In my 15 years working with inertial navigation and monitoring systems, I’ve seen firsthand how crucial pipeline integrity is for safe, efficient oil and gas operations. Traditional monitoring methods like GPS often fail in challenging environments—such as deep-sea or underground pipelines—where signals can’t reach. These limitations create significant risks, leaving deformations undetected and potentially leading to costly repairs or environmental damage.
Inertial Measurement Units (IMUs) provide an essential solution, allowing us to track pipelines accurately, even where GPS falls short, and ensuring we meet industry standards for safety and reliability.
This article explains how IMUs work, their unique benefits in oil and gas applications, and why they’re essential for enhancing pipeline safety and reliability.
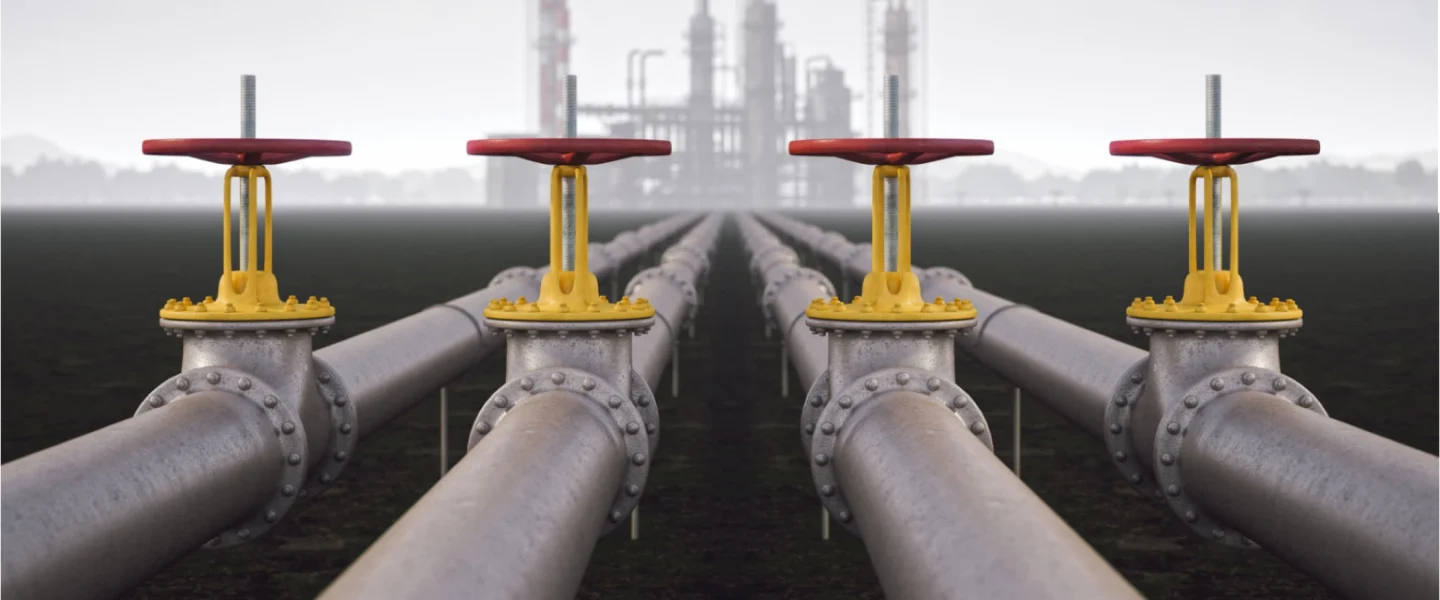
Table of contents
What Are IMUs and How Do They Work in Pipeline Monitoring?
The Inertial Measurement Unit combines accelerometers, gyroscopes, and sometimes magnetometers to measure linear and angular motion. By processing these measurements, IMUs track the movement and orientation of pipelines with high precision, making them invaluable in scenarios where GPS isn’t an option. This technology offers accuracy that can make the difference in early detection of stress or deformation, ensuring operational integrity.
Which IMU Type is Best for Pipeline Monitoring: MEMS or FOG?
In oil and gas pipeline monitoring, Fiber Optic Gyroscope (FOG) IMUs are the preferred choice for most clients, covering approximately 80% of applications. FOG IMUs deliver high precision and stability, which are essential for pipelines in challenging environments, such as offshore and deep-sea installations. Their low drift and high accuracy make them ideal for detecting even slight pipeline shifts, which is critical for maintaining structural integrity under extreme conditions.
- FOG IMUs: Due to their precision, FOG IMUs are widely used for offshore or underground pipeline monitoring, where even minor shifts can pose serious risks. Their durability and low drift over time provide the reliability necessary for long-term projects and harsh environmental conditions.
- MEMS IMUs: Although less common in these applications, MEMS IMUs are compact and cost-effective, making them a suitable choice for less demanding environments or for shorter-term monitoring needs. MEMS IMUs are generally used in applications where cost control is prioritized, though they lack the precision of FOG.
