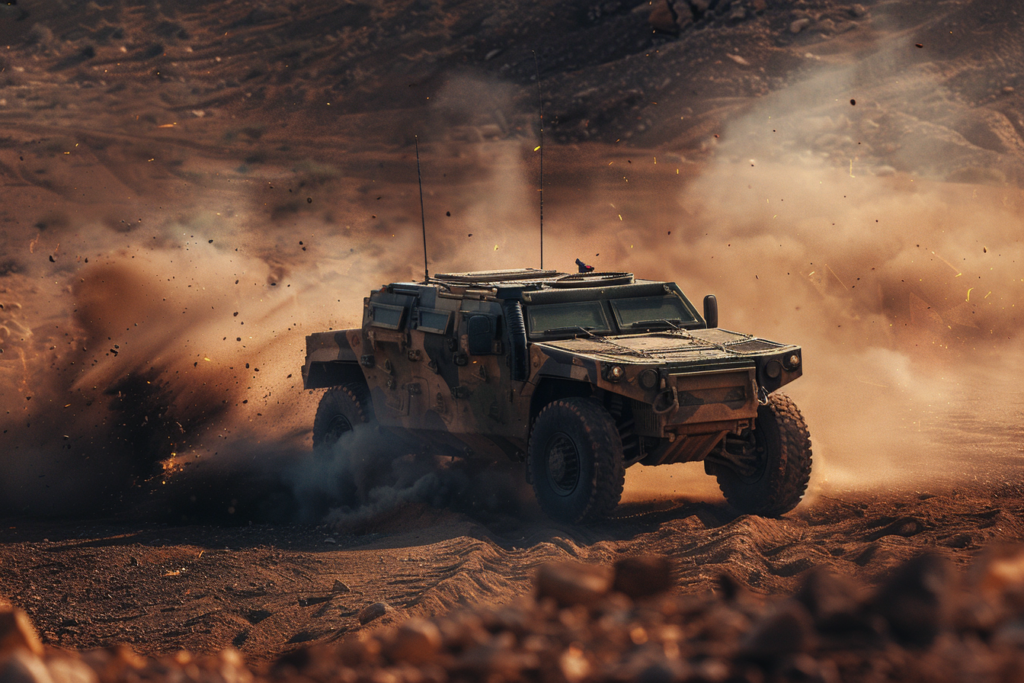
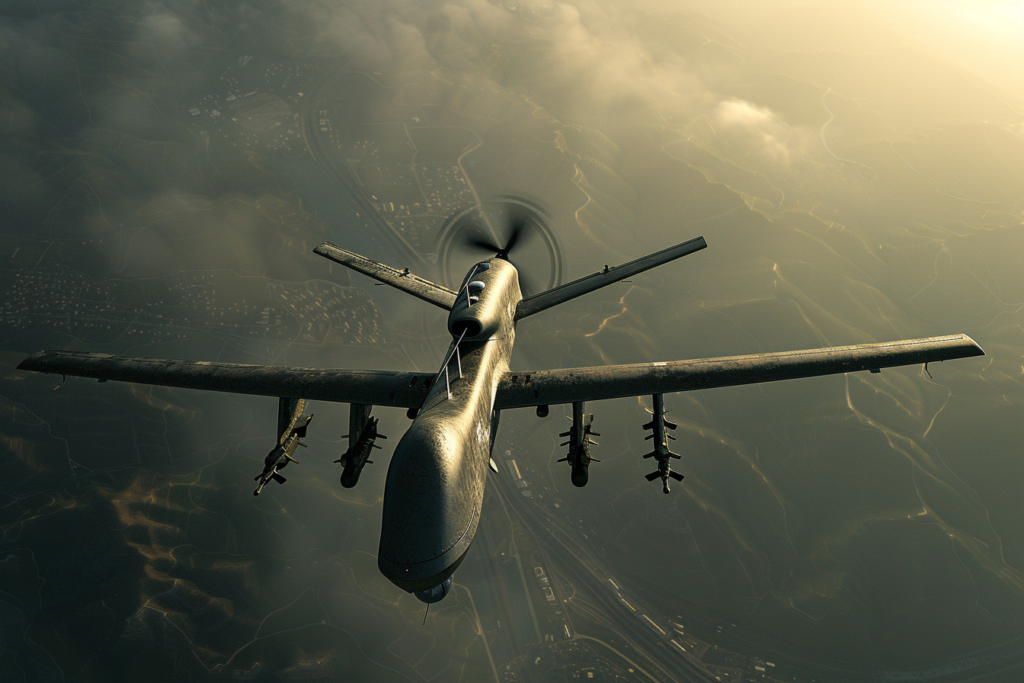
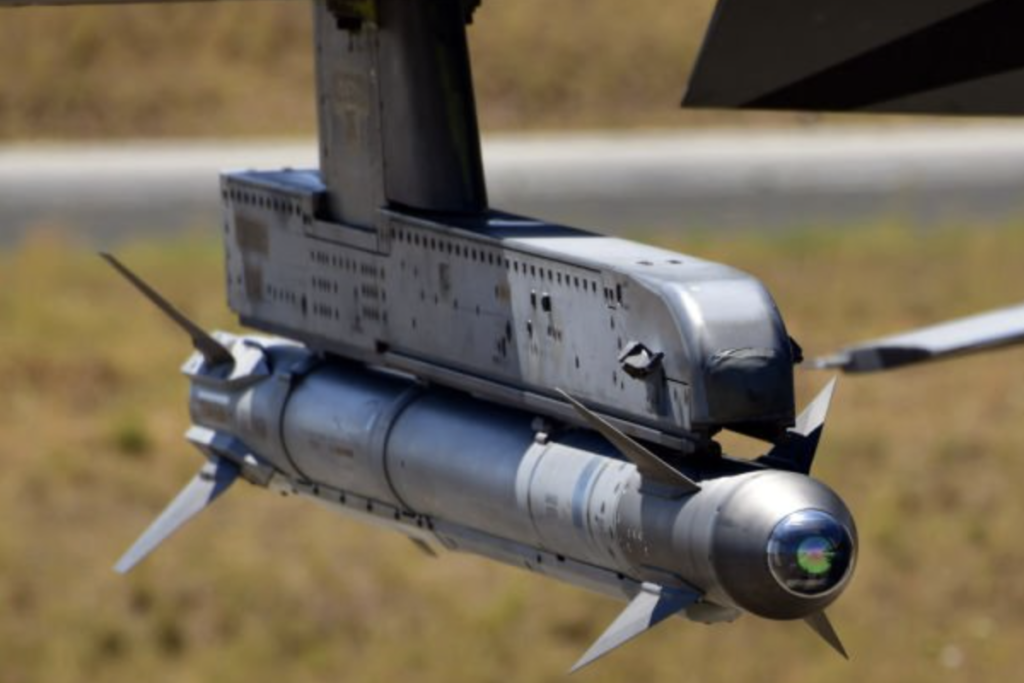
FAQS Inertial Measurement Unit
Answers to Your Questions
The primary functions of an IMU are to provide real-time orientation (such as pitch, roll, and yaw angles) and motion information (such as linear acceleration and angular velocity). This data helps systems like robots, drones, mobile devices, or smart vehicles with navigation, positioning, and control.
GPS provides geographical location and absolute velocity information through satellite positioning, while an IMU relies on internal sensor measurements to provide relative motion status and orientation changes. IMUs can operate without external positioning signals, making them especially useful in environments where GPS signals are unavailable or unreliable (e.g., indoors, tunnels, or underwater). Typically, combining IMU and GPS data results in more accurate and reliable positioning and navigation.
A typical IMU outputs include:
- Three-axis accelerometer data (X, Y, Z)
- Three-axis gyroscope data (X, Y, Z)
- (If equipped) Three-axis magnetometer data
- (If equipped) Barometric pressure and altitude data
We offer two main types of IMUs:
- MEMS IMUs: Smaller, lighter, and more affordable, ideal for medium precision applications. We also offer high-precision MEMS IMUs that provide accuracy levels up to 0.1°/hr, comparable to entry-level FOGs.
- FOG IMUs: High-precision and stable, used in demanding applications such as aerospace, defense, and high-end navigation systems.
Yes, GuideNav's IMUs are well-suited for military-grade applications. With a focus on high-precision, durability, and customization, our IMUs meet the demanding requirements for sensitive defense operations, including underwater reconnaissance, surveillance, and reconnaissance missions.
Yes, you can replace your existing IMU with our product. Our IMU is designed to be compatible with a wide range of systems and applications. Here are a few key points to consider:
Compatibility: Our IMU supports standard communication protocols (such as SPI, I2C, UART) and offers similar or improved specifications compared to most existing IMUs. This ensures that integration with your current system should be straightforward.
Enhanced Performance: Our IMU provides higher accuracy, lower noise levels, and better stability, which can enhance the overall performance of your application.
Additional Features: Depending on the model, our IMUs may include additional sensors (like magnetometers) and advanced data processing capabilities, offering more comprehensive motion and orientation data.
Support and Documentation: We provide detailed documentation and technical support to assist you in the replacement process, ensuring a smooth transition without significant downtime.
Customization: If you have specific requirements, our team can work with you to customize the IMU settings or firmware to better suit your application needs.