For the vast majority of oil and gas pipeline applications, FOG IMUs are the go-to solution, offering the high accuracy and reliability required to ensure pipeline safety and efficiency over long distances and in extreme settings.
How IMUs Provide Accurate Mapping in Hard-to-Reach Areas?
As professionals, we know that accurate mapping is the foundation for assessing pipeline stability. IMUs give us this capability where other tools fail. For example, in pipelines laid beneath the seabed, IMUs provide precise 3D mapping and can detect even minor shifts or curvature changes caused by external forces. This level of accuracy enables us to respond to potential issues early, preserving both pipeline integrity and safety.
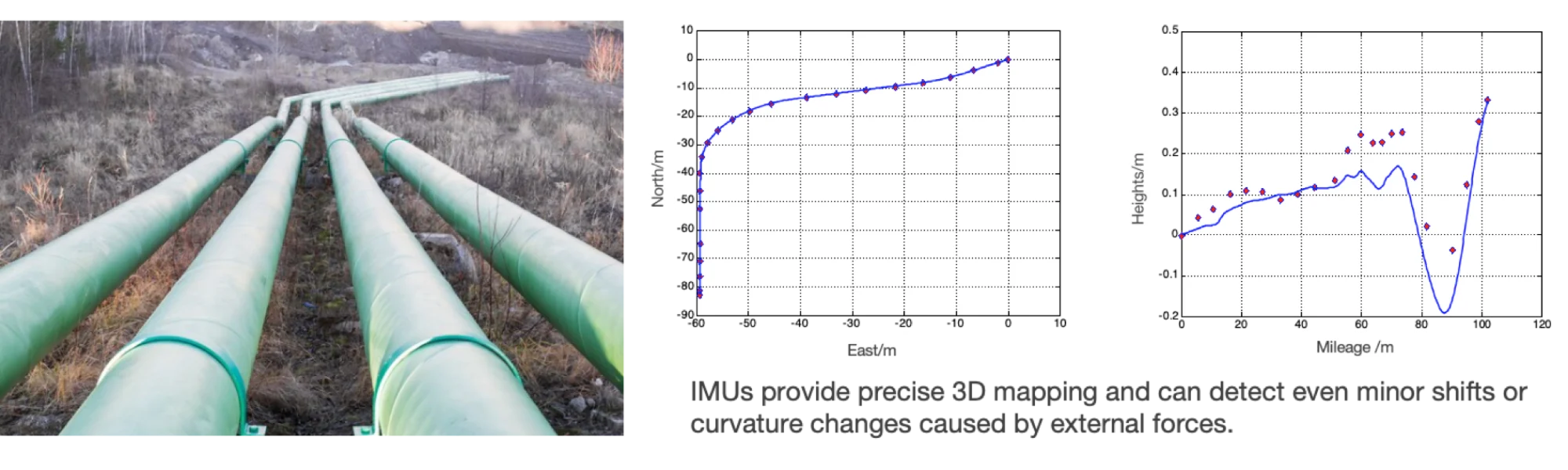
Key IMU Specifications for Pipeline Monitoring
Specification | Typical IMU Performance |
---|---|
Data Sampling Frequency | Up to 200 Hz |
Gyroscope Range | ±450°/s or higher |
Accelerometer Range | ±20g |
Bias Stability (Gyroscope) | Less than 0.5°/hr for precision-grade models |
Operating Temperature Range | -40°C to 85°C, ensuring suitability for extreme conditions |
Benefit | Impact |
---|---|
GPS Independence | Continuous tracking in inaccessible or GPS-limited areas |
Cost Efficiency | Early detection minimizes repair costs and downtime |
Enhanced Safety | Real-time data prevents catastrophic failures |
Regulatory Compliance | Precise tracking supports compliance with industry standards |
Why IMUs Are Essential for Underwater and Underground Pipelines
From experience, I can confirm that IMUs are critical where GPS access is impossible. In underwater and underground pipelines, GPS signals can’t penetrate, making it hard to monitor the line’s position and behavior. IMUs solve this by working independently of external signals, offering continuous, precise tracking regardless of environmental challenges. This is especially crucial in areas with environmental risks like seismic activity or shifting ground.
Leveraging IMU Data for Predictive Maintenance
One of the greatest benefits IMUs provide is predictive maintenance capabilities. Instead of reacting to pipeline issues, we can use IMU data to identify stress points or subtle shifts in alignment early on. This allows us to schedule maintenance proactively, reducing unexpected shutdowns and keeping repair costs down. IMUs empower us to move from reactive to predictive maintenance—ultimately increasing the lifespan and reliability of our pipelines.
How IMUs Integrate with Other Pipeline Inspection Technologies
IMUs don’t operate in isolation; in fact, they enhance the capabilities of other inspection tools. For instance, when we combine IMU data with metal-loss inspection or smart pigs, we gain a full picture of pipeline health. IMUs pinpoint the exact location of defects, allowing operators to respond quickly. By integrating multiple tools, we can develop a comprehensive, real-time understanding of pipeline status, improving both efficiency and safety.
Advantages of Using IMUs for Pipeline Integrity
IMUs provide substantial benefits for pipeline integrity management by offering consistent, high-accuracy tracking and monitoring. Below are the primary advantages:
Benefit | Impact |
---|---|
GPS Independence | Continuous tracking in inaccessible or GPS-limited areas |
Cost Efficiency | Early detection minimizes repair costs and downtime |
Enhanced Safety | Real-time data prevents catastrophic failures |
Regulatory Compliance | Precise tracking supports compliance with industry standards |
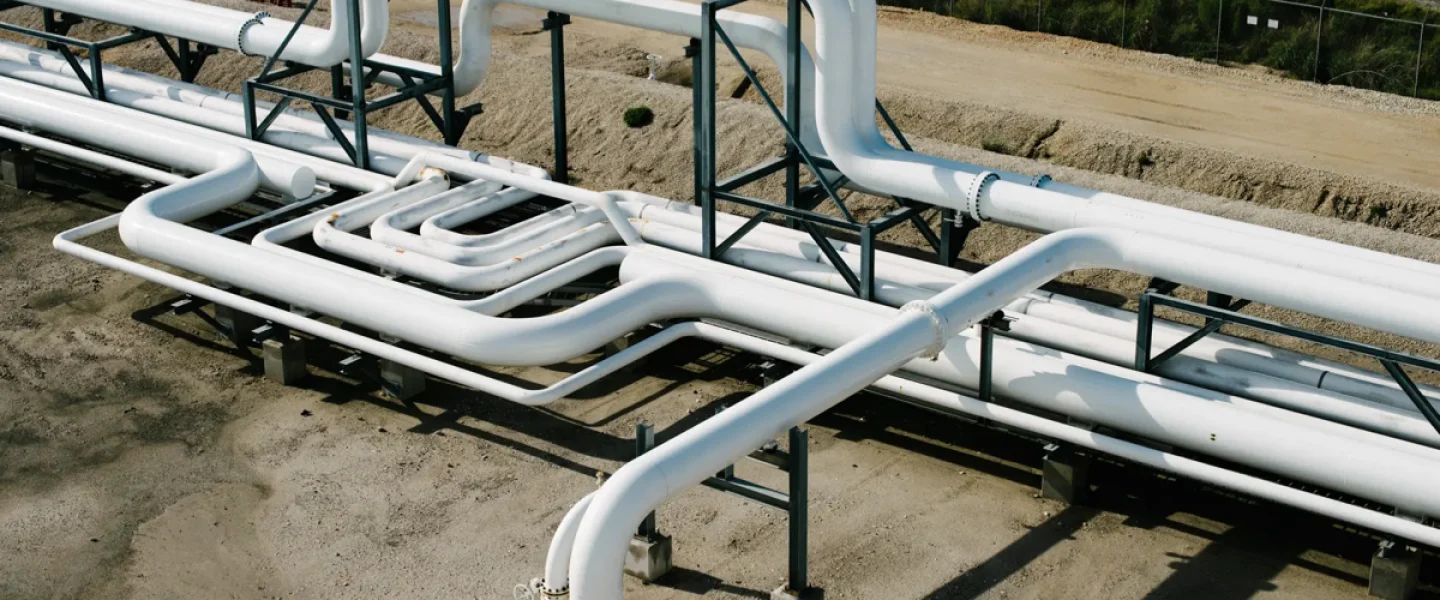
How Can GuideNav Help?
With extensive experience in oil and gas pipeline monitoring solutions, GuideNav has assisted numerous companies in enhancing the safety, precision, and reliability of their pipeline operations. Here’s how we can support your specific needs:
- Customized IMU Design
GuideNav understands that different pipeline environments require specific materials, sizes, and interfaces. We offer customization of IMU housing materials, dimensions, and connectivity optionsto ensure seamless integration with your existing infrastructure. - Precise Positioning in GPS-Deprived Areas
When GPS is unavailable, GuideNav’s IMUs step in to deliver accurate pipeline coordinates. Our FOG and MEMS IMUs provide position and orientation data, enabling operators to reliably track pipeline location even in deep-sea or underground settings. - Enhanced Durability and Environmental Resistance
GuideNav’s IMUs are built to withstand extreme conditions, including high pressures, vibrations, and temperature fluctuations. Our devices are ruggedized for long-term use in harsh environments, ensuring sustained accuracy and minimal maintenance. - Advanced Data Analysis and Integration
GuideNav offers data compatibility and integration support with other monitoring systems, allowing clients to combine IMU data with smart pigging tools or corrosion detection systems. This provides a full picture of pipeline integrity, simplifying data analysis and enhancing decision-making.